一種三通結構件及製造方法與流程
2024-02-23 15:36:15 1
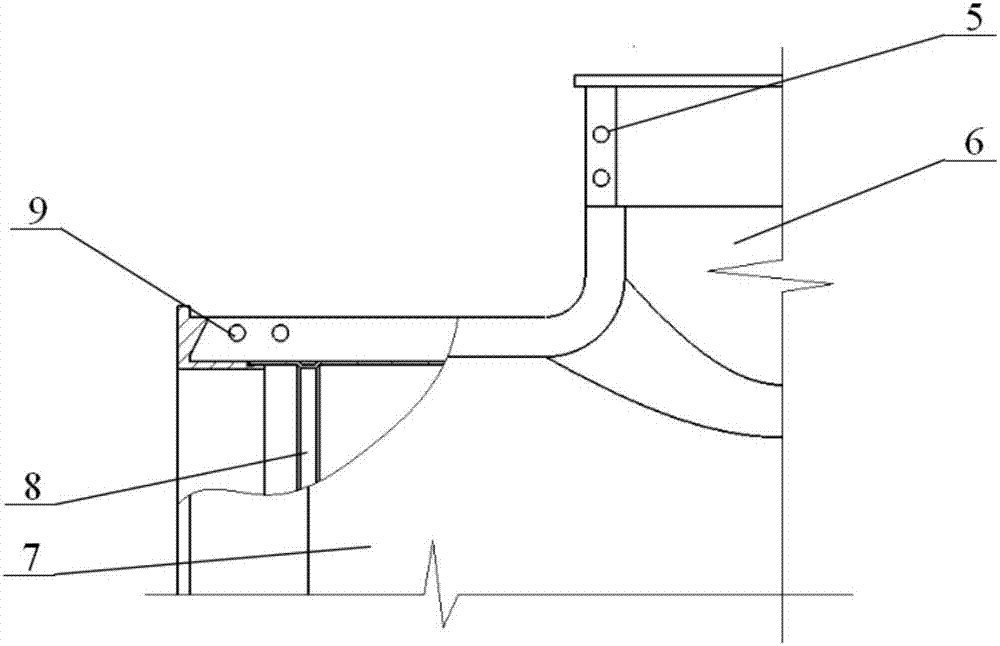
本發明涉及機械製造領域,特別涉及一種三通結構件及製造方法。
背景技術:
目前,國內外的三通管道主要有金屬三通和塑料三通。金屬三通具有耐腐蝕性差的缺點,一般使用壽命不超過3-5年,即使進行表面防護,使用壽麵也很難超過10年;同時,由於金屬材質的三通管道質量大,這也很大程度上增大運輸和施工成本。通過注射成型的塑料三通管道,雖然具有優異的耐腐蝕性,但由於其強度低,在泥土或海水等外界環境壓力條件下,極易使得管道壓潰或是開裂。近年來開發的纖維纏繞成型的熱固性複合材料,雖然具有質量輕,強度高的特點。但由於存在材料、設備成本高、生產效率低、工藝技術複雜、芯模脫出困難的缺點,使其應用受到很大限制。同時,由於熱固性複合材料回收利用難度大的特點,這也可能帶來今後的環境問題。
採用纖維增強的熱塑性複合材料具較高的強度,可以承受一定的內部和外部壓力,且熱塑性材料的基體具有優異的韌性,加之纖維的增強使其更不易開裂。比強度高的特點使得熱塑性複合材料三通管道具有更低的運輸成本和施工成本。同時,熱塑性基體的耐腐蝕性能優異,能夠抵抗土壤腐蝕幾十年,而且能夠在強酸強鹼的條件下使用近十年。此外,熱塑性複合材料可回收,這使得這種材料可以重複利用,並且不給環境帶來危害。熱塑性基體沒有固化時間,成型效率高,能夠滿足量產的需要。因此,熱塑性複合材料可作為這種三通管道的理想材料,特別適用於地下及海洋等惡劣環境中。
有國外專利已經報導過一種熱塑性複合材料管道及其製造方法,這種熱塑性複合材料管道是通過纖維帶纏繞的方式實現的,可實現連續批量生產。但這種製造方法並不適用於複雜結構的三通管道製造。
技術實現要素:
在本發明中,本發明第一方面提供了一種三通結構件,所述三通結構件包括:
一外管、一位於所述外管內的內管、以及用於對所述內管和所述外管進行固定密封的法蘭接頭;
其中,所述的外管由對稱的第一半管和第二半管構成,其中,各半管均設有翼板,所述翼板上設有用於通過螺栓進行固定的螺栓孔;
所述的第一半管和第二半管通過翼板融合區結合為一體結構,其中所述的翼板融合區包括所述第一半管的翼板、第二半管的翼板、以及位於所述第一半管的翼板和所述第二半管的翼板之間的網狀電阻絲,其中所述的第一半管的翼板和第二半管的翼板融合固化在一起;
所述法蘭接頭設有限位槽、限位螺孔、密封槽和密封圈;以及
所述螺栓通過所述限位螺孔和所述螺栓孔將所述外管和所述法蘭接頭進行固定。
在另一優選例中,所述內管的外輪廓與所述外管的內輪廓是相匹配或適形的。
在另一優選例中,所述的內管與所述外管之間通過膠粘劑固定連接。
在另一優選例中,所述的法蘭接頭還設有斜邊槽。
在另一優選例中,所述的斜邊槽為梯形斜邊槽。
在另一優選例中,所述的第一半管的翼板和第二半管的翼板的大小和/或形狀是基本相同的。
在另一優選例中,所述的第一半管的翼板和第二半管的翼板的大小和/或形狀是相同的。
在另一優選例中,所述的內管的直徑為100-5000mm。
在另一優選例中,所述的翼板融合區是通過電阻焊接形成的。
在另一優選例中,所述內管上設有膠槽。
在另一優選例中,所述內管的材質為短纖維增強熱塑性複合材料。
在另一優選例中,所述複合材料的基體材料選自下組:聚乙烯、聚丙烯、聚氯乙烯、聚苯乙烯、聚醯胺樹脂、聚酯樹脂、聚丙烯腈-丁二烯-苯乙烯樹脂、聚苯乙烯-丙烯腈樹脂、熱塑性聚酯和熱塑性聚氨酯、或其組合。
