自動成形設備的製作方法
2023-06-08 17:11:01
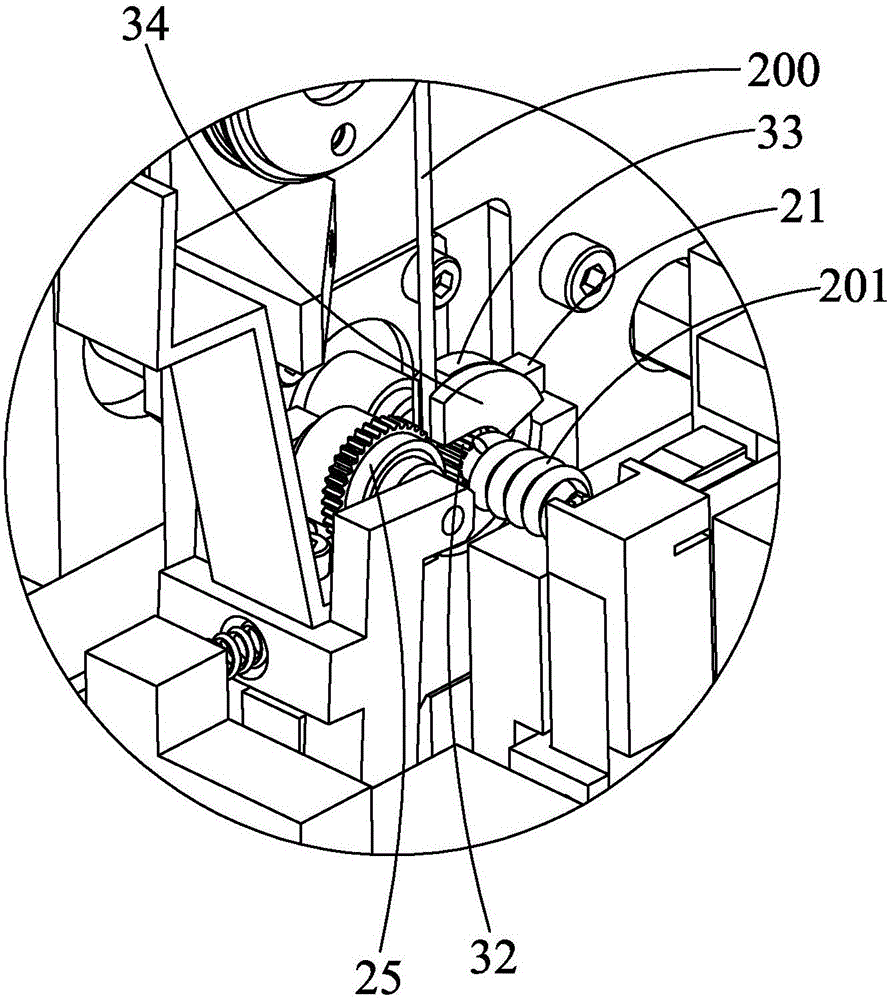
本發明涉及一種自動化加工設備,尤其涉及一種將金屬絲加工為環形金屬圈的自動成形設備。
背景技術:
隨著電子行業的發展、工業自動化的興起以及人力成本的越來越高,手工作業已經無法滿足大規模化生產的需求,高成本的自動化加工生產也越來越失去競爭優勢,此種情況催生出行業對於低成本、高效率的自動化製造的迫切需求。
目前市場上很少有自動成形環狀金屬圈的機構,多半是手工捲成特定形狀,耗費人力、產量低。鑑於此,有必要設計新的自動成形設備。
技術實現要素:
本發明目的在於提供一種具有節省人力、節省成本,批量生產,一致性好,以適應大規模工業生產的自動成形設備。
本發明採用的技術方案為:一種自動成形設備,用以把金屬絲成形為環形金屬圈,其包括機架及分別固定於機架上的繞圈機構、裁切機構、整平機構、出料箱,所述機架上樞接有用以纏繞金屬絲的放料盤,所述繞圈機構包括電機、轉動軸及抵推塊,所述電機用以驅動轉動軸帶動金屬絲旋轉後纏繞在轉動軸上,所述抵推塊設有供轉動軸向前穿過的圓孔,所述抵推塊前端面凹設有位於圓孔周緣的收容槽,所述收容槽內側設有朝向前方的螺旋面,所述收容槽的深度沿圓周線逐漸變深或變淺,所述裁切機構包括一裁切氣缸、在裁切氣缸驅動下左右移動的活動臂及固定於活動臂上的裁切刀,所述裁切刀位於轉動軸的一側,所述整平機構包括一整平氣缸、一按壓塊、連接在整平氣缸與按壓塊之間的聯結軸及支架,所述按壓塊設有位於轉動軸下方的整平凸部,所述支架包括一導引塊、一落料塊及一支撐塊,所述導引塊內側設有上下貫穿的導引槽,所述落料塊內側設有上下貫穿的落料槽,所述導引槽位於落料槽上方,兩者相鄰設置,分別在上下方向上呈開口朝向繞圈機構的U形,所述支撐塊固定於落料塊內側,並且遮擋於落料槽後方,但位於整平凸部下方,所述支撐塊向前超過整平凸部,落料槽向上超出支撐塊,所述出料箱位於落料槽下方。
作為本發明的進一步改進,所述轉動軸外側設有增加轉動軸與金屬絲間摩擦力的輪齒。
作為本發明的進一步改進,所述繞圈機構還包括固定於抵推塊前表面用以限制金屬絲向前偏移的限制塊。
作為本發明的進一步改進,所述支撐塊與整平凸部上下間隔開。
作為本發明的進一步改進,所述自動成形設備包括固定於機架上的一第一定位板,所述第一定位塊設有一弧形凹部及遮擋於凹部後方的定位板,所述定位板具有供轉動軸向前穿過的圓孔,抵推塊固定於凹部內,向後貼靠在定位板上。
作為本發明的進一步改進,所述自動成形設備包括一矯直機構,所述矯直機構包括一第一定位塊、一活動塊、一手柄及一張緊輪,第一定位塊固定於機架上,所述活動塊的下端樞接在第一定位塊上,所述手柄的下端固定於活動塊,位於張緊輪外側,所述張緊輪樞接在活動塊上端,並且與轉動軸左右相對,所述張緊輪外側具有輪齒。
