一種氣液分離輸送泵的製作方法
2023-05-29 23:55:02 1
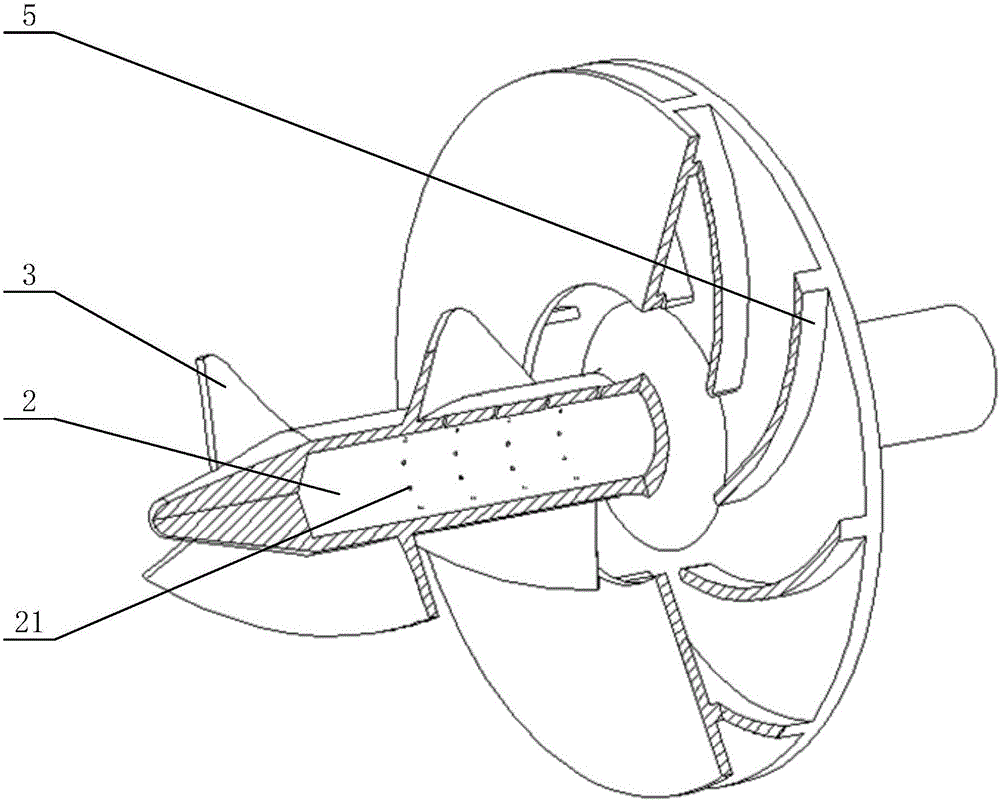
本發明涉及流體輸送技術領域,特別是涉及一種氣液分離輸送泵。
背景技術:
目前,各行業中常需要輸送含有較多氣體的液體介質,而液體介質中氣體的含量很大程度上影響著輸送效率。當氣體的含量達到或超過10%的狀態下,會造成液體無法通過液壓泵實現輸送,因此,需要增設單獨的氣液分離輔助設備,將液體介質中的氣液進行分離後再進行輸送,這造成了輸送成本的增加,且結構複雜,應用便捷性低。
以上現有技術中,對於液體輸送的成本高,結構設置複雜,以及應用便捷性低等缺陷是本領域技術人員需要解決的技術問題。
技術實現要素:
本發明的目的是提供一種氣液分離輸送泵,通過本發明的應用將顯著提高對於液體輸送便捷性,同時降低成本和結構複雜性。
為解決上述技術問題,本發明提供一種氣液分離輸送泵,包括筒狀殼體、能夠轉動的排氣管、螺旋葉片、蝸殼和直葉片,其中:
所述蝸殼接於所述筒狀殼體的尾端,且相互連通,所述筒狀殼體的首端設有輸入口;
所述排氣管沿縱向設於所述筒狀殼體與所述蝸殼的中部,在所述排氣管的側壁設有進氣孔,在所述排氣管的尾端設有與所述進氣孔連通的排氣口,所述排氣口設於所述蝸殼的外側;
所述螺旋葉片安裝於所述排氣管,且位於所述筒狀殼體內,所述直葉片安裝於所述排氣管,且位於所述蝸殼內,所述蝸殼的徑向設有用於排出液體的排液口。
可選地,所述進氣孔的數量為多個,多個所述進氣孔沿縱向間隔排列設置,且沿所述排氣管的徑向周圈均布排列設置。
可選地,所述螺旋葉片的數量為多個,各所述螺旋葉片沿軸向依次排列於所述排氣管,相鄰的所述螺旋葉片之間皆設有所述進氣孔。
可選地,所述螺旋葉片的數量為3個。
在一個關於氣液分離輸送泵的實施方式中,氣液分離輸送泵包括筒狀殼體、能夠轉動的排氣管、螺旋葉片、蝸殼和直葉片,蝸殼接於筒狀殼體的尾端,且相互連通,筒狀殼體的首端設有用於輸入流體介質的輸入口,排氣管沿縱向設於筒狀殼體與蝸殼的中部,這裡的中部,是指蝸殼與筒狀殼體相連結構的軸向位置,在排氣管的側壁設有進氣孔,在排氣管的尾端設有與進氣孔連通的排氣口,排氣口設於蝸殼的外側。螺旋葉片安裝於排氣管,且位於筒狀殼體內,直葉片安裝於排氣管,且位於蝸殼內,蝸殼的徑向設有用於排出液體的排液口。