混合料製備工藝的製作方法
2023-05-15 03:59:22
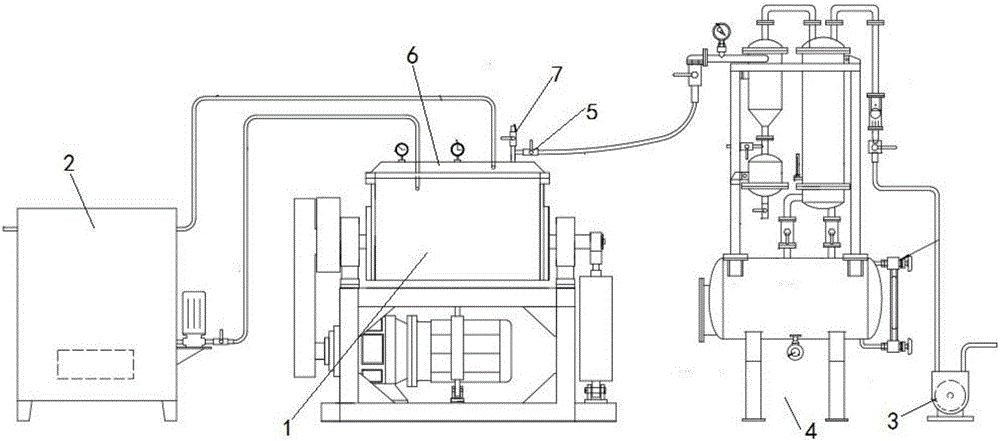
本發明涉及粉末冶金技術領域,具體地,涉及一種用於粉末冶金的混合料製備工藝。
背景技術:
粉末冶金是製取金屬或用金屬粉末(或金屬粉末與非金屬粉末的混合物)作為原料,經過成形和燒結,製造金屬材料、複合材料以及各種類型製品的工藝技術。粉末冶金法與生產陶瓷有相似的地方,因此,一系列粉末冶金新技術也可用於陶瓷材料的製備。由於粉末冶金技術的優點,它已成為解決新材料問題的鑰匙,在新材料的發展中起著舉足輕重的作用。目前,粉末冶金技術已被廣泛應用於交通、機械、電子、航空航天、兵器、生物、新能源、信息和核工業等領域,成為新材料科學中最具發展活力的分支之一。粉末冶金技術具備顯著節能、省材、性能優異、產品精度高且穩定性好等一系列優點,非常適合於大批量生產。另外,部分用傳統鑄造方法和機械加工方法無法製備的材料和複雜零件也可用粉末冶金技術製造,因而備受工業界的重視。
現代混合料的質量鑑定包括粉末性能(粒度和粒度組成、流動性等)、物理性能(鈷磁、磁力等)和金相性能(孔隙度、晶型形貌等)鑑定,只有這些鑑定指標全部符合產品技術性能,才能投入壓制生產。混合料製備時主要通過觀察制粒料的粒度及組成,測量其霍爾流速和松裝密度判斷其制粒條件是否恰當。特別是粒度要適當,太粗太硬,流動性好、壓制壓力小,但壓塊密度、強度低,表面現粒,易產生未壓好;太細太溼,粉末多,流動性差,製品單重、尺寸波動大,壓制壓力大,壓塊密度、強度大,易分層。所以料粒軟硬粗細直接影響接下來的使用性能。
傳統硬質合金混合料的製備,是將碳化鎢、鈷粉、CK料及其他元素按每個牌號以固定重量,在溼磨機中充分混合後,乾燥過篩製得不含成型劑的混合料,然後在混合料中摻入成型劑(橡膠等)經攪拌均勻後,再乾燥,最後擦篩、過篩、制粒。這個製備混合料的方法在乾燥時都是持續真空(真空度在-0.07以上),持續高溫(溫度80℃~120℃),能耗非常大。而且這種生產混合料的方法過程難控制,生產的混合料質量較差。有個別廠家嘗試加入PEG作為成型劑用於混合料的生產,但經乾燥制粒後難制粒且料粒過硬,從而影響後續產品的壓制性能,燒結性能,最終影響產品的使用性能,因無法解決技術問題而不得不放棄。也有選擇石蠟作為成型劑,雖然生產的混合料成形性好,但是石蠟難過篩,清洗困難,從而也只有少數廠家使用。
對於大批量混合料的生產,噴霧乾燥是一種高質量又經濟的混合料乾燥制粒方法。然而,對於中小企業小批量的、多牌號、常變動的生產,採用噴霧乾燥既沒有必要也不經濟。
鑑於此,有必要提供一種高效、經濟和可控的混合料製備工藝,以克服或緩解上述缺陷。
技術實現要素:
本發明的目的是提供一種高效、經濟和可控的混合料製備工藝。
為實現上述目的,本發明提供一種混合料製備工藝,其包括以下步驟:
步驟a、將配料後的成型劑和WC原料的進行球磨,其中,成型劑佔總料重的1.5~2.5%;
步驟b、啟動並預熱真空乾燥攪拌器的水加熱裝置,加熱水溫至75~95℃;
步驟c、將球磨好的混合料卸料過篩後裝入真空乾燥攪拌器內,並蓋好所述真空乾燥攪拌器的蓋板夾固後,開啟水環真空泵並調節所述真空乾燥攪拌器上的真空度為-0.06~-0.08,啟動所述真空乾燥攪拌器對混合料進行攪拌;
