一種用於分體蒸發器的連續處理系統及方法與流程
2023-04-29 15:56:41 4
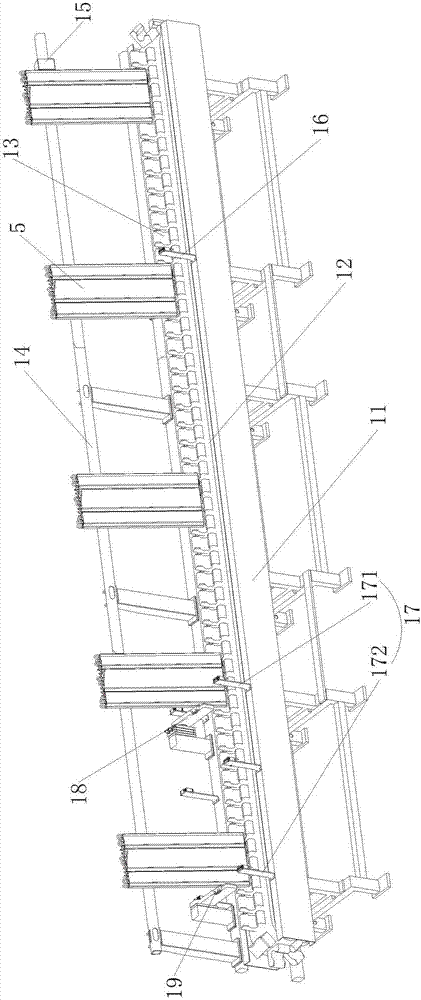
本發明涉及分體蒸發器的連續處理技術,具體涉及一種用於分體蒸發器的連續處理系統及方法。
背景技術:
隨著工業時代的不斷發展,同時面臨國內人口紅利的消失和人工成本的大幅度提升,國內幾乎所有大型工廠都在尋求各種形式的工業自動化舉措,現代工廠對自動化、智能化和數位化的需求越來越明顯。
在空調自動化領域中,分體蒸發器的切割組裝摺彎等工序現在幾乎全部依賴人工,這主要是因為分體蒸發器的成型工藝中,如穿管、脹管和脫脂烘乾等工序都會直接導致成品的整體尺寸偏差較大,同時存在應力不均和熱變形等異常,都會導致形位公差要求較高的分體蒸發器的切割、折彎等工藝的自動化難以實現,從而導致人工成本高、勞動強度大、生產效率低下。
技術實現要素:
本發明的目的在於克服上述技術不足,提出一種用於分體蒸發器的連續處理系統,其實現了供料、切割、折彎的自動化,降低了人力成本、提高了生產效率,同時還提供一種用於分體蒸發器的連續處理方法。
為達到上述技術目的,本發明的技術方案提供一種用於分體蒸發器的連續處理系統,包括,
供料裝置,所述供料裝置配置用於連續的將所述分體蒸發器輸送至設定位置;
切割裝置,所述切割裝置配置用於對所述分體蒸發器進行定位並按設定的切割線對定位後的所述分體蒸發器進行切割;
折彎裝置,所述折彎裝置配置用於將所述分體蒸發器折彎至設定角度;及
機械手臂,所述機械手臂配置用於抓取所述供料裝置上設定位置的所述分體蒸發器並將其依次移動至所述切割裝置和所述折彎裝置。
優選的,所述供料裝置包括:
架體;
設於所述架體上的輸送帶;
沿所述輸送帶長度方向均勻布置於所述輸送帶的輸送面上的多個下定位塊,所述下定位塊用於定位所述分體蒸發器下端;
設於所述輸送帶上方並用於支撐所述分體蒸發器上端的支撐橫梁;
設於所述支撐橫梁上的上定位塊,所述上定位塊靠近所述輸送帶的進料端設置;及
沿所述輸送帶運動方向依次設於所述架體上的放料傳感器和取料傳感器,所述放料傳感器配置用於感應到所述分體蒸發器時控制所述輸送帶停止運動一定時長,所述取料傳感器配置用於感應到所述分體傳感器時控制所述輸送帶停止運動;
所述切割裝置包括:
具有一條形切割孔的工作檯;
設於所述工作檯上的切割臺;
定位機構,所述定位機構包括設於所述工作檯上的定位氣缸和放置於切割臺上的定位杆,所述定位氣缸的活塞杆的自由端與所述定位杆連接並能夠驅動所述定位杆於所述切割臺上作往返運動;
壓緊機構,所述壓緊機構包括壓緊塊和驅動壓緊塊將分體蒸發器緊壓於所述切割臺上的壓緊氣缸;
切割機構,所述切割機構包括一設於所述切割孔下方的滑軌,一端滑動設置於所述滑軌上、另一端穿過所述切割孔並延伸至所述工作檯上表面的滑塊,設於所述滑塊上的切刀,驅動所述滑塊沿所述滑軌作往返運動的伺服電機;
所述折彎裝置包括操作臺、設於所述操作臺上的折彎臺、配合設置於折彎臺上方並用於將分體蒸發器緊壓固定於所述折彎臺上的壓緊部件、設於所述操作臺下表面的頂壓氣缸,所述頂壓氣缸的活塞杆穿過操作臺上的頂壓孔與第一頂壓板連接並驅動所述第一頂壓板作上下垂直往返運動,所述第一頂壓板上設置有球形槽,所述球形槽內配合設置有球頭關節,所述球頭關節自由端與一用於頂壓突出於折彎臺的分體蒸發器的第二頂壓板固定連接。
