退火設備及其退火工藝的製作方法
2023-08-05 00:12:56 1
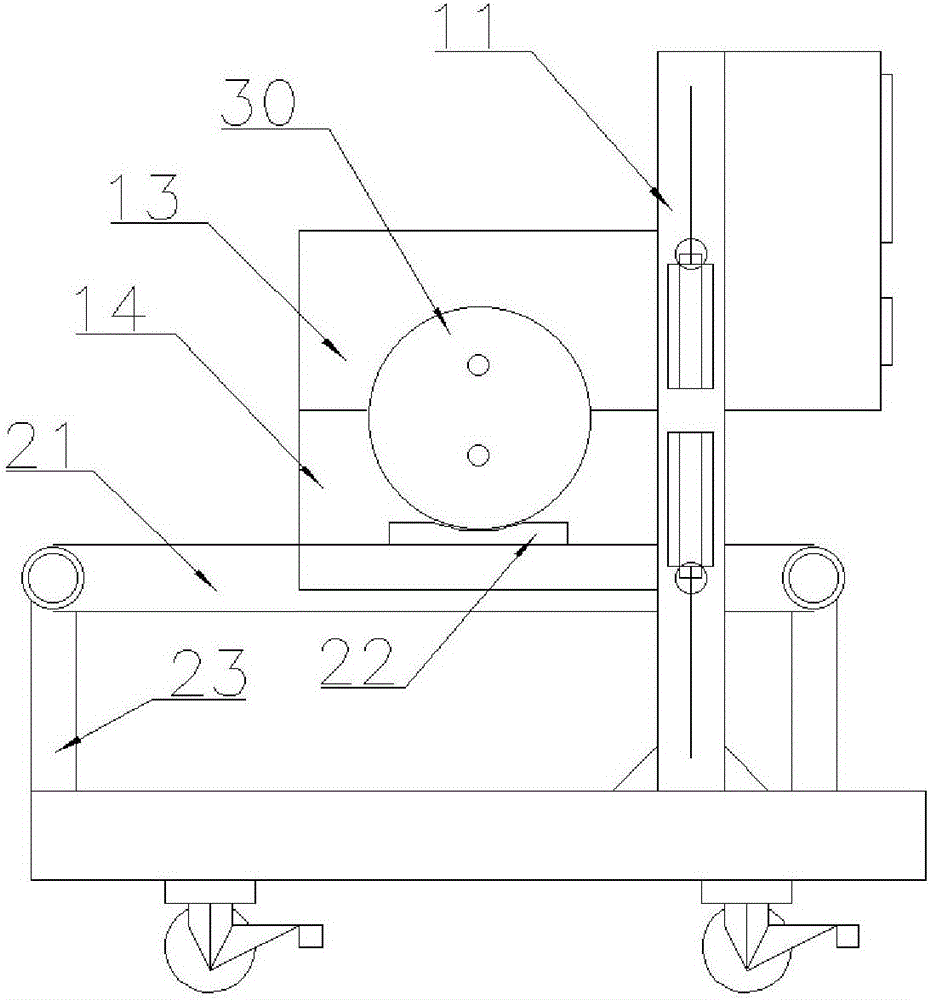
本發明涉及一種退火設備及其退火工藝,更具體而言,涉及一種降溫均勻、節省時間和能耗且可連續生產的便捷式退火設備及其退火工藝。
背景技術:
參與半導體或太陽能相關生產過程中均涉及單晶襯底,單晶棒質量的好壞直接關係到最終產品的質量。單晶棒的生長因熱場變化、溫度梯度和固液界面形狀等原因,內部會產生殘餘應力,導致晶格產生很大的畸變,故需要對單晶棒進行後期熱處理來消除或減少應力。退火是一種熱處理工藝,可有效地降低晶體中的殘留熱應力。
根據晶體低缺陷的需求,單晶棒在退火過程中,爐內保護氣體的分布均勻性、升溫和降溫過程中溫度均勻性及退火時間上的要求嚴苛,需要專門設計退火爐以滿足需求,獲得高質量的單晶材料。
現有技術中的退火設備採用通入保護氣體進行退火,結構多為管式加熱,存在裝卸麻煩;降溫不均,一半處於空氣中,一半與保溫層接觸;退火後進行下一個產品退火時,操作麻煩,耗費時間和能耗等缺點。
技術實現要素:
針對現有技術的上述缺陷,本發明的目的在於提供一種操作方便,降溫均勻、節省時間和能耗可快速連續生產的退火設備及其退火工藝。
本發明的上述目的通過以下技術方案來實現:
本發明提供的退火設備包括:加熱保護元件、保溫腔體和升降移動機構,其中:
所述加熱保護元件一端連接真空系統,另一端連接壓力系統;
所述保溫腔體包括上保溫腔體和下保溫腔體,上保溫腔體和下保溫腔體內部開有凹槽,用於套緊所述加熱保護元件;
所述升降移動機構包括豎直升降杆、水平移動帶和底座,其中:
豎直升降杆的底部垂直固定在底座上,豎直升降杆連接上保溫腔體和下保溫腔體,其設置在上保溫腔體和下保溫腔體的一側,上保溫腔體和下保溫腔體可以沿豎直升降杆上下移動,控制保溫腔體的開合;
水平移動帶為兩條,分別設置在保溫腔體的前端和後端,所述水平移動帶的兩端通過支撐座固定在底座上,水平移動帶上配有基座,用於固定加熱保護元件,水平移動帶帶動基座左右移動,從而將加熱保護元件移出和裝入所述保溫腔體。
本發明的退火工藝的步驟如下:
裝入產品的加熱保護元件的兩端分別通過抽空密封法蘭連接真空系統,通過進氣密封法蘭連接壓力系統,
將加熱保護元件放置在水平移動帶的基座上,水平移動帶在電機控制下帶動基座向上保溫腔體和下保溫腔體的凹槽間移動;
上保溫腔體和下保溫腔體在氣缸的控制下沿豎直升降杆上下移動閉合,將加熱保護元件夾套在凹槽中,真空系統和壓力系統進行抽空程序和充氣程序,控溫系統進行控溫程序,開啟加熱退火程序;
加熱退火程序結束,上保溫腔體和下保溫腔體在氣缸的控制下沿豎直升降杆上下移動打開,加熱保護元件在水平移動帶的帶動下移動到遠離上保溫腔體和下保溫腔體的一邊進行降溫;
進行降溫的加熱保護元件通過吊裝從基座上移走的同時,迅速裝入下一個裝有產品的加熱保護元件進行退火,實現連續生產。
相對於現有技術的管式退火設備及退火工藝,本發明退火設備及其退火工藝具有如下技術效果:
1)本發明退火設備的上保溫腔體和下保溫腔體沿升降移動杆上下移動控制保溫腔體的開合,方便加熱保護元件的裝入和移出,且移出冷卻時,加熱保護元件全部暴露在常溫狀態下進行降溫,降溫均勻。
2)本發明退火設備的水平移動帶帶動加熱保護元件左右移動,操作方便。
3)本發明退火設備的退火工藝過程中對加熱保護元件進行降溫後,經過吊裝移走的同時,迅速裝入下一個裝有加熱保護元件進行退火,可實現快速連續生產,節省升溫時間和能耗。
4)本發明退火設備的退火工藝過程中抽空密封法蘭和進氣密封法蘭將加熱保護元件進行密封,保證了加熱保護元件內的潔淨度,真空度和氣氛環境要求。
附圖說明
圖1是本發明退火設備的結構示意圖。
圖2是本發明退火設備升溫狀態下左視圖。
圖3是本發明退火設備降溫狀態下左視圖。
圖4是本發明退火設備保溫腔體(上保溫腔體和下保溫腔體)的內部結構示意圖。
圖5是本發明退火流程圖。
圖6是本發明退火設備進行加熱時升溫曲線圖。
具體實施方式
下面將結合附圖更詳細地描述本發明的退火設備及其退火方法。
如圖1-4所示,本發明提供的退火設備包括加熱保護元件、保溫腔體和升降移動機構,其中:
加熱保護元件優選高純石英管30,高純石英管30的一端通過抽空密封法蘭33連接真空系統,另一端通過進氣密封法蘭34連接壓力系統;
保溫腔體包括形狀為長方體的上保溫腔體13和下保溫腔體14,上保溫腔體13和下保溫腔體14內部開有圓柱形凹槽,用於套緊所述高純石英管30;
升降移動機構包括豎直升降杆11、水平移動帶21和底座20,其中:
豎直升降杆11的底部垂直固定在底座20上,底座20底部安裝四個滑輪24,便於退火設備的整體移動。豎直升降杆11為兩根且平行設置在上保溫腔體13和下保溫腔體14的一側,並且連接上保溫腔體13和下保溫腔體14。豎直升降杆11上安裝氣缸12來控制上保溫腔體13和下保溫腔體14沿豎直升降杆11上下移動,控制保溫腔體的開合;
水平移動帶21為兩條,分別設置在保溫腔體的前端和後端,水平移動帶21的兩端通過支撐座23固定在底座20上。水平移動帶21上配有基座22,用於固定高純石英管30。水平移動帶21兩端設置電機25來控制水平移動帶21帶動基座22左右移動,從而將高純石英管30移出和裝入保溫腔體。
在本發明的退火設備中,上保溫腔體13和下保溫腔體14的結構由內到外分別是:氧化鋁保溫層16,冷卻水層17和雙層莫來石外壁層18,其中,所述氧化鋁保溫層16內鑲嵌八根滷素加熱管15,滷素加熱管15均勻分布在上保溫腔體13和下保溫腔體14內。上保溫腔體13和下保溫腔體14的兩端裝有耐高溫陶瓷襯塊19。保溫腔體結構的設計使得本發明的退火設備具有溫場均衡,表面溫度低,升溫速率快,節能等優點。
在本發明的退火設備中,加熱保護元件優選高純石英管,具有耐高溫、耐腐蝕、熱穩定性好、透光性能好等優點。由於高純石英管的透光性,在降溫狀態下,可以無需破壞試樣所處環境直接觀測試樣的試驗情況,優越於以往的退火爐想觀測時,必須將試樣取出的方式。
如圖5、6所示運用本發明的退火設備進行退火工藝步驟如下:
裝入單晶棒的高純石英管30的一端通過抽空密封法蘭33連接真空系統,另一端通過進氣密封法蘭34連接壓力系統,其中:
抽空密封法蘭33和進氣密封法蘭34優選不鏽鋼密封法蘭,耐高溫、耐腐蝕。
真空系統,由真空泵41、抽空閥42、真空傳感器43等組成。通過真空傳感器43檢測高純石英管30內的真空度,根據工作真空度設定值比較運算,調節真空泵41和真空閥42來控制真空度。
壓力系統,壓力傳感器1、充氣閥2、調壓閥3、氣路閥4、氣路閥5、安全閥6、排氣閥7等組成。其中,氣路閥4和氣路閥5並列設置。通過壓力傳感器1採集高純石英管30內的壓力值,控制充氣閥2,以及氣路閥4和氣路閥5調整高純石英管30氣氛壓力。調壓閥3和安全閥6起保護作用,防止高純石英管30內超壓,當高純石英管30內壓力過高時可通過排氣閥4降壓。雙路氣路閥的組成可以調節複合退火氛圍,避免氣氛單一,實現高效退火。
將高純石英管30放置在水平移動帶21的基座22上,水平移動帶21在電機25控制下帶動基座22向上保溫腔體13和下保溫腔體14的凹槽間移動;
上保溫腔體13和下保溫腔體14在氣缸12的控制下沿豎直升降杆11上下移動閉合,將高純石英管60夾套在凹槽中,PLC將自動通過判斷真空和壓力條件,控制進行抽空程序和充氣程序,同時控溫系統進行控溫程序,開啟加熱退火程序,;其中:
豎直升降杆11上部設置電氣控制櫃,電氣控制櫃包括操作界面、控制按鈕8、溫控表32、觸控螢幕9等。其中,觸控螢幕9展示各種參數,如報警信息,會通過加亮突出的方式顯示在觸控螢幕9上;還可查看數據記錄採集的真空度,壓力值,以及高純石英管30內溫度數值等。本發明所述的退火設備基於PLC開發,通過儀表和傳感器進行檢測和控制,並通過觸控螢幕9顯示和操作,自動化程度高,能夠減少出錯,提高效率。
控溫系統,由溫控表32,熱電偶31,高純石英管30和繼電器等組成。熱電偶31設置在抽空密封法蘭33上且與高純石英管30平行設置,保證了本發明退火設備升溫和降溫的精確度。優選地,溫控表32選擇宇電AI-759P人工智慧溫控器,性價比高,具備50段程序控制功能,可實現任意斜率的升、降溫控制,具有跳轉(循環)、運行、暫停及停止等可編程/可操作命令,並允許在程序的控制運行中隨時修改程序。採用具備曲線擬合功能的AI人工智慧調節算法,能獲得光滑平順的曲線控制效果。在加熱退火過程中,觸控螢幕9一直記錄和顯示溫度、真空度、壓力值及自動控制調節參數,使本發明的退火設備按照設定的工藝進行退火,並通過觸控螢幕9將工藝曲線參數載入到溫控儀表,操作方便、高效且準確。加熱階段升溫曲線如圖6所示。
加熱退火程序結束,上保溫腔體13和下保溫腔體14在氣缸12的控制下沿豎直升降杆11上下移動打開保溫腔體,高純石英管30在水平移動帶21的帶動下移動到遠離上保溫腔體13和下保溫腔體14的一邊進行降溫;高純石英管30敞開化,完全暴露在常溫下,使降溫速度得到保證,實現了加溫節能,降溫迅速的目的.
按照上述退火工藝方法,進行降溫的高純石英管30通過吊裝從基座22上移走的同時,迅速裝入下一個裝有單晶棒的高純石英管30進行退火,實現連續生產,節省時間和能耗。