在另一優選例中,所述複合材料的增強纖維選自下組:玻璃纖維、碳纖維、有機聚合物纖維、天然纖維、或其組合。
在另一優選例中,按複合材料的總質量計,所述增強纖維質量分數為2-30%。
在另一優選例中,所述增強纖維長度為1-5mm。
在另一優選例中,所述第一半管和第二半管的材質均為連續纖維增強熱塑性複合材料。
在另一優選例中,所述複合材料基體相的樹脂選自下組:聚丙烯、聚氯乙烯、聚苯乙烯、聚醯胺樹脂、聚酯樹脂、聚丙烯腈-丁二烯-苯乙烯樹脂、聚苯乙烯-丙烯腈樹脂、熱塑性聚酯、熱塑性聚氨酯、聚甲醛樹脂、聚醚酮類、熱塑性聚醯亞胺、聚苯醚、聚苯硫醚、或其組合。
在另一優選例中,所述複合材料增強相的連續纖維的形式選自下組:單向纖維和織物纖維、或其組合。
在另一優選例中,所述連續纖維材料選自下組:玻璃纖維、碳纖維、有機聚合物纖維、天然纖維、或其組合。
在另一優選例中,所述內管的斷裂伸長率大於1%,抗拉強度為60-120mpa;
所述外管的抗拉強度大於120mpa,抗壓強度大於60mpa。
在另一優選例中,所述半管的厚度為2-8mm,所述半管的主管的直徑為d2,且所述d2為200-2000mm;
所述半管的支管的直徑為d1,且所述d1與所述d2的比值為0.5-1;
所述主管與所述支管之間的過渡圓角的半徑為r,所述支管的半徑為d3,且所述r與所述d3的比值為0.3-0.7。
在另一優選例中,所述內管的外徑形狀和所述半管的內徑形狀相同,且所述內管的外徑尺寸與所述半管的內徑尺寸相同;
所述內管的壁厚為1-4mm,所述膠槽的寬度為20-40mm;
所述膠粘劑的搭接剪切強度大於20mpa,斷裂伸長率大於5%。
在另一優選例中,所述法蘭接頭採用金屬材料,所述密封圈採用橡膠材料,所述限位槽沿軸向的截面為直角梯形,所述梯形斜邊槽沿軸向截面為鋸齒形。
本發明第二方面提供了一種三通結構件的製造方法,包括步驟:
(a)提供一內管、第一半管、第二半管、法蘭接頭和網狀電阻絲;
其中,所述的第一半管和第二半管是對稱的,並均設有翼板,所述翼板上設有用於通過螺栓進行固定的螺栓孔;
所述法蘭接頭設有限位槽、限位螺孔、密封槽和密封圈;
並且,所述的網狀電阻絲在通電時構成閉合迴路;
(b)將所述第一半管、所述第二半管進行對準,構成外管形狀,並使得所述第一半管的翼板和所述第二半管的翼板互相對準,並在互相對準的所述第一半管的翼板和第二半管的翼板之間放置所述網狀電阻絲;
(c)在對互相對準的所述的第一半管的翼板和第二半管的翼板施加壓力的條件下,對所述網狀電阻絲進行通電,所述的網狀電阻絲構成閉合迴路,從而使得所述的第一半管的翼板和第二半管的翼板發生熔融,形成熔融的翼板融合區;
(d)對所述網狀電阻絲進行斷電,並使得所述熔融的翼板融合區固化,從而形成固化的翼板融合區,得到外管;和
(e)將所述的內管、外管以及法蘭接頭進行裝配,形成三通結構件。
在另一優選例中,步驟(a)中還包括製造所述第一半管和第二半管的步驟(z):對坯料進行衝壓,從而形成所述第一半管和第二半管。
在另一優選例中,所述的步驟(z)包括以下子步驟:
(z1)制胚:採用熱壓法製備連續纖維增強的熱塑性複合材料層合板,之後將所述層合板裁切成t型坯料;
(z2)預熱:使用加熱設備,將所述層合板加熱至tm-30℃~tm+20℃;
(z3)轉移:快速轉移預熱後的所述層合板至模具中間,該過程在10s內完成;
