晶片的阻擋層及其製備方法與流程
2023-07-30 11:02:42 4
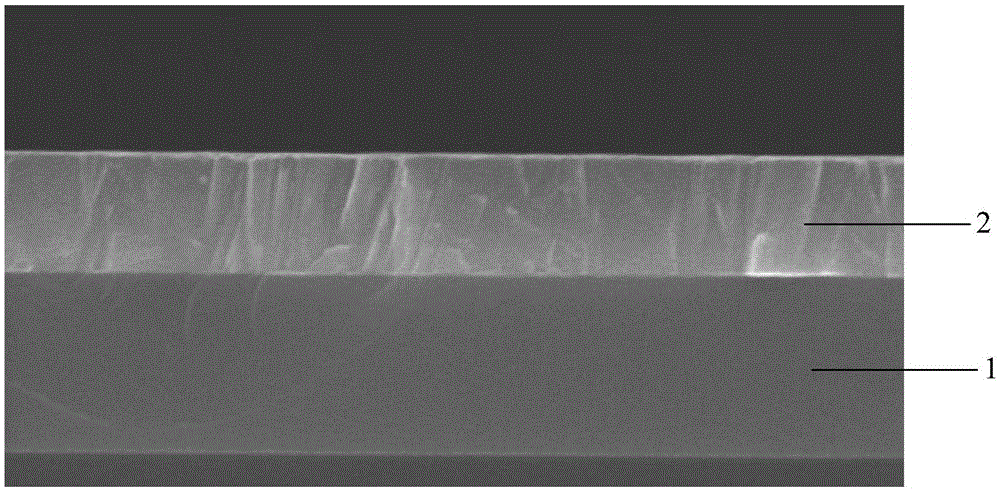
本發明涉及半導體技術領域,尤其涉及一種晶片的阻擋層及其製備方法。
背景技術:
在集成電路晶片製造技術中,應用物理或化學的方法在基片上沉積導電金屬薄膜的過程稱為金屬化,通過金屬化能夠形成互連的金屬線和對集成電路的孔填充塞。通常進行金屬化需要在基片上層疊兩種金屬膜層:阻擋層和導電層,其中阻擋層位於導電層與基片之間,阻擋層的主要作用為防止導電層與基片之間的擴散,導電層主要起導電作用。
常見的,用於形成阻擋層的金屬薄膜為TiW(鈦鎢,10%鈦和90%鎢的合金)薄膜,製備TiW薄膜的過程大致為:將基片置於濺射鍍膜機臺的腔室內的下方,腔室內的上方設置有TiW合金靶材,向腔室內通入Ar(氬)氣作為濺射氣體,Ar氣在腔室內形成Ar等離子體,Ar等離子體對TiW合金靶材產生轟擊作用,使TiW合金靶材中的原子脫離靶材表面,進而沉積到基片上形成TiW薄膜。
由於TiW合金為一種柱狀晶體,因此在形成TiW薄膜的時候,會導致結構類似「樹林」的柱狀晶體的TiW薄膜中存在縫隙,如圖1所示,從而造成阻擋層2的阻擋作用減弱。為了提高阻擋層2的阻擋作用,往往需要製備厚度D比較厚的TiW薄膜,例如厚度D在300nm以上。
但是,請再次參見圖1,圖1中TiW薄膜的厚度D為545nm,隨著TiW薄膜厚度D的增加,TiW薄膜的柱狀晶體結構也越來越明顯,阻擋作用並沒有得到本質上的改善。另一方面,當製備的TiW薄膜的厚度D較厚時,會在腔室內壁上留下較厚的TiW合金材料,由於TiW合金是一種應力比較大金屬,因此腔室內壁上留下的TiW合金材料極易開裂並剝落,從而在所製備的TiW薄膜上形成顆粒。為了避免顆粒的形成,只有增加濺射鍍膜機臺的維護次數,以及時去 除腔室內壁上留下的TiW合金材料,這不僅造成人力成本的增加,而且維護次數的增加意味著利用靶材進行暖機的次數增加,導致相當一部分靶材浪費在暖機工序上,降低了靶材的利用率,導致生產成本的增加。
技術實現要素:
為克服上述現有技術中的缺陷,本發明提出一種晶片的阻擋層及其製備方法,不僅能夠提高阻擋層的阻擋作用,而且不會增加甚至可以減少濺射鍍膜機臺的維護次數。
為達到上述目的,本發明採用如下技術方案:
本發明的第一方面提供了一種晶片的阻擋層,所述阻擋層為單層金屬薄膜結構或者多層金屬薄膜層疊的結構,且所述阻擋層中至少一層金屬薄膜具有非晶結構。
本發明所提供的阻擋層中包括具有非晶結構的金屬薄膜,這種金屬薄膜具有無定形的結構特徵,在薄膜的生長過程中,晶體的生長並不是沿著特殊的方向生長,而是無序生長,因此具有非晶結構的金屬薄膜內部不會產生像TiW薄膜的柱狀晶體結構所產生的縫隙,阻擋層中包括具有非晶結構的金屬薄膜能夠有效的減少縫隙,從而提高阻擋作用,進而也就無需通過增大阻擋層的厚度來提高阻擋作用,避免了由此引起的濺射鍍膜機臺維護次數增多的問題。
