一種旋浮銅冶煉方法及旋浮銅冶煉裝置與流程
2023-05-09 07:58:02 4
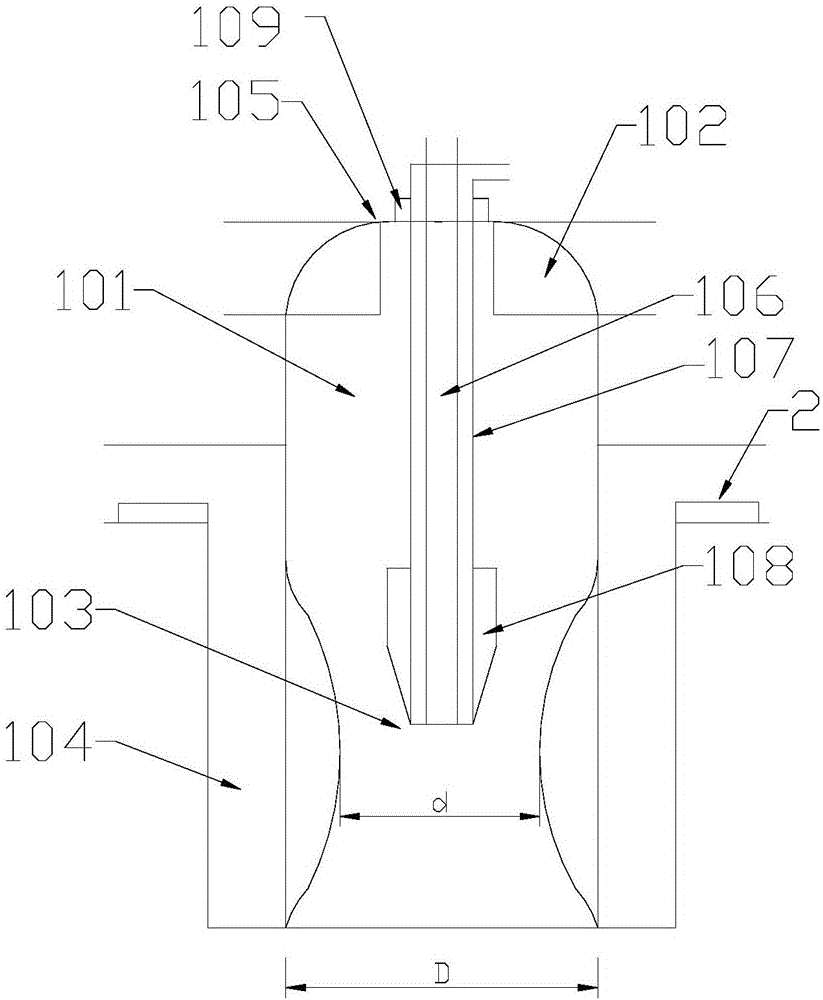
本發明涉及金屬硫化物冶煉技術領域,特別涉及一種旋浮銅冶煉方法,本發明還涉及適用於上述旋浮銅冶煉方法的一種旋浮銅冶煉裝置。
背景技術:
目前,金屬硫化物的精礦一般是採用火法冶金的方式實現冶煉,即利用金屬硫化物礦中的硫和鐵與氧反應後被脫除最終得到金屬的過程,特別是銅、鎳等金屬的火法冶煉。
火法冶金工藝大致可分為沉澱池熔煉和空間熔煉兩大類,其中空間懸浮熔煉的實質是利用乾燥後粉狀硫化物礦的巨大表面積,使物料粒子(指的是粉狀硫化物礦)與氧充分結合,在瞬間(2~3秒)內完成氧化反應。空間懸浮熔煉所採用的主要核心工藝是直流噴射技術,在熔煉過程中利用中間分布風和垂直工藝風的共同作用實現氣-固之間的接觸反應,但是由於受上述工藝中直流特性的影響,生產中常常會出現氧利用率低、煙塵率高、爐襯被衝刷腐蝕嚴重、精礦沒有反應在爐內堆積成生料堆等惡性狀況。
而為了改善上述問題,近幾年又開發出了旋流噴射技術,即令氣體螺旋流動而實現與物料粒子的接觸反應,但其工作效果仍不盡理想,無法較好的滿足冶煉技術的高投料量、高負荷、高氧濃和高作業率(簡稱為「四高」)的發展趨勢。
因此,如何進一步提硫化銅的冶煉效果,已經成為目前本領域技術人員亟待解決的問題。
技術實現要素:
有鑑於此,本發明提供了一種旋浮銅冶煉方法,其能夠進一步的提高硫化銅化物的冶煉效果,本發明還提供了適用於上述旋浮銅冶煉方法的一種旋浮銅冶煉裝置。
為了達到上述目的,本發明提供如下技術方案:
一種旋浮銅冶煉方法,包括以下步驟:
令乾燥的銅精礦粉和冰銅粉中的一者,與熔劑和/或煙塵按比例混合形成混合物料,並進入噴嘴的物料通道中,再經過所述物料通道進入到冶煉爐的反應塔中;
反應氣體在所述噴嘴的旋流器作用下形成旋流,並進入到所述噴嘴的旋流氣體通道中,所述旋流在所述旋流氣體通道的引導下經過所述噴嘴的文丘裡通道,並最終進入所述反應塔;
經過所述文丘裡通道而被高速膨脹的所述旋流,在所述反應塔中與所述混合物料接觸反應;
接觸反應生成的熔體落入到所述冶煉爐的沉澱池中,並分離為渣層和產品層,當所述混合物料中含有銅精礦粉時產品層為冰銅層,當所述混合物料中含有冰銅粉時產品層為粗銅層。
優選的,上述旋浮銅冶煉方法中,還包括以下步驟:
通過所述噴嘴的輔助氧氣通道和輔助燃料通道向所述反應塔中補充反應氣體和/或燃料。
優選的,上述旋浮銅冶煉方法中,向所述噴嘴輸送所述混合物料的過程還包括以下操作:
使用輸料管將所述混合物料送入到所述噴嘴中,並先進入所述噴嘴的流化給料器中進行流化,然後再進入到所述物料通道中。
優選的,上述旋浮銅冶煉方法中,所述反應氣體中的氧氣濃度為40%VOL~90%VOL,所述旋流進入所述冶煉爐的旋轉流速為220m/s~300m/s。
