一種雙界面智慧卡的焊接方法與流程
2023-05-10 05:16:26 2
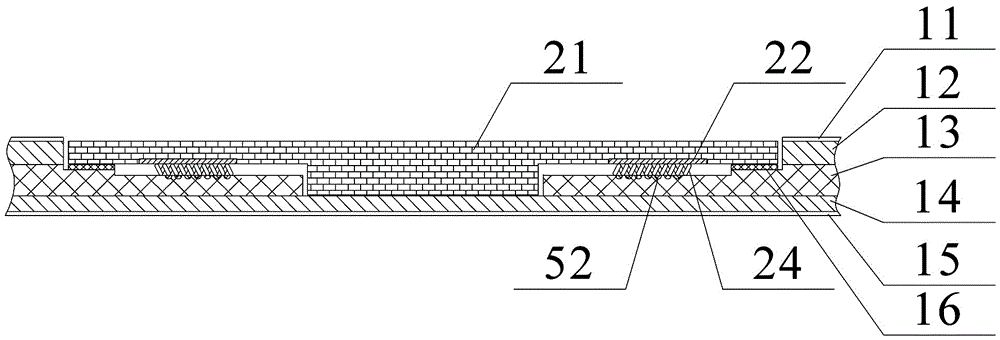
本發明涉及一種智慧卡,特別是公開一種雙界面智慧卡的焊接方法,是一種應用於信息技術領域智慧卡的製造方法。
背景技術:
目前雙界面智慧卡的製作方式一般包括以下步驟:
在卡體材料(PVC、PETG等)上使用超聲波將銅漆包線植入,形成金屬天線,也有一些廠家將繞線機繞制好的漆包線線圈使用粘結的方法粘在天線基材上,形成金屬天線。
雙界面智慧卡卡基,是通過將透明膜、印刷層和中間層(含天線)、印刷層和表面膜裝訂後進行層壓形成的大張半成品,再放入切卡機中衝切而成。
卡基模塊焊盤是通過在雙界面智慧卡卡基的雙界面模塊所在處進行銑槽得到,但為露出用於焊接的天線兩個端頭,必須使用手工將天線兩端的線頭從卡基中挑出,並將天線從卡基中拉出一定長度,將拉出的兩段天線修剪為相同長度並使其垂直向上。
接下來對雙界面模塊焊盤進行上錫處理,焊盤以外的地方粘貼熱熔膠膜。
通過手工或自動機器將雙界面模塊焊盤與雙界面智慧卡卡基上直立的天線焊接在一起,並將焊接好的雙界面模塊擺放在雙界面智慧卡卡基銑好的槽內,並使用熱壓設備將雙界面模塊上的熱熔膠膜融化後,最後將雙界面模塊與雙界面智慧卡卡基粘結在一起,最終得到雙界面智慧卡的成品。
從上述雙界面智慧卡的結構及製作過程來看,至少在幾個方面存在問題:
需要對天線進行挑線頭、拉線、立線、剪線頭等手工處理,然後將帶有直立線頭的雙界面智慧卡基往設備上擺放等,致使該種雙界面智慧卡的廢品率高,質量難以保證,並且焊接後卡片變形大、外觀凹凸不平。
專利號ZL 2011 1 0187452.1公開的一種雙界面智慧卡,通過銑加工出焊接槽再採用錫焊的方式提高了產品焊接的可靠性和成品率。這種焊接方式理論上是可行的,但是在實際生產中有一明顯弊端:這種焊接模式決定了在雙界面模塊焊盤上留有的焊錫太多(焊錫厚度需要達到0.3mm左右),熔化這些焊錫需要的時間長、溫度高,對於智慧卡卡基材料PVC來說,這麼高的溫度和加熱時間,足以使PVC變形,對智慧卡的外觀產生較大影響。如果為了避免變形而減少加熱時間或降低加熱溫度,則又會帶來虛焊的隱患,這給生產現場的機器操作員很大的不確定性。
技術實現要素:
本發明的目的是解決現有技術的缺陷,設計一種雙界面智慧卡的焊接方法,採用鍍錫銅線管作為焊接中間介質,即使使用行業內普遍使用的漆包銅線作為天線,也能獲得良好的焊接效果。而且本發明使用目前行業內智慧卡生產中普遍具備的超聲波繞線設備來完成天線的繞制,不需要另外增加設備,因此該種雙界面智慧卡的成本較低。
本發明是這樣實現的:一種雙界面智慧卡的焊接方法,所述雙界面智慧卡包括金屬天線、模塊槽和焊接槽,所述的金屬天線具有兩個天線焊盤,雙界面模塊放置於雙界面智慧卡的卡基銑好的模塊槽內,並使金屬天線的兩個天線焊盤分別與雙界面模塊的兩個雙界面模塊焊盤的區域重疊,通過對天線焊盤的區域進行二次銑槽,露出天線的兩個天線焊盤得到所述的兩個焊接槽,以進行雙界面模塊焊盤與天線焊盤之間的錫焊連接,其特徵在於:所述的焊接方法是在所述的兩個焊接槽內分別放置有一段鍍錫銅線管,通過對雙界面模塊表面施加180℃~190℃的高溫,熱量傳遞至所述鍍錫銅線管熔化鍍錫銅線管表面的焊錫,實現雙界面模塊焊盤與天線焊盤之間的連接。
