工業爐用蓄熱式衝擊傳熱裝置的製作方法
2023-05-03 12:23:16 2
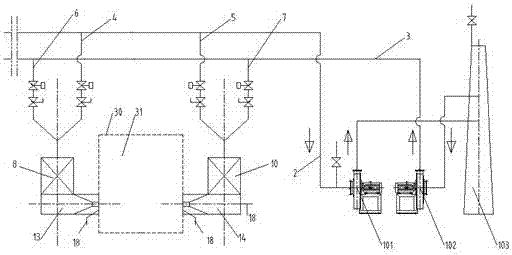
本發明涉及工業工業爐的附屬部件,尤其是採用天然氣、液化氣等作為燃料的工業爐用蓄熱式衝擊傳熱裝置。
背景技術:
採用天然氣、煤氣或燃料油作為燃料的工業爐,其工作原理是將待加熱工件放置在爐膛內,加熱升溫達到工藝要求的溫度,保溫或均溫。在加熱過程中,普遍認為傳熱有三種形式:輻射、對流和傳導加熱。
在加熱之初的低溫階段,主要靠對流傳熱,基本沒有輻射傳熱,或者輻射傳熱效果很差,此階段放置在爐膛內待加熱工件與爐氣間的熱交換能力比較差,導致加熱效率很低。正是由於加熱之初的對流傳熱能力很差,以鍛造工業爐為例,其加熱效率很低,通常在10%以內,某些甚至只有3—5%,能源浪費嚴重;採用蓄熱式燃燒以後,熱效率提高至30-50%左右,已經大幅提高了熱效率,但基本上達到了現階段蓄熱式工業爐廢熱極限回收率,再提高加熱效率很難了。
由於燃料燃燒時溫度較高,如天然氣火焰達到2000℃以上,這樣高溫度的火焰如果直接噴到待加熱工件上,是會燒壞工件的,工件軟化或部分融化等,使工件內部結構產生不利變化,影響性能甚至大幅度降低其相關性能指標,所以是必須避免火焰直接噴到待加熱工件上的,因此現有的技術中提高對流傳熱的手段不多。這就是低溫階段對流傳熱加熱效率很低的主要原因。
現在雖然可以採用高速燃燒器,但是高速燃燒器的火焰必須避免直接噴到待加熱工件上,一般採用將待加熱工件支架起來遠離火焰。對於高溫爐,通常採用平焰燃燒的方式,它們都直接或間接降低對流傳熱效果,對流傳熱係數仍然很低,導致加熱時間較長,燃料消耗較多等。
如何在高溫火焰不直接噴到待加熱工件上的情況下,提高對流傳熱係數,大幅度提高工業爐的加熱效率,以縮短加熱時間、減少燃料消耗、提高爐膛內溫度和氣體的均勻度,是本領域迫切想解決的技術難題。
技術實現要素:
本發明針對現有技術中工業爐在加熱過程中,因對流傳熱係數低,導致加熱效率較低、延長了加熱時間、增大了燃料消耗等不足,提供一種大幅度提高加熱效率的工業爐用蓄熱式衝擊傳熱裝置。
本發明的技術方案:工業爐用蓄熱式衝擊傳熱裝置,其特徵在於:包括對氣體進行加壓的氣體處理裝置,抽氣管路和吹氣管路分別設置在氣體處理裝置的抽氣口和出氣口;在抽氣管路上,分別設置第一抽氣支路和第二抽氣支路,在吹氣管路上,分別設置第一吹氣支路和第二吹氣支路;第一抽氣支路和第一吹氣支路分別在受控狀態下都與第一蓄熱體連通,第一蓄熱體後面的管路上設置有第一開口,作為抽氣的排出口或進氣的吹入口;第二抽氣支路和第二吹氣支路分別在受控狀態下都與第二蓄熱體連通,第二蓄熱體後面的管路上設置有第二開口,作為抽氣的排出口或進氣的吹入口。
進一步的特徵是:在第一開口和第二開口上設置噴嘴,噴嘴的橫截面逐漸縮小。
所述的受控狀態,是在第一抽氣支路、第二抽氣支路和第一吹氣支路、第二吹氣支路上分別設置控制閥,用以通斷每條支路,形成一路進氣、另一路排氣的循環管道。
在每條分支管路上,分別設置自動換向閥和/或手動控制閥。
兩條或四條支路上的自動換向閥聯動設置,同時產生動作,同時控制兩條或四條支路的通斷。
在第一開口與第一蓄熱體之間的管路上,設置第一集氣箱,在第二開口和第二蓄熱體之間的管路上,設置第二集氣箱。
在第一開口與第一蓄熱體之間的管路上,或者第一集氣箱上,設置補充燃氣通道;在第二開口與第二蓄熱體之間的管路上,或者第二集氣箱上,設置補充燃氣通道。
