一種超硬材料合成用零部件分級裝置的製作方法
2023-12-04 07:46:41
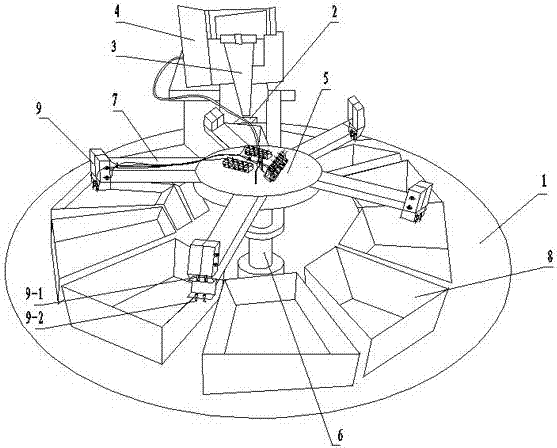
本發明涉及超硬材料技術領域,尤其涉及一種超硬材料合成用零部件分級裝置。
背景技術:
在超硬材料合成行業中,超硬材料的生產是通過一些組件組裝後進行高溫高壓下合成的。對每一個組件尺寸、重量、電阻等要求都非常嚴格,並且,同一種組件間對產品一致性要求也非常高。而作為超硬材料合成主要性能的發熱元件,其要求更是嚴苛。由於其原材料加工無法滿足其近於苛刻的要求,就需要按照產品要求對其進行分級才能滿足生產需要。
傳統金剛石合成用的發熱元件分重方法是採用人工方法用電子天平進行重量分級,每人一臺電子天平,逐片進行稱量分重,這樣分重效率非常低下,需要較大的人力投入,不但增加了人工成本,而且由於人工分級不可避免會產生人為錯誤,保證不了分級精度。並且,由於其需要量巨大,通常的手工分級的方法投入人工成本太高,勞動強度大、生產效率十分低下,不能保證分級質量,嚴重影響超硬材料合成的生產效率。
在公知的技術中,人造金剛石零部件----發熱組件分重工藝通常是小作坊式的,而合成金剛石的工藝要求發熱元件的尺寸、密度一致性極高。其要求零部件生產也必須適應高品級金剛石合成的需要,逐步淘汰小作坊式的手工操作方式,進而如何採用適當的自動化生產技術為現在生產過程中急需解決的技術問題。
專利號為201520483310.3的專利申請文件公開了一種超硬材料合成用發熱組件自動分重裝置,具體包括,包括稱重裝置、操作臺和設置在操作臺上的分級裝置、微控器、為分級裝置提供動力的動力裝置;此實用新型採用電磁吸合方式自動分選,採用微電腦自動分級機與切帶機結合,實現全自動聯機工作,提高了生產效率和降低人工成本。但是,此裝置在分級的過程中,採用是的電磁吸盤,利用磁效應吸附帶有磁性的組件,具有較強的針對性,使用具有局限性。
技術實現要素:
本發明的目的是提供一種超硬材料合成用零部件分級裝置,能夠針對不同材質的零部件進行分級操作,普遍性強,且替代傳統手工操作方式,降低勞動強度及生產成本,提高生產效率,保證合成用零部件的精度、重量一致性要求,提高超硬材料零部件分級的自動化水平。
本發明採用的技術方案為:
一種超硬材料合成用零部件分級裝置,包括操作臺、稱重機構和多個接料盒,稱重機構和接料盒設於操作臺上,還包括設置在操作臺上的分級動力機構、設於分級動力機構上的分級機構、為分級機構提供動力的氣動系統和微控器;
所述的分級動力機構包括豎向設於操作臺中心點處的電機,電機的受控端連接微控器,電機的輸出軸連接迴轉盤的中心,沿迴轉盤的圓周方向均勻間隔設有多個水平轉動杆;
所述的分級機構包括多個雙向定位氣缸吸附器,每個雙向定位氣缸吸附器設於一個水平轉動杆的末端,且雙向定位氣缸吸附器處於稱重機構的正上方;
所述的氣動系統包括氣動旋轉接頭和多路氣動控制管路,每路氣動控制管路包括電磁換向閥、兩個真空發生器和四通接頭,氣動旋轉接頭的進氣口通過氣管連接氣源,氣動旋轉接頭的出氣口分別連接每路電磁換向閥的進氣口,每路電磁換向閥的第一出氣口氣路連接一個雙向定位氣缸吸附器的第一進氣孔,每路電磁換向閥的第二出氣口氣路連接到相應管路的四通接頭的進氣口,四通接頭的第一出氣口連接到雙向定位氣缸吸附器的第二進氣孔,四通接頭的第二出氣口通過一個真空發生器連接到雙向定位氣缸吸附器的第一負壓孔,四通接頭的第三出氣口通過另一個真空發生器連接到雙向定位氣缸吸附器的第二負壓孔;