優選的,上述旋浮銅冶煉方法中,所述輔助氣體通道噴入所述反應氣體的流量為10Nm3/h~200Nm3/h,所述輔助燃料通道噴入燃料的流量為10Nm3/h~100Nm3/h。
一種旋浮銅冶煉裝置,包括輸料管、冶煉爐,以及連通所述輸料管和所述冶煉爐的噴嘴,適用於上述任意一項所述的旋浮銅冶煉方法,所述噴嘴包括:
導流反應氣體的旋流氣體通道,所述旋流氣體通道的進氣口上設置有旋流器;
設置在所述旋流氣體通道內的文丘裡通道;
套設在所述旋流氣體通道的外側,並與所述輸料管連通的物料通道。
優選的,上述旋浮銅冶煉裝置中,所述文丘裡通道的最小內徑d,不大於所述旋流氣體通道的內徑D,且大於D/2。
優選的,上述旋浮銅冶煉裝置中,所述旋流器通過垂直於所述旋流氣體通道的進氣管,與所述旋流氣體通道連接形成,並且所述進氣管和所述旋流氣體通道連通形成氣體入口,所述氣體入口包括靠近所述進氣管的收縮口和靠近所述旋流氣體通道的切向口。
優選的,上述旋浮銅冶煉裝置中,所述物料通道與所述輸料管連通的部位設置有流化給料器,並且所述輸料管相對於所述物料通道傾斜設置,所述輸料管相對於水平面的傾斜角度為10度~40度。
優選的,上述旋浮銅冶煉裝置中,還包括:
設置在所述旋流氣體通道內的輔助氧氣通道;
套設在所述輔助氧氣通道的外側,並位於所述旋流氣體通道內的輔助燃料通道。
優選的,上述旋浮銅冶煉裝置中,還包括套設在所述輔助燃料通道的外壁上,且能夠沿所述輔助燃料通道的軸嚮往復移動的調節錐,以及設置在所述旋流氣體通道的頂壁外側,控制所述調節錐移動的控制器。
優選的,上述旋浮銅冶煉裝置中,所述旋流氣體通道、所述文丘裡通道、所述物料通道、所述輔助氧氣通道和所述輔助燃料通道同軸設置,並且所述旋流氣體通道的頂壁為弧形壁面。
優選的,上述旋浮銅冶煉裝置中,所述輔助燃料通道、所述輔助氧氣通道的出氣口和所述旋流氣體通道的出氣口平齊設置。
本發明提供的旋浮銅冶煉方法,其操作過程為:將乾燥的銅精礦粉或者冰銅粉與乾燥的粉狀熔劑等形成的混合物料,均勻的送入到噴嘴的物料通道中,混合物料在重力的作用下經物料通道進入到冶煉爐的反應塔中;反應氣體進入到噴嘴的旋流器中,使反應氣體形成旋流並沿切線方向進入旋流氣體通道內形成旋流風,在旋流氣體通道內以旋轉流動的方式向反應塔移動,在此移動過程中,旋流風經過文丘裡通道後,旋流風以高速膨脹、旋流的方式噴射進入反應塔,形成噴射旋流氣體;噴射旋流氣體在高速膨脹的作用下快速與進入反應塔的混合物料接觸,並在旋流的作用下,旋流氣體將混合物料卷吸進入噴射氣流中,隨著溫度的不斷升高,混合物料與反應氣體不斷碰撞而快速反應,然後進入位於反應塔下方的沉澱池(沉澱池為冶煉爐的組成部分)中,形成冰銅層或粗銅層(當混合物料中含有銅精礦粉時形成冰銅層,當混合物料中含有冰銅粉時形成粗銅層)和渣層,反應產生的高溫氣體富含二氧化硫,經冶煉爐的排氣口進入餘熱鍋爐。
