一種推板式模塊化動態煅燒爐的製作方法
2023-04-23 23:53:12 2
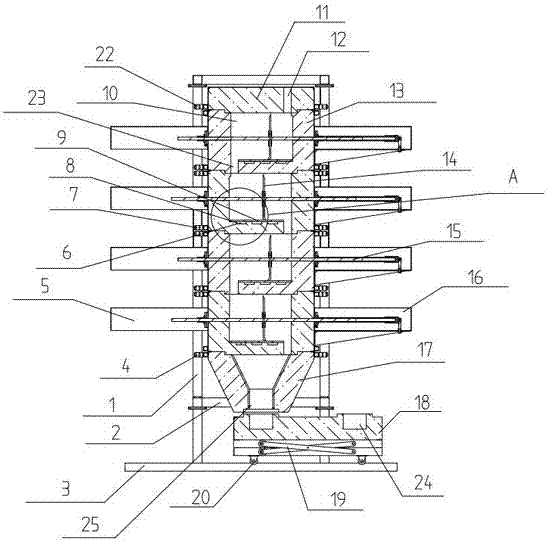
本發明涉及機械製造熱處理領域,尤其涉及一種推板式模塊化動態煅燒爐。
背景技術:
目前,公知的對粉狀物料或微小顆粒狀物料一般採用靜態及半動態煅燒,而靜態或半動態煅燒在工作過程中,由於物料與熱介質不能充分交換,因而造成能源浪費大,煅燒效率低,產品質量不穩定等缺陷,尤其對於半動態煅燒設備來說,還涉及機械傳動部分,因此結構複雜,維修保養不方便。而傳統的煅燒設備在處理一些物料時會產生強酸強鹼性氣體,設備的耐腐蝕性能差,使用壽命低。而目前市場主流設備主要是利用磁性力、電力、機械力等在攪拌或翻騰的狀態下被加熱的煅燒爐,常見有震動煅燒爐、攪動煅燒爐、迴轉窯等,而這些爐型是目前對非金屬礦產品、耐火材料、矽酸鹽原料進行熱處理加工的重要爐型,這些爐型加工溫區單一,對加工工藝複雜需要多段溫區進行處理的物料,就需要再次反覆處理。整個過程過於繁瑣,換料過於麻煩,影響這個處理過程的效率。
技術實現要素:
本發明的目的是提供了一種推板式模塊化動態煅燒爐,針對當前動態煅燒爐溫度不均勻、熱效率低、防腐性能差、自動化程度低,煅燒溫區單一而設計一種煅燒爐,實現物料爐內停留時間可自主控制、多溫區加熱、溫度均勻、熱效率高、超高耐腐蝕性、自動化程度高、更環保的目的。
本發明的目的可採用如下技術方案來實現:
一種推板式模塊化動態煅燒爐,由基體框架、爐體總成和接料小車構成,所述的爐體總成由多層爐體模塊疊加而成,並和基體框架通過螺栓連接;每一層爐體模塊由殼體、底板、爐門、爐體耳板,下料口、推料杆、推料板、推桿託架、進給機構、加熱元件、集料槽構成,所述爐體模塊殼體為長方體結構,上部敞開,上部設置成凹形槽,下部設置有凸出臺階,爐體耳板設置在爐體模塊殼體的兩側通過螺栓和基體框架連接,爐體模塊殼體的下部突出臺階設置在下一層爐體模塊上部的凹形槽內;爐體模塊中心為爐膛,爐膛底部設置底板,底板下部的爐膛上設置有安裝槽,加熱元件矽碳加熱棒設置在安裝槽內,下料口設置在殼體底部一側;推桿託架和進給機構分別設置在殼體外兩側;推料板垂直設置在爐膛內,推料杆水平設置在爐體內腔,推料杆中部和推料板中央垂直連接,推料杆的兩端伸出爐體殼體左右外側,一端設置在推桿託架上,另一端與進給機構連接,爐門設置在爐體殼體的前面,通過轉軸設置在爐體殼體上;集料槽設置爐體總成的最底部,底層的爐體模塊底部的凸出臺階上與集料槽上部連接,集料槽下部設置接料小車;相鄰的兩層爐體模塊在疊加設置時爐體模塊殼體底部的下料口設置的位置為交錯設置,下層的爐體模塊下料口設置在上層爐體模塊下料口相反一側;爐體總成上最頂層設置有上蓋板,上蓋板設置在上部的凹形槽內,上蓋板上面一側設置有進料口。
所述的基體框架由立柱、小車軌道和橫梁構成,立柱垂直設置在框架的四周,橫梁設置在立柱之間並與立柱連接,小車軌道橫向設置在基體框架底部;所述的接料小車設置在基體框架底部的小車軌道上。
所述的接料小車設置在基體框架底部,接料小車的上部為小車料鬥;小車料鬥的中部設置舉升器,舉升器為剪刀支撐架結構,小車的底部設置有底盤,底盤兩側設置有車輪。
所述的爐體模塊爐膛上的安裝槽與爐體外部接線箱連通,從爐體外部安裝矽碳加熱棒插入到底板下方,底板採用石英材質製成。