(z4)壓料:壓塊下移將所述層合板壓緊在模具凹模上,不同的區域採用不同的壓緊力,選擇0.05-0.25mpa和0.1-0.5mpa兩個壓力區間,所述模具凹模和壓塊的溫度為tm-120℃~tm-50℃;
(z5)預壓實:模具凸模快速下移,當所述凸模快接近所述坯料時,控制下移速率為50mm/s-200mm/s,將所述坯料壓入所述模具凹模型腔內,所述模具凸模溫度為tm-120℃~tm-50℃;
(z6)保壓:模具間壓力增至1-4mpa,模具溫度和壓力不變並保持30-120s;
(z7)降溫開模:使用循環冷水將模具溫度降低至80℃以下,提起所述模具凸模並取出製件;
(z8)修邊制空:使用機械切割或水切割的方法切除步驟(z7)得到的製件的飛邊,並在翼板上制螺栓孔得到所述第一半管;和
(z9)採用步驟(z1)-步驟(z8)中相同的成型加工方法製造另外對稱的所述第二半管,步驟(z9)中採用的模具模腔形狀與步驟(z1)-步驟(z8)中採用的模具模腔形狀對稱。
在另一優選例中,所述t型坯料的橫邊寬度和所述半管的主管直徑之比為3.2-4.0;
所述t型坯料的縱邊寬度和所述半管的支管的直徑之比為3.2-4.0;
所述t型坯料橫邊與縱邊的過度圓角半徑與所述主管和支管的過渡圓角半徑之比等於所述t型坯料的橫邊寬度和所述半管的主管直徑之比;和/或
所述層合板中每一鋪層的纖維主方向與所述t型坯料的橫邊方向夾角為40°-50°。
在另一優選例中,步驟(a)中還包括製造所述內管的步驟(a1):採用短纖維增強熱塑性複合材料將所述內管注射成型。
在另一優選例中,步驟(a)中還包括製造所述法蘭接頭的步驟(a2):採用視管徑尺寸選擇鑄造、焊接和機械加工中一種或幾種加工方法將所述法蘭接頭加工而成。
在另一優選例中,步驟(z)中所述的坯料為t型坯料,且所述的坯料為連續纖維增強的熱塑性複合材料。
在另一優選例中,步驟(e)包括以下子步驟:
(e1)施膠:在所述內管的膠槽上施一定量的膠粘劑;
(e2)焊接、固化:將對稱的兩部分所述半管扣合在所述內管兩側,同時在所述半管的翼板間嵌入網狀電阻絲,將所述網狀電阻絲接通電源形成閉合迴路,並對所述半管的管壁及所述翼板施加壓力並保壓,待所述翼板表面的基體樹脂熔融後斷開電源迴路,卸下壓力;和
(e3)裝配法蘭接頭:將密封圈裝配在所述法蘭接頭上,並將所述法蘭接頭分別壓入所述半管的主管和支管以及所述內管中,並用螺栓通過螺栓孔和限位螺孔將所述半管和所述法蘭接頭固定。
附圖說明
圖1為實施例1的三通結構件的整體結構示意圖;
圖2為實施例1的三通結構件的主視圖;
圖3為實施例1的三通結構件的左視圖;
圖4為圖2的剖視圖;
圖5為實施例3的坯料的結構示意圖。
具體實施方式
本發明人經過廣泛而深入的研究,首次開發了一種三通結構件及製造方法。本發明採用高性能連續纖維增強的熱塑性複合材料作為外管,充分提高了三通管道的強度和耐腐蝕性並降低了三通管道的重量;本發明採用兩個對稱半管形成外管,通過法蘭接頭對內管和外管進行固定密封,提高了產品成品率;本發明採用以下技術方法:內管採用注射成型、法蘭接頭採用普通的金屬製造及加工方法、外管採用採用熱壓的方式成型,之後採用緊固系統將內管、外管和法蘭接頭各部分固定,大大提高了製造效率。
術語
如本文所用,術語「三通結構件」、「三通構件」、「三通」可互換使用,含義相同。
三通結構件
本發明提供了一種三通結構件,所述三通結構件包括:
一外管、一位於所述外管內的內管、以及用於對所述內管和所述外管進行固定密封的法蘭接頭。
本發明中,所述的外管由對稱的第一半管和第二半管構成,其中,各半管均設有翼板,所述翼板上設有用於通過螺栓進行固定的螺栓孔。
本發明中,所述的第一半管和第二半管通過翼板融合區結合為一體結構,其中所述的翼板融合區包括所述第一半管的翼板、第二半管的翼板、以及位於所述第一半管的翼板和所述第二半管的翼板之間的網狀電阻絲,其中所述的第一半管的翼板和第二半管的翼板融合固化在一起。
本發明中,所述法蘭接頭設有限位槽、限位螺孔、密封槽和密封圈。
本發明中,所述螺栓通過所述限位螺孔和所述螺栓孔將所述外管和所述法蘭接頭進行固定。
優選地,所述內管的外輪廓與所述外管的內輪廓是相匹配或適形的。
在另一優選例中,所述的內管與所述外管之間通過膠粘劑固定連接。
在另一優選例中,所述的法蘭接頭還設有斜邊槽。
在另一優選例中,所述的斜邊槽為梯形斜邊槽。
在另一優選例中,所述的第一半管的翼板和第二半管的翼板的大小和/或形狀是基本相同的。
在另一優選例中,所述的第一半管的翼板和第二半管的翼板的大小和/或形狀是相同的。
在另一優選例中,所述的內管的直徑為100-5000mm。
在另一優選例中,所述的翼板融合區是通過電阻焊接形成的。
在另一優選例中,所述內管上設有膠槽。
在另一優選例中,所述內管的材質為短纖維增強熱塑性複合材料。
在另一優選例中,所述複合材料的基體材料選自下組:聚乙烯、聚丙烯、聚氯乙烯、聚苯乙烯、聚醯胺樹脂、聚酯樹脂、聚丙烯腈-丁二烯-苯乙烯樹脂、聚苯乙烯-丙烯腈樹脂、熱塑性聚酯和熱塑性聚氨酯、或其組合。
在另一優選例中,所述複合材料的增強纖維選自下組:玻璃纖維、碳纖維、有機聚合物纖維、天然纖維、或其組合。
在另一優選例中,按複合材料的總質量計,所述增強纖維質量分數為2-30%。
在另一優選例中,所述增強纖維長度為1-5mm。
在另一優選例中,所述第一半管和第二半管的材質均為連續纖維增強熱塑性複合材料。
在另一優選例中,所述複合材料基體相的樹脂選自下組:聚丙烯、聚氯乙烯、聚苯乙烯、聚醯胺樹脂、聚酯樹脂、聚丙烯腈-丁二烯-苯乙烯樹脂、聚苯乙烯-丙烯腈樹脂、熱塑性聚酯、熱塑性聚氨酯、聚甲醛樹脂、聚醚酮類、熱塑性聚醯亞胺、聚苯醚、聚苯硫醚、或其組合。
在另一優選例中,所述複合材料增強相的連續纖維的形式選自下組:單向纖維和織物纖維、或其組合。
在另一優選例中,所述連續纖維材料選自下組:玻璃纖維、碳纖維、有機聚合物纖維、天然纖維、或其組合。
在另一優選例中,所述內管的斷裂伸長率大於1%,抗拉強度為60-120mpa;
所述外管的抗拉強度大於120mpa,抗壓強度大於60mpa。
在另一優選例中,所述半管的厚度為2-8mm,所述半管的主管的直徑為d2,且所述d2為200-2000mm;
所述半管的支管的直徑為d1,且所述d1與所述d2的比值為0.5-1;
所述主管與所述支管之間的過渡圓角的半徑為r,所述支管的半徑為d3,且所述r與所述d3的比值為0.3-0.7。
在另一優選例中,所述內管的外徑形狀和所述半管的內徑形狀相同,且所述內管的外徑尺寸與所述半管的內徑尺寸相同;
所述內管的壁厚為1-4mm,所述膠槽的寬度為20-40mm;
所述膠粘劑的搭接剪切強度大於20mpa,斷裂伸長率大於5%。
在另一優選例中,所述法蘭接頭採用金屬材料,所述密封圈採用橡膠材料,所述限位槽沿軸向的截面為直角梯形,所述梯形斜邊槽沿軸向截面為鋸齒形。
