一種針狀焦的製備方法與流程
2023-08-09 02:53:06 2
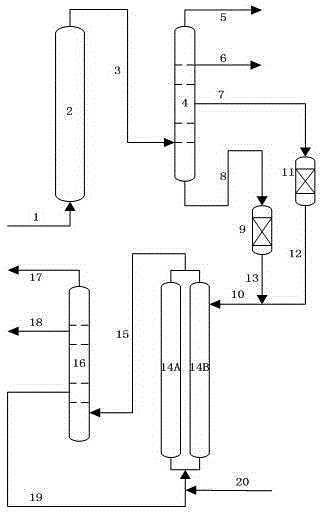
本發明涉及一種製備針狀焦的方法,特別是涉及一種催化裂化-延遲焦化組合工藝製備針狀焦的方法。
背景技術:
針狀焦具有CTE低、易石墨化等特點,是生產高功率和超高功率石墨電極的優選材料。在針狀焦的形成過程中,原料油需要經歷中間相小球體的生成、長大、融並等歷程,發育為廣域中間相,然後再在氣流的作用下形成線型紋理結構,最後固化製得針狀焦。在焦化初期,體系內部要避免出現過大的擾動,以保證中間相小球體緩慢、平穩地發育,中間相的發育程度直接影響著針狀焦的產品性能;在「拉焦」階段,體系內需要不斷有氣流勻速逸出,將廣域中間相拉成線型結構。
CN103045301公開了一種以催化裂化油漿為原料製備針狀焦的方法,當延遲焦化裝置處理量達到其處理總量的60%~80%時,將生成油分離出汽油後其餘餾分全部進入延遲焦化裝置作為拉焦氣體,製得的針狀焦具有高纖維結構。
CN103184057公開了一種製備均質石油針狀焦的方法。該方法在反應初期,原料以較低溫度進入焦化塔形成中間相液晶,隨著加熱爐溫度的提高,原料依次混合重餾分油和中間餾分油一起進入焦化塔,最終使得焦化塔內溫度達到510℃。
技術實現要素:
現有技術在針狀焦製備過程中,需要為廣域中間相的形成提供一個緩和、平穩的環境,避免反應體系出現過大的擾動。相反,在焦化反應中後期,又需要體系內部不斷有氣流勻速逸出,將廣域中間相拉成線型紋理結構。此外,針狀焦的製備通常採用程序升溫控制,起始溫度較低,隨著反應溫度的升高,原料油反應逐漸加劇,在高溫反應階段,原料油中的重組分容易縮聚,快速生成焦炭,不利於針狀焦的生成。針對現有技術的不足,本發明提供一種焦化塔及製備針狀焦的方法。該方法中焦化塔通過採用原料上進料方式,有效地消除了進料對廣域中間相形成帶來的擾動;在反應中後期,從下進料口向延遲焦化塔內通入循環油和不易結焦物質,作為體系的「拉焦」氣和供熱劑。
本發明提供一種針狀焦的製備方法,所述方法包括以下內容:
(1)催化裂化原料油進入催化裂化裝置發生反應,生成的油氣從塔頂排出進入催化裂化分餾系統,分離後得到氣體、輕油、中間餾分油和催化油漿;
(2)步驟(1)生成的中間餾分油和催化油漿經過原料油加熱爐加熱至430℃~510℃後通過焦化塔的上進料口進入焦化塔,反應生成的油氣從塔頂排出進入焦化分餾系統,分離後得到氣體、輕油和循環油,所述的原料油加熱爐採用一段恆溫-二段升溫-三段恆溫的程序升溫操作方式,其中,一段恆溫為430~490℃恆溫10~25h,二段升溫以1~5℃/h的速率升至490℃~510℃;三段恆溫為490~510℃恆溫1~5h;
(3)當原料油加熱爐結束一段恆溫開始二段升溫時,上進料口停止催化油漿進料,只進步驟(1)生成的中間餾分油,同時,步驟(2)生成的循環油從焦化塔的下進料口進入焦化塔;
(4)當原料油加熱爐出口溫度大於490℃時,開始從延遲焦化塔的下進料口向延遲焦化塔內通入不易結焦物質,直至反應周期結束,生成的針狀焦沉積在焦化段底部。
本發明方法中,所述的原料油加熱爐採用一段恆溫-二段升溫-三段恆溫的程序升溫操作方式,其中,一段恆溫為430~490℃恆溫10~25h,二段升溫以1~5℃/h的速率升至490~510℃;三段恆溫為490~510℃恆溫1~5h;當原料油加熱爐處於一段恆溫時,中間餾分油和催化油漿通過焦化塔的上進料口進入焦化塔;當原料油加熱爐結束一段恆溫開始二段升溫時,上進料口停止通入催化油漿,只通入中間餾分油,同時循環油通過下進料口進入焦化塔;當原料油加熱爐出口溫度大於490℃時,上進料口繼續通入中間餾分油,下進料口繼續通入循環油,不易結焦物質也通過下進料口進入焦化塔,直至充焦周期結束。