所述的上下相鄰兩層爐體模塊內的推料板設置運動的方向相反,推料板為石英材料製成。
所述爐體模塊的推料杆為t形結構,一端為圓柱形,另一端為連接法蘭,分別設置在推料板的兩側;推料板一側的推料杆圓柱部分設置在推料託架內,連接法蘭和推料板連接,推料板另一側的推料杆圓柱部分設置在進給機構內,連接法蘭和推料板連接,推料板兩側的推料杆軸線同軸。
所述的爐體模塊進給機構由電機和減速器構成,控制電機的轉速來控制推料杆的推進速度,並控制推料板的推進速度。
所述的爐體總體集料槽為倒錐形,兩側的集料槽耳板與基體框架通過螺栓連接,集料槽上部與爐體總成中的底層爐體模塊連接,集料槽下部出料口設置有內凹槽,與接料小車上的接料槽位置對應,集料槽為石英材料製成。
所述的小車料鬥上部設置有雙工位接料槽,接料槽上部設置有凸出臺階,與集料槽下部的內凹槽結合,小車採用電動定時控制接料切換工位,小車料鬥採用氧化鋁纖維製成。
所述的爐體模塊的爐膛為氧化鋁纖維爐膛。
本發明由於採用如上所述的技術方案,本發明具有如下優越性:物料自上而下進入加熱組,靠推板完成物料加熱過程中的運動,發熱原件在加熱底板底部,相當於物料在底板上運動,受熱均勻,更節能、更環保、熱效率更高,噪音更低,模塊化設計互換性高、易維修、易更換,每層加熱組單獨控制溫度,同時可以把溫度控制在精確範圍內,推料板的推動速度、每組的加熱溫度用戶可根據自身需求,自主設定,用途更廣,更多元化,內部採用防腐處理設計,防腐性能更高,底部設計雙工位接料小車,自主完成工位切換,節省人力。
附圖說明
圖1為本發明的內部結構示意圖。
圖2為圖1的側面結構示意圖。
圖3為圖1中的a處放大示意圖
圖中:1、立柱,2、橫梁,3、小車軌道,4、集料槽耳板,5、推桿託架,6、安裝槽,7、爐體耳板,8、矽碳加熱棒,9、底板,10、內腔,11、上蓋板,12、進料口,13、殼體,14、推料板,15、推料杆,16、進給機構,17、集料槽,18、小車料鬥,19、剪刀支撐架,20、車輪,21、接線箱,22、上蓋板耳板,23、下料口,24、接料槽,25、出料口,26、爐門。
具體實施方式
下面結合附圖和具體實施方式對本發明作進一步描述:
通過下面的實施例可以詳細的解釋本發明,公開本發明的目的旨在保護本發明範圍內的一切技術改進。
如附圖1、圖2所示的一種推板式模塊化動態煅燒爐,由基體框架、爐體總體和接料小車構成,所述的基體框架為框架結構的鋼結構框架,由立柱1、橫梁2和小車軌道3構成,立柱1垂直設置在框架的四周,橫梁2設置在立柱之間並與立柱連接,基體框架底部橫向設置有小車軌道3;所述的爐體總成由層爐體模塊疊加而成,並和基體框架連接;每層個爐體模塊由殼體13、底板9、內腔10、爐門25、爐體耳板7、上蓋板11、進料口12、下料口23、推料杆15、推料板14、推桿託架5、進給機構16、矽碳加熱棒8、集料槽17構成,所述爐體模塊殼體13為長方體結構,上部敞開,上部設置成凹形槽,下部設置有凸出臺階,這種設計可以提高爐體模塊之間的密封性;爐體耳板7設置在爐體模塊殼體13的兩側通過螺栓和基體框架連接,殼體13底部下料口23設置在凸出臺階上的一側,下料口23設置的位置為交錯設置,下部爐體模塊下料口23設置在上部爐體模塊下料口23相反方向一側;爐體模塊