基於上述晶片的阻擋層,可選的,當所述阻擋層的結構為多層金屬薄膜層疊的結構時,所述阻擋層中至少一層金屬薄膜可具有晶體結構,具有晶體結構的金屬薄膜與具有非晶結構的金屬薄膜可交替設置。
進一步的,具有晶體結構的金屬薄膜可為TiW薄膜、Ti(鈦)薄膜、W(鎢)薄膜、Ta(鉭)薄膜、Mo(鉬)薄膜、Co(鈷)薄膜或Pt(鉑)薄膜。
進一步的,具有非晶結構的金屬薄膜可為TiWN(鈦鎢氮)薄膜。
優選的,所述阻擋層可包括一層具有非晶結構的金屬薄膜和兩層具有晶體結構的金屬薄膜,該具有非晶結構的金屬薄膜設置於兩層具有晶體結構的金屬薄膜之間。
在此基礎上,優選的,所述具有非晶結構的金屬薄膜可為TiWN薄膜,所述具有晶體結構的金屬薄膜可為TiW薄膜。
本發明的第二方面提供了一種晶片的阻擋層的製備方法,所述製備方法包括:採用濺射工藝製備TiW薄膜,製備時採用TiW合金作為靶材並加載直流功率,採用Ar氣作為濺射氣體;採用濺射工藝製備TiWN薄膜,製備時採用TiW合金作為靶材並加載直流功率,採用Ar氣和氮氣作為濺射氣體;其中,製備TiW薄膜的步驟和製備TiWN薄膜的步驟交替進行。
採用本發明所提供的晶片的阻擋層的製備方法所製備的阻擋層包括交替層疊的TiW薄膜和TiWN薄膜,其中TiWN薄膜具有非晶結構,在該薄膜生長的過程中,晶體的生長並不是沿著特殊的方向生長,而是無序生長,因此TiWN薄膜內部不會形成縫隙。由於TiWN薄膜與TiW薄膜交替設置,單層TiW薄膜的厚度不至於太厚,因此這種薄膜設置方式能夠有效地減小TiW薄膜內部所形成的縫隙的大小,並減少縫隙的數量,從而提高阻擋層的阻擋作用,並且由於所製備的單層TiW薄膜的厚度減小,因此也就不會造成濺射鍍膜機臺維護次數的增加,甚至可以減少濺射鍍膜機臺的維護次數。此外,本發明所提供的製備方法製備TiW薄膜與製備TiWN薄膜所採用的靶材均為TiW合金,所採用的濺射氣體均包括Ar氣,在製備TiWN薄膜時僅需比製備TiW薄膜時多通入一路氮氣,即可實現TiW薄膜與TiWN薄膜的原位濺射鍍膜,製備方法簡單易行。
基於上述晶片的阻擋層的製備方法,可選的,製備鈦鎢薄膜時,氬氣的流量為5sccm~200sccm,直流功率為0~60kW,所製備的鈦鎢薄膜的厚度為5nm~300nm。
在此基礎上,進一步的,製備鈦鎢薄膜時,氬氣的流量為20sccm,直流功率為5kW,所製備的鈦鎢薄膜的厚度為20nm。
可選的,製備鈦鎢氮薄膜時,氬氣的流量為5sccm~200sccm,氮氣的流量為5sccm~200sccm,直流功率為0~60kW,所製備的鈦鎢氮薄膜的厚度為5nm~300nm。
在此基礎上,進一步的,製備鈦鎢氮薄膜時,氬氣的流量為20sccm,氮氣的流量為20sccm,直流功率為5kW,所製備的鈦鎢氮薄膜厚度為10nm。
