含金屬內襯碳纖維複合材料身管及其預應力施加方法與流程
2023-06-09 15:07:36 2
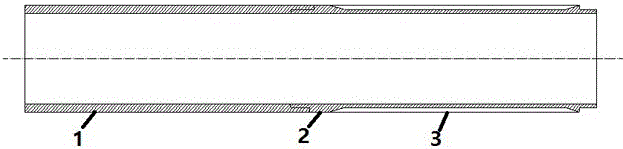
本發明涉及一種含有金屬內襯碳纖維複合材料承壓身管結構及相應的預應力施加方法。
背景技術:
現代軍事技術的發展要求未來武器裝備具有輕便、機動、靈活快速反應等特點,因此必須大力開發新型結構和功能材料。其中纖維複合材料具有輕質、高強、不鏽蝕、耐腐蝕、耐疲勞及可設計性好等優點,是目前應用最為廣泛的一類新型材料。但纖維複合材料的抗燒蝕能力和密閉性較差,所以一般在纖維複合材料發射筒的內壁附加一層金屬材料,這種含金屬內襯的纖維複合材料發射筒不僅質量輕、可設計性強,還具有很好的密封性,可滿足各種武器平臺對發射筒的使用要求,具有廣泛的應用前景。目前我國部隊採用的發射筒身管仍採用全金屬製作,過重的發射筒不方便戰士攜帶,作戰的靈活機動性也較差。
如果直接在金屬內襯外表面纏繞碳纖維複合材料來製作身管,也存在一些技術上的不足:
其一:金屬內襯外表面纏繞的複合材料層需要高溫固化,如採用熱固性聚醯亞胺樹脂,固化溫度達三百度以上,在這麼高的固化溫度下,金屬內襯發生膨脹,而外表面的碳纖維複合材料層對溫度不敏感,高溫下基本不發生膨脹,金屬內襯熱膨脹後將外表面纏繞的碳纖維複合材料層撐開,固化冷卻後,金屬內襯發生收縮,容易在複合材料層與金屬內襯界面產生間隙,發生結合不緊密的情況,導致碳纖維複合材料層無法起到加固身管環向強度的作用。
其二:金屬內襯的模量一般為200GPa,屈服強度為1280MPa,而碳纖維(T800)複合材料層環向模量一般小於金屬的模量,一般為180GPa,強度為3000MPa左右,因為複合材料的環向模量小於金屬內襯,所以在實彈發射時,碳纖維複合材料層上的環向應力小於金屬內襯上的環向應力更遠遠低於其自身強度,造成材料的浪費。
技術實現要素:
本發明所要解決的技術問題是針對上述現有技術提供一種含金屬內襯碳纖維複合材料身管及其預應力施加方法,提高金屬內襯與作為加固件的碳纖維複合材料層之間的接觸緊密性。利用金屬塑性變形的特性使金屬內襯在外部高壓作用下環向發生不可恢復的塑性變形,同時金屬內襯外的碳纖維複合材料層保持彈性變形狀態,產生環向拉應力,從而使金屬內襯在碳纖維複合材料層的作用下產生環向壓應力。當金屬內襯內腔受到壓力時,環向壓應力將抵消部分金屬內襯承受的拉應力,從而改善金屬內襯的受力狀況。而且,如果金屬內襯中有細微裂紋存在,由於環向壓應力的存在,可延緩其發展過程,從而提高身管耐疲勞性能。
本發明解決上述問題所採用的技術方案為:一種金屬內襯纏繞碳纖維複合材料身管,包括金屬內襯、金屬尾管和碳纖維複合材料層,所述金屬內襯和金屬尾管銜接,所述金屬內襯的筒身外周成型有環形凹槽,所述碳纖維複合材料層對應纏繞在所述環形凹槽內,並且所述碳纖維複合材料層具有環向壓緊該金屬內襯的趨勢。
金屬內襯的兩端設置有連接螺紋,若干金屬內襯之間通過螺紋實現依次連接,金屬尾管與末端金屬內襯相連接。金屬尾管設置在身管的末端部位,無需碳纖維複合材料層的加固。
本發明解決另一技術問題所採用的技術方案是提供一種含金屬內襯碳纖維複合材料身管預應力施加方法,提高金屬內襯與碳纖維複合材料層間的接觸緊密性,將碳纖維複合材料均勻環向纏繞至金屬內襯的環形凹槽上,高溫固化完成後,將金屬內襯兩端暫時密封,用水壓機對含金屬內襯碳纖維複合材料身管內腔進行加壓,加壓過程中記錄水壓與碳纖維複合材料層的環向應變,用於判斷碳纖維複合材料層與金屬內襯界面之間的鬆緊狀況及金屬內襯的應力狀態;假設金屬內襯的屈服強度為1280MPa,彈性模量為200GPa,碳纖維(T800)複合材料層環向強度為3000MPa,環向模量為180GPa,則金屬內襯發生彈性應變的最大值為0.64%,碳纖維複合材料層的極限應變為1.67%。當金屬內襯被判斷出發生塑性變形並且碳纖維複合材料層所產生的環向變形量大於金屬內襯的環向彈性變形量的最大值時,洩壓,可以通過調整碳纖維複合材料層產生的環向變形量與0.64%的差值的大小來調整金屬內襯與碳纖維複合材料層間預應力的大小;洩壓完成後,測量金屬內襯內壁尺寸,並車加工至需要的口徑;最後將做好的纏繞有碳纖維複合材料層的若干金屬內襯依次首尾連接,並將金屬尾管連接到末端的金屬內襯的端部,即為身管。
