基於閉式溫鍛的整體式結合齒齒輪的實現方法與流程
2023-04-24 23:48:26 1
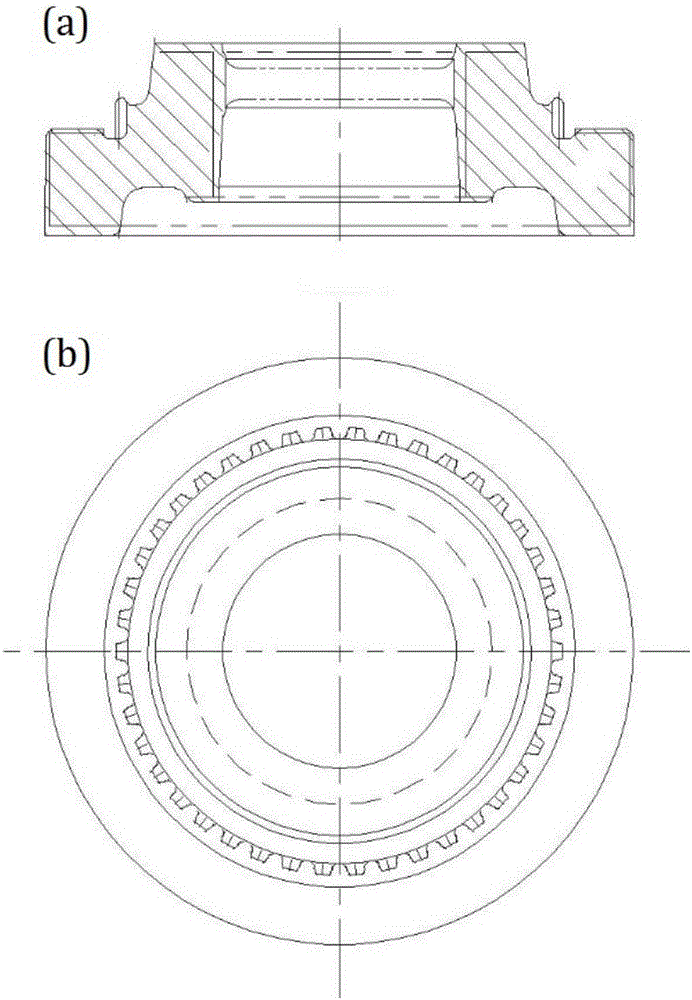
本發明涉及的是一種材料成型領域的技術,具體是一種基於閉式溫鍛的整體式結合齒齒輪的實現方法。
背景技術:
齒輪作為汽車變速器中的重要組成零件之一,其作用主要是傳遞大扭矩和交變載荷,從而實現汽車換擋、變速的目的。整體式結合齒是將結合齒齒輪與斜/直齒傳動齒輪合二為一的一種傳動齒輪。該結構能夠減小傳動軸長度,具有結構緊湊、靈活可靠的優點,因此,被廣泛用於汽車變速器傳動機構當中。
整體式結合齒齒輪結構複雜,尺寸精度要求高,產品服役環境惡劣,因此,對於其加工製造方法要求嚴格。目前對於整體式結合齒齒輪的主要製造方法有兩種。一種是將結合齒齒輪和斜/直齒傳動齒輪分開,採用傳統機加工或鍛造方法分別生產,然後再將兩者焊接成為一體。這種方法生產的產品雖然能滿足客戶要求,但是焊接性能、產品強度以及穩定性無法保證,影響產品質量。另一種方法是採用開式熱鍛工藝鍛造出整體式結合齒齒輪毛坯,然後再經過冷鍛整形和機加工獲得最終產品。該方法主要缺點是開式熱鍛工藝對鍛造溫度要求高,達到1100℃以上,加熱時間長,產品脫碳嚴重,從而造成鍛件性能不足。另外,由於鍛件具有飛邊,導致材料利用率低,生產投入成本大。
技術實現要素:
本發明針對現有技術存在的上述不足,提出了一種基於閉式溫鍛的整體式結合齒齒輪的實現方法,能夠在較低溫度和較高材料利用率的條件下生產出尺寸精度和性能要求均合格的整體式結合齒齒輪鍛件。
本發明是通過以下技術方案實現的:
本發明通過對預熱後的棒料表面噴塗潤滑劑進行預潤滑後,將棒料加熱至鍛造溫度後經整形、制坯、預鍛、終鍛和衝孔組成的閉式溫鍛處理,製成整體式結合齒齒輪。
所述的棒料根據理論計算長度採用圓盤鋸進行切割下料,所述的棒料名義重量與終鍛件的重量相同。
所述的棒料,優選在預熱前經過拋丸處理,該拋丸處理是指使用滾筒式拋丸機去除棒料表面氧化皮和附著物。
所述的預熱是指用中頻加熱設備將棒料加熱至120-200℃。
所述的潤滑劑優選採用溶液濃度為3-5wt.%的石墨潤滑劑。
所述的鍛造溫度為870-970℃。
所述的閉式溫鍛處理使用曲柄壓力機對加熱後的棒料進行整形和制坯處理,得到材料分布合理的坯料;然後經預鍛處理得到預鍛件,再經終鍛處理得到帶結合齒的終鍛件,最後衝孔得到整體式結合齒齒輪鍛件。
技術效果
與現有技術相比,本發明採用的閉式溫鍛成形工藝一方面可以在較低成形載荷條件下直接生產出尺寸精度合格的汽車整體式結合齒齒輪鍛件,對生產設備要求低,產品強度優異;另一方面棒料加熱溫度要求為870-970℃,低於目前開式熱鍛工藝所需的1100℃,能源消耗少,結合齒全脫碳層小於0.1mm,低於開式熱鍛工藝0.5mm的全脫碳層,溫鍛零件沒有氧化皮,鍛件表面質量高,性能優異,終鍛件無飛邊,無需切邊工藝,保證法蘭部分的材料流線完整,下料工藝中棒料的名義重量與終鍛件重量相同,材料利用率高達92%,高於開式熱鍛工藝82%的材料利用率,生產成本低。