在抽氣管路上設置輔助進氣管道。
還設置有補熱燒嘴,補熱燒嘴與第一開口或第二開口分別連通,補熱燒嘴上設置了燃料進料管和助燃氣體進入管,在受控狀態下將需要的燃料、助燃氣體分別從燃料進料管和助燃氣體進入管通入補熱燒嘴內,再通入爐膛內。
所述氣體處理裝置是兩臺,第一臺氣體處理裝置與第二臺氣體處理裝置是串聯,抽氣管路連接在第一臺氣體處理裝置的進口處,第一臺氣體處理裝置的出口的管路直接連接第二臺氣體處理裝置的進口,第二臺氣體處理裝置的出口連接吹氣管路;或者第一臺氣體處理裝置的出口先連接到氣體存儲腔體,第二臺氣體處理裝置的進口連接氣體存儲腔體,第二臺氣體處理裝置的出口連接吹氣管路。
本發明工業爐用蓄熱式衝擊傳熱裝置,相對於現有技術,具有如下特徵:
1、煙氣經過蓄熱體的熱交換,充分利用熱能,同時被蓄熱體加熱的煙氣的溫度仍然適合直接噴在待加熱工件上,直接加熱工件,顯著提高了加熱效率。
2、被風機強制加速的煙氣,從進氣噴口高速吹入爐膛,強制對流,在直接高速噴在待加熱工件上加熱工件的同時,並產生強制攪動作用,顯著提高對流傳熱係數。
3、從進氣噴口高速吹向爐膛,產生強制攪動作用,提高爐膛內溫度和氣體的均勻度,對工件的加熱更均勻。
4、本發明充分利用蓄熱體作為熱交換媒介,通過蓄熱體加熱煙氣,最大限度利用了燃燒產生的熱量,顯著提高了加熱效率;同時,強制對流並將高溫煙氣直接噴在待加熱工件上,顯著提高對流傳熱係數;經試驗驗證,本發明的加熱效率,在原來的蓄熱式燃燒基礎上再提高20%甚至更高,不誇張地說,是一個重大突破。
5、通過對熱煙氣進行補熱,即在熱煙氣中加入少量的熱量,少量熱量可以由燃料燃燒或電加熱提供,其目的是提高經蓄熱體後熱煙氣的溫度並與爐膛溫度適應,在提高對流能力的同時提高均勻度。
附圖說明
圖1是本發明工業爐用蓄熱式衝擊傳熱裝置結構示意圖;
圖2是本發明工業爐用蓄熱式衝擊傳熱裝置第二實施例結構示意圖;
圖3是本發明工業爐用蓄熱式衝擊傳熱裝置第三實施例結構示意圖。
具體實施方式
如圖1所示,本發明工業爐用蓄熱式衝擊傳熱裝置,包括對氣體進行加壓以提高流速的氣體處理裝置1以及氣體進入氣體處理裝置1的抽氣管路2和氣體排出氣體處理裝置1的吹氣管路3,抽氣管路2和吹氣管路3分別設置在氣體處理裝置1的進氣口和排氣口,氣體處理裝置1就是風機(鼓風機)等,對氣體進行加壓處理,以提高吹氣管路3中氣體的流速。
在抽氣管路2上,分別設置兩條抽氣支路,即第一抽氣支路4和第二抽氣支路5;在吹氣管路3上,分別設置兩條吹氣支路,即第一吹氣支路6和第二吹氣支路7;第一抽氣支路4和第一吹氣支路6上分別設置有控制閥,在受控狀態下都與第一蓄熱體8連通,第一蓄熱體8後面的管路上設置有第一開口9,作為抽氣的排出口或進氣的吹入口;第二抽氣支路5和第二吹氣支路7上分別設置有控制閥,在受控狀態下都與第二蓄熱體10連通,第二蓄熱體10後面的管路上設置有第二開口11,作為抽氣的排出口或進氣的吹入口。工作時,在控制閥作用下,第一開口9、第二開口11,輪流作為抽氣的排出口或進氣的吹入口。
為了提高氣體噴射速度,在第一開口9和第二開口11上設置噴嘴12,噴嘴12的橫截面積逐漸縮小,形成縮口效應以提高流速,形成高速噴口,從噴嘴12內噴出的氣體速度更高,直接噴射到待加熱工件上。噴嘴12的優選結構是圓形,橫截面逐漸縮小的圓錐狀。從噴嘴12噴射的氣體,通常要達到80米/秒以上,速度低的效果不佳,速度太高噪音太大,優選的方案為150米/秒—200米/秒,形成高速流動的氣流。