所述的稱重機構設置在切帶機的下料口,稱重機構為電子稱量設備,且電子稱量設備的信號輸出端連接微控器的採集信號輸入端;
所述的多個接料盒放置在操作臺上,多個接料盒圍繞電機均勻分布,且設在雙向定位氣缸吸附器運動軌跡的正下方。
所述的雙向定位氣缸吸附器包括雙缸定位氣缸體和設於雙缸氣缸伸縮端的橡膠吸嘴。
所述的接料盒採用扇形結構。
所述的電機採用步進電機。
本發明利用操作臺支撐整個裝置,在操作臺中心點處設置電機,電機的輸出軸端連接一個水平的迴轉盤,迴轉盤可以在電機的帶動下進行轉動,同時帶動水平轉動杆和設於水平轉動杆末端的雙向定位氣缸吸附器進行圓周轉動,在轉動的同時,利用氣動旋轉接頭能夠有效避免氣路在電機帶動迴轉盤旋轉的過程中發生纏繞。
在操作臺上設有稱重機構和接料盒,當進行物料分級操作時,利用多路氣動控制管路控制雙向定位氣缸吸附器從而對吸附電子稱量設備的載板上的物料進行吸附並分級。
具體是通過每路氣動旋轉接頭進行氣路分配,每路氣動旋轉接頭的出氣口連接一路電磁換向閥的進氣口,電磁換向閥的第一出氣口氣路連接雙向定位氣缸吸附器的第一進氣孔,電磁換向閥的第二出氣口氣路連接到一個四通接頭的進氣口,四通接頭的第一出氣口連接到雙向定位氣缸吸附器的第二進氣孔,雙向定位氣缸吸附器的第一進氣孔和第二進氣孔主要是用於控制氣缸的上下伸縮動作。之後再通過四通接頭的第二出氣口和第三出氣口,分別通過一個真空發生器連接到雙向定位氣缸吸附器的第一負壓孔和第二負壓孔。第一負壓孔和第二負壓孔主要是用於控制吸嘴動作,當需要吸附電子稱量設備的載板上的物料時,啟動雙缸氣缸,使得雙缸氣缸的氣缸杆向下伸,之後再通過第一負壓孔和第二負壓孔產生負壓,利用吸嘴吸附電子稱量設備的載板上的物料。
此時,電子稱量設備的載板上的物料可以是鋼片或者其他的不具有磁性的物料,均能夠達到吸附的作用,使用範圍更加寬廣,能夠針對不同材質的零部件進行分級操作,普遍性強。
附圖說明
圖1為本發明的結構示意圖;
圖2為本發明的氣動系統結構示意。
具體實施方式
如圖1所示,本發明包括操作臺1、稱重機構2和多個接料盒8,稱重機構2和接料盒8設於操作臺1上,操作臺1用於支撐整個裝置,所述的稱重機構2設置在切帶機的下料口,稱重機構2為電子稱量設備,且電子稱量設備的信號輸出端連接微控器的採集信號輸入端;所述的多個接料盒8放置在操作臺1上,所述的接料盒8採用扇形結構,多個接料盒8圍繞電機6均勻分布,且設在雙向定位氣缸吸附器9運動軌跡的正下方。微控器一方面用於採集電子稱量設備的重量信號,之後再將這個信號數值與設定值比較,再控制步進電機6動作,根據設定的梯度值,對物料進行依次分級放置。
還包括設置在操作臺1上的分級動力機構、設於分級動力機構上的分級機構、為分級機構提供動力的氣動系統和微控器。
所述的分級動力機構包括豎向設於操作臺1中心點處的電機6,電機6的受控端連接微控器,電機6的輸出軸連接迴轉盤5的中心,沿迴轉盤5的圓周方向均勻間隔設有多個水平轉動杆7。