步驟d、所述真空乾燥攪拌器以20~40r/min的頻率攪拌,直至混合料的料粒呈半乾不幹狀,並將溫度平穩維持在45~80℃;
步驟e、0.5~1小時後,將真空乾燥攪拌器的真空度降至0~-0.05;
步驟f、 2~3小時之後停止乾燥,擦篩制粒並過60目篩,再將分級料放在乾燥櫃內返幹,最後包裝入庫。
在步驟e後,若混合料呈現鬆散泥巴狀,則進行攪拌,攪拌速度為 5~15分鐘/每 2~3圈;該過程中乾燥溫度為30~55℃,2~3小時之後停止乾燥。
在步驟a中,所述成型劑設為PEG,所述球磨設為溼磨,且溼磨過程中加入酒精。
在步驟c中,卸料時,對混合料進行攪動防止混合料發生沉澱;啟動水環真空泵後,開啟酒精回收裝置上的各開關氣閥和酒精回收裝置的冷卻水閥,開啟蓋板上的回收控制閥,並通過酒精回收裝置上的洩壓閥調節所述真空乾燥攪拌器上的真空度為-0.06~-0.08,啟動所述真空乾燥攪拌器對混合料進行攪拌。
在步驟f中,擦篩制粒的具體步驟包括:
f1、啟動擦篩機的刮刀,使其旋轉和振動;
f2、將由所述真空乾燥攪拌器乾燥完畢後的混合料以1~3Kg/每次的方式加入擦篩機的篩框內;
f3、開啟圓筒制粒機的開水加熱裝置,將水溫設定為45~50℃;
f4、將經擦篩機擦篩後的粉料鏟入圓筒制粒機中,加入量為25Kg左右;
f5、啟動所述圓筒制粒機的制粒筒,所述制粒機旋轉,調整傾斜裝置使粉料在制粒筒中邊旋轉邊翻滾,直至粉料的運動狀態呈瀑布狀態;
f6、取樣檢測料粒的流動性、松裝比及料粉比例,若不合格,重複步驟f5,調節料粒至合格要求;
f7、 採用60目篩網將制粒好的料粒分級過篩,料粒過篩一次或兩次。
在步驟f中,返幹包裝的具體步驟包括:
g1、將乾燥櫃的水溫設置為90℃;
g2、將混合料按10Kg每份分裝在乾燥盤中,放入乾燥櫃中關好門;
g3、乾燥過程中將乾燥盤中的料粒翻動2~3次;
g4、乾燥2小時後,對料粒進行包裝,且包裝後入庫。
在步驟b中,所述真空乾燥攪拌器的水加熱裝置的預設時間為30分鐘,水溫設為80~90℃。
在步驟d中,所述真空乾燥攪拌器的攪拌頻率設為26r/min,且所述真空乾燥攪拌器的溫度設為50~70℃。
在步驟e中,調節所述真空乾燥攪拌器的真空度至-0.02~-0.05。
制粒筒的開口向上傾斜,傾斜度設為45°。
本發明相對於現有技術,具有如下優點之處:
1、在本發明中,在所述真空乾燥攪拌器的真空度為-0.06~-0.08的狀態下進行快速連續攪拌,以加快乾燥速度以防止混合料氧化和/或混合料過硬;攪拌至所述真空乾燥攪拌器內溫度有一個明顯的上升過程,混合料呈半乾不幹的狀態時,停止連續攪拌後,將所述真空乾燥攪拌器的真空度降低至0~-0.05,避免將混合料打碎以方便後續制粒料粒;如此生產出料的混合料料粒物流軟而易碎、壓制性能好,燒結出來的產品孔隙可以達到A02以下,且WC生長完全、金相組織均勻;
2、在本發明中,當混合料漿呈現鬆散泥巴狀,則進行間接性攪拌且速度為 5~15分鐘/每2~3圈,以防止混合料結塊,而期間溫度由原來的45~80℃降到該步驟中的30~55℃,以防止混合料氧化和/或混合料過硬。