在第一開口9與第一蓄熱體8之間的管路上,設置第一集氣箱13,在第二開口11和第二蓄熱體10之間的管路上,設置第二集氣箱14,第一集氣箱13與第二集氣箱14的結構可以相同,主要作用是增大管路在第一開口9和第二開口11前的橫截面積,或者噴嘴12前的橫截面積,形成靜壓,利於形成高速噴射。
本發明的受控狀態,是在第一抽氣支路4和第二抽氣支路5、第一吹氣支路6和第二吹氣支路7上分別設置控制閥,用以控制第一抽氣支路4和第二抽氣支路5、第一吹氣支路6和第二吹氣支路7的管路通斷,形成一路進氣、另一路排氣的循環管道;圖中所示,在第一抽氣支路4和第二抽氣支路5、第一吹氣支路6和第二吹氣支路7上,分別設置手動控制閥16和自動換向閥17,手動控制閥16和自動換向閥17串聯結構,手動控制閥16用於在需要時的人工手動操作控制;兩條或四條分支管路上的自動換向閥17可以聯動設置,如採用電磁閥或液壓閥等,同時產生動作,同時通斷,以使換向準確無誤,保證形成煙氣流動的循環通道即可。
在第一開口9與第一蓄熱體8之間的管路上,或者第一集氣箱13上,設置補充燃氣通道18,在需要時打開補充燃氣通道18,向該管路中補充少量燃料,在熱煙氣中加入少量的燃料,提高熱煙氣的溫度與爐膛溫度適應,可以提高中溫和高溫段的對流能力,提高均勻度。在第二開口11與第二蓄熱體10之間的管路上,或者第二集氣箱14上,設置補充燃氣通道18,在需要時打開補充燃氣通道18,向該管路中補充少量燃料。
另外,在較長的加熱時間後,或者爐膛溫度較高后,蓄熱體自身的溫度較高,導致從抽氣管路2進入氣體處理裝置1的氣體溫度較高,可能影響氣體處理裝置1的正常使用,本發明在抽氣管路2上設置輔助進氣管道20,在需要時打開輔助進氣管道20,向抽氣管路2內補充冷空氣,以降低抽氣管路2內氣體的溫度,以保護氣體處理裝置1。當然,在氣體處理裝置1上還需要設置安全排氣管路,在需要時打開,將氣體處理裝置1或吹氣管路3內的氣體向外排出,起到洩壓的作用。
如圖所示的本發明加熱裝置的使用狀態示意圖,本發明的加熱裝置設置在工業爐本體30,工業爐本體30中間的空腔形成爐膛31,待加熱工件放置在爐膛31內被加熱升溫。在爐膛31上,設置兩個開口,第一爐口32和第二爐口33,第一爐口32和第二爐口33分別與爐膛31連通,第一開口9和第二開口11分別設置在第一爐口32和第二爐口33上,密封后其中一個作為進氣口時,另一個則作為排氣口,分別輪流進排氣,分別與氣體處理裝置1的抽氣管路2和吹氣管路3連接,形成循環迴路,形成爐膛31內煙氣的進排氣循環通道。
本發明的工業爐用蓄熱式衝擊傳熱裝置,在工業爐本體30的燃燒裝置燃燒、工業爐膛31以及爐膛31內的待加熱工件時,開啟氣體處理裝置1,並調整管路上的控制閥,將爐膛31內的較高溫度的煙氣從第二開口11排出,通過第二蓄熱體10,進入氣體處理裝置1的抽氣管路2,經氣體處理裝置1加壓處理後,從吹氣管路3排出的高速氣體在吹氣管路3內,經第一蓄熱體8從第一開口9高速進入爐膛31,形成高速衝擊式對流傳熱,高速氣流直接噴到爐膛31內的待加熱工件上,提高對流傳熱效率;調整管路上的控制閥,氣體相應反向流動,爐膛31內的較高溫度的煙氣從第一開口9、第一蓄熱體8排出,進入氣體處理裝置1的抽氣管路2,經氣體處理裝置1加壓處理後,從吹氣管路3排出的高速氣體在吹氣管路3內,經第二蓄熱體10從第二開口11高速進入爐膛31,形成高速衝擊式對流傳熱,高速氣流直接噴到爐膛31內的待加熱工件上,提高對流傳熱效率。