所述的鍍錫銅線管的銅線直徑在0.05~0.20mm。所述的鍍錫銅線管表面的鍍錫層厚度為0.05~0.15mm。所述的鍍錫銅線管繞制呈螺旋形,螺距為0.2~0.5mm,螺旋直徑為小於或等於0.5mm。所述的鍍錫銅線管繞製成螺旋形後的長度小於或等於6mm。
所述的金屬天線由蝕刻、電鍍、印刷或超聲波繞制工藝製得。
本發明的有益效果是:本發明不僅解決了現有技術中採用銅漆包線天線在錫焊時的虛焊現象,以及使用銅漆包線天線使得只能半自動化、半手工的作業模式,而且由於採用鍍錫銅線管作為焊接中間介質,還解決了現在雙界面智慧卡穩定性低、生產中廢品率較高,以及熱壓變形明顯的問題,即使在全自動化、大批量的生產情況下仍能大幅提高該雙界面智慧卡的焊接可靠性和成品率。並且由於只使用適量的焊錫,所以整個焊接過程時間短,焊接後的焊點平整,智慧卡卡體變形小、外觀更加美觀。本發明採用了目前行業內智慧卡生產中普遍具備的超聲波繞線設備來完成天線的繞制,不需要另外增加設備,因此實現容易、生產成本較低。
附圖說明
圖1是繞制後的金屬天線的結構示意圖。
圖2是本發明雙界面智慧卡剖視結構示意圖。
圖3是本發明雙界面智慧卡焊接槽銑槽處的結構示意圖。
圖4是本發明雙界面智慧卡的鍍錫銅線管的結構示意圖。
圖中:11、第一透明膜;12、第一印刷層;13、卡體中間層;14、第二印刷層;15、第二透明膜; 16、熱熔膠膜; 21、雙界面模塊; 22、雙界面模塊焊盤; 24、鍍錫銅線管;51、金屬銅天線; 52、天線焊盤; 61、卡基; 63、模塊槽。
具體實施方式
根據附圖2~4,本發明為一種雙界面智慧卡的焊接方法,所述的雙界面智慧卡包括金屬天線、模塊槽和焊接槽。所述的金屬天線具有兩個天線焊盤52,雙界面模塊21放置於雙界面智慧卡的卡基61銑好的模塊槽63內,並使金屬天線的兩個天線焊盤52分別與雙界面模塊的兩個雙界面模塊焊盤22的區域重疊,通過對天線焊盤52的區域進行二次銑槽,露出天線的兩個天線焊盤52得到所述的兩個焊接槽,以進行雙界面模塊焊盤22與天線焊盤52之間的錫焊連接。本發明的焊接方法是在所述的兩個焊接槽內分別放置有一段鍍錫銅線管24,通過對雙界面模塊21表面施加180℃~190℃的高溫,熱量再傳遞至所述鍍錫銅線管24熔化鍍錫銅線管24表面的焊錫,實現雙界面模塊焊盤22與天線焊盤52之間的連接。
所述的鍍錫銅線管24的銅線直徑在0.05~0.20mm。所述的鍍錫銅線管24表面的鍍錫層厚度為0.05~0.15mm。所述的鍍錫銅線管繞制呈螺旋形,螺距為0.1~0.2mm,螺旋直徑小於或等於0.5mm。所述的鍍錫銅線管24繞製成螺旋形後的長度小於或等於6mm。
