壓力傳感器的製備方法及壓力傳感器與流程
2023-06-27 21:45:26 1
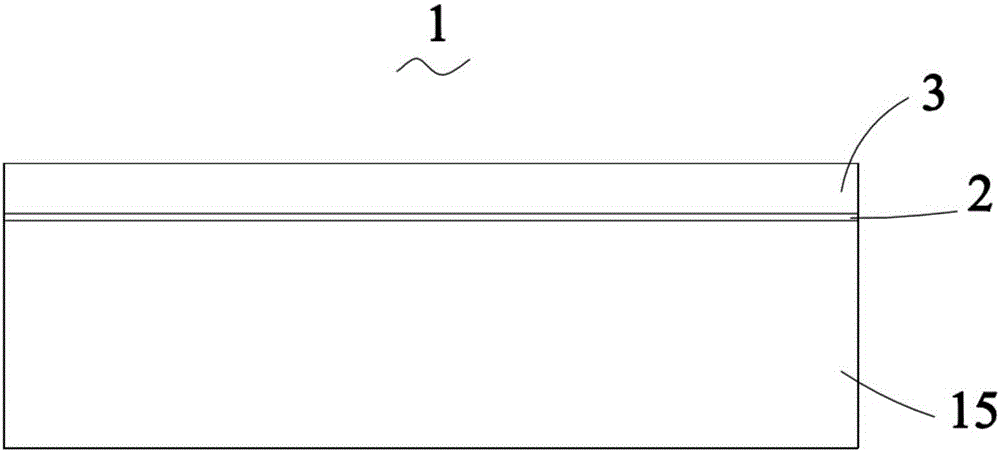
本發明涉及一種壓力傳感器的製備方法及壓力傳感器,屬於微機械製造領域。
背景技術:
1962年,Tufte等第一次用擴散矽壓阻條和矽膜結構加工出壓阻式壓力傳感器,開始了壓阻式壓力傳感器的研究。20世紀60年代末70年代初,矽各向異性腐蝕技術、離子注入技術以及陽極鍵合技術三大技術的出現給壓力傳感器帶來了巨大的變革,它們在提高壓力傳感器的性能上起到了舉足輕重的作用。從20世紀80年代至今,微加工技術的進一步發展,如各向異性腐蝕、光刻、擴散摻雜、離子注入、鍵合以及鍍膜等技術,使得壓力傳感器的尺寸不斷減小、靈敏度得以提高、產量高以及性能優異。同時,新的微加工工藝的開發和應用使得壓力傳感器的膜厚得以精確控制。Jackson等以及Kim和Wise分別研究了P-N結的電化學性質,利用P型矽和N型矽在腐蝕液中腐蝕率的差異(3000:1在乙二胺為主的腐蝕液中)來製備矽膜。Kloeck等報導了利用電化學自停止技術來提高壓阻式壓力傳感器的輸出特性。在20世紀80年代後期,NovaSensor開始利用該技術生產出大量的壓力傳感器。
至今,壓力傳感器的製造已經發展到一個新的階段,更多新的工藝技術將應用於壓力傳感器的生產中,以下為最具代表性的三種現有技術。
現有技術一,Freescale Manifold Air Pressure(MAP)sensor利用KOH等各向異性溼法腐蝕技術刻蝕深腔形成壓力敏感膜,最後在背面深腔側鍵合玻璃或矽片形成壓力腔。但,使用KOH等溼法腐蝕溶液,會有K離子汙染,影響器件性能,汙染產線;另外時間控制腐蝕深度,使壓力敏感膜厚度難以精確控制;鍵合工藝會對圓片正面的金屬層造成壓傷;
現有技術二,NovaSensor pressure sensor首先在襯底圓片上腐蝕出壓力深腔,然後在壓力深腔側鍵合一片N型圓片,通過減薄拋光上面的N型圓片,形成壓力敏感膜,接著在壓力敏感膜上注入擴散等工藝形成壓阻,金屬連線及鈍化層等結構,最後對背面進行減薄等工藝從背面打開壓力腔。但是,該技術存在如下問題:首先完成壓力深腔,壓力敏感膜密封在上面,後續高溫工藝會使壓力敏感膜變形,甚至破裂,影響後續工藝及成品率;壓力敏感膜使用圓片鍵合減薄等工藝,工藝難度大,難以製造較薄並平坦的壓力敏感膜;
現有技術三,Bosch多孔矽外延技術製備的壓阻式壓力傳感器,其工藝使用多孔矽外延單晶矽形成密封腔和壓力敏感膜。但,多孔矽外延單晶矽技術等相關工藝技術,包括其它在空腔上外延單晶矽技術形成密封腔和壓力敏感膜技術,工藝難度高,很難形成平坦的壓力敏感膜,並且並不適用表壓壓力傳感器的製造。
技術實現要素:
本發明的目的在於提供一種壓力傳感器的製備方法,通過該製備方法避免了高溫擴散工藝對鍵合工藝的影響,防止了高溫擴散工藝破壞真空腔上的壓力敏感膜,並且避免了鍵合工藝對金屬連線的壓傷。
為達到上述目的,本發明提供如下技術方案:一種壓力傳感器的製備方法,包括如下步驟:
S1:提供具有背面和正面的晶圓;
在所述晶圓的正面形成壓阻條和重摻接觸區;
通過所述晶圓的背面刻蝕形成壓力深腔;
S2:在所述晶圓的背面鍵合支撐片;
S3:在所述晶圓的正面製作引線孔和金屬連線,連接壓阻條形成惠斯通電橋;
S4:在所述晶圓的正面沉積形成鈍化層,打開部分鈍化層以形成金屬焊盤區域。
進一步的:所述S1具體包括如下步驟:
S11:提供具有背面和正面的晶圓,在所述晶圓上定義壓力敏感膜的厚度;
S12:在所述晶圓的正面使用離子注入,採用高溫擴散工藝製作壓阻條,重摻接觸區;
S13:在晶圓的正面沉積形成保護層;
S14:在所述晶圓背面刻蝕形成壓力深腔以形成壓力敏感膜。
進一步的:所述晶圓為SOI。
進一步的:所述壓力深腔通過深反應離子蝕刻工藝形成。
進一步的:所述S13具體包括:在晶圓的正面沉積以氧化層和氮化層形成保護層。
進一步的:所述S13與S14之間包括:將所述晶圓的背面減薄拋光以降低晶圓厚度。
進一步的:在所述S3中,還包括:當晶圓的背面鍵合支撐片後,在所述支撐片上打孔以形成與所述壓力深腔連接的通孔。
進一步的:所述支撐片為矽片或者玻璃片。
進一步的:在所述S4中,所述鈍化層通過沉積氧化矽和氮化矽而形成。
本發明還提供了一種壓力傳感器,通過上述壓力傳感器的製備方法所形成。
本發明的有益效果在於:本發明的壓力傳感器的製備方法將鍵合工藝放在高溫擴散工藝之後,金屬連線工藝之前,從而避免了高溫擴散工藝對鍵合工藝的影響,防止了高溫擴散工藝破壞真空腔上的壓力敏感膜,並且避免了鍵合工藝對金屬連線的壓傷,進而提升了產品的製造良率。
上述說明僅是本發明技術方案的概述,為了能夠更清楚了解本發明的技術手段,並可依照說明書的內容予以實施,以下以本發明的較佳實施例並配合附圖詳細說明如後。
附圖說明
圖1為本發明一實施例所示的表壓壓力傳感器;
圖2A至圖2I為圖1所示的表壓壓力傳感器的製備方法;
圖3為本發明另一實施例所示的絕壓壓力傳感器。
具體實施方式
下面結合附圖和實施例,對本發明的具體實施方式作進一步詳細描述。以下實施例用於說明本發明,但不用來限制本發明的範圍。
請參見圖1並結合圖2A至圖2I,本發明一較佳實施例所示的表壓壓力傳感器100的製備方法包括如下:
請結合圖2A,第一步:提供晶圓1,該晶圓1為(100)晶面的SOI(silicon on insulator)。所述晶圓1從下至上依次為下層矽15、氧化埋層2和位於氧化埋層2上的上層矽3;該氧化埋層2的材料為氧化矽。將氧化埋層2上的上層矽3厚度精確定義為表壓壓力傳感器100的壓力敏感膜4的厚度;
請結合圖2B,第二步:在所述晶圓1的正面製作零層對位標記5,用於後續工藝的前層對位標記;
請結合圖2C,第三步:在晶圓1的正面使用離子注入,採用高溫擴散工藝製作壓阻條6,重摻接觸區7;
請結合圖2D,第四步:在晶圓1上沉積氧化層和氮化層,以作為後續減薄拋光工藝的保護層8,同樣的,該保護層8又可以作為表壓壓力傳感器100的絕緣層;
請結合圖2E,第五步:將晶圓1的背面減薄拋光以降低晶圓1的厚度,進而減少後續刻蝕壓力深腔的深度,使表壓壓力傳感器100總厚度減小;
