一種半導體器件的導通孔結構的製作方法
2023-06-09 11:17:46 3
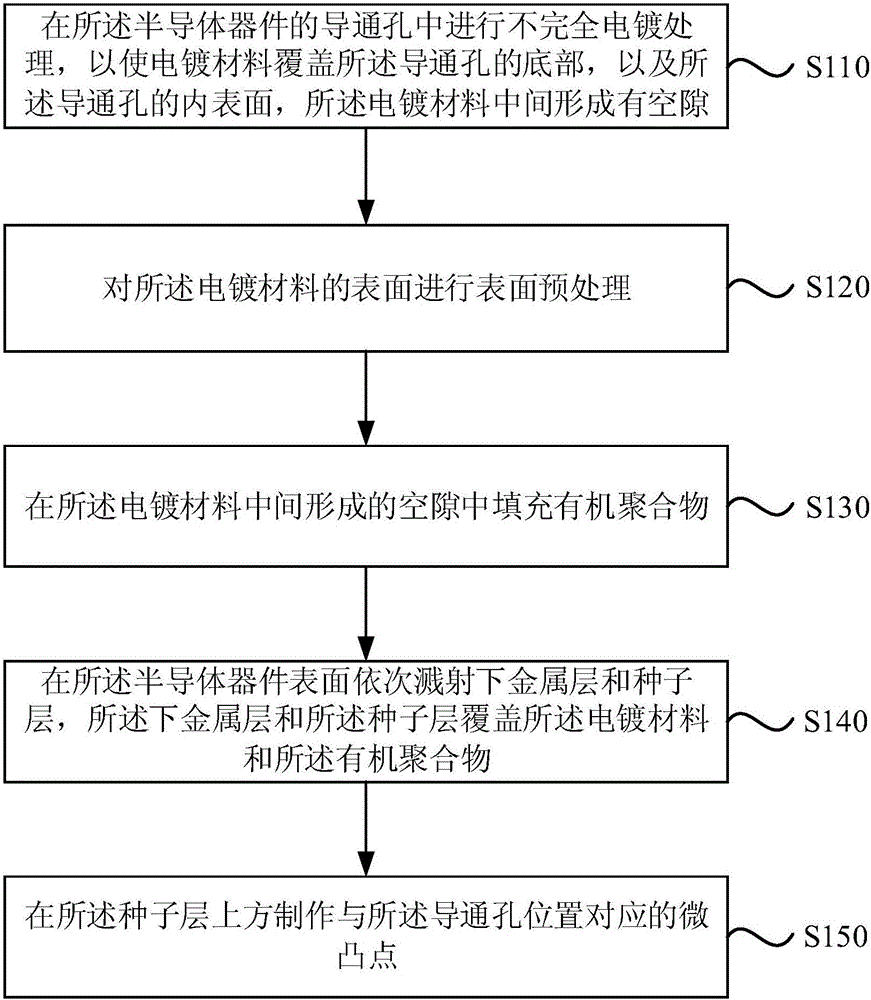
本發明實施例涉及微電子封裝技術,尤其涉及一種半導體器件的導通孔結構。
背景技術:
隨著半導體工業的飛速發展,對微系統的小型化、多功能集成化的要求日益迫切,具有高速互連、高密度集成、小型化以及同質和異質功能整合等優點半導體通孔的三維封裝,逐步成為半導體封裝技術的熱門的研究之一。
通過半導體導通孔的鍍銅填充來實現3D疊層電子封裝是今後重要的電子封裝形式。但是現有的半導體器件的導通孔結構一般採用鍍銅填充的方式來封裝導通孔,存在不能完全填充導通孔從而在導通孔中形成縫隙的問題,這些半導體器件的導通孔結構中的縫隙在後續的封裝過程中會造成應力集中問題,容易造成集成電路因應力集中而被破壞。
技術實現要素:
本發明實施例提供一種半導體器件的導通孔結構,以避免半導體通孔結構中出現縫隙以及應力集中的問題。
本發明實施例提供了一種半導體器件的導通孔結構,包括:
半導體基體;
導通孔,形成在所述半導體基體中,所述導通孔中填充有電鍍材料,所述電鍍材料覆蓋所述導通孔的底部,以及所述導通孔的內表面,所述電鍍材料中間形成有空隙,所述空隙中填充有有機聚合物;
依次形成在所述半導體器件表面的下金屬層和種子層,所述下金屬層和所述種子層覆蓋所述電鍍材料和所述有機聚合物;
微凸點,形成在所述種子層上方,且與所述導通孔的位置對應。
可選地,所述電鍍材料為銅。
可選地,所述有機聚合物為通過化學接枝工藝製成。
可選地,所述半導體基體的電阻率小於或等於106Ω·cm。
可選地,所述導通孔的直徑小於或等於50μm,所述導通孔的深寬比範圍為5:1~20:1。
可選地,所述半導體基體為單質半導體或化合物半導體。
可選地,所述半導體基體p型半導體或n型半導體。
可選地,所述半導體基體的材料為矽。
可選地,所述半導體基體的材料為砷化鎵。
可選地,所述導通孔為通孔或盲孔。
本發明實施例中,半導體器件導通孔結構的導通孔中填充有電鍍材料,電鍍材料未完全填滿導通孔並在導通孔中形成空隙,空隙中填充了有機聚合物,一方面,有機聚合物相比於金屬來說更易於實現孔徑的完全填充,避免了半導體器件導通孔結構中出現縫隙以及應力集中的問題;另一方面,在後續的封裝過程中,有機聚合物能夠有效地緩衝應力,進一步避免了應力集中的問題。
附圖說明
圖1為本發明實施例一提供的一種半導體器件的導通孔結構的結構示意圖;
圖2為本發明實施例二提供的一種半導體器件的導通孔結構的製作方法的流程圖;
圖3a為本發明實施例二提供的一種半導體器件的導通孔結構的製作方法的剖面結構示意圖一;
圖3b為本發明實施例二提供的一種半導體器件的導通孔結構的製作方法的剖面結構示意圖二;
圖3c為本發明實施例二提供的一種半導體器件的導通孔結構的製作方法的剖面結構示意圖三;
圖3d為本發明實施例二提供的一種半導體器件的導通孔結構的製作方法的剖面結構示意圖四。
具體實施方式