製造方法
本發明提供了一種三通結構件的製造方法,包括步驟:
(a)提供一內管、第一半管、第二半管、法蘭接頭和網狀電阻絲;
其中,所述的第一半管和第二半管是對稱的,並均設有翼板,所述翼板上設有用於通過螺栓進行固定的螺栓孔;
所述法蘭接頭設有限位槽、限位螺孔、密封槽和密封圈;
並且,所述的網狀電阻絲在通電時構成閉合迴路;
(b)將所述第一半管、所述第二半管進行對準,構成外管形狀,並使得所述第一半管的翼板和所述第二半管的翼板互相對準,並在互相對準的所述第一半管的翼板和第二半管的翼板之間放置所述網狀電阻絲;
(c)在對互相對準的所述的第一半管的翼板和第二半管的翼板施加壓力的條件下,對所述網狀電阻絲進行通電,所述的網狀電阻絲構成閉合迴路,從而使得所述的第一半管的翼板和第二半管的翼板發生熔融,形成熔融的翼板融合區;
(d)對所述網狀電阻絲進行斷電,並使得所述熔融的翼板融合區固化,從而形成固化的翼板融合區,得到外管;和
(e)將所述的內管、外管以及法蘭接頭進行裝配,形成三通結構件。
優選地,步驟(a)中還包括製造所述第一半管和第二半管的步驟(z):對坯料進行衝壓,從而形成所述第一半管和第二半管。
在另一優選例中,所述的步驟(z)包括以下子步驟:
(z1)制胚:採用熱壓法製備連續纖維增強的熱塑性複合材料層合板,之後將所述層合板裁切成t型坯料;
(z2)預熱:使用加熱設備,將所述層合板加熱至tm-30℃~tm+20℃;
(z3)轉移:快速轉移預熱後的所述層合板至模具中間,該過程在10s內完成;
(z4)壓料:壓塊下移將所述層合板壓緊在模具凹模上,不同的區域採用不同的壓緊力,選擇0.05-0.25mpa和0.1-0.5mpa兩個壓力區間,所述模具凹模和壓塊的溫度為tm-120℃~tm-50℃;
(z5)預壓實:模具凸模快速下移,當所述凸模快接近所述坯料時,控制下移速率為50mm/s-200mm/s,將所述坯料壓入所述模具凹模型腔內,所述模具凸模溫度為tm-120℃~tm-50℃;
(z6)保壓:模具間壓力增至1-4mpa,模具溫度和壓力不變並保持30-120s;
(z7)降溫開模:使用循環冷水將模具溫度降低至80℃以下,提起所述模具凸模並取出製件;
(z8)修邊制空:使用機械切割或水切割的方法切除步驟(z7)得到的製件的飛邊,並在翼板上制螺栓孔得到所述第一半管;和
(z9)採用步驟(z1)-步驟(z8)中相同的成型加工方法製造另外對稱的所述第二半管,步驟(z9)中採用的模具模腔形狀與步驟(z1)-步驟(z8)中採用的模具模腔形狀對稱。
在另一優選例中,所述t型坯料的橫邊寬度和所述半管的主管直徑之比為3.2-4.0;
所述t型坯料的縱邊寬度和所述半管的支管的直徑之比為3.2-4.0;
所述t型坯料橫邊與縱邊的過度圓角半徑與所述主管和支管的過渡圓角半徑之比等於所述t型坯料的橫邊寬度和所述半管的主管直徑之比;和/或
所述層合板中每一鋪層的纖維主方向與所述t型坯料的橫邊方向夾角為40°-50°。
在另一優選例中,步驟(a)中還包括製造所述內管的步驟(a1):採用短纖維增強熱塑性複合材料將所述內管注射成型。
在另一優選例中,步驟(a)中還包括製造所述法蘭接頭的步驟(a2):採用視管徑尺寸選擇鑄造、焊接和機械加工中一種或幾種加工方法將所述法蘭接頭加工而成。
在另一優選例中,步驟(z)中所述的坯料為t型坯料,且所述的坯料為連續纖維增強的熱塑性複合材料。