作為本發明的進一步改進,所述矯直機構還包括固定於機架上的第二定位塊及擠壓在第二定位塊與活動塊之間的彈簧。
作為本發明的進一步改進,所述裁切氣缸為夾抓氣缸。
本發明自動成形設備取代了人工折金屬圈的方式,各機構配合緊湊,自動成形,結構簡單,節省成本;適用於大批量自動化生產,生產效率高;所製作的環形金屬圈一致性高,保證了產品品質。
附圖說明
圖1為本發明自動成形設備的立體示意圖。
圖2為圖1圓圈內的放大圖。
圖3為本發明自動成形設備另一角度的立體示意圖。
圖4為本發明自動成形設備的矯直機構的立體示意圖。
圖5為本發明自動成形設備的繞圈機構的立體示意圖。
圖6為圖6的立體分解圖。
圖7為本發明自動成形設備的裁切機構的立體示意圖,未顯示電機。
圖8為本發明自動成形設備的整平機構的立體示意圖。
圖9為本發明自動成形設備的整平機構的立體分解圖。
圖10為本發明自動成形設備的整平機構的部分元件的剖面圖。
圖11為螺旋狀金屬圈的立體示意圖。
圖12為半成品金屬圈的立體示意圖。
圖13為成品金屬圈的立體示意圖。
具體實施方式
請參閱圖1至圖13所示,本發明提供一種自動成形設備100,用以把金屬絲200裁斷並成形為環形金屬圈203,其包括機架10及分別固定於機架10上的矯直機構20、繞圈機構30、裁切機構40、整平機構50及出料箱60。
機架10上樞接有放料盤11,用以纏繞待加工為環形金屬圈203的金屬絲200。
矯直機構20包括一第一定位塊21、一第二定位塊22、一活動塊23、一手柄24、一張緊輪25及一彈簧26。第一定位塊21和第二定位塊22固定於機架10上,第二定位塊22位於機架10外側,並且左右對齊。活動塊23的下端樞接在第一定位塊21上。手柄24的下端固定於活動塊23,位於張緊輪25外側。張緊輪25靠近於繞圈機構30,位於放料盤11下方,樞接在活動塊23上端,張緊輪25外側具有輪齒。彈簧26擠壓在第一定位塊21與活動塊23之間。通過手動扳動手柄24,可以促使活動塊23克服彈簧26的彈力,帶動張緊輪25向外側移動,鬆開手後,活動塊23依靠彈簧26的彈性恢復力,帶動張緊輪24向內側移動至原位。
繞圈機構30包括電機31、轉動軸32、抵推塊33及限制塊34,電機31位於轉動軸32後方,用以驅動轉動軸32旋轉,轉動軸32外側也設有輪齒,與張緊輪25的輪齒左右對齊。第一定位塊21設有一弧形凹部211遮擋於凹部211後方的定位板212,定位板212具有供轉動軸32向前穿過的圓孔213,抵推塊33固定於凹部211內,向後貼靠在定位板212上,抵推塊33也設有供轉動軸32向前穿過的圓孔333,抵推塊33前端面凹設有位於圓孔333周緣的收容槽331,收容槽331內側設有朝向前方的螺旋面335,使得收容槽331在前後方向上的深度沿圓周線逐漸變深或變淺,定位板212固定於抵推塊33上,圍設於收容槽331前側。限制塊34固定於抵推塊33前表面,用以限制金屬絲200向前偏移。