下面結合附圖和實施例對本發明作進一步的詳細說明。可以理解的是,此處所描述的具體實施例僅僅用於解釋本發明,而非對本發明的限定。另外還需要說明的是,為了便於描述,附圖中僅示出了與本發明相關的部分而非全部結構。
實施例一
圖1為本發明實施例一提供的一種半導體器件的導通孔結構的結構示意圖,如圖1所示,該導通孔結構包括半導體基體10、導通孔11、電鍍材料20、有機聚合物30、下金屬層41、種子層42以及微凸點50。其中,導通孔11形成在半導體基體10中,導通孔11中填充有電鍍材料20,電鍍材料20覆蓋導通孔11的底部以及導通孔11的內表面,電鍍材料20中間形成有空隙21,空隙21中填充有有機聚合物30。下金屬層41和種子層42依次形成在半導體器件的表面,下金屬層41和種子層42覆蓋電鍍材料20和有機聚合物30;微凸點50形成在種子層42上方,且與導通孔11的位置對應。
其中,導通孔11可以為通孔或盲孔。電鍍材料20為金屬材料,常見的為鎳、銅、鉻和鋅等金屬材料。可選地,電鍍材料20為銅。
下金屬層41可以由包含鈦或鉭等元素的材料組成,種子層42可以由包含銅元素的材料組成。下金屬層41的設置是為了增加種子層42和半導體器件表面的結合力,防止種子層42從半導體器件表面脫落,即防止種子層42與半導體基體10剝離。微凸點50可以採用銅錫焊料。需要說明的是,微凸點50通過種子層42和下金屬層41與半導體器件導通孔中的電鍍材料20相連接。
需要說明的是,半導體基體10上可以設置多個導通孔11,圖1中示例性地在半導體基體10上設置一個導通孔11。微凸點50與導通孔11一一對應,微凸點50可以位於與該微凸點50對應的導通孔11的一側,也可以是微凸點50位於與該微凸點50對應的導通孔11的正上方,此時,微凸點陣列塑性功密度最低,且分布均勻,微凸點的這種設計最為合理。
在上述結構的基礎上,可選地,半導體基體10的材料為矽或砷化鎵,半導體基體10為p型半導體或n型半導體,半導體基體10為單質半導體或化合物半導體,半導體基體10的電阻率小於或等於106Ω·cm。
在上述結構的基礎上,可選地,導通孔11的直徑小於或等於50μm,導通孔11的深寬比範圍為5:1~20:1。
可選地,有機聚合物30為通過化學接枝工藝製成。在電鍍材料中間形成的空隙中填充有機聚合物包括:將半導體器件放入水相溶液中進行化學接枝,以在空隙中填充有機聚合物。化學接枝方法是利用材料表面的反應基團與被接枝的單體或大分子鏈發生化學反應而實現表面接枝。其中,水相溶液為包含表面活性劑、有機單體、引發劑、絡合劑和酸的溶液,pH≤2.5。表面活性劑為十二烷基磺酸鈉和/或月桂醇醚磷酸酯;有機單體為含有碳碳雙鍵結構的物質;引發劑為氟硼酸重氮鹽、吡唑重氮內鹽和三蝶烯重氮鹽中的至少一種。化學接枝的溫度為5-35℃,反應時間為0.1-10h。
採用化學接枝的方式來達到對導通孔中縫隙填充進而實現導通孔完全填充的目的,而不是採用灌注的方式將有機聚合物灌注到導通孔中是因為有機物聚合物具有一定的黏度,且有機物聚合物對半導體材料的潤溼性不好,因而無法實現對導通孔的完全填充。