在另一優選例中,步驟(e)包括以下子步驟:
(e1)施膠:在所述內管的膠槽上施一定量的膠粘劑;
(e2)焊接、固化:將對稱的兩部分所述半管扣合在所述內管兩側,同時在所述半管的翼板間嵌入網狀電阻絲,將所述網狀電阻絲接通電源形成閉合迴路,並對所述半管的管壁及所述翼板施加壓力並保壓,待所述翼板表面的基體樹脂熔融後斷開電源迴路,卸下壓力;和
(e3)裝配法蘭接頭:將密封圈裝配在所述法蘭接頭上,並將所述法蘭接頭分別壓入所述半管的主管和支管以及所述內管中,並用螺栓通過螺栓孔和限位螺孔將所述半管和所述法蘭接頭固定。
本發明的主要優點包括:
(a)本發明充分利用了熱塑性樹脂基體的氣密性、耐腐蝕性、和質量輕的特點,防止管內被輸送液體的洩露以及管路被內部液體腐蝕;
(b)本發明充分利用連續纖維增強熱塑性複合材料的高強度、高韌性、耐腐蝕性,充分提高了三通管道的耐衝擊性、抗裂、抗腐蝕性以及承載能力,保證三通管道抵抗來自土壤、海水等條件的壓力和侵蝕,提高了三通管道的使用壽命,降低的維修成本,具有顯著的經濟效益;
(c)本發明利用金屬接固定內外管,進一步提高了三通的剛度和整體性能,法蘭接頭採用法蘭的形式與其他管道連接,使得本發明更具有通用性;
(d)本發明提供的製造方法,具有快速、自動化程度高、低成本的特點,尤其是針對外管連續纖維增強熱塑性複合材料的成型方法,不僅效率高,而且通過三通的幾何尺寸設計、鋪層設計及其他成型工藝參數的設計使製品的具有較高成品率以及力學性能;
(e)內管、外管以及接頭之間的連接和固定方法很大程度提高了三通整體強度和剛度;
(f)本發明具有優良的力學性能、耐久性能,同時生產效率高、成本低、便於運輸和安裝,特別適用於耐久性要求很高的海洋、河流、地下等環境的管道。
下面結合具體實施例,進一步闡述本發明。應理解,這些實施例僅用於說明本發明而不用於限制本發明的範圍。下列實施例中未註明具體條件的實驗方法,通常按照常規條件,或按照製造廠商所建議的條件。除非另外說明,否則百分比和份數是重量百分比和重量份數。
需要說明的是,在本專利的權利要求和說明書中,諸如第一和第二等之類的關係術語僅僅用來將一個實體或者操作與另一個實體或操作區分開來,而不一定要求或者暗示這些實體或操作之間存在任何這種實際的關係或者順序。而且,術語「包括」、「包含」或者其任何其他變體意在涵蓋非排他性的包含,從而使得包括一系列要素的過程、方法、物品或者設備不僅包括那些要素,而且還包括沒有明確列出的其他要素,或者是還包括為這種過程、方法、物品或者設備所固有的要素。在沒有更多限制的情況下,由語句「包括一個」限定的要素,並不排除在包括所述要素的過程、方法、物品或者設備中還存在另外的相同要素。
實施例1
本實施例提供了一種三通結構件,圖1為本實施例的三通結構件整體結構示意圖,圖2為本實施例的三通結構件的主視圖,圖3為本實施例的三通結構件的左視圖,圖4為圖2的剖視圖。
如圖1-4所示,所述三通結構件包括:
一外管、一位於所述外管內的內管3、以及用於對所述內管3和所述外管進行固定密封的法蘭接頭1。
本實施例中,所述的外管由對稱的第一半管2和第二半管16構成,其中,各半管均設有翼板,所述翼板上設有用於通過螺栓進行固定的螺栓孔9。