所述的金屬天線51由蝕刻、電鍍、印刷或超聲波繞制工藝製得,採用的金屬必須能與焊錫有效接合,比如蝕刻銅天線和電鍍銅天線等。
下面結合具體實施例對本發明作進一步說明。
實施例:
本實施例中的雙界面智慧卡採用具有銅漆包線作為天線的卡體中間層13,所述的銅漆包線天線具有兩個天線焊盤52。
雙界面智慧卡的卡基61通過對所述帶有金屬天線51的卡體中間層13、第一透明膜11、第一印刷層12、第二印刷層14和第二透明膜15進行裝訂並層壓後得到。
模塊槽63設於所述雙界面智慧卡的卡基61表面,使用銑刀銑出的一個用於放置雙界面模塊21的模塊槽63。
通過對天線焊盤52的區域進行二次銑槽,露出兩個天線焊盤52,所述雙界面模塊21放置於雙界面智慧卡的卡基61銑好的模塊槽63內,並使兩個天線焊盤52分別與兩個雙界面模塊焊盤22的區域重疊。
將兩段所述螺旋形的鍍錫銅絲管24分別放置於兩個露出的天線焊盤52上,再將雙界面模塊21放置於模塊槽63內。使用熱壓頭壓在雙界面模塊21表面,通過熱量傳遞,使鍍錫銅絲管24表面的焊錫熔化,並分別與天線焊盤52和雙界面模塊焊盤22焊接在一起。
根據附圖1,本實施例採用普通的銅漆包線作為卡基61內的金屬天線,在設定位置反覆繞制並形成天線焊盤52,並使用超聲波在PVC表面進行植入。這種工藝可以方便的將兩個天線焊盤52做成較大面積,減輕了銑槽位置的精度要求,方便了裝訂和銑槽工序,從而提高了生產的自動化程度。
根據附圖2和附圖3,本實施例對於雙界面智慧卡的卡基61,其通過帶有金屬天線51的中間層13、第一透明膜11、第一印刷層12、第二印刷層14和第二透明膜15進行裝訂並層壓後得到。然後在雙界面智慧卡的卡基61的雙界面模塊21所在處進行銑槽,得到模塊槽63,然後在天線焊盤52的區域進行二次銑槽,且正好露出天線焊盤52。
最後,本實施例在雙界面模塊21的雙界面模塊焊盤22上做適焊性清潔,並將熱熔膠膜16裝到雙界面模塊21的雙界面模塊焊盤22一側,但是避開雙界面模塊焊盤的區域;然後將鍍錫銅線管24放置在天線焊盤52上,再將雙界面模塊21放入銑好的模塊槽63內;並使用熱壓裝置在雙界面模塊21表面施加180℃~190℃的高溫,融化雙界面模塊21背面的熱熔膠膜16,將雙界面模塊21與卡基61粘合在一起;與此同時,熱量進一步傳遞至鍍錫銅線管24,將鍍錫銅線管24表面的焊錫熔化,焊錫與組成天線焊盤52的銅漆包線焊接在一起,焊錫也與雙界面模塊焊盤22焊接在一起。
本發明通過採用鍍錫銅線管作為焊接中間介質,用錫焊的方法將雙界面智慧卡的卡基中的金屬天線與雙界面模塊焊盤連接在一起,使得雙界面智慧卡在全自動化、大批量的生產的情況下,仍能保證高的可靠性和成品率。並且由於鍍錫銅線管表面的鍍錫層厚度為0.05~0.15mm,所以整個焊接過程時間短,焊接後的焊點平整,智慧卡卡體變形小、外觀更加美觀。
本發明上述實施例僅為用於解釋和對本發明技術方案的說明,而非用於限定本發明保護範圍。在本發明公開的技術方案基礎上,本領域技術人員進行各種等同或等效的改進或替換,均應落在本發明的保護範圍內。