殼體13的下部突出臺階設置在下一級爐體模塊上部的凹形槽內;爐體模塊中心為內腔10,底板下部的爐膛上設置有安裝槽6,加熱元件設置在安裝槽6內,加熱元件為矽碳加熱棒8,爐體模塊底板9下的安裝孔8與爐體外部接線箱21連通,從爐體外部安裝矽碳加熱棒8插入到底板9下方,方便安裝更換矽碳加熱棒8,爐體內腔10採用優質氧化鋁纖維爐膛,底板9採用石英材質製成,增加爐體的耐高溫性和耐腐蝕性;推料板14垂直設置在爐體內腔10內,推料板14前板面底部設置成刨刀形,前板面的底部一段向前傾斜面,底邊和內腔10中底板9接近,前板面的上部一段向後設置一斜面,推料板14的中心設置有與推料杆15法蘭連接的連接孔,上下相鄰兩層爐體模塊內推料板14推料方向相反,推料板14為石英材料製成,增加推料板的耐高溫性和耐腐蝕性;推料杆15水平設置在爐體內腔10內,推料杆15和推料板14中央垂直連接,推料杆15的兩端伸出殼體13體左右外側,一端設置在推桿託架5上,另一端與進給機構16連接,推料杆15為t形結構,一端為圓柱形,另一端為連接法蘭,分別設置在推料板14的兩側;推料板15一側的推料杆15圓柱部分設置在推料託架5內,連接法蘭和推料板連接,推料板另一側的推料杆15圓柱部分設置在進給機構16內,連接法蘭和推料板14連接,推料板14兩側的推料杆軸線同軸;進給機構16由電機和減速器構成,控制電機的轉速來控制推料杆的推進速度,並控制推料板的推進速度,通過控制推進的速度達到最佳的加熱效果;上蓋板11設置在最上級爐體殼體13的上部凹形槽內,上蓋板11上面一側設置有進料口12,下面設置有凸出臺階,兩側設置有上蓋板耳板22,上蓋板耳板2與基體框架立柱1連接;爐門26設置在爐體殼體13的前面;通過轉軸設置在爐體殼體13上,爐門26可以提供很好的檢修窗口和檢查口;集料槽17設置在最底部的爐體模塊底部的凸出臺階上與爐體模塊連接,集料槽17為倒錐形,倒錐形可以提高收料的效果;兩側的集料槽耳板4與基體框架立柱1通過螺栓連接,集料槽17上部與底部爐體模塊連接,下部出料口25設置有內凹槽,與接料小車上的料鬥24位置對應,,集料槽17為石英材料製成,增加了集料槽17的耐高溫性和耐腐蝕性;所述的接料小車設置在基體框架底部的小車軌道3上,接料小車的上部為小車料鬥18,接料小車的中部設置有剪刀支撐架19結構,剪刀支撐架19可以調整小車的高低,小車的底部設置車輪20,小車料鬥18上部設置有雙工位接料槽24,接料槽24上部設置有凸出臺階,與集料槽17下部的內凹槽結合,通過凸出臺階和內凹槽的接合,能夠達到很好的密封效果;小車採用電動定時控制,自動接料工位,自動切換工位,降低了操作者的勞動強度,小車料鬥18採用氧化鋁纖維製成。
在加熱物料時,先通過加料設備給爐體總體的上蓋板進料口加入,物料進入最上部的爐體模塊內爐體模塊底部開始加熱,同時內部的推料板開始把物料慢慢的向進料口的反向推進,在推進的過程中不斷的加熱翻轉,物料被推到下料口後,進入下部的爐體模塊內,下部的爐體模塊開始加熱,並啟動這級爐體模塊的推料板向這級爐體模塊的下料口推進,直到完成本級加熱送到下一級,下部的幾級依次完成加熱,到達底部的集料槽內,通過集料槽出料口進入小車料鬥上的接料槽內,接料槽加滿後自動切換另一個接料槽,完成整個操作過程。
本發明未詳述部分為現有技術。