所述的第一半管2和第二半管16通過翼板融合區結合為一體結構,其中所述的翼板融合區包括所述第一半管2的翼板4、第二半管16的翼板17、以及位於所述第一半管2的翼板4和所述第二半管16的翼板17之間的網狀電阻絲15,其中所述的第一半管2的翼板4和第二半管16的翼板17融合固化在一起。
所述法蘭接頭1設有限位槽14、限位螺孔5、密封槽10和密封圈11。
所述螺栓通過所述限位螺孔5和所述螺栓孔9將所述外管和所述法蘭接頭1進行固定。
本實施例中,所述的法蘭接頭1還設有斜邊槽,所述的斜邊槽為梯形斜邊槽12。
本實施例中,所述內管3上設有膠槽8。
實施例2
本實施例提供了一種三通結構件,與實施例1提供的三通結構件基本相同,不同之處在於:
本實施例中,所述內管3的外輪廓與所述外管的內輪廓是相匹配或適形的;
所述的內管3與所述外管之間通過膠粘劑13固定連接;
所述的第一半管2的翼板4和第二半管16的翼板17的大小和形狀是基本相同的;
所述的第一半管2的翼板4和第二半管16的翼板17的大小和形狀是相同的;
所述的內管3的直徑為500mm;
所述的翼板融合區是通過電阻焊接形成的;
所述內管3的材質為短纖維增強熱塑性複合材料,所述複合材料的基體材料為聚乙烯,所述複合材料的增強纖維為有機聚合物纖維,按複合材料的總質量計,所述增強纖維質量分數為10%,所述增強纖維長度為3mm;
所述第一半管2和第二半管16的材質均為連續纖維增強熱塑性複合材料,所述複合材料基體相的樹脂為聚丙烯,所述複合材料增強相的連續纖維的形式為單向纖維和織物纖維的組合,所述連續纖維材料為玻璃纖維和有機聚合物纖維的組合;
所述內管3的斷裂伸長率為5%,抗拉強度為80mpa;
所述外管的抗拉強度為130mpa,抗壓強度為70mpa;
所述半管的厚度為6mm,所述半管的主管7的直徑為d2,且所述d2為500mm;
所述半管的支管6的直徑為d1,且所述d1與所述d2的比值為0.6;
所述主管7與所述支管6之間的過渡圓角的半徑為r,所述支管6的半徑為d3,且所述r與所述d3的比值為0.5;
所述內管3的外徑形狀和所述半管的內徑形狀相同,且所述內管3的外徑尺寸與所述半管的內徑尺寸相同;
所述內管3的壁厚為3mm,所述膠槽8的寬度為30mm;
所述膠粘劑13的搭接剪切強度為30mpa,斷裂伸長率為8%;
所述法蘭接頭1採用金屬材料,所述密封圈11採用橡膠材料,所述限位槽14沿軸向的截面為直角梯形,所述梯形斜邊槽12沿軸向截面為鋸齒形。
實施例3
本實施例提供了一種三通結構件的製造方法,包括步驟:
(a)提供一內管3、第一半管2、第二半管16、法蘭接頭1和網狀電阻絲15;
其中,所述的第一半管2和第二半管16是對稱的,並均設有翼板,所述翼板上設有用於通過螺栓進行固定的螺栓孔9;
所述法蘭接頭1設有限位槽14、限位螺孔5、密封槽10和密封圈11;
並且,所述的網狀電阻絲15在通電時構成閉合迴路;
(b)將所述第一半管2、所述第二半管16進行對準,構成外管形狀,並使得所述第一半管2的翼板4和所述第二半管16的翼板17互相對準,並在互相對準的所述第一半管2的翼板4和第二半管16的翼板17之間放置所述網狀電阻絲15;
(c)在對互相對準的所述的第一半管2的翼板4和第二半管16的翼板17施加壓力的條件下,對所述網狀電阻絲15進行通電,所述的網狀電阻絲15構成閉合迴路,從而使得所述的第一半管2的翼板4和第二半管16的翼板17發生熔融,形成熔融的翼板融合區;
(d)對所述網狀電阻絲15進行斷電,並使得所述熔融的翼板融合區固化,從而形成固化的翼板融合區,得到外管;和