本發明提供的旋浮銅冶煉方法,通過使反應氣體以高速膨脹、旋流等方式與混合物料接觸反應,能夠使得冶煉反應更加充分的進行,氧氣利用率得到了提高,渣含銅量降低,煙塵發生率也得到了降低,同時還可以採用較高的富氧濃度的反應氣體,提高了煙氣的二氧化硫含量,令煙氣帶走的熱量降低,而且還能夠適應投料量大範圍波動的需要,令產能得到了顯著提升。
本發明提供的旋浮銅冶煉裝置,主要包括輸料管、冶煉爐以及連通輸料管和冶煉爐的噴嘴,其中的噴嘴又包括旋流氣體通道、旋流器、文丘裡通道、物料通道。旋流器設置在旋流氣體通道的進氣口上,用於使進入到旋流氣體通道內的反應氣體形成旋流,反應氣體形成旋流後,在旋流氣體通道的導向下沿其軸向旋動,而文丘裡通道由於固定設置在旋流氣體通道的內壁上,所以旋流會進入到文丘裡通道中,在文丘裡通道的作用下,使得旋流以高速膨脹的狀態進入到冶煉爐中(具體為冶煉爐的反應塔中),同時,粉末狀的混合物料經過輸料管進入到套設在旋流氣體通道外側的物料通道中,並與形成旋流的反應氣體一同進入到冶煉爐中,使得銅精礦粉或冰銅粉在高溫環境下被卷吸進旋流中,並與反應氣體不斷碰撞而快速反應,然後進入反應塔下方的沉澱池中,形成冰銅層或粗銅層和渣層,反應產生的高溫氣體富含二氧化硫,經冶煉爐的排氣口進入餘熱鍋爐。
附圖說明
為了更清楚地說明本發明實施例或現有技術中的技術方案,下面將對實施例或現有技術描述中所需要使用的附圖作簡單地介紹,顯而易見地,下面描述中的附圖僅僅是本發明的實施例,對於本領域普通技術人員來講,在不付出創造性勞動的前提下,還可以根據提供的附圖獲得其他的附圖。
圖1為本發明實施例提供的旋浮銅冶煉裝置的結構示意圖;
圖2為一種噴嘴的結構示意圖;
圖3為另一種噴嘴的結構示意圖;
圖4為旋流器的工作示意圖。
在圖1-圖4中:
1-噴嘴,2-流化給料器,3-輸料管,4-冶煉爐;
101-旋流氣體通道,102-旋流器,103-文丘裡通道,104-物料通道,105-頂壁,106-輔助氧氣通道,107-輔助燃料通道,108-調節錐,109-控制器;
1021-進氣管,1022-收縮口,1023-切向口。
具體實施方式
本發明提供了一種旋浮銅冶煉裝置,其能夠進一步的提高硫化銅的冶煉效果。
下面將結合本發明實施例中的附圖,對本發明實施例中的技術方案進行清楚、完整地描述,顯然,所描述的實施例僅僅是本發明一部分實施例,而不是全部的實施例。基於本發明中的實施例,本領域普通技術人員在沒有做出創造性勞動前提下所獲得的所有其他實施例,都屬於本發明保護的範圍。