本發明方法中,所述焦化塔包括筒體、上封頭和下封頭,所述筒體由上至下依次設置焦化段和填料段,焦化段和填料段之間設有擋板,所述擋板為帶有篩孔的擋板,焦化段、擋板和填料段通過法蘭固定連接,所述焦化段的筒體上設置上進料口,所述下封頭設置下進料口,下進料口與填料段連通。
所述焦化塔中,所述填料段高度為焦化塔總高度的1/20~1/2,優選為1/20~1/5。
所述焦化塔中,所述上進料口位於焦化塔的焦化段的中上部,距離焦化塔的塔底高度為總塔高的3/5~4/5。
所述焦化塔中,所述擋板為帶有篩孔的擋板,所述擋板篩孔的形狀為正方形,長方形,三角形,圓形中的一種,優選為圓形;篩孔大小為0.1mm~10mm,優選1mm~5mm,篩孔沿擋板徑向呈同心圓分布,擋板的總開孔率為5%~50%,可以是均勻開孔率,也可以是非均勻開孔率,優選非均勻開孔率,當為非均勻開孔率時,從圓心沿著擋板半徑方向篩孔孔徑逐漸增大或者篩孔數量逐漸增多。
所述焦化塔中,所述填料段內填充耐溫、耐壓、耐腐蝕的惰性填料,所述填料可以為不鏽鋼、陶瓷、惰性氧化矽中的一種或多種,其形狀可以是拉西環、鮑爾環,也可以是無孔的顆粒狀填料,填料的主要作用是使不易結焦物質沿塔徑向分散,避免不易結焦物質集中在塔中心軸區。
本發明方法中,步驟(1)所述的催化裂化原料油為常規催化裂化原料油,包括常壓加氫渣油、減壓加氫渣油、低硫直餾蠟油、低硫焦化蠟油等中的一種或幾種混合。催化裂化裝置可以是一套或一套以上,每套裝置至少包括一個反應器、一個再生器。催化裂化裝置按照本領域常規條件操作:反應溫度為480℃~530℃,再生溫度為650℃~750℃,劑油比為2~10(質量比),壓力0.1MPa~0.5 MPa。催化裂化裝置所用的催化劑為常規催化劑,包括矽鋁催化劑、矽鎂催化劑,也可以是X型、Y型、ZSM-5等分子篩催化劑。
本發明方法中,步驟(1)所述的催化裂化分餾系統分離出的中間餾分油餾程為250℃~500℃,最好為320℃~490℃,比中間餾分油重的餾分為催化油漿,要求中間餾分油和催化油漿的S≯0.5%(質量計)。
本發明方法中,步驟(2)中所述中間餾分油和催化油漿經過濾去除其中含有的灰分後在進入原料油加熱爐,過濾後的中間餾分油和催化油漿中含有的灰分≯0.1%(質量計)。
本發明方法中,所述焦化塔的操作溫度為410℃~505℃,操作壓力為0.5 MPa ~2MPa,可以是恆壓操作,也可以是變壓操作。
本發明方法中,所述的焦化塔底的下進料口位置為常規延遲焦化進料口的位置。
本發明方法中,步驟(2)所述的焦化分餾系統分離出的循環油為>200℃餾分油,優選>350℃餾分油。
本發明方法中,步驟(3)所述的循環油經加熱至430℃~510℃後進入延遲焦化塔,所述循環油的溫度比延遲焦化塔內溫度高0.1℃~25℃
本發明方法中,步驟(3)所述的循環油進料量為中間餾分油進料量的0.1~2(質量比)。
本發明方法中,所述不易結焦物質是水蒸氣、C1~C5輕烴、汽油餾分、柴油餾分中的一種或幾種。
本發明方法中,步驟(4)所述的不易結焦物質經加熱至460℃~535℃後進入延遲焦化塔,所述不易結焦物質的溫度比延遲焦化塔內溫度高10℃~40℃。
本發明方法中,步驟(4)所述的不易結焦物質的進料量為中間餾分油進料量的0.5~3倍。
與現有技術相比,本發明所述焦化塔及製備針狀焦的方法具有如下優點:
1、在焦化反應初期,中間餾分油和催化油漿採用上進料方式進入焦化塔,避免了由於新鮮原料的進入而造成體系擾動過大,為中間相小球體的生成、長大和融並提供了一個緩和、平穩的發育環境,有利於大面積廣域中間相的形成。在此階段,由於焦化塔內溫度較低、反應緩慢,體系粘度可以保持較低的水平。