(e)將所述的內管3、外管以及法蘭接頭1進行裝配,形成三通結構件。
本實施例中,步驟(a)中還包括製造所述第一半管2和第二半管16的步驟(z):對坯料進行衝壓,從而形成所述第一半管2和第二半管16。
本實施例中,所述的步驟(z)包括以下子步驟:
(z1)制胚:採用熱壓法製備連續纖維增強的熱塑性複合材料層合板,之後將所述層合板裁切成t型坯料,圖5為所述坯料的結構示意圖;
(z2)預熱:使用加熱設備,將所述層合板加熱至tm-30℃~tm+20℃;
(z3)轉移:快速轉移預熱後的所述層合板至模具中間,該過程在10s內完成;
(z4)壓料:壓塊下移將所述層合板壓緊在模具凹模上,不同的區域採用不同的壓緊力,選擇0.05-0.25mpa和0.1-0.5mpa兩個壓力區間,所述模具凹模和壓塊的溫度為tm-120℃~tm-50℃;
(z5)預壓實:模具凸模快速下移,當所述凸模快接近所述坯料時,控制下移速率為50mm/s-200mm/s,將所述坯料壓入所述模具凹模型腔內,所述模具凸模溫度為tm-120℃~tm-50℃;
(z6)保壓:模具間壓力增至1-4mpa,模具溫度和壓力不變並保持30-120s;
(z7)降溫開模:使用循環冷水將模具溫度降低至80℃以下,提起所述模具凸模並取出製件;
(z8)修邊制空:使用機械切割或水切割的方法切除步驟(z7)得到的製件的飛邊,並在翼板上制螺栓孔9得到所述第一半管2;和
(z9)採用步驟(z1)-步驟(z8)中相同的成型加工方法製造另外對稱的所述第二半管16,步驟(z9)中採用的模具模腔形狀與步驟(z1)-步驟(z8)中採用的模具模腔形狀對稱。
本實施例中,所述t型坯料的橫邊寬度和所述半管的主管7直徑之比為3.2-4.0;
所述t型坯料的縱邊寬度和所述半管的支管6的直徑之比為3.2-4.0;
所述t型坯料橫邊與縱邊的過度圓角半徑與所述主管7和支管6的過渡圓角半徑之比等於所述t型坯料的橫邊寬度和所述半管的主管7直徑之比;和/或
所述層合板中每一鋪層的纖維主方向與所述t型坯料的橫邊方向夾角為40°-50°。
本實施例中,步驟(a)中還包括製造所述內管3的步驟(a1):採用短纖維增強熱塑性複合材料將所述內管3注射成型。
本實施例中,步驟(a)中還包括製造所述法蘭接頭1的步驟(a2):採用視管徑尺寸選擇鑄造、焊接和機械加工中一種或幾種加工方法將所述法蘭接頭1加工而成。
本實施例中,步驟(z)中所述的坯料為t型坯料,且所述的坯料為連續纖維增強的熱塑性複合材料。
本實施例中,步驟(e)包括以下子步驟:
(e1)施膠:在所述內管3的膠槽8上施一定量的膠粘劑13;
(e2)焊接、固化:將對稱的兩部分所述半管扣合在所述內管3兩側,同時在所述半管的翼板間嵌入網狀電阻絲15,將所述網狀電阻絲15接通電源形成閉合迴路,並對所述半管的管壁及所述翼板施加壓力並保壓,待所述翼板表面的基體樹脂熔融後斷開電源迴路,卸下壓力;和
(e3)裝配法蘭接頭1:將密封圈11裝配在所述法蘭接頭1上,並將所述法蘭接頭1分別壓入所述半管的主管7和支管6以及所述內管3中,並用螺栓通過螺栓孔9和限位螺孔5將所述半管和所述法蘭接頭1固定。
在本發明提及的所有文獻都在本申請中引用作為參考,就如同每一篇文獻被單獨引用作為參考那樣。此外應理解,在閱讀了本發明的上述講授內容之後,本領域技術人員可以對本發明作各種改動或修改,這些等價形式同樣落於本申請所附權利要求書所限定的範圍。