一種錐體和錐孔的加工方法與流程
2023-04-30 20:25:21
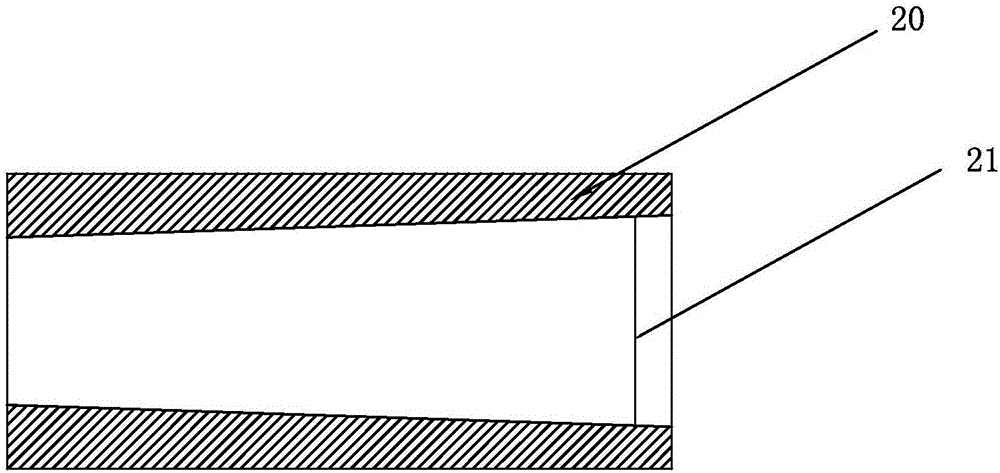
本發明涉及船用螺旋槳及艉軸技術領域,尤其涉及一種錐體和錐孔的加工方法。
背景技術:
目前,螺旋槳錐孔加工的傳統工藝路線為:首先,用車床粗加工螺旋槳錐孔,直徑留0.5mm的刮配餘量,然後採用刮刀或小的砂輪磨頭採用手工磨削的方法與螺旋槳軸進行拂配,拂配時控制接觸斑點的數量以達到對接觸面積的控制。隨著船舶大型化的發展,螺旋槳錐孔直徑和長度越來越大,螺旋槳錐孔與螺旋槳軸採用無鍵聯接形式的越來越多,對錐體配合接觸面和粗糙度也有更高的要求。傳統的拂配工藝效率低,質量不高,無法從根本上滿足接觸面積和粗糙度的要求,而且互換性差。目前,每當船舶螺旋槳損壞需要更換時,必須將艉軸從船上拆下搬運至刮配車間,同新製作的螺旋槳進行刮配,此方式工作量大,周期長,維修成本高,亟需改善。綜上所述,需要改進螺旋槳錐孔的製作方法,用於解決現有技術中操作複雜、效率低、成本高和互換性差的問題。
技術實現要素:
為了克服上述現有技術的不足,本發明提供了一種錐體和錐孔加工方法,該方法加工精度高、錐體配合接觸面好、操作簡單、互換性好,可以節省人工、製作成本低。
本發明解決其技術問題所採用的技術方案為:
一種錐體和錐孔的加工方法,其特徵在於:該方法包括以下步驟:
步驟1:所述錐度棒和錐度套按相同的錐度製作,經過研磨加工,兩者接觸面積佔錐體配合比例達到95%以上;
步驟2:所述錐度棒在與預設螺旋槳錐孔大端標準直徑值相等處刻畫出第一標記線,錐度套在與上述標準直徑相等處刻畫出第二標記線;
步驟3:製作螺旋槳錐孔和艉軸錐體,所述螺旋槳錐孔長度對應小於錐度棒錐體長度,所述艉軸錐體長度對應小於錐度套錐孔長度;
步驟4:加工螺旋槳錐孔,直至螺旋槳錐孔大端端面距離第一標記線4~6mm,並檢查所述錐度棒和螺旋槳錐孔接觸面積,如果接觸面積佔錐體配合比例超過85%,則進入下一步驟,否則調整加工的錐度,繼續加工,然後重複此步驟;
步驟5:按步驟4確定的車削角度,繼續車削螺旋槳錐孔,直至螺旋槳錐孔大端端面與第一標記線基本重合;
步驟6:加工艉軸錐體,直至艉軸錐體小端端面直徑大於預設艉軸錐體小端標準直徑0.27~0.4mm,並檢查所述錐度套和艉軸錐體接觸面積,如果接觸面積佔錐體配合比例超過85%,則進入下一步驟,否則調整加工的錐度,繼續加工,然後重複此步驟;
步驟7:按步驟5確定的車削角度,繼續車削艉軸錐體,直至艉軸錐體小端端面直徑位於預設艉軸錐體小端標準直徑的±0.1mm範圍內。
作為上述技術方案的改進,所述錐度棒的大端直徑大於錐度套的大端直徑,當錐度棒與錐度套在套合時,錐度棒上的第一標記線和錐度套內的第二標記線重合。
作為上述技術方案的改進,在步驟3和步驟4之間還設有以下步驟:在所述錐度棒位於第一標記線的左右兩側較近位置處分別輕劃出進線和止線。
作為上述技術方案的改進在步驟4中,當螺旋槳錐孔大端端面與第一標記線基本重合時,螺旋槳錐孔的大端端面在錐度棒的進線和止線之間。
本發明的有益效果有:
本發明提出的螺旋槳錐孔加工方法,螺旋槳錐孔與艉軸的配合接觸面不是傳統拂配出的斑點式接觸,而是面接觸,可以提高螺旋槳工作時的穩定性,減少振動,螺旋槳錐孔表面粗糙度大幅提高,接觸面積大,可互換性高,重做螺旋槳時不需要與軸拂配,在工具機上完成錐孔的拂配,解決了現有技術中拂配時操作複雜,效率低,拂配完成的螺旋槳互換性差的難題,大幅降低了工人的勞動強度,降低了生產企業的用工成本,生產效率大幅提升,並且節約很多拂配時間,大幅節省了船東的維修成本。