附圖說明
圖1為汽車變速器四擋從動齒輪鍛件整體結構示意圖;
圖2為汽車變速器四擋從動齒輪鍛件平面結構示意圖;
圖中:(a)為剖面結構圖,(b)為俯視圖;
圖3為本發明中閉式溫鍛成形工序流程圖;
圖4為圖3中預鍛件部分結構放大圖;
圖5為圖3中終鍛件部分結構放大圖;
圖6為預鍛件中法蘭部E4、中間部E3、軸套部E2和連皮部E1的材料體積分布圖;
圖7為終鍛件中法蘭部F4、中間部F3、軸套部F2和連皮部F1的材料體積分布圖。
具體實施方式
下面對本發明的實施例作詳細說明,本實施例在以本發明技術方案為前提下進行實施,給出了詳細的實施方式和具體的操作過程,但本發明的保護範圍不限於下述的實施例。
實施例1
如圖1和圖2所示,本實施例以某一汽車變速器中結合齒小徑為的四擋從動齒輪為例,說明結合齒齒輪鍛件的製造工藝。
本實施例包括以下步驟:
S1,下料:根據四擋從動齒輪鍛件生產加工圖紙計算出鍛件重量,選擇合適直徑的棒料,確定棒料長度,根據棒料長度採用圓盤鋸進行下料;所述的棒料名義重量與終鍛件的重量相同;
S2,拋丸:使用滾筒式拋丸機去除棒料表面氧化皮和附著物,以便潤滑;
S3,預熱:使用中頻加熱裝置,將拋丸後的棒料加熱至150±20℃;
S4,預潤滑:採用溶液濃度為3-5wt.%的石墨潤滑劑對預熱後的棒料進行潤滑;
S5,加熱:使用中頻加熱裝置將預潤滑處理後的棒料加熱至920±20℃後保溫,同時通過火焰加熱裝置將模具加熱至150±20℃後保溫;
S6,閉式溫鍛成形:如圖3所示,使用曲柄壓力機通過模具對加熱後的棒料進行整形和制坯處理,得到材料分布合理的坯料;然後經預鍛處理得到預鍛件,再經終鍛處理得到帶結合齒的終鍛件,最後通過衝孔得到整體式結合齒齒輪鍛件。
優選地,所述棒料的牌號SAE5120H-M,晶粒度6-8級,材料硬度230HB。
所述的整形操作在棒料的上、下端面加工分別得到直徑為2-3mm的同軸的定位孔,且上端面定位孔的直徑大於下端面定位孔,便於自動化搬運時坯料的定位。
所述的制坯操作形成四擋從動齒輪的法蘭部、用於成形結合齒的中間部和用於成形軸孔的軸套部,各部分材料與終鍛件相應位置的材料在重量分布上相匹配。
所述的預鍛操作分別在上、下定位孔基礎上形成上、下軸孔,上下軸孔間連接有連皮部E1,上、下軸孔直徑相同且與軸承直徑匹配;同時用於成形結合齒的中間部E3材料體積大於終鍛件結合齒中間部F3的材料體積,保證結合齒充填完整,如圖6和圖7所示;中間部外徑D為69.24mm小於終鍛件中成形結合齒70.2mm的小徑直徑,如圖3和圖4所示。
所述的終鍛操作形成結合齒,終鍛件結合齒眉角端面為平面,如圖5所示,結合齒充填完整。
所述的衝孔操作去除上、下軸孔間的連皮部F1。
本發明實施例涉及上述方法製備得到的整體式結合齒齒輪,齒輪強度高,結合齒齒形和齒向精度高,鍛件法蘭與結合齒同軸度達到0.2mm,便於後續加工的定位。