裁切機構40包括一裁切氣缸41、在裁切氣缸41驅動下左右移動的活動臂42及固定於活動臂42上的裁切刀43,裁切氣缸41為夾抓氣缸。
整平機構50包括一整平氣缸51、一按壓塊52、連接在整平氣缸51與按壓塊52之間的聯結軸53及支架54,按壓塊52位於轉動軸32下方,其具有向前凸出的整平凸部520。整平氣缸51通過聯結軸53驅動按壓塊52前後移動。
支架54包括一導引塊541、一落料塊542及一支撐塊543,導引塊541內側設有上下貫穿的導引槽544,落料塊54內側也設有上下貫穿的落料槽545,導引槽544位於落料槽545上方,兩者相鄰設置,在上下方向上呈開口朝向繞圈機構30的U形。支撐塊543固定於落料塊542內側,遮擋於落料槽545後方,但位於整平凸部520下方,並且上下間隔開,支撐塊543還向前超過整平凸部520,導引槽544向上超出支撐塊543。
出料箱60位於落料塊542下方,用以收容自落料槽545掉落的金屬圈203。
本發明自動成形設備100工作時,按如下步驟進行:
(1)手動扳動矯直機構20的手柄24,促使活動塊23克服彈簧26的彈力,帶動張緊輪25向外側移動。
(2)金屬絲200頭部向下送入張緊輪25與轉動軸32之間,鬆開手後,活動塊23依靠彈簧26的彈性恢復力,帶動張緊輪24向內側移動至原位,使金屬絲200被夾持在張緊輪25與轉動軸32之間。
(3)電機31驅動轉動軸32旋轉,利用輪齒與金屬絲200之間的摩擦力,促使金屬絲200纏繞在轉動軸32。
(4)抵推塊33收容槽331的深度沿圓周線逐漸變深或變淺,其後內側壁在金屬絲200纏繞過程中,抵推金屬絲200向前移動,促使金屬絲200纏繞為螺旋狀金屬圈201。
(5)螺旋狀金屬圈202向前移動至整平機構40導引槽544的上方時,裁切氣缸41驅動裁切刀43朝螺旋狀金屬圈201方向移動,把螺旋狀金屬圈201裁切為半成品金屬圈202,半成品金屬圈202向下掉落於落料槽545內,但被支撐塊543託住,具體的說,半成品金屬圈202的一部分位於落料槽545內,另一部分被支撐塊543託住。
(6)整平氣缸51驅動按壓塊52向前移動,按壓塊52的整平凸部520向前抵壓半成品金屬圈202,促使半成品金屬圈202被按壓塊52與落料塊542擠壓後,整平為環形金屬環203,然後,自落料槽545繼續向下掉落於出料箱60內。
本發明自動成形設備100取代了人工折金屬圈的方式,各機構配合緊湊,自動成形,結構簡單,節省成本;適用於大批量自動化生產,生產效率高;所製作的環形金屬圈203一致性高,保證了產品品質。
上述實施例僅為本發明結構的一種實施方式,但本發明結構的實施方式並不受上述實施例的限制,加工材料也不僅僅局限於柱狀金屬環,還包括帶狀金屬條、三角形金屬條、橢圓金屬條等截面不同的金屬絲,其他的任何未背離本發明結構的精神實質與原理下所作的改變、替換、組合、簡化,均應為等效的置換方式,都包含在本發明結構的保護範圍之內。