鋁電解槽低溫餘熱回收利用系統的製作方法
2023-06-12 20:47:11 1
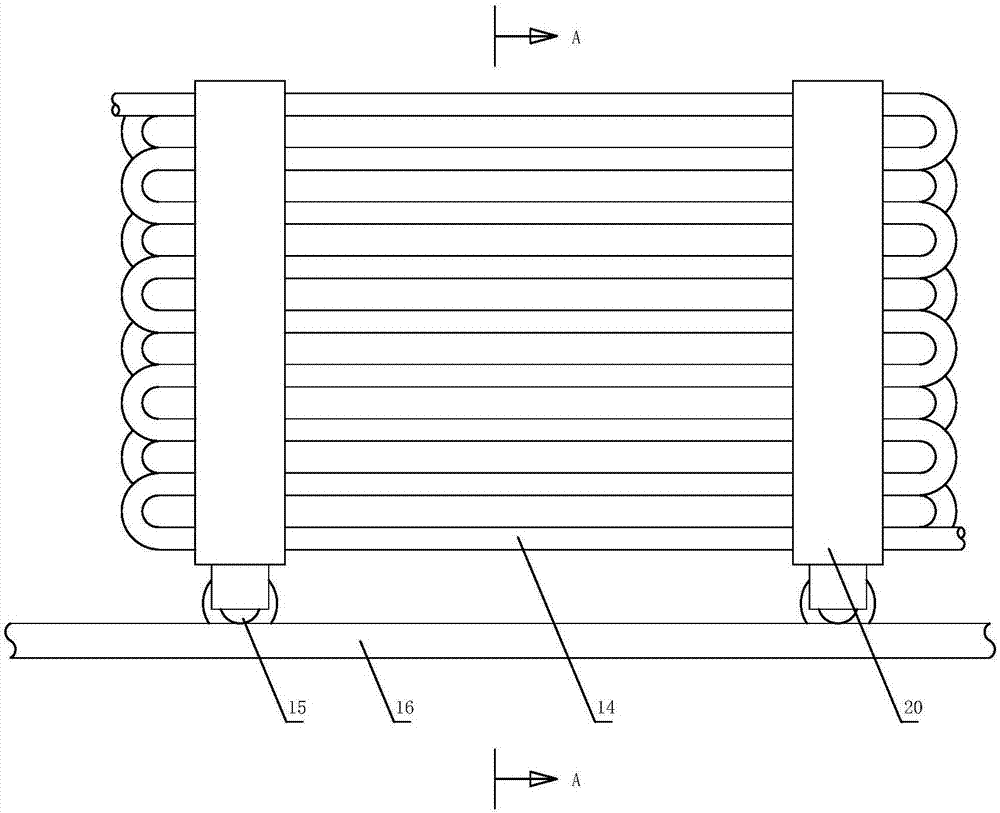
本實用新型涉及餘熱回收利用系統,尤其涉及鋁電解槽低溫餘熱回收利用系統。
背景技術:
:
電解鋁行業屬於高耗能行業,目前電解鋁生產能源利用率不到50%,電能除一部分用於電解反應生產出電解鋁外,其它一半以上以熱散失的形式損失掉。損失的熱量通過電解槽的不同部位散發到外圍空間,其中一部分以低溫煙氣形式排放到大氣中,所含的餘熱資源被白白浪費掉,煙氣帶走的熱量大致佔整個槽體系支出的15%-30%。雖然電解槽容量不同,但是在一般情況下電解槽的煙氣系統基本相同,每臺槽子的煙氣分別通過槽體系本身的支氣煙氣管,匯總進入地下煙道,然後送入除塵系統,經過除塵淨化後的煙氣最後由引風機抽到煙囪後排出,電解鋁生產過程中生產的低溫煙氣溫度一般為85℃-140℃,回收利用這部分餘熱能夠開創電解鋁行業節能減排工作的新局面,而低溫煙氣餘熱技術是一種有效的節能途徑。
技術實現要素:
:
本實用新型的目的是為了解決現有鋁電解槽生產過程中大量低溫煙氣被排放到大氣中,其中所含的餘熱資源被白白浪費掉的問題,提供一種鋁電解槽低溫餘熱回收利用系統。
本實用新型的目的由如下技術方案實施,鋁電解槽低溫餘熱回收利用系統,其包括電解槽地下煙道、收塵裝置和排煙裝置,所述電解槽地下煙道的煙氣出口與所述收塵裝置的煙氣入口連通,所述收塵裝置的煙氣出口與所述排煙裝置的煙氣入口連通;
其還包括吸收式熱泵機組、煙氣換熱器和鍋爐;
所述吸收式熱泵機組中取熱器的煙氣入口與所述電解槽地下煙道通過第一煙氣支管連通,所述取熱器的煙氣出口與所述電解槽地下煙道通過第二煙氣支管連通,在所述第一煙氣支管或所述第二煙氣支管上設有循環泵;所述吸收式熱泵機組中再熱器的熱介質出口與熱站連接,所述吸收式熱泵機組中加熱器的進水口與熱站回水連接;
所述煙氣換熱器設於電解槽地下煙道內,所述煙氣換熱器包括支撐架和固定設於所述支撐架上的蛇形管,所述蛇形管的進水口連接水源,所述蛇形管的出水口分別與所述熱站和所述鍋爐的進水口連接;在所述支撐架的下方設有行走輪,在所述電解槽地下煙道內設有與所述行走輪對應的軌道,所述行走輪支撐於所述軌道上,並可沿所述軌道行走,方便所述換熱器進出所述電解槽地下煙道,便於所述煙氣換熱器的布置與檢修;