優選的,所述取料傳感器包括沿輸送帶運動方向依次布置的第一取料傳感器和第二取料傳感器,所述第一取料傳感器和所述第二取料傳感器之間設有一可擺動的第一擋塊,所述第一擋塊配置用於當所述第二取料傳感器感應到分體蒸發器時控制所述第一擋塊擺動至所述下定塊上方並阻止分體蒸發器繼續通過;所述輸送帶出料端設有一用於阻止所述分體蒸發器通過的第二擋塊,所述取料傳感器靠近所述第二擋塊設置。
優選的,所述下定位塊上設置有一定位槽,所述分體蒸發器的下端置於所述定位槽內,且所述下定位塊相對所述支撐橫梁一側向上延伸形成一用於支撐所述分體蒸發器側壁的支撐靠背。
優選的,所述放料傳感器和上定位塊在輸送帶上的相對距離與所述第一取料傳感器和所述第二取料傳感器之間的距離相同設置。
優選的,所述壓緊機構還包括一端與所述壓緊塊連接的壓杆及一支撐座,所述支撐座和壓緊氣缸均一端固定於所述工作檯上、另一端與所述壓杆鉸接,所述壓緊氣缸能夠驅動所述壓杆以支撐座為軸心旋轉並使壓緊塊作遠離和靠近所述切割臺的運動;所述切割機構還包括一與所述伺服電機連接的減速器、與所述減速器連接的同步輪、與所述同步輪連接的同步帶,所述同步帶與所述滑塊連接並帶動所述滑塊於所述滑軌上運動;其中,所述切割臺、定位氣缸、壓緊機構均為兩個,且均一一對應設置。
優選的,兩個所述定位氣缸均與所述定位杆鉸接,使其中一所述定位氣缸能夠驅動定位杆相對另一定位氣缸旋轉;兩個所述切割臺沿切割孔長度延伸方向依次布置。
優選的,所述球形槽至少為兩個且沿第一頂壓板長度延伸方向依次布置,每個所述球形槽內均配合設置有球頭關節,每個球頭關節自由端均垂直固定於所述第二頂壓板上;其中,每個所述球頭關節的長度均相同設置。
優選的,所述折彎裝置還包括一固定於所述操作臺下表面的固定支架,所述固定支架呈直角三角形,且一直角邊固定於操作臺下表面,所述頂壓氣缸固定於另外一直角邊上。
同時,本發明還提供一種用於分體蒸發器的連續處理方法,包括如下步驟:
(1)將加工成型的分體蒸發器通過供料裝置連續輸送至設定位置;
(2)通過機械手臂將設定位置的分體蒸發器抓取並移動至切割裝置上,切割裝置對分體蒸發器進行定位並按設定的切割線對分體蒸發器進行切割;
(3)機械手臂將切割後的分體蒸發器抓取並移動至折彎裝置,折彎裝置將所述分體蒸發器折彎至設定角度。
與現有技術相比,本發明通過供料裝置實現分體蒸發器的連續供料,並通過切割裝置對分體蒸發器定位後切割,有利於提高切割的準確性,同時通過折彎裝置對切割後的分體蒸發器進行折彎,實現了分體蒸發器的供料、切割、折彎的自動化連續生產,進而提高了生產效率、降低了生產成本。
附圖說明
圖1是本發明的用於分體蒸發器的連續處理系統的連接結構示意圖;
圖2是本發明的供料裝置的立體結構示意圖;
圖3是本發明的下定位塊的立體結構示意圖;
圖4是本發明的切割裝置的切割立體示意圖;
圖5是本發明的切割裝置的主視結構示意圖;
圖6是本發明的圖5的左視圖;
圖7是本發明的折彎裝置的連接結構示意圖;
圖8是本發明的頂壓氣缸與第二頂壓板的立體連接結構示意圖。
具體實施方式
為了使本發明的目的、技術方案及優點更加清楚明白,以下結合附圖及實施例,對本發明進行進一步詳細說明。應當理解,此處所描述的具體實施例僅僅用以解釋本發明,並不用於限定本發明。
請參閱附圖1,本發明的實施例提供了一種用於分體蒸發器的連續處理系統,包括,
供料裝置1,所述供料裝置1配置用於連續的將所述分體蒸發器5輸送至設定位置;
切割裝置2,所述切割裝置2配置用於對所述分體蒸發器5進行定位並按設定的切割線對定位後的所述分體蒸發器5進行切割;
折彎裝置3,所述折彎裝置3配置用於將所述分體蒸發器5折彎至設定角度;及