附圖說明
為了更清楚地說明本發明實施例或現有技術中的技術方案,下面將對實施例或現有技術描述中所需要使用的附圖作簡單地介紹,顯而易見地,下面描述中的附圖僅僅是本發明的一些實施例,對於本領域普通技術人員來講,在不付出創造性勞動的前提下,還可以根據這些附圖獲得其它的附圖。
圖1為現有技術中採用TiW薄膜形成的阻擋層的掃描電鏡圖;
圖2為採用本發明實施例所提供的製備方法製備的阻擋層的掃描電鏡圖;
圖3為製備阻擋層的濺射鍍膜機臺的結構圖。
附圖標記說明:
1-基片; 2-阻擋層;
D-厚度; 3-腔室;
4-磁鐵; 5-進氣口;
6-直流電源; 7-基座;
8-TiW合金靶材; 9-偏置射頻電源;
10-抽氣口。
具體實施方式
為使本發明的上述目的、特徵和優點能夠更加明顯易懂,下面將結合本發明實施例中的附圖,對本發明實施例中的技術方案進行清楚、完整地描述。顯然,所描述的實施例僅僅是本發明一部分實施例,而不是全部的實施例。基於本發明中的實施例,本領域普通技術人員在沒有作出創造性勞動的前提下所獲得的所有其它實施例,均屬於本發明保護的範圍。
實施例一
本實施例提供了一種晶片的阻擋層,該阻擋層的結構為單層金屬薄膜結構或者多層金屬薄膜層疊的結構,且該阻擋層所包括的金屬薄膜中至少一層為具有非晶結構的金屬薄膜。也就是說,阻擋層的結構可以為單層金屬薄膜結構, 此時用於形成阻擋層的金屬薄膜為具有非晶結構的金屬薄膜;阻擋層的結構也可以為多層金屬薄膜層疊的結構,此時用於形成阻擋層的多層金屬薄膜中至少有一層金屬薄膜具有非晶結構。
具有非晶結構的金屬薄膜具有結構無定形的特點,在具有非晶結構的金屬薄膜的生長過程中,晶體的生長並不是沿著特殊的方向生長,而是無序生長,因此具有非晶結構的金屬薄膜內部不會產生像TiW薄膜的柱狀晶體結構所產生的縫隙,從而具有非晶結構的金屬薄膜的阻擋導電層與基片之間擴散的作用較強。對於由單層具有非晶結構的金屬薄膜形成的阻擋層而言,相當於整個阻擋層全部具有非晶結構,因此該阻擋層的阻擋作用相比現有技術由TiW薄膜形成的阻擋層有較大的提高;對於包括至少一層具有非晶結構的金屬薄膜的阻擋層而言,阻擋層的至少一部分具有非晶結構,因此也有利於提高其阻擋作用。由於本實施例中的阻擋層的阻擋作用提高,因此也就不必通過增大阻擋層的厚度來提高阻擋作用,避免了由此引起的濺射鍍膜機臺維護次數增多的問題,有利於降低人力成本,且有利於提高靶材利用率,從而降低生產成本。
當阻擋層由單層具有非晶結構的金屬薄膜形成時,該具有非晶結構的金屬薄膜優選的可為TiWN薄膜,TiWN薄膜既能夠作為歐姆接觸材料與基片和導電層形成良好的歐姆接觸,又能夠阻擋基片與導電層之間的擴散作用。
