一種複合材料車輛抗側滾扭杆及其製備方式的製作方法
2023-05-21 14:04:21 2
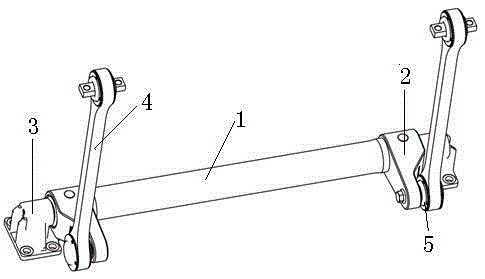
本發明涉及一種軌道交通車輛用部件,具體涉及一種安裝在軌道車輛車體和轉向架之間的軌道交通車輛用抗側滾扭杆系統,屬於機械工程技術領域。
技術背景
抗側滾扭杆系統(簡稱扭杆系統)是軌道交通車輛(包括幹線鐵路車輛,地鐵城軌車輛,有軌電車等)的關鍵部件,用於抑制在車輛轉彎,側風等情況下的車體側滾,扭杆系統由垂向連杆組件,扭轉臂,支撐座組件和扭杆軸組成。隨著車輛運行速度以及其乘坐舒適性要求的提高,對扭杆系統以及軌道交通車輛系統部件(如懸掛連杆部件,定位轉臂組件等)也提出越來越高的要求,其中輕量化是其中的一個技術發展趨勢。
通常扭杆系統的車輛根據其布置方式的不一樣,區分為內置式和外置式兩種型式,其中內置式的扭杆系統布置在轉向架橫梁的內側,扭杆軸的長度為1300-1800mm,扭杆系統的重量約120-150kg,外置式扭杆系統布置在轉向架橫梁的外側,扭杆軸的長度為1800-2500mm,扭杆系統的重量150-220kg。
扭杆系統中的部件除極少部分的金屬橡膠件,或者高分子材料外,其餘的金屬部件的重量佔到95%以上。在目前的技術方案的前提下,只能通過扭杆軸空心化,優化支撐座和扭轉臂結構等方式減輕扭杆系統的重量,但存在較大的局限,可減少的重量範圍小於10%。軌道交通車輛的內飾,車體等部件紛紛採用輕金屬合金(鋁合金,鎂合金等),高分子複合材料等手段來不斷降低車輛的重量,因此,如何通過選用其他非金屬部件來製造扭杆系統,並形成批量的生產製造工藝和質量控制手段是系統部件產品開發過程中亟待解決的問題。
目前採用以金屬部件為主的扭杆系統主要存在如下缺陷:
1.製造成本高,由於金屬部件的原材料和成型工藝的限制,製造成本相對較高,以扭杆軸為例,採用用量少,強度高,高淬透性的52CrMoV4 acc EN 10089的彈簧鋼材料的原材料成本較高,其次扭杆軸的成型工藝包括端部鐓粗,機械加工,熱處理,表面噴丸等各種工序,還包括超聲波探傷,磁粉探傷等無損檢測手段,工藝複雜導致成本較高;
2.質量控制難,由於其複雜的成型工藝,扭杆系統的各部件在質量控制方面要求的項點也相對較多,常用的包括金屬原材料的化學成分,熱處理後的機械性能,體現其淬透性的外部和芯部的硬度檢測,以及超聲波無損檢測(金屬原材料內部質量)和磁粉探傷(產品的表面缺陷情況)等,任何質量控制將導致成本,控制失效將導致產品的潛在失效風險的;
3.重量高,軌道交通車輛的輕量化是其發展的趨勢,目前出系統部件外,其餘產品均進行採用輕金屬或者複合材料進行材料替代的輕量化應用,而系統部件通常在重量方面佔有較大的重量比重,如能進行輕量化的應用,經存在極大的優化空間。車輛的輕量化將從運行的能耗,乘坐的舒適性等各個方面來優化整車的性能。
技術實現要素:
為解決以上技術問題,本發明提供一種複合材料車輛抗側滾扭杆及其製造方式,具體技術方案如下:
一種複合材料車輛抗側滾扭杆,包括扭杆軸、扭轉臂、支撐座和垂向連杆,扭轉臂安裝在扭杆軸上,扭杆軸連接安裝座,垂向連杆通過關節軸與扭轉臂連接,其特徵在於:扭杆軸、垂向連杆和支撐座採用纖維類環氧樹脂複合材料。
進一步,所述扭杆軸通過支撐軸連接安裝座,所述扭轉臂、扭杆軸和支撐軸採用粘結劑連接,並通過錐銷將扭杆軸、扭轉臂和支撐軸三個部件連接在一起。扭轉臂和支撐軸採用粘結劑為環氧樹脂粘結劑。
進一步,纖維類環氧樹脂複合材料,為碳纖維增強環氧樹脂、玻璃纖維環氧樹脂基複合材料的一種或兩種。
一種複合材料車輛抗側滾扭杆製造方式,扭杆軸和垂向連杆,採用金屬芯模或可融芯模,在纏繞機上通過機械張力器,將浸潤了環氧樹脂液體的長纖維逐層纏繞在金屬芯模或可融芯模上,進行固化後脫模或融模;所述支撐座採用模壓纖維環氧樹脂,根據產品的結構尺寸和安裝接口的需要,設計專用的模壓模具進行支撐座的模壓製造。