如圖1-圖4所示,本發明實施例提供的旋浮銅冶煉裝置,主要包括輸料管3、冶煉爐4以及連通輸料管3和冶煉爐4的噴嘴1,本申請主要對噴嘴1進行了改進,具體的,改進後的噴嘴1包括:導流反應氣體的旋流氣體通道101,旋流氣體通道101的進氣口上設置有使反應氣體形成旋流的旋流器102;同軸設在旋流氣體通道101內並與旋流氣體通道101的內壁連接的文丘裡通道103,形成旋流的反應氣體經過文丘裡通道103後,反應氣體以高速膨脹、旋流的方式噴射進冶煉爐4的反應塔,形成噴射旋流氣體;套設在旋流氣體通道101的外側並與輸料管3連通的物料通道104,物料通道104用於輸送由乾燥的銅精礦粉和冰銅粉中的一者,與熔劑和/或煙塵按比例混合形成的混合物料。
上述旋浮銅冶煉裝置在進行工作時,被輸料管3送來的混合物料經過物料通道104進入到冶煉爐4的反應塔中,與此同時,反應氣體進入到旋流氣體通道101中,進入到旋流氣體通道101的過程中,反應氣體首先進入到旋流器102中而形成旋流,之後在旋流氣體通道101的導向下沿旋流氣體通道101的軸向移動,並進入到文丘裡通道103中,在文丘裡通道103的作用下,使得旋流以高速膨脹的狀態進入到反應塔中,形成噴射旋流氣體。噴射旋流氣體在高速膨脹的作用下,快速與進入反應塔的混合物料接觸,並在旋流作用下,將混合物料卷吸進入噴射旋流氣體中,隨著溫度的不斷升高,混合物料與反應氣體不斷碰撞而快速反應,然後進入反應塔下方的沉澱池中,形成冰銅層或粗銅層(當混合物料中含有銅精礦粉時形成冰銅層,當混合物料中含有冰銅粉時形成粗銅層)和渣層,反應產生的高溫氣體富含二氧化硫,經冶煉爐4的排氣口進入餘熱鍋爐。
本實施例提供的旋浮銅冶煉裝置,通過將噴嘴1設置為上述結構,使得氣-固接觸更加充分,從而令冶煉反應能夠充分進行,氧氣利用率得到了提高,渣含銅量降低,煙塵發生率也得到了降低。同時還可以採用較高的富氧濃度的反應氣體,提高了煙氣的二氧化硫含量,令煙氣帶走的熱量降低,而且還能夠適應投料量大範圍波動的需要,令產能得到了顯著提升,且能耗低,投資少。
另外,上述結構的反應空間小,由於反應氣體以旋流方式流動,使得反應空間中無反應死區,且對爐體耐火材料的衝刷較小,而且改進後的噴嘴1,結構簡單,控制、操作、維護等更加方便、可靠,能夠充分利用流體的勢能,運行成本也較低。
為了進一步優化技術方案,本實施例提供的旋浮銅冶煉裝置中,文丘裡通道103的最小內徑為d,旋流氣體通道101的內徑為D,則優選D/2<d≤D,如圖2和圖3所示,文丘裡通道103的弧度半徑為R,則優選d<R<D。上述數值範圍的選擇,更加有利於反應氣體的高速膨脹,所以將其作為優選。並且,優選文丘裡通道103的最下端是文丘裡通道103的圓弧與旋流氣體通道101垂直壁的交點,該設置能夠對反應氣體更近一步的起到加速膨脹的作用,使反應氣體在進入反應塔後滿足旋流風速220m/s-300m/s的要求,且使氣流快速膨脹,卷吸旋流周圍的混合物料,使形成的氣-固旋流體能量更大,對促進氣-固、固-固的多次碰撞反應提供了更加良好的反應條件。
此外,本實施例中的文丘裡通道103還可以僅包括收縮段和圓喉段,圓喉段的埠和旋流氣體通道101的出氣口平齊設置,如圖3所示。此種設置方式,同樣能夠起到反應氣體快速膨脹的作用,所以也將其作為一種優選結構。