2、在焦化反應中期,隨著反應溫度的升高,體系縮聚反應逐漸加劇,上進料口停止通入催化油漿,只通入中間餾分油,目的是為了緩解反應進程,避免原料油熱反應劇烈造成上部體系粘度迅速增加;從下進料口通入循環油,在有效的降低下部體系粘度的同時,隨著溫度的提高以氣體形式逸出,大大增加了體系內部氣流沿軸向方向的線速度,有利於芳香片層沿氣流方向有序排列。
3、在焦化反應後期,從塔底的下進料口向延遲焦化塔內通入不易結焦物質,大大加快了體系內部輕組分的逸出速率,廣域中間將在氣流的作用下發生內部結構定向排列,形成線型結構,完成「拉焦」過程;此外,不易結焦物質結焦傾向較低、分散性好,其以較高溫度進入焦化塔,將熱量迅速供給反應體系,在「拉焦」的同時促進體系固化。
4、催化裂化裝置的中間餾分油沒有以回煉油的形式返回裝置,採用單程通過的方式,大大降低了催化裂化再生器的燃燒負荷,為了維持體系熱量平衡,可以採取催化裂化原料油殘渣的方式,有利於提高催化裂化裝置的經濟效益。
5、焦化塔填料段和擋板對底部進料起到很好的分散作用,對氣流沿塔徑向方向上的分散起到促進作用,也使得體系溫度的均勻分布得到改善,大大提高焦炭的紋理結構和性能。在除焦階段,卸開焦化段、擋板和填料段連接處的法蘭,移開擋板和填料段,然後進行正常的除焦操作。對於填料上附著的焦炭,可以在空氣氣氛中燒掉,不會影響填料的循環使用。
附圖說明
圖1為本發明催化裂化-延遲焦化組合工藝製備針狀焦的流程示意圖。
圖2為本發明所述焦化塔結構示意圖。
具體實施方式
下面結合實施例進一步說明本發明的過程及效果。如圖1所述,催化裂化原料油1經過催化裂化裝置2反應,生成的油氣3進入催化裂化分餾系統4,分離出氣體5、輕油6、中間餾分油7和催化油漿8;其中,中間餾分油7和催化油漿8分別經過過濾裝置11和9過濾,去除灰分後的中間餾分油12和催化油漿13混合,混合油10經原料油加熱爐加熱至430℃~490℃的一段恆溫階段後,從上進料口進入焦化塔14A或14B(所述14A和14B切換使用),生成的油氣15經過焦化分餾系統16分離,得到氣體17、輕油18和循環油19;當原料油加熱爐進入二段升溫階段時,停止催化油漿13進料,去除灰分的中間餾分油12單獨從上進料口進入焦化塔,焦化循環油19經加熱後從下進料口進入焦化塔;當原料油加熱爐出口溫度大於490℃時,去除灰分的中間餾分油12從上進料口進入焦化塔、焦化循環油19從下進料口進入焦化塔,不易結焦物質20經加熱後也從下進料口進入焦化塔,直至充焦周期結束。
如圖2所示,本發明方法中,所述焦化塔包括筒體1、上封頭2和下封頭3,所述筒體1由上至下依次設置焦化段4和填料段5,焦化段4和填料段5之間設有擋板9,所述擋板9為帶有篩孔的擋板,焦化段4、擋板9和填料段5通過法蘭10固定連接,所述焦化段4的筒體上設置上進料口8,所述下封頭3設置下進料口7,下進料口7與填料段5連通。
實施例1
採用本發明所述的焦化塔和製備針狀焦的組合工藝方法,其中焦化塔上進料口距離塔底高度為總塔高的4/5,塔底填料段的高度為總塔高的1/10。
催化裂化原料油的基本性質見表1,催化裂化裝置的工藝條件見表2,催化劑採用牌號為RICC-1的催化劑。催化裂化產物進入分餾系統,分離出氣體、輕油、中間餾分油和催化油漿,其中,中間餾分油和催化油漿經過過濾處理,灰分含量降至0.1%以下。另外,中間餾分油餾程為348℃~454℃;延遲焦化生成的循環油為>350℃餾分。
表1 催化裂化原料油的基本性質
表2 催化裂化裝置的工藝條件
