汽車內飾件氣體輔助注塑工藝的製作方法
2023-05-25 23:30:41 1
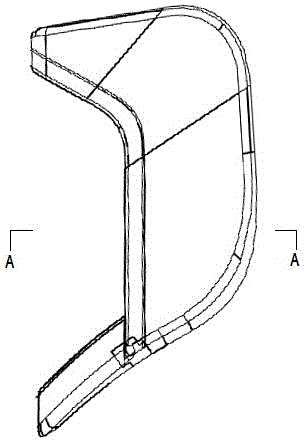
本發明涉及一種氣體輔助注塑工藝,特別是涉及一種適用於具有氣道橫截面積大及氣道長度長的汽車內飾件氣體輔助注塑工藝。
背景技術:
傳統汽車內飾注塑產品的氣道橫截面積為橢圓形或者圓形,且橫截面積比較小,並且與氣道外壁與內壁基本成同一或者類似形狀。但是部分車型為了增加美感,氣道設計的截面積很大,採用傳統的注塑模及工藝會隨著氣道產生周圈的發白現象,影響產品美觀,產品合格率低。
技術實現要素:
針對上述現有技術的不足,本發明的目的是提供一種汽車內飾件氣體輔助注塑工藝,解決產品在氣道位置對應表面產生發白的亮印問題。
本發明的技術方案是這樣的:一種汽車內飾件氣體輔助注塑工藝,包括注塑保壓、高壓吹氣形成產品氣道、氣道內高壓氣體保壓、氣道內正常壓力氣體保壓,所述注塑保壓時在產品外觀面一側的模具內沿產品氣道軸線等間距布置若干加熱管,所述加熱管軸線呈產品外觀面法線方向布置,加熱管端面距離產品外觀面20~25mm;膠料注射前,所述加熱管預熱溫度為膠料熔融溫度的1/2,所述模具的預熱溫度為30~35℃。
優選的,所述加熱管的間距為20~25mm。
進一步的,所述氣道內正常壓力氣體保壓開始後由刺破針刺破氣道進行排氣,在氣道通過刺破孔排氣的同時持續以正常壓力氣體進行保壓。
進一步的,所述刺破氣道時在產品溢料位置刺破氣道。
進一步的,所述刺破氣道在所述氣道內正常壓力氣體保壓開始1s後進行。
優選的,所述高壓吹氣時氣體壓力位135±2Ba,吹氣時間1s。
優選的,所述氣道內高壓氣體保壓時氣體壓力140±2Ba,保壓時間15±1s。
優選的,所述氣道內正常壓力氣體保壓時氣體壓力90±2Ba,保壓時間10±1s。
本發明所提供的技術方案的有益效果是:氣道截面積很大的汽車內飾件產品採用現有注塑工藝生產時,由於氣體與200°以上的膠料接觸,氣道內壁表面快速冷卻,形成較硬的冷卻層,導致後續氣體無法將氣道內壁形狀支撐膨脹至與外壁保持一致。因此一半均形成截面為圓形的氣道,使得氣道與產品外觀面之間形成了局部的壁厚差異,進而在產品表面形成周圈的發白亮印。而採用本發明技術方案,通過局部加熱,使氣道內的膠料在吹氣過程中一直處於比較高溫融體狀態,減緩冷卻硬化過程,讓膠料更容易吹動,使內壁的形狀基本與外壁保持一致,減少了壁厚差異進而減少亮印產生。另外通過刺破氣道使正常壓力氣體保壓時,氣道內氣體流動加強產品氣道位置冷卻,減少冷卻周期,一方面保證了產品氣道內壓力適當,另一方面加速冷卻使產品氣道位置快速成型,從而不易產生氣道爆裂或坍塌,提高了產品合格率,降低成本。
附圖說明
圖1為汽車地圖袋結構示意圖。
圖2為圖1的AA截面示意圖。
圖3為圖2的B區域局部示意圖。
圖4為現有注塑工藝生產後氣道截面示意圖。
圖5為加熱管與汽車地圖袋產品相對位置示意圖。
圖6為本發明工藝生產後氣道截面示意圖。
具體實施方式
下面結合實施例對本發明作進一步說明,但不作為對本發明的限定。
以汽車地圖袋為例,請結合圖1至圖3,該產品設計為具有一條截面積大且長的氣道1,氣道1橫截面積160mm2,氣道1總長度450mm。以現有注塑工藝生產時,容易在圖4中氣道與產品外觀面之間的壁厚差異較大處2形成亮印缺陷。
生產該產品的模具可採用中國專利CNCN104908258A公開的技術方案,在動模上設有產品成型腔及溢料槽,溢料槽與產品成型腔連通並且連通位置位於產品氣道處。在動模上與產品氣道位置處設置氣針,溢料槽位置處設置刺破機構,刺破機構包括刺破油缸和刺破針。另外請結合圖5所示,在動模上沿產品氣道軸線3每間隔20~25mm布置一根加熱管2,加熱管2軸線呈產品外觀面法線方向布置,加熱管2端面距離產品外觀面20~25mm。
本發明的具體生產方法是這樣的,按傳統工藝進行注塑生產,塑料熔體膠料注射前,定模模溫加熱至35℃,動模模溫加熱至30℃,加熱管加熱溫度至120℃,料溫為240℃。膠料注入產品成型腔待注塑保壓結束後,由氣針刺入塑料熔體,採用135±2Ba壓力氣體高壓吹氣1s,在塑料熔體內產生中空結構形成產品氣道,推動塑料熔體充滿產品成型腔並在溢料槽內形成溢料。然後以140±2Ba壓力進行氣道內高壓氣體保壓,保壓時間為15±1s。氣道內高壓氣體保壓結束後降低氣體壓力至90±2Ba,進行氣道內正常壓力氣體保壓,保壓開始後1s,刺破油缸動作,帶動刺破針刺破溢料槽內溢料的氣道,氣道通過刺破孔排氣的同時持續以正常壓力氣體進行保壓,整個氣道內正常壓力氣體保壓時間為10±1s,最後氣體供應關閉,氣體保壓結束刺破針回復原位,氣體輔助注塑完成。開模完成後取出產品,其氣道截面如圖6所示,能形成與產品外表面形狀近似的截面,減少了氣道與產品外觀面之間的壁厚差異,進而消除亮印缺陷的產生。