機械手臂4,所述機械手臂4配置用於抓取所述供料裝置1上設定位置的所述分體蒸發器5並將其依次移動至所述切割裝置2和所述折彎裝置3。其中,本實施例的機械手臂4可採用現有技術的機械式抓取裝置,在此不作贅述。
請參閱附圖2,所述供料裝置1包括,
架體11;
設於所述架體11上的輸送帶12;
沿所述輸送帶12長度方向均勻布置於所述輸送帶12的輸送面上的多個下定位塊13,所述下定位塊13用於定位所述分體蒸發器5下端;
設於所述輸送帶12上方並用於支撐所述分體蒸發器5上端的支撐橫梁14;
設於所述支撐橫梁14上的上定位塊15,所述上定位塊15靠近所述輸送帶12的進料端設置;及
沿所述輸送帶12運動方向依次設於所述架體11上的放料傳感器16和取料傳感器17,所述放料傳感器16配置用於感應到所述分體蒸發器5時控制所述輸送帶12停止運動一定時長,所述取料傳感器17配置用於感應到所述分體傳感器5時控制所述輸送帶12停止運動,並給出抓取裝置取料信號。
具體的,其操作流程如下,首先人工將託盤上的分體蒸發器5放置於輸送帶12的進料端,且分體蒸發器5下端置於下定位塊13上、上端倚靠於支撐橫梁14上,使得分體蒸發器5稍微傾斜設置,以保證分體蒸發器5在輸送帶12上運動時不會傾倒,同時放置時根據上定位塊15進行精準定位;然後啟動供料裝置1,輸送帶12開始轉動,分體蒸發器5隨下定位塊13運動,當分體蒸發器5運動至放料傳感器16時,放料傳感器16感應到該分體蒸發器5,控制輸送帶12停止運動一定時間,具體時間可根據需要設置,本實施例可將其設置為3秒,在輸送帶12停止運動的3秒時間內,操作人員再次放置第二個分體蒸發器5於輸送帶12的進料端,放置要求同第一個分體蒸發器5相同,3秒後,輸送帶12繼續運動,當第二個分體蒸發器5運動至放料感應器16時,再次停止運動3秒,可放置第三個分體蒸發器5於輸送帶12的進料端,依次類推可不間斷的循環向所述輸送帶12上放置分體蒸發器5,實現連續上料;而當第一個分體蒸發器5隨輸送帶12運動至取料感應器17時,取料蒸發器17感應到該分體蒸發器5,控制輸送帶12停止運動,以避免分體蒸發器5從輸送帶12的出料端掉出,同時等待機械手臂4將第一個分體蒸發器5抓取,當機械手臂4將第一個分體蒸發器5抓取離開後,取料傳感器17感應不到該分體蒸發器5,然後驅動輸送帶12繼續運動,至第二個分體蒸發器5運動至取料傳感器17時,輸送帶12再次停止運動等待機械手臂4,如此循環實現連續供料。其中,操作者在等待機械手臂4的過程中可檢查分體蒸發器5在輸送帶12上的放置狀況,避免因放置質量較差導致機械手臂4的抓取困難。而且,需要說明的是,本實施例中放料傳感器16和取料傳感器17通過感應控制輸送帶12的停止和運動為本領域的常規技術,其具體控制過程在此不作贅述。
進一步的,為了提高生產效率,可將所述取料傳感器17設置為包括沿輸送帶12運動方向依次布置的第一取料傳感器171和第二取料傳感器172,機械手臂4可設置為兩個或多個,可分別依次抓取與第一取料傳感器171、第二取料傳感器172相對應的分體蒸發器5,或同時抓取上述兩個分體蒸發器5,以提高機械手臂4的抓取效率。而為了避免重複供料,本實施例在所述第一取料傳感器171和所述第二取料傳感器172之間設有一可擺動的第一擋塊18,所述第一擋塊18配置用於當所述第二取料傳感器172感應到分體蒸發器5時控制所述第一擋塊18擺動至所述下定塊13上方並阻止分體蒸發器5通過,即當所述第二取料傳感器172未感應到分體蒸發器5時,第一擋塊18擺動至遠離輸送帶12一側,分體蒸發器5可順利通過並隨輸送帶12運動,當所述第二取料傳感器172感應到分體蒸發器5時,第一擋塊18擺動至下定位塊13上方,分體蒸發器5不能繼續隨輸送帶12運動。