通過以上結構設置,在混雜著氣體的氣液混合物通過輸入口流入筒狀殼體內部後,通過排氣管的轉動,排氣管帶動螺旋葉片和直葉片同步轉動,隨著螺旋葉片的轉動,使得氣液混合物被螺旋葉片攪動,這一方面使得氣液混合物產生了沿軸向前進的作用力,形成軸向流動,另一方面,氣液混合物因螺旋葉片的攪動而產生了繞軸向轉動的離心力,隨著離心力的作用,氣液混合物具有向徑向邊側流動的趨勢,這一過程中,氣液混合物中比重較大的液體受到的離心力相比於比重小的氣體更大,因此,液體流動至徑向邊側,而氣體在沿軸向移動的同時,逐漸向中部匯聚,因中部的排氣管的側壁上設有進氣孔,則氣體進入進氣孔,並繼續沿軸向移動,最終,氣體從排氣口排出,因排氣口設在蝸殼外側,則氣體從筒狀殼體和蝸殼的整體空間內排出。而對於液體,液體在徑向邊側,即,沿著筒狀殼體的內沿逐步移動至蝸殼位置,隨著直葉片的轉動,使得液體被直葉片推入蝸殼徑向的排液口,完成氣液分離輸送泵對於液體的輸送,在這一輸送過程中,通過結構設置,利用離心力的物理原理,將氣體從氣液混合物中進行了分離,通過蝸殼的排液口輸出的液體中的氣體得到了排除。由此,在未設置獨立的氣液分離輔助設備的狀態下,通過本氣液分離輸送泵的應用便同時完成了輸送和氣液分離的作用,這使得液體輸送便捷性得到了提高,同時降低了應用成本和結構複雜性。
附圖說明
為了更清楚地說明本發明實施例或現有技術中的技術方案,下面將對實施例或現有技術描述中所需要使用的附圖作簡單地介紹,顯而易見地,下面描述中的附圖僅僅是本發明的實施例,對於本領域普通技術人員來講,在不付出創造性勞動的前提下,還可以根據提供的附圖獲得其他的附圖。
圖1為本發明結構第一示意圖;
圖2為本發明結構第二示意圖;
圖3為本發明結構分解示意圖;
圖1至圖3中:筒狀殼體—1、排氣管—2、進氣孔—21、排氣口—22、螺旋葉片—3、蝸殼—4、排液口—41、直葉片—5。
具體實施方式
本發明的核心是提供一種氣液分離輸送泵,通過本發明的應用將顯著提高對於液體輸送便捷性,同時降低成本和結構複雜性。
下面將結合本發明實施例中的附圖,對本發明實施例中的技術方案進行清楚、完整地描述,顯然,所描述的實施例僅僅是本發明一部分實施例,而不是全部的實施例。基於本發明中的實施例,本領域普通技術人員在沒有做出創造性勞動前提下所獲得的所有其他實施例,都屬於本發明保護的範圍。
請參考圖1至圖3,圖1為本發明結構第一示意圖;圖2為本發明結構第二示意圖;圖3為本發明結構分解示意圖。