本發明的其它特徵和優點將在隨後的具體實施方式部分予以詳細說明。
附圖說明
為了更清楚地說明本發明實施例或現有技術中的技術方案,下面將對實施例中所需要使用的附圖作簡單地介紹,顯而易見地,下面描述中的附圖僅僅是本發明的一些實施例,對於本領域普通技術人員來講,在不付出創造性勞動的前提下,還可以根據這些附圖獲得其他的附圖。
圖1是根據本發明的混合料製備工藝的部分裝置示意圖;
圖2是採用現有技術的混合料製備工藝所制的的式樣條;
圖3是採用本發明所述的混合料製備工藝所制的的式樣條。
附圖標記說明
1-真空乾燥攪拌器;2-水加熱裝置;3-水環真空泵;4-酒精回收裝置;5-回收控制閥;6-蓋板;7-洩壓閥。
具體實施方式
下面將結合本發明實施例中的附圖,對本發明實施例中的技術方案進行清楚、完整地描述,顯然,所描述的實施例僅僅是本發明一部分實施例,而不是全部的實施例。基於本發明中的實施例,本領域普通技術人員所獲得的所有其他實施例,都屬於本發明保護的範圍。
本發明提供一種混合料製備工藝,其包括以下步驟:
步驟a、將成型劑和WC、鈷粉原料進行球磨,其中,成型劑佔總混合料重的1.5~2.5%;
步驟b、啟動並預熱真空乾燥攪拌器1的水加熱裝置2,加熱水溫至75~95℃;
步驟c、將球磨好的混合料卸料過篩後裝入真空乾燥攪拌器1內,並蓋好所述真空乾燥攪拌器1的蓋板6夾固後,開啟水環真空泵3並調節所述真空乾燥攪拌器1上的真空度為-0.06~-0.08,啟動所述真空乾燥攪拌器1對混合料進行攪拌;
步驟d、所述真空乾燥攪拌器1以20~40r/min的頻率攪拌,直至混合料的料粒呈半乾不幹狀,並將溫度平穩維持在45~80℃;
步驟e、0.5~1小時後,將真空乾燥攪拌器1的真空度降至0~-0.05;
步驟f、 2~3小時之後停止乾燥,擦篩制粒並過60目篩,再將分級料放在乾燥櫃內返幹,最後包裝入庫。
在步驟e後,若混合料呈現鬆散泥巴狀,則進行間接性攪拌,攪拌速度為 5~15分鐘/每 2~3圈;該過程中乾燥溫度為30~55℃,2~3小時之後停止乾燥。
在本發明中,在所述真空乾燥攪拌器1的真空度為-0.06~-0.08的狀態下進行快速連續攪拌,以加快乾燥速度以防止混合料氧化和/或混合料過硬;攪拌至所述真空乾燥攪拌器1內溫度有一個明顯的上升過程,混合料呈半乾不幹的狀態時,停止連續攪拌後,將所述真空乾燥攪拌器1的真空度降低至0~-0.05,避免將混合料打碎以方便後續制粒料粒;如此生產出料的混合料料粒物流軟而易碎、壓制性能好,燒結出來的產品孔隙可以達到A02以下,且WC生長完全、金相組織均勻。在本實施例中,優選所述真空乾燥攪拌器1為Z型混合乾燥器。
在步驟a中,所述成型劑設為PEG,所述球磨設為溼磨,且溼磨過程中加入酒精;PEG成型劑和WC原料一起溼磨且後續一起直接卸料乾燥,減少了工藝流程;同時,酒精的加入可以提高溼磨效率,且溼磨的產品細度均勻。
如圖1所示,在步驟c中,卸料時,對混合料進行攪動防止混合料發生沉澱;啟動水環真空泵3後,開啟酒精回收裝置4上的各開關氣閥和酒精回收裝置4的冷卻水閥,開啟蓋板6上的回收控制閥5;通過酒精回收裝置4上的洩壓閥7調節所述真空乾燥攪拌器1上的真空度為-0.06~-0.08,啟動所述真空乾燥攪拌器1對混合料進行攪拌;在本實施例中,優選所述真空乾燥攪拌器1的真空度為-0.06;在乾燥過程中,通過所述酒精回收裝置4對混合料中含有的酒精進行回收。