在具體設置時,所述放料傳感器16和上定位塊15在輸送帶12上的相對距離與所述第一取料傳感器171和所述第二取料傳感器172之間的距離相同設置,以保證相鄰兩個分體蒸發器5同時分別被第一取料傳感器171和第二取料傳感器172感應到,更好的配合第一擋塊18實現重複供料。其中,上述相對距離指的是上定位塊15在輸送帶12上的投影與放料傳感器16之間的距離,即放料傳感器16和上定位塊15在輸送帶12所在平面的距離,若將上述相對距離設置為a,將第一取料傳感器171和第二取料傳感器172之間的距離設置為b,則a和b相同。
而為了避免分體蒸發器5從輸送帶12上直接從其出料端掉落,本實施例所述供料裝置1在所述輸送帶12的出料端設有一用於阻止所述分體蒸發器5通過的第二擋塊19,所述取料傳感器17靠近所述第二擋塊19設置,通過第二擋塊19的設置避免因設備故障而導致分體蒸發器5掉落,避免分體蒸發器5掉落損壞。
由於分體蒸發器5相對輸送帶12稍微傾斜設置,為了避免分體蒸發器5相對下定位塊13滑動,增加下定位塊13的定位效果,請參閱附圖3,本實施例在所述下定位塊13上設置有一定位槽131,所述分體蒸發器5的下端置於所述定位槽131內,具體設置時,定位槽131的形狀應與分體蒸發器5的下端相配合。
當分體蒸發器5隨下定位塊13運動時,分體蒸發器5上端會與支撐橫梁14發生摩擦,一方面容易損壞分體蒸發器5,導致保護性磨損,另一方面當上述摩擦力較大時易導致分體蒸發器5運動過程中傾倒,故所述下定位塊13相對所述支撐橫梁14一側向上延伸形成一用於支撐所述分體蒸發器5側壁的支撐靠背132,通過支撐靠背132的設置減少了支撐橫梁14給予分體蒸發器5的支撐力,進而減少了分體蒸發器5與支撐橫梁14之間的摩擦力。
為了提高檢測的準確性,本實施例所述放料傳感器16和取料傳感器17均為對射式傳感器,所述對射式傳感器的發射端和接收端分別設於所述輸送帶12的兩側。
請參閱附圖4~6,所述切割裝置2包括,
具有一條形切割孔211的工作檯21;
設於所述工作檯21上的切割臺22;
定位機構23,所述定位機構23包括設於所述工作檯21上的定位氣缸231和放置於切割臺22上的定位杆232,所述定位氣缸231的活塞杆的自由端與所述定位杆232連接並能夠驅動所述定位杆232於所述切割臺22上作往返運動;
壓緊機構24,所述壓緊機構24包括壓緊塊241和驅動壓緊塊241將分體蒸發器5緊壓於所述切割臺22上的壓緊氣缸242;
切割機構25,所述切割機構25包括一設於所述切割孔211下方的滑軌251,一端滑動設置於所述滑軌251上、另一端穿過所述切割孔211並延伸至所述工作檯21上表面的滑塊252,設於所述滑塊252上的切刀253,驅動所述滑塊252沿所述滑軌251作往返運動的伺服電機254。
為了提高生產效率,本實施例將兩個切割裝置2方向相對設置,以形成一種自動切割系統,該兩個切割裝置2方向相對抵接,有利於提高工作檯的整體重量和結構的穩定性,以便於後續與機械手臂4之間的配合。