請結合圖2F,第六步:在晶圓1的背面通過深反應離子蝕刻工藝(DRIE)刻蝕形成壓力深腔9,刻蝕停止在氧化埋層2上,形成壓力敏感膜4;由於刻蝕氧化矽和矽具有很高的選擇比,所以通過深反應離子蝕刻工藝可以精準控制壓力敏感膜4的厚度;
請結合圖2G,第七步:在晶圓1背面鍵合支撐片10,該支撐片10材料可以但不局限於矽片或是玻璃片。在本實施例中,當晶圓1的背面鍵合支撐片10後,在所述支撐片10上打孔以形成與所述壓力深腔9聯通的通孔16;
請結合圖2H,第八步:在晶圓1的正面的保護層8上開孔以製作形成引線孔11,在引線孔11和保護層8上形成金屬連線12以連接壓阻條6形成惠斯通電橋,以用於測量壓力敏感膜4變化引起的電阻變化;
請結合圖2I,第九步:在晶圓1的正面沉積氧化矽和氮化矽作為鈍化層13,打開部分鈍化層13以形成金屬焊盤14區域,用於後續打線。
在其他實施例中,可將第三步放在第六步之後,但是,通過本實施例中將第六步放在第三步之前(即:將高溫擴散工藝放在壓力深腔9製備的前面),可避免由於熱效應而引起壓力敏感膜4遭到破壞,可提高產品成品率和工藝可行性。另外,在本實施例中,通過將深反應離子蝕刻工藝刻蝕壓力深腔9結合使用SOI製備壓力敏感膜,可以精確控制壓力敏感膜4的厚度,提高壓力傳感器的一致性,避免了金屬離子汙染,並且減小了壓力傳感器的面積,而且,與現有技術相比,還可避免直接使用減薄拋光等技術,可以更精確的控制壓力敏感膜4的厚度,更易獲得平坦的壓力敏感膜4。
上述製備工藝可形成表壓壓力傳感器100,在其他實施方式中,若在第七步中,當晶圓1的背面鍵合支撐片10後,在所述支撐片10上不打孔,則可形成絕壓壓力傳感器200(請參見圖3)。
綜上所述:通過上述壓力傳感器的製備方法的製備方法可得到如下優點:
1、通過將鍵合工藝移至金屬層工藝之前,避免了鍵合工藝對金屬層(金屬連線12)的壓傷;
2、通過將鍵合工藝放在高溫擴散工藝之後,避免了高溫擴散工藝對鍵合工藝的影響,防止了高溫擴散工藝破壞壓力深腔9上的壓力敏感膜4;
3、通過將高溫擴散工藝放在壓力深腔9製備之前,可避免由於熱效應引起壓力敏感膜4遭到破壞,提高產品成品率和工藝可行性;
4、通過將深反應離子蝕刻工藝刻蝕深腔結合使用SOI製備壓力敏感膜4,可以精確控制壓力敏感膜4的厚度,提高壓力傳感器的一致性,避免了金屬離子汙染,並且減小了壓力傳感器的面積,而且,與現有技術相比,還可避免直接使用減薄拋光等技術,可以更精確的控制壓力敏感膜4的厚度,更易獲得平坦的壓力敏感膜4。
以上所述實施例的各技術特徵可以進行任意的組合,為使描述簡潔,未對上述實施例中的各個技術特徵所有可能的組合都進行描述,然而,只要這些技術特徵的組合不存在矛盾,都應當認為是本說明書記載的範圍。
以上所述實施例僅表達了本發明的幾種實施方式,其描述較為具體和詳細,但並不能因此而理解為對發明專利範圍的限制。應當指出的是,對於本領域的普通技術人員來說,在不脫離本發明構思的前提下,還可以做出若干變形和改進,這些都屬於本發明的保護範圍。因此,本發明專利的保護範圍應以所附權利要求為準。