在步驟f中,擦篩制粒的具體步驟包括:
f1、啟動擦篩機的刮刀,使其旋轉和振動;
f2、將由所述真空乾燥攪拌器1乾燥完畢後的混合料以1~3Kg/每次的方式加入擦篩機的篩框內;
f3、開啟圓筒制粒機的開水加熱裝置2,將水溫設定為45~50℃;
f4、將經擦篩機擦篩後的粉料鏟入圓筒制粒機中,加入量為25Kg左右;
f5、啟動所述圓筒制粒機的制粒筒,所述制粒機旋轉,調整傾斜裝置使粉料在制粒筒中邊旋轉邊翻滾,直至粉料的運動狀態呈瀑布狀態;
f6、取樣檢測料粒的流動性、松裝比及料粉比例,若不合格,重複步驟f5,調節料粒至合格要求;
f7、採用60目篩網將制粒好的料粒分級過篩,料粒過篩一次或兩次。
在步驟f中,返幹包裝的具體步驟包括:
g1、將乾燥櫃的水溫設置為90℃;
g2、將混合料按10Kg每份分裝在乾燥盤中,放入乾燥櫃中關好門;
g3、乾燥過程中將乾燥盤中的料粒翻動2~3次;
g4、乾燥2小時後,對料粒進行包裝,且包裝後入庫。
在步驟b中,所述真空乾燥攪拌器1的水加熱裝置2的預設時間為30分鐘,水溫設為80~90℃。
在步驟d中,所述真空乾燥攪拌器1的攪拌頻率設為26r/min,且所述真空乾燥攪拌器1的溫度設為50~70℃。
在步驟e中,調節所述真空乾燥攪拌器1的真空度至-0.02~-0.05。
制粒筒的開口向上傾斜,傾斜度設為45°。
如圖1所示的裝置,本發明的具體實施方式如下:
步驟a 、將5個微米碳化鎢和鈷粉混合成混合料,其中,5個微米碳化鎢的重量佔總混合料重量的92%,鈷粉的重量佔總混合料重量的8%,總混合料重量為280Kg;以PEG成型劑佔混合料總重的1.5%~2.5%的方式將PEG成型劑和WC原料混合形成混合料,混合後加入球磨機中溼磨15~20個小時,溼磨過程中加入酒精,以提高溼磨效率且溼磨後的混合料細度均勻;具體地,可以根據實際需要,設置所述PEG成型劑佔混合料重量的1.5%或2.5%或2%,溼磨時間根據混合料的磨後狀態來設置,如對磨後狀態要求低時,可以選擇溼磨時間為15小時,如對磨後狀態要求低高時,可以選擇溼磨時間為20小時,當然還可以選擇中間值如16小時或17小時或18小時或19小時或16.8小時或18.5小時或者19.2小時等任意數值;
步驟b、提前30分鐘啟動真空乾燥攪拌器1的水加熱裝置2,將水溫設定在75~95℃之間,即可以將預熱水溫設為75~95℃之間的任一值,如75℃或78℃80℃或85.3℃或86.7℃或89.5℃或91.8℃或92.5℃或95℃等具體值;本發明中,可以優選將水溫設定在80~90℃之間,即優選80℃或90℃度之間的任一值,如85℃、89℃等;
步驟c、
包括步驟c1、將球磨好的混合料全部卸入真空乾燥攪拌器1內;卸料時,對混合料進行攪動防止混合料發生沉澱。
步驟c2、將混合料裝入所述真空乾燥攪拌器1並蓋好蓋板6夾固後,開水環真空泵3進水閥,啟動水環真空泵3;開啟酒精回收裝置4上的各開關氣閥和酒精回收裝置4的冷卻水閥,開啟蓋板6上的回收控制閥5;通過酒精回收裝置4上的洩壓閥7調節所述真空乾燥攪拌器1上的真空度為-0.06~-0.08,啟動所述真空乾燥攪拌器1對混合料進行攪拌;