本實施例中,旋流器102包括:旋流管;與旋流管切向連通的進氣管1021,進氣管1021和旋流管連通形成的氣體入口,包括靠近進氣管1021的收縮口1022和靠近旋流管的切向口1023,如圖4所示。為了使結構更加簡單,本實施例優選收縮口1022的一側為旋流管的外壁,另一側形成收縮口1022為。
優選的,物料通道104與輸料管3連通的部位設置有流化給料器2,如圖1所示。本實施例中,增設流化給料器2的作用,是為了使混合物料均勻能夠更加均勻的進入到物料通道104中,進而更加均勻的進入到反應塔中,從而最大程度的防止偏析現象的發生,令反應效果更加突出。
進一步的,輸料管3相對於物料通道104傾斜設置,輸料管3相對於水平面的傾斜角度為10度~40度。本實施例中,令輸料管3相對於整體沿豎直方向設置的噴嘴1傾斜設置,是為了最大程度的降低物料直接進入噴嘴1的衝擊力,從而避免因衝擊力過大而對噴嘴1內的結構造成損害;另外,使輸料管3相對於水平面的傾斜角度優選為10度~40度,能夠使得混合物料可以經過較小的斜度流入流化給料器2,使混合物料更加均勻的進入噴嘴1,為反應塔內的充分反應提供更加良好的條件。
更優選的,本實施例提供的旋浮銅冶煉裝置中,還包括設置在旋流氣體通道101內,用於向冶煉爐4的反應塔內補充氧氣或反應氣體的輔助氧氣通道106,以及套設在輔助氧氣通道106的外側,並位於旋流氣體通道101內,用於向反應塔內噴入燃料以補充反應所需熱量的輔助燃料通道107,如圖2和圖3所示。本實施例中,輔助氧氣通道106向反應塔噴入反應氣體,輔助燃料通道107向反應塔噴入燃料用於補充反應氣體和/或熱量,同時還起到加速噴嘴1旋流氣體膨脹的作用,從而使得反應能夠更加充分、高效的進行。
本實施例中,還包括套設在輔助燃料通道107的外壁上,且能夠沿輔助燃料通道107的軸嚮往復移動的調節錐108,以及設置在旋流氣體通道101的頂壁105外側,控制調節錐108移動的控制器109。本實施例中,優選管狀的輔助燃料通道107的外壁上設置有螺紋,調節錐108通過螺紋與輔助燃料通道107連接,當設置在頂壁105上的控制器109控制輔助燃料通道107旋轉時,就能夠實現調節錐108的上下移動(類似於絲槓螺母機構)。本實施例還優選調節錐108的移動下限量為文丘裡通道103的最小內徑處。通過設置上述結構,可以滿足不同工況條件下,對風量、風速的調節要求,使反應氣體進入反應塔後具有快速膨脹旋流的作用,保證反應的充分進行。
如圖2和圖3所示,優選旋流氣體通道101、文丘裡通道103、物料通道104、輔助氧氣通道106和輔助燃料通道107同軸設置。本實施例優選上述部件均同軸設置,能夠使得噴嘴1的結構分布更加緊湊合理,工作可靠性也相對較高,同時還能夠實現反應氣體、混合物料更加均勻的接觸、混合,因此將其作為優選方案。