所述的分級機構包括多個雙向定位氣缸吸附器9,每個雙向定位氣缸吸附器9設於一個水平轉動杆7的末端,且雙向定位氣缸吸附器9處於稱重機構2的正上方。所述的雙向定位氣缸吸附器9包括雙缸定位氣缸體9-1和設於雙缸氣缸伸縮端的橡膠吸嘴9-2。
所述的氣動系統包括氣動旋轉接頭10和多路氣動控制管路,氣動旋轉接頭10通過一個支架進行固定在迴轉盤5上,每路氣動控制管路包括電磁換向閥12、兩個真空發生器11和四通接頭13,氣動旋轉接頭10的進氣口通過氣管連接氣源,氣動旋轉接頭10的出氣口分別連接每路電磁換向閥12的進氣口a,每路電磁換向閥12的第一出氣口b氣路連接一個雙向定位氣缸吸附器9的第一進氣孔a,每路電磁換向閥12的第二出氣口c氣路連接到相應管路的四通接頭13的進氣口,四通接頭13的第一出氣口連接到雙向定位氣缸吸附器9的第二進氣孔b,四通接頭13的第二出氣口通過一個真空發生器11連接到雙向定位氣缸吸附器9的第一負壓孔c,四通接頭13的第三出氣口通過另一個真空發生器11連接到雙向定位氣缸吸附器9的第二負壓孔d。
下面結合附圖說明發明的工作原理:
正常工作時:切帶機對鋼帶進行切割,切割後的鋼片通過下料口落入到電子稱量設備的載板上,此時電子稱量設備對鋼片進行了稱重,並發送鋼片重量值到微控器,微控器接收到重量值後,發送控制信號到步進電機6,步進電機6在微控器的控制下通過水平轉動杆7帶動設置在水平轉動杆7末端的雙向定位氣缸吸附器9進行轉動,當雙向定位氣缸吸附器9轉動到電子稱量設備的載板上方時,由氣動系統控制雙向定位氣缸吸附器9對鋼帶進行吸附,然後旋轉,根據收納盒的擺放數量(多個收納盒之間緊挨擺放,且收納盒整體擺放為一個圓形,便於鋼帶的放料),微控器對鋼帶進行分類放置,根據對鋼帶的需求,電子稱量設備稱重的數值與設定值比較後,根據設定的梯度值對鋼帶進行依次分級放置。
其中,氣動系統的工作原理為:首先,氣源由氣動旋轉接頭10引入,利用氣動旋轉接頭10能夠有效避免氣路在電機6帶動迴轉盤5旋轉的過程中發生纏繞,再將壓縮氣體通過管路分配到多路氣動控制管路中,本實施例採用5路氣動控制管路,相應的水平轉動杆7也採用5根。如圖2所示,下面以一路氣動控制管路為例進行說明,氣動控制管路包括一個電磁換向閥12、兩個真空發生器11和一個四通接頭13,氣動旋轉接頭10的出氣口連接一路電磁換向閥12的進氣口a,電磁換向閥12的第一出氣口b氣路連接雙向定位氣缸吸附器9的第一進氣孔a,電磁換向閥12的第二出氣口c氣路連接到一個四通接頭13的進氣口,四通接頭13的第一出氣口連接到雙向定位氣缸吸附器9的第二進氣孔b,雙向定位氣缸吸附器9的第一進氣孔a和第二進氣孔b主要是用於控制氣缸的上下伸縮動作,由於氣缸採用的是雙缸氣缸,所以,兩個進氣孔分別控制兩個氣缸。之後再通過四通接頭13的第二出氣口和第三出氣口,分別通過一個真空發生器11連接到雙向定位氣缸吸附器9的第一負壓孔c和第二負壓孔d。第一負壓孔c和第二負壓孔d主要是用於控制吸嘴9-2動作,當需要吸附電子稱量設備的載板上的物料時,啟動雙缸氣缸,使得雙缸氣缸的氣缸杆向下伸,之後再通過第一負壓孔c和第二負壓孔d產生負壓,利用吸嘴9-2吸附電子稱量設備的載板上的物料。此時,電子稱量設備的載板上的物料可以是鋼片或者其他的不具有磁性的物料,均能夠達到吸附的作用,使用範圍更加寬廣,能夠針對不同材質的零部件進行分級操作,普遍性強。