當阻擋層的結構為多層金屬薄膜層疊的結構時,阻擋層所包括的金屬薄膜中除具有非晶結構的金屬薄膜外,其餘金屬薄膜可為具有晶體結構的金屬薄膜,即阻擋層可由具有非晶結構的金屬薄膜和具有晶體結構的金屬薄膜層疊而成,此時由於具有晶體結構的金屬薄膜內部會形成縫隙,因此為了儘量改善具有晶體結構的金屬薄膜內部形成縫隙的問題,優選的可使具有晶體結構的金屬薄膜與具有非晶結構的金屬薄膜交替設置。本實施例中,具有非晶結構的金屬薄膜優選的可為TiWN薄膜,具有晶體結構的金屬薄膜優選的可為TiW薄膜、Ti薄膜、W薄膜、Ta薄膜、Mo薄膜、Co薄膜或Pt薄膜等。
示例性地給出一種具體的阻擋層結構,該阻擋層可包括一層具有非晶結構的金屬薄膜和兩層具有晶體結構的金屬薄膜,該具有非晶結構的金屬薄膜夾設於兩層具有晶體結構的金屬薄膜之間,從而使該阻擋層形成「三明治」結構。 兩層具有晶體結構的金屬薄膜之間夾設有一層具有非晶結構的金屬薄膜,從而從一定程度上減薄了單層具有晶體結構的金屬薄膜的厚度,減少具有晶體結構的金屬薄膜中出現縫隙的數量,並減小縫隙的大小,提高了阻擋層的阻擋能力。較為優選的是,該「三明治」結構的阻擋層中,具有非晶結構的金屬薄膜可為TiWN薄膜,具有晶體結構的金屬薄膜可為TiW薄膜。
需要說明的是,通常情況下,晶片可包括:基片、阻擋層和導電層,其中阻擋層設置於基片上,導電層設置於阻擋層上。之所以在基片與導電層之間設置阻擋層,是因為導電層中通常含有金屬Al(鋁),如導電層由純Al或AlCu合金(鋁銅合金)形成,基片的材料為Si(矽),導電層中的Al與基片中的Si之間極易發生擴散作用,造成晶片的電性能下降,因此需要在導電層與基片之間設置一阻擋層,以防止導電層與基片之間的擴散。由於本實施例中晶片的阻擋層為具有阻擋能力強的優點,能夠更好地防止導電層與基片之間的擴散,因此晶片的電性能相比現有技術更優,並且能夠用較薄的阻擋層實現較強的阻擋能力,降低了單片晶片的成本。
實施例二
本實施例提供了一種晶片的阻擋層的製備方法,該製備方法包括製備TiW薄膜的步驟和製備TiWN薄膜的步驟,兩個步驟交替進行,且兩個步驟均採用濺射工藝,優選的可採用PVD(Physical Vapor Deposition,磁控濺射物理氣相沉積)工藝。製備TiW薄膜時,採用TiW合金作為靶材並加載直流功率,採用Ar氣作為濺射氣體;製備TiWN薄膜時,無需更換靶材,同樣採用TiW合金作為靶材並加載直流功率,並在通入Ar氣作為濺射氣體的同時,再通入一路氮氣,由Ar氣和氮氣所形成的等離子體轟擊TiW合金靶材,TiW原子被轟擊出來沉積在基片上的同時,氮原子也沉積在基片上,形成TiWN薄膜。
上述製備方法實現了TiW薄膜與TiWN薄膜的原位濺射鍍膜,即無需更換靶材,無需更換濺射氣體,也無需在製備好一種薄膜後製備另一種薄膜前中斷濺射鍍膜工藝,製備方法十分簡單易行。