本發明實施例中,半導體器件導通孔結構的導通孔中填充有電鍍材料,電鍍材料未完全填滿導通孔並在導通孔中形成空隙,空隙中填充了有機聚合物,一方面,有機聚合物相比於金屬來說更易於實現孔徑的完全填充,避免了半導體器件導通孔結構中出現縫隙以及應力集中的問題;另一方面,在後續的封裝過程中,有機聚合物能夠有效地緩衝應力,進一步避免了應力集中的問題。
實施例二
圖2為本發明實施例二提供的一種半導體器件的導通孔結構的製作方法的流程圖,可以用於製造上述的半導體器件的導通孔結構,如圖2所示,該方法包括如下步驟:
S110、在所述半導體器件的導通孔中進行不完全電鍍處理,以使電鍍材料覆蓋所述導通孔的底部,以及所述導通孔的內表面,所述電鍍材料中間形成有空隙。
其中,導通孔可以為通孔或盲孔。電鍍材料為金屬材料,常見的為鎳、銅、鉻和鋅等金屬材料。可選地,電鍍材料為銅。
S120、對所述電鍍材料的表面進行表面預處理。
可選地,對電鍍材料的表面進行除油處理以去除電鍍材料表面的油汙等雜質;然後對電鍍材料的表面進行酸洗處理,可以是無機酸也可以是有機酸,可以是一種酸也可以是多種酸的混合物,本發明實施例對此不作限定,例如,可以使用硫酸對電鍍材料的表面進行酸洗處理,以去除電鍍材料表面的氧化層;然後對電鍍材料的表面進行水洗處理,本發明實施例對水洗處理過程中使用的水的類型不做限定,可以是去離子水、蒸餾水或純水。
S130、在所述電鍍材料中間形成的空隙中填充有機聚合物。
S140、在所述半導體器件表面依次濺射下金屬層和種子層,所述下金屬層和所述種子層覆蓋所述電鍍材料和所述有機聚合物。
下金屬層可以由包含鈦或鉭等元素的材料組成,種子層可以由包含銅元素的材料組成。下金屬層的設置是為了增加種子層和半導體器件表面的結合力,防止種子層從半導體器件表面脫落。
S150、在所述種子層上方製作與所述導通孔位置對應的微凸點。
其中,微凸點可以採用銅錫焊料。需要說明的是,微凸點通過種子層和下金屬層與半導體器件導通孔中的電鍍材料相連接。
在種子層的上方形成微凸點可以採用塗覆光刻膠的方式,具體為:在種子層上方通過旋塗的方式塗覆光刻膠,示例性地本發明實施例使用的是正膠;對光刻膠掩膜曝光使之圖形化,再以溶劑浸泡將光刻膠中受到光照的部分溶解掉,以形成設定圖形,且漏出部分種子層;然後在光刻膠漏出種子層的部分通過電鍍的方式形成微凸點;去除光刻膠。本發明實施例中可以使用正膠或負膠,本發明實施例對此不作限定。
需要說明的是,微凸點與導通孔一一對應,微凸點可以位於與該微凸點對應的導通孔的一側,也可以是微凸點位於與該微凸點對應的導通孔的正上方,此時,微凸點陣列塑性功密度最低,且分布均勻,微凸點的這種設計最為合理。