進一步,扭杆軸和垂向連杆,固化後脫模或融模,通過機械加工或打磨的方式改善纏繞表面質量。
進一步,通過纏繞成型的方式製造空心的扭杆軸,扭杆軸的內外直徑根據扭杆系統的整體強度、剛度的要求進行結構設計,其中,內徑為30-50mm,外徑為80-120mm,長度為1200-2500mm的範圍。
採用可融芯模或金屬芯模進行纏繞,針對不同長度的扭杆軸進行選擇,當扭杆系統為外置式,扭杆軸的長度稍短時,採用金屬芯模(容易脫模)進行纏繞;當扭杆系統為內置式,扭杆軸的長度稍長時,採用可融芯模(無需脫模)進行纏繞。
本發明採用纖維環氧樹脂複合材料代替原有金屬部件的輕量化抗側滾扭杆系統,整體重量減輕40%,工藝簡單,質量易於控制,實現了抗側滾扭杆系統的輕量化。使用本發明的纖維環氧樹脂複合材料替代後,其質量控制的項點可大大降低,主要控制項點主要在於纏繞材料和粘結劑的原材料控制,纏繞的內部質量和粘結的強度的控制3個項點,相對原有金屬部件的化學成分,機械強度,熱處理,表面缺陷,內部缺陷,產品油漆質量等大大降低。
金屬和複合材料的關節處粘結連接,為了保證其強度、可靠性和穩定性,本發明將採用如下措施進行粘結強度的加強: A.對粘結部位進行如螺紋、凹凸槽、型面等各種方式,增加粘結面的面積和支擋的局部結構來增強強度;B.通過在粘結結構的複合材料和金屬部件之間增加連接的錐銷或其他結構形式來增強粘結。
本發明使用複合材料對金屬部件的替代,將大大降低扭杆系統的整體重量,以目前在生產的模型外置式的扭杆系統為例,使用常規金屬部件的重量達到了110kg,進行複合材料替代後,整體重量僅60kg,重量減輕45%。
附圖說明
圖1本發明實施例1一種複合材料的車輛抗側滾扭杆示意圖
圖2本發明實施例1一種複合材料的車輛抗側滾扭杆支撐座示意圖
圖3本發明實施例1 一種複合材料的車輛抗側滾扭杆中扭杆軸和扭轉臂的組裝結構示意圖
圖4本發明實施例1 一種複合材料的車輛抗側滾扭杆中扭杆軸和扭轉臂的組裝結構剖切圖
圖5本發明實施例1一種複合材料的車輛抗側滾扭杆芯模纏繞示意圖
圖中標記,1、扭杆軸 2、扭轉臂 3、支撐座 4、垂向連杆 5、關節軸
6、錐銷 7、支撐軸 8、金屬芯模或可融芯模 9、纏繞機。
具體實施方式
現有技術對比例:
根據目前現有技術的扭杆系統相關國內外標準,扭杆系統部件主要以金屬材料為主,以EN 15049和TB/T 3485《動車組抗側滾扭杆》,相關的材料要求如下表1:
表1 抗側滾扭杆系統的材料選用
本發明實施例
一種複合材料車輛抗側滾扭杆,包括扭杆軸1、扭轉臂2、支撐座3和垂向連杆4,扭轉臂2安裝在扭杆軸1上,所述扭杆軸1通過支撐軸7連接安裝座3,垂向連杆4通過關節軸5與扭轉臂2連接,扭杆軸1、垂向連杆4和支撐座3採用碳纖維增強環氧樹脂,扭轉臂2、扭杆軸1和支撐軸7採用環氧樹脂粘結劑連接,並通過錐銷6將扭杆軸1、扭轉臂2和支撐軸7三個部件連接在一起,起到固定粘結,增加強度的作用。
一種複合材料的車輛抗側滾扭杆製造方式,扭杆軸和垂向連杆,採用可融芯模8,在纏繞機9上通過機械張力器,將浸潤了環氧樹脂液體的長碳纖維逐層纏繞在模具上,進行固化後融模,再通過機械加工或打磨的方式改善纏繞表面質量。通過纏繞成型的方式製造空心的扭杆軸,扭杆軸的內外直徑根據扭杆系統的整體強度、剛度的要求進行結構設計,其中內徑為30mm,外徑為80mm,長度為1200mm。
支撐座採用模壓的纖維增強環氧樹脂,根據產品的結構尺寸和安裝接口的需要,設計專用的模壓模具進行產品製造。
本發明主要使用碳纖維增強環氧樹脂高分子複合材料替代扭杆軸,垂向連杆杆體,支撐座,其中扭杆軸和垂向連杆杆體採用纏繞的工藝,支撐座採用模壓的工藝。
相關材料替代如表2所示:
表2 輕量化扭杆系統的材料替代和成型工藝
通過上述使用複合材料對金屬部件的替代,將大大降低扭杆系統的整體重量,以目前在生產的模型外置式的扭杆系統為例,使用常規金屬部件的重量達到了110kg,進行複合材料替代後,整體重量僅60kg,重量減輕45%。