根據圖中所示,氣液分離輸送泵包括筒狀殼體1、能夠轉動的排氣管2、螺旋葉片3、蝸殼4和直葉片5。蝸殼4接於筒狀殼體1的尾端,且相互連通,筒狀殼體1的首端設有輸入口,排氣管2沿縱向設於筒狀殼體1與蝸殼4的中部,在排氣管2的側壁設有進氣孔21,在排氣管2的尾端設有與進氣孔21連通的排氣口22,排氣口22設於蝸殼4的外側,螺旋葉片3安裝於排氣管2,且位於筒狀殼體1內,直葉片5安裝於排氣管2,且位於蝸殼4內,蝸殼4的徑向設有用於排出液體的排液口41。本實施例中,通過結構設置,在排氣管2、螺旋葉片3和直葉片5構成的整體結構進行單一同步的轉動狀態下,便利用了離心力的物理原理使得比重小的氣體靠近中部傳送,進而通過進入進氣孔21並從排氣口22被排放,而比重相對較大的液體靠近筒狀殼體1的徑向內壁傳送,進而通過殼體4的排液口41被排出,通過本氣液分離輸送泵的單一應用,單一轉動便同時實現了輸送和氣液分離,由此,本氣液分離輸送泵的應用顯著提高了輸送的便捷性,同時降低了結構複雜性和使用成本。
上述實施例的基礎上,對於排氣管2上的進氣管21,優選的設置結構為設置多個進氣孔21,同時,將多個進氣孔21在縱向上依次間隔排列設置,且在排氣管2的徑向周圈均部排列設置,由此,使得轉動過程中,向中部匯集的氣體能夠在軸向移動的各位置,且在排氣管2的周圈各位置皆能夠通過進氣孔21進入排氣管2中,進而最終通過排氣口22排出,本實施例中,對於多個進氣口21的設置,相當於在排氣管2的整體結構中將進氣孔21進行了沿軸向和周圈的陣列布置,這使得氣液分離的效果進一步得到了提高。
進一步地,設置螺旋葉片3的數量為多個,使各螺旋葉片3沿軸向依次排列於排氣管2,同時,在相鄰的螺旋葉片3之間皆設有進氣孔21。對於每一個螺旋葉片3,在轉動過程中都是對於流體的實際驅動結構,多個螺旋葉片3沿軸向依次排列,類似於在軸向的每一段位置設置一級對於流體的驅動,每一螺旋葉片3對於液體的攪動都增強了離心力,這種狀態下,在每個螺旋葉片3的位置都設置進氣孔21,這使得受到離心力的狀態下,氣體能夠即刻通過進氣孔21流入中部的排氣管2內,這使得氣液分離的效果進一步得到提高。這其中,比較優選的數量是設置三管個螺旋葉片3。
對所公開的實施例的上述說明,使本領域專業技術人員能夠實現或使用本發明。對這些實施例的多種修改對本領域的專業技術人員來說將是顯而易見的,本文中所定義的一般原理可以在不脫離本發明的精神或範圍的情況下,在其它實施例中實現。因此,本發明將不會被限制於本文所示的這些實施例,而是要符合與本文所公開的原理和新穎特點相一致的最寬的範圍。