在工業爐本體1燃燒加熱過程中,第一蓄熱體8和第二蓄熱體10所在的管路,分別輪流作為進氣、排氣管路,第一開口9和第二開口11分別作為爐膛31的煙氣進氣、排氣出,高溫煙氣通過該管路上的蓄熱體進行熱交換,蓄熱體溫度身高而蓄熱(同時降低了煙氣的溫度,煙氣溫度最低到100℃左右),其中另一個口將經氣體處理裝置1加壓處理後的氣體在通過該管路上的蓄熱體後被加熱,溫度升高的煙氣經該口高速進入爐膛31,形成高速衝擊式對流傳熱;在控制閥的控制作用下,第一蓄熱體8和第二蓄熱體10所在的管路,分別輪流作為進氣、排氣管路,輪流進氣和排氣,形成爐膛31內煙氣流動的循環通道。
本發明,通過第一蓄熱體8和第二蓄熱體10所在的管路,第一蓄熱體8和第二蓄熱體10作為媒介,兩個蓄熱體輪流吸熱和放熱,一個吸收從爐膛31排出的高溫煙氣的熱量儲存在蓄熱體上,使氣體溫度降低進入氣體處理裝置1中加壓處理;從氣體處理裝置1加壓處理後的煙氣,流過第二個蓄熱體時(此時該蓄熱體處於高溫狀態),再加熱煙氣,形成高溫、高流速(高壓)的氣體噴射到爐膛31內,直接作用在待加熱工件上,顯著提高對流傳熱係數;尤其在從低溫升高到高溫的過程中,形成蓄熱式衝擊傳熱,提高對流傳熱係數很多倍,顯著提高加熱效率;經實驗驗證,本發明的加熱效率,在傳統蓄熱燃燒爐的基礎上,至少能再將加熱效率提高20%,甚至更高。
本發明的第一蓄熱體8和第二蓄熱體10,成對設置,其內有供氣體通過的通道和熱交換介質,可以採用現有技術中蓄熱燃燒爐的蓄熱體,作為現有技術在此不做進一步說明。根據實際需要,如果工業爐是多個,或者同一臺工業爐上要設置一個以上的抽氣口和吹氣口,則可以在抽氣管路2和吹氣管路3上設置多路第一抽氣支路、第二抽氣支路和第一吹氣支路和第二吹氣支路,用本裝置同時向多個工業爐提供煙氣,或者向同一臺工業爐通過一個以上的抽氣口和吹氣口多路抽氣和吹氣,形成煙氣的循環通路,各自循環使用。
圖2所示的本發明的第二種實施例結構中,與圖1相同的部分不再介紹,其區別點如下:氣體處理裝置1是兩臺,或兩臺以上,圖中是串聯結構,第一臺氣體處理裝置101與第二臺氣體處理裝置102是串聯,抽氣管路2連接在第一臺氣體處理裝置101的進口處,第一臺氣體處理裝置101的出口的管路直接連接第二臺氣體處理裝置102的進口,第二臺氣體處理裝置102的出口連接吹氣管路3;或者第一臺氣體處理裝置101的出口先連接到氣體存儲腔體103,將氣體通入氣體存儲腔體103內緩存;第二臺氣體處理裝置102的進口連接氣體存儲腔體103,第二臺氣體處理裝置102的出口連接吹氣管路3;還有不同點是補充燃氣通道18還可以直接通入爐膛31內,直接向爐膛31內按照需要補充一定量的燃氣。
如圖3所示,本發明的第三種實施例結構,與圖1相同的部分不再介紹,其區別點如下:設置了補熱燒嘴21,補熱燒嘴21與第一開口9或第二開口11分別連通,補熱燒嘴21上設置了燃料進料管22和助燃氣體進入管23,在受控狀態下將需要的燃料、助燃氣體分別從燃料進料管22和助燃氣體進入管23通入補熱燒嘴21內,再分別從第一開口9或第二開口11流入爐膛。
爐膛31上,也可以設置帶有控制閥洩氣管路,需要時打開洩壓,保證爐膛內爐氣的壓力正常,起到安全作用。
最後需要說明的是,以上實施例僅用以說明本發明的技術方案而非限制技術方案,儘管申請人參照較佳實施例對本發明進行了詳細說明,本領域的普通技術人員應當理解,那些對本發明的技術方案進行修改或者等同替換,而不脫離本技術方案的宗旨和範圍,均應涵蓋在本發明的權利要求範圍當中。