在上述製作方法的基礎上,可選地,在電鍍材料中間形成的空隙中填充有機聚合物包括:將半導體器件放入水相溶液中進行化學接枝,以在空隙中填充有機聚合物。化學接枝方法是利用材料表面的反應基團與被接枝的單體或大分子鏈發生化學反應而實現表面接枝。其中,水相溶液為包含表面活性劑、有機單體、引發劑、絡合劑和酸的溶液,pH≤2.5。表面活性劑為十二烷基磺酸鈉和/或月桂醇醚磷酸酯;有機單體為含有碳碳雙鍵結構的物質;引發劑為氟硼酸重氮鹽、吡唑重氮內鹽和三蝶烯重氮鹽中的至少一種。化學接枝的溫度為5-35℃,反應時間為0.1-10h。
採用化學接枝的方式來達到對導通孔中縫隙填充進而實現導通孔完全填充的目的,而不是採用灌注的方式將有機聚合物灌注到導通孔中是因為有機物聚合物具有一定的黏度,且有機物聚合物對半導體材料的潤溼性不好,因而無法實現對導通孔的完全填充。
在上述製作方法的基礎上,可選地,在所述半導體器件表面依次濺射下金屬層和種子層之前還包括:對所述半導體器件的表面進行化學機械拋光,以使所述半導體器件的表面平整。
可選地,半導體器件包括半導體基體,半導體基體的材料為矽或砷化鎵。
示例性地,本發明實施例以矽器件導通孔結構和砷化鎵器件導通孔結構為例來說明半導體器件導通孔結構的製作方法,可以理解的是,半導體導器件的導通孔結構的製作方法包括但不限於矽器件導通孔結構和砷化鎵器件導通孔結構的製作方法。
一方面,本實施例提供的一種矽器件導通孔結構的製作方法,如下:
步驟(1)、矽器件採用P型矽,其電阻率為5Ω·cm。參考圖3a,該矽器件包括半導體基底10(材料為矽),在矽器件的導通孔11中進行不完全電鍍銅處理,以使電鍍材料20覆蓋導通孔11的底部,以及導通孔11的內表面,且電鍍材料20中間形成有空隙21,電鍍材料20可以採用銅,即電鍍填銅,但不完全填滿。然後將不完全鍍銅填充的矽器件放入丙酮、乙醇中進行除油處理,使用酸洗處理方法除去銅表面的氧化物,並對電鍍材料的表面使用純水衝洗乾淨。
步驟(2)、將經過步驟(1)處理後的矽器件放入配置好的水相溶液中反應。其中,水相溶液的組分為0.01g/mL的十二烷基磺酸鈉、6%體積分數的鹽酸和丙烯酸、0.002g/mL的吡唑重氮內鹽和0.01g/mL的EDTA-2Na(乙二胺四乙酸二鈉)。
步驟(3)、於設定時間間隔後,將矽器件從水相溶液中取出。
需要說明的是,有機聚合物的生長是自導通孔結構的底部嚮導通孔結構的頂部生長的,且有機聚合物的生長隨時間的變化關係是線性的。可以理解的是,設定時間間隔越長,有機聚合物在電鍍材料形成的空隙中生長的越充分,參考圖3b,當達到某一時間間隔時,有機聚合物30完全填充了電鍍材料形成的空隙21。
步驟(4)、對矽器件的表面進行化學機械拋光。
參考圖3c,對矽器件的表面進行化學機械拋光,以使矽器件的表面變得平整,以便後續工序的進行,保證了矽導通孔結構的質量。
步驟(5)、參考圖3d,在矽器件表面依次濺射下金屬層41和種子層42,下金屬層41和種子層42覆蓋電鍍材料銅20和有機聚合物30。種子層42可以採用材料銅。
步驟(6)、參考圖1,在種子層42的上方形成微凸點50,且微凸點50與矽器件的導通孔11的位置對應。
在種子層42的上方形成微凸點50,具體可以採用塗覆光刻膠的方式,在此不再贅述。