採用上述製備方法所製備的阻擋層包括交替層疊的TiW薄膜和TiWN薄膜,其中TiWN薄膜具有非晶結構,其內部不會形成縫隙,由於TiWN薄膜與TiW 薄膜交替設置,因此單層TiW薄膜的厚度不至於太厚,有效地減小了TiW薄膜內部所形成的縫隙的大小,並減少縫隙的數量,從而提高了阻擋層的阻擋作用,並且所製備的單層TiW薄膜的厚度減小,不會造成濺射鍍膜機臺維護次數的增加,甚至可以減少濺射鍍膜機臺的維護次數,避免了由此引起的人力成本和生產成本的增加。如圖2所示,為採用上述製備方法製備的阻擋層2的掃描電鏡圖,從圖中能夠看出:與圖1中的阻擋層2相比,圖2中阻擋層內部的縫隙數量明顯減少,大小明顯減小。
需要說明的是,本實施例中對TiW薄膜與TiWN薄膜製備的先後順序並不限定,可以先在基片上製備TiW薄膜,再在TiW薄膜上製備TiWN薄膜,之後交替進行兩種薄膜的製備;也可以先在基片上製備TiWN薄膜,再在TiWN薄膜上製備TiW薄膜,之後交替進行兩種薄膜的製備。
下面結合具體的設備對本實施例所提供的晶片的阻擋層的製備方法進行示例性的說明。
如圖3所示,將基片1置於濺射鍍膜機臺的腔室3內,通過抽氣口10對腔室3進行抽真空,通過進氣口5向腔室3內通入濺射氣體:Ar氣,直流電源6向腔室3施加直流電壓,偏置射頻電源7向腔室3施加偏置射頻電壓,位於腔室3外部兩側的磁鐵4產生磁場。所通入的Ar氣在電磁場的作用下形成等離子體,高速轟擊TiW合金靶材8,TiW合金靶材8中的原子受到轟擊脫離靶材,沉積到基片1上,形成TiW薄膜。
在完成一層設定厚度的TiW薄膜的製備後,通過進氣口5向腔室3內通入濺射氣體:Ar氣和氮氣,所通入的Ar氣和氮氣在電磁場的作用下形成等離子體,其中Ar等離子體起主要的轟擊作用,將TiW合金靶材8中的原子轟擊出來,氮氣起化學反應的作用,與被轟擊出來的TiW原子結合,並沉積到TiW薄膜上,形成TiWN薄膜。
若一層TiW薄膜和一層TiWN薄膜所構成的阻擋層的厚度沒有達到所需要的厚度,則可在完成設定厚度的TiWN薄膜的製備後,交替進行TiW薄膜的製備和TiWN薄膜的製備,直至TiW薄膜和TiWN薄膜層疊而成的阻擋層的厚度達到所需要的厚度。
在上述過程中,製備TiW薄膜時,所通入的Ar氣的氣體流量可為5sccm~200sccm,優選20sccm;直流電壓的功率(即直流功率)可為0~60kw,優選5kw;所製備的TiW薄膜的厚度可為5nm~300nm,優選20nm。製備TiWN薄膜時,所通入的Ar氣的氣體流量可為5sccm~200sccm,優選20sccm;所通入的氮氣的氣體流量可為5sccm~200sccm,優選20sccm;直流電壓的功率可為0~60kw,優選5kw;所製備的TiWN薄膜的厚度可為5nm~300nm,優選10nm。
以上所述僅為本發明的具體實施方式,但本發明的保護範圍並不局限於此,任何熟悉本技術領域的技術人員在本發明揭露的技術範圍內,可輕易想到的變化或替換,都應涵蓋在本發明的保護範圍之內。因此,本發明的保護範圍應以所述權利要求的保護範圍為準。