原料油加熱爐採用變溫控制,起始溫度440℃保持16h,然後以4℃/h的速率升溫至505℃保持3h。當原料油加熱爐出口溫度為440℃恆溫時,催化裂化裝置生成的中間餾分油和催化油漿從上進料口進入焦化塔;當原料油加熱爐處於程序升溫階段時,停止通入催化油漿,中間餾分油單獨從上進料口進入焦化塔,循環油從下進料口進入焦化塔,循環油預先經過變溫控制的加熱爐加熱,起始溫度440℃,然後在15h內勻速升溫至505℃,並保持恆溫直至充焦周期結束;當原料油加熱爐出口溫度大於490℃時,從延遲焦化塔塔底的下進料口通入不易結焦物質,不易結焦物質預先經過變溫控制的加熱爐加熱,起始溫度485℃,然後在3h內勻速升溫至520℃,並保持恆溫直至充焦周期結束。其中,循環油的進料量為中間餾分油進料量的1.5倍,不易結焦物質的進料量為中間餾分油進料量的1.3倍。在整個反應過程中,延遲焦化塔內溫度範圍為425℃~494℃,壓力恆定為0.8MPa。製備出的樣品較脆,粉焦過多,經2750℃石墨化後,熱膨脹係數為1.51×10-6/℃(100℃~600℃)。
實施例2
實施例採用本發明方法製備針狀焦,與實施例1的區別在於,延遲焦化裝置操作條件有所不同,體系採用變壓控制。
原料油加熱爐採用變溫控制,起始溫度440℃保持16h,然後以4℃/h的速率升溫至505℃保持3h。當原料油加熱爐出口溫度為440℃恆溫時,催化裂化裝置生成的中間餾分油和催化油漿從上進料口進入焦化塔;當原料油加熱爐處於程序升溫階段時,停止通入催化油漿,中間餾分油單獨從上進料口進入焦化塔,循環油從下進料口進入焦化塔,循環油預先經過變溫控制的加熱爐加熱,起始溫度440℃,然後在15h內勻速升溫至505℃,並保持恆溫直至充焦周期結束;當原料油加熱爐出口溫度大於490℃時,從延遲焦化塔塔底的下進料口通入不易結焦物質,不易結焦物質預先經過變溫控制的加熱爐加熱,起始溫度485℃,然後在3h內勻速升溫至520℃,並保持恆溫直至充焦周期結束。其中,循環油的進料量為中間餾分油進料量的1.5倍,不易結焦物質的進料量為中間餾分油進料量的1.3倍。在整個反應過程中,延遲焦化塔內溫度範圍為423℃~498℃;體系起始壓力為0.8MPa,當原料油加熱爐出口溫度達到505℃時,將體系壓力在1h內降至0.5MPa。製備出的樣品局部區域有存在大氣孔,經2750℃石墨化後,熱膨脹係數為1.37×10-6/℃(100℃~600℃)。
實施例3
實施例採用本發明方法製備針狀焦,與實施例1的區別在於,延遲焦化裝置操作條件有所不同,體系採用變壓控制。
原料油加熱爐採用變溫控制,起始溫度440℃保持16h,然後以4℃/h的速率升溫至505℃保持3h。當原料油加熱爐出口溫度為440℃恆溫時,催化裂化裝置生成的中間餾分油和催化油漿從上進料口進入焦化塔;當原料油加熱爐處於程序升溫階段時,停止通入催化油漿,中間餾分油單獨從上進料口進入焦化塔,循環油從下進料口進入焦化塔,循環油預先經過變溫控制的加熱爐加熱,起始溫度440℃,然後在15h內勻速升溫至505℃,並保持恆溫直至充焦周期結束;當原料油加熱爐出口溫度大於490℃時,從延遲焦化塔塔底的下進料口通入不易結焦物質,不易結焦物質預先經過變溫控制的加熱爐加熱,起始溫度485℃,然後在3h內勻速升溫至525℃,並保持恆溫直至充焦周期結束。其中,循環油的進料量為中間餾分油進料量的1.5倍,不易結焦物質的進料量為中間餾分油進料量的0.8倍。在整個反應過程中,延遲焦化塔內溫度範圍為425℃~497℃;體系起始壓力為1.2MPa,當原料油加熱爐出口溫度大於490℃時,將體系壓力在4h內降至0.5MPa。製備出的樣品外觀形貌較好,針狀焦經2750℃石墨化後,熱膨脹係數為1.33×10-6/℃(100℃~600℃)。