上述矽器件導通孔結構的製作方法為優選方案,可實現有機聚合物優先從導通孔結構的底部生長,即實現有機聚合物自導通孔結構的底部嚮導通孔結構的頂部生長,若將上述步驟(2)中水相溶液的組分替換為:0.01g/mL的十二烷基磺酸鈉,2%體積分數的硫酸,6%體積分數的甲基丙烯酸甲酯,0.002g/mL的吡唑重氮內鹽。則發現有機聚合物同時在導通孔的底部和內表面沉積,無法實現底部優先生長,因此填充的有機物聚合物無法實現緻密完全的生長。
另一方面,本實施例還提供了一種砷化鎵導通孔結構的製作方法,如下:
步驟(1)、砷化鎵器件採用n型砷化鎵,其電阻率為50Ω·cm。在砷化鎵器件的導通孔中進行不完全電鍍銅處理,以使電鍍材料銅覆蓋導通孔的底部,以及導通孔的內表面,且電鍍材料銅中間形成有空隙,即電鍍填銅,但不完全填滿。然後將不完全鍍銅填充的砷化鎵器件放入丙酮、乙醇中進行除油處理,然後使用酸洗處理方法除去銅表面的氧化物,並對電鍍材料的表面使用純水衝洗乾淨。
步驟(2)、將經過步驟(1)處理後的砷化鎵器件放入配置好的水相溶液中反應。其中,水相溶液的組分為組分為1g/mL的十二烷基磺酸鈉,2%體積分數的硫酸,6%體積分數的丙烯酸,0.002g/mL的三蝶烯重氮鹽,0.01g/mL的EDTA-2Na(乙二胺四乙酸二鈉)。
步驟(3)、於設定時間間隔後,將砷化鎵器件從水相溶液中取出。
需要說明的是,有機聚合物的生長是自導通孔結構的底部嚮導通孔結構的頂部生長的,且有機聚合物的生長隨時間的變化關係是線性的。可以理解的是,設定時間間隔越長,有機聚合物在電鍍材料形成的空隙中生長的越充分,當達到某一時間間隔時,有機聚合物完全填充了電鍍材料形成的空隙。
步驟(4)、對砷化鎵器件的表面進行化學機械拋光,以使砷化鎵器件的表面變得平整,以便後續工序的進行,保證了砷化鎵導通孔結構的質量。
步驟(5)、在砷化鎵器件表面依次濺射下金屬層和銅種子層,下金屬層和銅種子層覆蓋電鍍材料銅和有機聚合物。
步驟(6)、在銅種子層的上方形成微凸點,且微凸點與砷化鎵器件的導通孔的位置對應。
本發明實施例通過對半導體器件的導通孔進行不完全電鍍處理和對電鍍材料進行表面預處理,並將表面預處理後的半導體器件放入到水相溶液中進行化學接枝,一方面,由於對半導體器件在水相溶液中進行化學接枝時,能夠在電鍍材料和有機聚合物之間形成結合力好的電鍍材料-C化學鍵,使得半導體器件的導通孔結構中的電鍍材料和有機物聚合物的接觸面有較強的結合力,另一方面,由於對半導體器件在水相溶液中進行化學接枝時,有機物聚合物自導通孔結構的底部嚮導通孔結構的頂部生長,實現了半導體器件的導通孔的完全填充,避免了孔內缺陷。
注意,上述僅為本發明的較佳實施例及所運用技術原理。本領域技術人員會理解,本發明不限於這裡所述的特定實施例,對本領域技術人員來說能夠進行各種明顯的變化、重新調整和替代而不會脫離本發明的保護範圍。因此,雖然通過以上實施例對本發明進行了較為詳細的說明,但是本發明不僅僅限於以上實施例,在不脫離本發明構思的情況下,還可以包括更多其他等效實施例,而本發明的範圍由所附的權利要求範圍決定。