更近一步的,還優選旋流氣體通道101的頂壁105為弧形壁面,即弓形頂,如圖2和圖3所示。該結構有利於反應氣體形成的旋流快速向下移動,相比現有技術的平頂結構,其對旋流螺旋流動的效果影響較小,能夠促進旋流向下(即向靠近反應塔的方向)移動的更快。
本實施例中,輔助燃料通道107、輔助氧氣通道106的出氣口優選與旋流氣體通道101的出氣口平齊設置。此種設置方式也有利於混合物料與反應氣體在反應塔中的充分混合。
本實施例還提供了一種旋浮銅冶煉方法,該方法能夠應用於上述的旋浮銅冶煉裝置,包括以下步驟:
首先,銅精礦粉和冰銅粉中的一者,與熔劑和/或煙塵按比例混合形成混合物料,並使該混合物料經輸料管3進入到物料通道104中,並通過物料通道104進入到與物料通道104連通的冶煉爐4的反應塔中;
同時,令反應氣體進入噴嘴1,在進入的過程中,反應氣體先進入到噴嘴1的旋流器中,並使反應氣體在旋流器的作用下形成旋流,然後再進入到旋流氣體通道101中,之後旋流在旋流氣體通道101的引導下經過設置在旋流氣體通道101內的文丘裡通道103,文丘裡通道103令旋流以高速膨脹、螺旋流動的方式進入到反應塔中;
此外,還通過輔助氧氣通道106和輔助燃料通道107向反應塔中補充反應氣體和/或燃料,以為反應的進行提供足夠的原料以及所需的熱量,令反應氣體和混合物料反應的更加充分;
之後,經過文丘裡通道103的被高速膨脹的旋流進入到反應塔中,在反應塔中與混合物料不斷碰撞而快速反應;
最後,反應生成的熔體落入到反應塔下方的沉澱池中,形成渣層和產品層,當混合物料中含有銅精礦粉時產品層為冰銅層,當混合物料中含有冰銅粉時產品層為粗銅層。
需要注意的是,上述各個步驟並不限於按照上述順序進行操作,在符合工藝要求的前提下,上述不同步驟之間可以顛倒順序或者同時進行,例如令反應氣體和混合物料同時進入到噴嘴1中。
具體的,上述旋浮銅冶煉方法中,優選反應氣體中的氧氣濃度為40%VOL~90%VOL,旋流進入冶煉爐4的流速為220m/s~300m/s,輔助氣體通道噴入反應氣體的流量為10Nm3/h~200Nm3/h,輔助燃料通道107噴入燃料的流量為10Nm3/h~100Nm3/h。上述數值的選擇,能夠使反應充分的進行,以進一步提高冶煉效果。當然,在保證冶煉反應正常進行的前提下,上述參數也可以為其他數值,本實施例對此不做限定。
本說明書中對各部分結構採用遞進的方式描述,每個部分的結構重點說明的都是與現有結構的不同之處,旋浮銅冶煉裝置的整體及部分結構可通過組合上述多個部分的結構而得到。
對所公開的實施例的上述說明,使本領域專業技術人員能夠實現或使用本發明。對這些實施例的多種修改對本領域的專業技術人員來說將是顯而易見的,本文中所定義的一般原理可以在不脫離本發明的精神或範圍的情況下,在其它實施例中實現。因此,本發明將不會被限制於本文所示的這些實施例,而是要符合與本文所公開的原理和新穎特點相一致的最寬的範圍。