切割時,如附圖4所示,機械手臂4將抓取的分體蒸發器5放置於切割臺22上,而為了將分體蒸發器5緊壓於切割臺22上,一般需通過下壓的方式給予分體蒸發器5壓力,本實施例則通過槓桿力傳遞的方式實現下壓。具體的,本實施例所述壓緊機構24還包括一端與所述壓緊塊241連接的壓杆243及一支撐座244,所述支撐座244和壓緊氣缸242均一端固定於所述工作檯21上、另一端與所述壓杆243鉸接,所述壓緊氣缸242能夠驅動所述壓杆243以支撐座244為軸心旋轉並使壓緊塊241作遠離和靠近所述切割臺22的運動,具體的壓杆243以支撐座244與壓杆243的鉸接軸為軸心旋轉。本實施例的壓緊機構23具體連接可採用兩種方式:第一種為所述支撐座244設置於壓緊氣缸242和壓緊塊241之間,即支撐座244鉸接於壓杆243的靠近中部的位置,通過壓緊氣缸242向上頂實現壓杆243另一端的壓緊塊241下壓;第二種則是壓緊氣缸242設置於支撐座244與壓緊塊241之間,即壓緊氣缸242鉸接於壓杆243的靠近中部的位置,通過壓緊氣缸242下拉實現壓杆243另一端的壓緊塊241下壓。上述兩種方式均能夠實現壓緊塊241的下壓,為了便於描述,本實施例採用第一種下壓方式,且第一種下壓方式也是本實施例的優選方式。而為緊壓的穩定性,本實施例在壓緊塊241一側面上設置有橡膠層245,一方面可以更好的將分體蒸發器5緊壓與切割臺22上,另一方面避免壓緊塊241緊壓時損壞分體蒸發器5。
其中,為了便於切割的精確性,通過滑軌251和切割孔211將滑塊252較好的固定,本實施例優選採用滑塊252下端配合套設於滑軌251上,且滑塊252與切割孔211的寬度配合設置,以避免滑塊252相對切割孔211發生晃動導致分體蒸發器5的切割面參差不齊。為了與滑塊252配合驅動切刀253,所述切割機構25還包括一與所述伺服電機254連接的減速器255、與所述減速器255連接的同步輪256、與所述同步輪256連接的同步帶257,所述同步帶257與所述滑塊252連接並帶動所述滑塊252於所述滑軌251上運動,通過同步帶257帶動滑塊252相對滑軌251和切割孔211運動,進而帶動切刀253切割分體蒸發器5,有利於提高切割效率。
為了提高分體蒸發器5的定位、固定的準確性和穩定性,所述切割臺22、定位氣缸231、壓緊機構24均為兩個,且均一一對應設置,當分體蒸發器5放置於切割臺22上後,通過兩點定位提高了定位精度。由於在定位、固定時,機械手臂4上的擋塊是相對切割孔211平行設置的,為了提高定位、固定的便捷性,本實施例將兩個所述切割臺22沿切割孔211長度延伸方向依次布置,即兩個切割臺22中軸線的連線與切割孔211保持平行,對應的,兩個定位氣缸211和壓緊機構24也沿切割孔211長度延伸方向布置,以保持整體切割裝置2的對稱性。
而且,機械手臂4將分體蒸發器5放置於切割臺22上時,分體蒸發器5不可避免的相對切割孔211具有一個傾斜角度,由於兩個定位氣缸231相對切割孔211是平行設置的,易導致定位杆232兩端受力不均,故本實施例將兩個所述定位氣231缸均與所述定位杆232鉸接,使其中一所述定位氣缸231能夠驅動定位杆232相對另一定位氣缸231旋轉,從而保證了定位杆232可多角度的給予分體蒸發器5以推力,避免定位杆232因兩側受力不均被定位氣缸321推拉損壞。同時,定位杆232兩端能夠分別給予分體蒸發器5壓力,使分體蒸發器5一側能夠緊密抵接至機械手臂4上的擋塊,避免因分體蒸發器5的不規則性導致定位的準確性降低。