附圖說明
下面結合附圖及具體實施例對本發明作進一步說明,其中:
圖1是本發明實施例錐度棒的結構示意圖;
圖2是本發明實施例錐度套的剖面圖;
圖3是本發明實施例錐度棒和錐度套的組合結構示意圖;
圖4是本發明實施例錐度棒和螺旋槳錐孔的組合結構示意圖;
圖5是本發明實施例錐度套和艉軸錐體的組合結構示意圖;
圖6是本發明實施例螺旋槳錐孔和艉軸錐體的組合結構示意圖。
具體實施方式
參見圖1至圖6,一種錐體和錐孔的加工方法,該方法包括以下步驟:
步驟1:製作錐度套20和錐度棒10,所述錐度棒10和錐度套20按相同的錐度製作,經過研磨加工,兩者接觸面積佔錐體配合比例達到95%以上;
步驟2:所述錐度棒10在與預設螺旋槳錐孔30大端標準直徑值相等處刻畫出第一標記線11,錐度套20在與上述標準直徑相等處刻畫出第二標記線21;
步驟3:製作螺旋槳錐孔30和艉軸錐體40,所述螺旋槳錐孔30長度對應小於錐度棒10錐體長度,所述艉軸錐體40長度對應小於錐度套20錐孔長度;
步驟4:加工螺旋槳錐孔30,直至螺旋槳錐孔30大端端面距離第一標記線4~6mm,並檢查所述錐度棒10和螺旋槳錐孔30接觸面積,如果接觸面積比例超過85%,則進入下一步驟,否則調整加工的錐度,繼續加工,然後重複此步驟;
步驟5:按照步驟4確定的車削角度,繼續車削螺旋槳錐孔30,直至螺旋槳錐孔30大端面與第一標記線基本重合;
步驟6:加工艉軸錐體40,直至艉軸錐體40小端端面直徑大於預設艉軸錐體小端標準直徑0.27~0.4mm,並檢查所述錐度套20和艉軸錐體40接觸面積,如果接觸面積佔錐體配合比例超過85%,則進入下一步驟,否則調整加工的錐度,繼續加工,然後重複此步驟;
步驟7:按步驟5確定的車削角度,繼續車削艉軸錐體40,直至艉軸錐體40小端端面直徑位於預設艉軸錐體小端標準直徑的±0.1mm範圍內。
所述錐度棒10的大端直徑大於錐度套20的大端直徑,當錐度棒10與錐度套20在套合時,錐度棒10上的第一標記線11和錐度套20內的第二標記線21重合;在步驟3和步驟4之間還設有以下步驟:在所述錐度棒10位於第一標記線11的左右兩側較近位置處分別輕劃出進線和止線。當在加工螺旋槳錐孔30時,錐度棒10插入螺旋槳錐孔30內,螺旋槳錐孔30的大端面在進線和止線之間即可完成加工;在步驟5中,當螺旋槳錐孔30大端端面與第一標記線11基本重合時,螺旋槳錐孔30的大端端面在錐度棒10的進線和止線之間。
此外錐度棒10錐體大端直徑大於對應的螺旋槳錐孔30大端直徑,小端直徑小於對應的螺旋槳錐孔30小端直徑,這樣利用錐度的特性螺旋槳錐孔30可以套牢在錐度棒10錐體和檢測兩者接觸面是否滿足要求,當所述螺旋槳錐孔30套合在錐度棒10錐體時,螺旋槳錐孔30的大端面與錐度棒10錐體上的第一標記線11位於同一平面;錐度套20錐體孔大端直徑大於對應的艉軸錐體40大端直徑,小端孔直徑小於對應艉軸錐體40小端直徑,便於檢測艉軸錐體40在錐度套20內是否滿足接觸面積達85%,當艉軸錐體40插入錐度套20內時,艉軸錐體40小端端面直徑位於預設艉軸錐體小端標準直徑的±0.1mm範圍內。
基於此方法,本發明具有以下實施例:
使本發明的技術方案更加清晰明確,下面以加工螺旋槳錐孔30大端直徑D0設為85mm,錐度α設為1:15,螺旋槳錐孔30長度L0設為240mm;相應的艉軸錐體40大端直徑D1為85mm,錐度與螺旋槳錐孔30的錐度同為1:15,錐體長度為233mm,設為L1,要求螺旋槳錐孔30小端端面突出艉軸錐體40小端端面長度為X,X為6~9mm,來做進一步說明具體加工方法:
步驟一:製作錐度棒10和錐度套20。錐度棒10的大端直徑為87mm,錐度為1:15,錐體長度為300mm,在錐度棒10錐體直徑為85mm處輕劃出第一標記線11,在其左側1.5mm和右側1.5mm處各刻畫出一條線作為進線和止線;錐度套20內孔大端直徑為86mm,錐度為1:15,錐孔長度為270mm,在錐度套20錐孔直徑為85mm處輕劃出第二標記線,錐度棒10和錐度套20錐體部分經過研磨,兩者配合的接觸面積需大於95%;
步驟二:調整車床車削角度,車削螺旋槳錐孔30;
步驟三:當螺旋槳錐孔30大端餘量剩4~6mm時,即錐孔直徑在84.6~84.74mm時,用所述步驟一中的錐度棒10檢查接觸面積的比例,如果接觸面積超過85%,則進入下一步;否則反覆調整車床車削角度,繼續車削,然後用所述步驟一中的錐度棒10檢查接觸面積的比例,直至接觸面積比例超過85%;
步驟四:按步驟三確定的車削角度,繼續車削螺旋槳錐孔30;
步驟五:用步驟一中的錐度棒10檢查螺旋槳錐孔30大端面在錐度棒10上的位置,如果位於進線和止線之間,則螺旋槳錐孔30車削完成,並記下錐度棒10大端端面到螺旋槳錐孔30大端端面的距離,定義為LA,否則重複步驟四,直至完成車削;
步驟六:調整車床車削角度,車削艉軸錐體40;
步驟七:當艉軸錐體40小端餘量剩4~6mm時,即艉軸錐體40的小端直徑為69.07~69.2mm時,用所述步驟一中的錐度套20檢查接觸面積的比例,如果接觸面積超過85%,則進入下一步;否則反覆調整車床車削角度,繼續車削,然後用所述步驟一中的錐度套20檢查接觸面積的比例,直至接觸面積比例超過85%;
步驟八:按步驟七確定的車削角度,繼續車削艉軸錐體40;
步驟九:用步驟一中的錐度套20來檢查艉軸錐體40在錐度套20上的位置,記下錐度套20錐孔小端端面到艉軸錐體40小端面的距離,定義為LB。
進一步參見圖4和圖5,由於錐度棒10錐體的大端直徑為87mm,長為300mm,錐度套20錐孔的大端直徑為86mm,長為270mm,則錐度棒10的小端比錐度套20的小端長了一個錐度的反比值即1/α;當用步驟一中錐度套20和錐度棒10分別與艉軸錐體40以及螺旋槳錐孔30套合,現假設錐度棒10上的第一標記線11和錐度套20上的第二標記線21位於同一基準面並同向排布,錐度棒10錐體的長度(L0+4/α)等於LA、螺旋槳錐孔30的長度(L0)、LB-X以及一個錐度的反比值(1/α)的總和,其中LB-X等於錐度套20小端面和螺旋槳錐孔30小端面之間的距離,X為螺旋槳錐孔30小端面突出艉軸錐體40小端端面的距離,X等於(6~9)mm,則LB等於X+3/α- LA,由於X需要處於6~9mm,那麼若LB大於(51-LA)mm且小於(54-LA)mm,則車削完成,否則重複步驟八,直至完成車削。
以上所述,只是本發明的較佳實施方式而已,但本發明並不限於上述實施例,只要其以任何相同或相似手段達到本發明的技術效果,都應屬於本發明的保護範圍。