步驟d、啟動乾燥器攪拌;所述真空乾燥攪拌器1以20~40r/min的頻率攪拌,直至混合料的料粒呈半乾不幹狀,並將溫度平穩維持在45~80℃,即可以溫度維持在45℃至80℃中的任一值,如45℃或49℃或60℃或71℃或80℃等;在本發明中,優選攪拌頻率為20~40r/min,且進一步優選快速連續攪拌的攪拌頻率為26r/min;攪拌過程中,溫度有一個明顯的上升過程,當混合料呈半乾不幹的狀態時,停止連續攪拌,且優選最後溫度平穩維持在50~70℃,如51℃或66℃或55.6℃或60℃或63℃或68℃等;
步驟e、 0.5~1小時後,將真空乾燥攪拌器1的真空度降至0~-0.05,其中優選將所述真空乾燥攪拌器1的真空度設為-0.02,當然還可以設為其他值如-0.03或-0.04或-0.01等;進一步,2小時後開蓋查看混合料,若混合料呈現鬆散泥巴狀,進行間接性攪拌,攪拌速度為 5~15分鐘/每 2~3圈,該過程中乾燥溫度為30~55℃,2~3小時之後停止乾燥;
步驟f、包括擦篩制粒步驟和返幹包裝步驟,
具體地,擦篩制粒步驟包括:
f1、啟動擦篩機的刮刀,使其旋轉和振動;
f2、將由所述真空乾燥攪拌器1乾燥完畢後的混合料以1~3Kg/每次的方式加入擦篩機的篩框內,加料時,可以每次加入1kg,也可以每次加入2kg或3kg或2.5kg或1.8kg等;
f3、開啟圓筒制粒機的開水加熱裝置2,將水溫設定為45~50℃,即水溫可以設為50℃或45℃或46℃或47.2℃或48.6℃或49.5℃等45~50℃之間的任一溫度值;其中,制粒筒的開口向上傾斜,其具體地傾斜度設為45°;
f4、將經擦篩機擦篩後的粉料鏟入圓筒制粒機中,加入量為25Kg左右;
f5、啟動所述圓筒制粒機的制粒筒,所述制粒機旋轉,調整傾斜裝置使粉料在制粒筒中邊旋轉邊翻滾,直至粉料的運動狀態呈瀑布狀態;
f6、取樣檢測料粒的流動性、松裝比及料粉比例,若不合格,重複步驟f5,調節料粒至合格要求;
f7、採用60目篩網將制粒好的料粒分級過篩,料粒過篩一次或兩次;
具體地,返幹包裝步驟包括:
g1、將乾燥櫃的水溫設置為90℃;
g2、將混合料按10Kg每份分裝在乾燥盤中,放入乾燥櫃中關好門;
g3、乾燥過程中將乾燥盤中的料粒翻動2~3次;
g4、乾燥2小時後,對料粒進行包裝,且包裝後入庫,該乾燥時間2小時,從乾燥櫃溫度升至90℃時計算時間。
由上述工藝製造出來的混合料具有合理的粒度和粒度組成、料粒軟而易碎;取該混合料壓制一組試樣條,壓制過程中壓制力為1.8~2.0t,燒結後試樣條的孔隙為A02以下,如圖2所示,投入壓制生產產品性能穩定。
而採用現有技術中的混合工藝製成的混合料製成的試樣條的孔隙為A06以上,如圖3所示,如此的試樣條達不到生產要求。
顯然,上述實施方式僅僅是為清楚地說明所作的舉例,而並非對實施方式的限定。對於所屬領域的普通技術人員來說,在上述說明的基礎上還可以做出其它不同形式的變化或變動。這裡無需也無法對所有的實施方式予以窮舉。而由此所引伸出的顯而易見的變化或變動仍處於本發明創造的保護範圍之中。