請參閱附圖4~6,本實施例的切割裝置2的工作流程如下:首先通過機械手臂4將供料裝置1上的分體蒸發器5抓至切割臺22上,機械手臂4末端的夾爪鬆開,定位機構23的兩個定位氣缸231工作,通過定位杆232推動分體蒸發器5抵緊夾爪上的擋塊,實現分體蒸發器5寬度方向校準至垂直於分體蒸發器5上的實切線,同時實切線也能夠位於切刀253運動軌跡為基準的±1mm的偏差範圍內;定位完畢後,壓緊結構24的壓緊氣缸242作用,驅動壓緊塊241緊壓於分體蒸發器5上,同時機械手臂4上夾爪也會夾緊分體蒸發器5,進而將分體蒸發器5固定於切割臺22上;最後,伺服電機254驅動切刀253運動,並將分體蒸發器5快速切割,從而完成了分體蒸發器5的高精度自動切割。
請參閱附圖7~8,折彎裝置3包括操作臺31、設於所述操作臺31上的折彎臺32、配合設置於折彎臺32上方並用於將分體蒸發器5緊壓固定於所述折彎臺32上的壓緊部件33、設於所述操作臺31下表面的頂壓氣缸34,所述頂壓氣缸34的活塞杆穿過操作臺31上的頂壓孔與第一頂壓板35連接並驅動所述第一頂壓板35作上下垂直往返運動,所述第一頂壓板35上設置有球形槽,所述球形槽內配合設置有球頭關節36,所述球頭關節36自由端與一用於頂壓突出於折彎臺32的分體蒸發器5的第二頂壓板37固定連接。
在上述切割裝置2完成切割後,機械手臂4將分體蒸發器5移動至折彎臺32上,通過壓緊部件33將分體蒸發器5緊壓於折彎臺32上,然後通過頂壓氣缸34頂壓驅動第一頂壓板35作垂直向上的運動,第一頂壓板35通過球頭關節36轉變力的方向並傳遞給第二頂壓板37,第二頂壓板37一側面頂壓住突出於折彎臺32的分體蒸發器5的下表面,分體蒸發器5在第二頂壓板37頂壓作用下被折彎,且在球頭關節36的不斷轉向的力的傳遞作用下,第二頂壓板37持續給予分體蒸發器5以頂壓力,直至分體蒸發器5被折彎到設定的彎折角度。
具體的,所述球形槽至少為兩個且沿第一頂壓板35長度延伸方向依次布置,每個所述球形槽內均配合設置有球頭關節36,每個球頭關節36自由端均垂直固定於所述第二頂壓板37上,從而保證球頭關節36在規定的平面內相對球形槽旋轉,避免球頭關節36多方向旋轉導致分體蒸發器5折彎角度的不一致性,有利於提高分體蒸發器5的折彎質量。而為了進一步的提高折彎質量,本實施例將每個所述球頭關節36的長度均設置為相同。
本實施例所述壓緊部件33包括一氣缸和一與氣缸的活塞杆連接並由氣缸驅動作上下垂直往返運動的壓緊板331,通過氣缸驅動壓緊板331緊壓分體蒸發器5,便於分體蒸發器5的緊壓和鬆弛,有利於提高操作效率。
由於頂壓氣缸34固定於操作臺31上,且在頂壓折彎時具有較大的力度,為保證頂壓氣缸34的固定性,減少頂壓氣缸34在折彎過程中發生不必要的振動或晃動,本實施例通過一固定於所述操作臺31下表面的固定支架38來固定所述頂壓氣缸34,提高頂壓氣缸34固定的穩定性。進一步的,本實施例將所述固定支架38設置為直角三角形狀,將其一直角邊固定於操作臺31下表面,將頂壓氣缸34固定於另外一直角邊上,從而提高了頂壓氣缸34相對操作臺的穩定性,減少其振動和晃動的機率。
為了避免分體蒸發器5折彎過程中造成分體蒸發器5的損傷,本實施例在第二頂壓板37相對分體蒸發器5一側的表面上設有柔性墊板39,同時在所述壓緊板331和折彎臺32的相對面上均設置有柔性墊板39,通過柔性墊板39可進行一定的緩衝作用,減少分體蒸發器5折彎過程中損壞的機率。其中,本實施例的上述柔性墊板39優選為橡膠材質。
以上所述本發明的具體實施方式,並不構成對本發明保護範圍的限定。任何根據本發明的技術構思所做出的各種其他相應的改變與變形,均應包含在本發明權利要求的保護範圍內。