與現有技術相比,本發明具有如下特點:
1、本發明的身管可作為炮筒使用,身管採用分段連接設計方式,若干帶有碳纖維複合材料層的金屬內襯之間通過螺紋連接,再依次與金屬尾管及支架等組裝,可減輕身管每段的重量,便於戰士攜帶,纏繞碳纖維複合材料層的金屬內襯結構堅固,便於進行打壓工序。
2、本發明的提高金屬內襯和碳纖維複合材料層間接觸緊密性的工藝,利用了金屬內襯在水壓作用下發生可恢復的彈性形變和不可恢復的塑性形變的特性,使碳纖維複合材料層對金屬內襯產生了環向預應力,從而使兩者接觸更加緊密,碳纖維複合材料層受到一個環向拉應力,而金屬內襯受到一個環向壓應力,相應的身管在作為炮筒使用的情況下,當發射使炮筒內產生高膛壓時,金屬內襯受到的環向壓應力將抵消部分火藥氣體帶來的巨大拉應力,從而改善金屬內襯的受力狀況。如果金屬內襯中有細微裂紋存在,由於壓應力的存在,可延緩其發展過程,從而提高身管的抗疲勞性能。
3、本發明的身管可以使碳纖維複合材料層更多地承擔環向承壓負荷,充分發揮碳纖維複合材料高強度的優勢,使整個身管結構受力更加合理,使採用低牌號低模量(例如T700級)碳纖維進行纏繞成為可能性,提高了產品的經濟性。
附圖說明
圖1為本發明實施例中身管的後半部分結構示意圖;
圖2為本發明實施例中身管的前半部分結構示意圖;
圖3為本發明實施例中未車削螺紋的金屬內襯和碳纖維複合材料層的組裝示意圖。
具體實施方式
以下結合附圖實施例對本發明作進一步詳細描述。
如圖1至3所示,本實施例中的身管,包括若干金屬內襯2和與金屬內襯數量相等的碳纖維複合材料層3和金屬尾管1,各金屬內襯2的兩端分別設置有(內、外)連接螺紋2.2,若干金屬內襯2之間依次通過螺紋首尾連接,金屬尾管1與末端金屬內襯2連接,金屬內襯2的筒身外周成型有環形凹槽2.1,碳纖維複合材料一一對應纏繞在各金屬內襯2的環形凹槽2.1內以形成前述的碳纖維複合材料層3,並且所述碳纖維複合材料層3始終具有環向壓緊該金屬內襯2的趨勢,金屬內襯2兩端作為待車削成上述連接螺紋2.2的相應部位4。
身管採用了分段組裝的設計方式,可減輕身管每段的重量,便於戰士攜帶,纏繞碳纖維複合材料層的金屬內襯結構堅固,耐衝擊壓能力強,提高了身管的使用壽命。
身管的製造方法具體為,將碳纖維複合材料纏繞至金屬內襯的環形凹槽上,高溫固化後,將金屬內襯兩端暫時密封,用水壓機對含金屬內襯碳纖維複合材料身管內腔進行加壓,加壓過程中記錄水壓與碳纖維複合材料層的環向應變,用於判斷碳纖維複合材料層與金屬內襯界面之間的鬆緊狀況及金屬內襯的應力狀態;當金屬內襯被判斷出發生塑性變形並且碳纖維複合材料層所產生的環向變形量大於金屬內襯的環向彈性變形量的最大值時,洩壓,可以通過調整碳纖維複合材料層產生的環向變形量與金屬內襯產生的環向彈性變形量差值的大小來調整金屬內襯與碳纖維複合材料層間預應力的大小;洩壓完成後,去掉兩端密封裝置,測量金屬內襯內壁尺寸,並車加工至需要的口徑;最後將做好的纏有碳纖維複合材料層的若干金屬內襯依次首尾連接,並將金屬尾管連接到末端金屬內襯的端部,即為身管。
上述身管的製造工藝使碳纖維複合材料層與金屬內襯之間產生了環向預應力,從而使兩者接觸更加緊密,碳纖維複合材料層受到一個環向拉應力,而金屬內襯受到一個環向壓應力,從而改善金屬內襯的受力狀況。