所述鍋爐的排汽口與所述吸收式熱泵機組中濃縮器的驅動熱源入口連接。
進一步的,在所述第一煙氣支管與所述第二煙氣支管之間的所述電解槽地下煙道內設有閥門。
進一步的,所述煙氣換熱器設置於所述第一煙氣支管上遊或所述第二煙氣支管下遊的所述電解槽地下煙道內。
本實用新型的優點:
1、本實用新型利用鍋爐蒸汽作為吸收式熱泵機組的驅動熱源,回收利用來自鋁電解槽煙氣中的低溫餘熱,並將該熱量轉換為中溫熱水,結構簡單,設備投資少,回收了低溫餘熱,有效減少了資源浪費;而且進入鍋爐內的來水首先經過煙氣換熱器的換熱,提高了煙氣的熱利用率。
2、本實用新型中煙氣換熱器結構簡單,蛇形管外無殼體包覆,便於清理蛇形管壁上的積灰;煙氣換熱器可沿軌道滑動,方便了安裝於檢修。
附圖說明:
為了更清楚地說明本實用新型實施例或現有技術中的技術方案,下面將對實施例或現有技術描述中所需要使用的附圖作簡單地介紹,顯而易見地,下面描述中的附圖僅僅是本實用新型的一些實施例,對於本領域普通技術人員來講,在不付出創造性勞動的前提下,還可以根據這些附圖獲得其他的附圖。
圖1為實施例1鋁電解槽低溫餘熱回收利用系統結構示意圖;
圖2為實施例1中煙氣換熱器結構示意圖;
圖3為圖2的A-A視圖;
圖4為實施例1中吸收式熱泵機組結構示意圖。
圖中:電解槽地下煙道1,收塵器2,煙囪3,吸收式熱泵機組4,煙氣換熱器5,鍋爐6,取熱器7,第一煙氣支管8,第二煙氣支管9,閥門10,循環泵11,再熱器12,加熱器13,蛇形管14,行走輪15,軌道16,濃縮器17,熱站18,水源19,支撐架20。
具體實施方式:
下面將結合本實用新型實施例中的附圖,對本實用新型實施例中的技術方案進行清楚、完整地描述,顯然,所描述的實施例僅僅是本實用新型一部分實施例,而不是全部的實施例。基於本實用新型中的實施例,本領域普通技術人員在沒有作出創造性勞動前提下所獲得的所有其他實施例,都屬於本實用新型保護的範圍。
實施例1:
鋁電解槽低溫餘熱回收利用系統,其包括電解槽地下煙道1、收塵器2、煙囪3、吸收式熱泵機組4、煙氣換熱器5和鍋爐6;電解槽地下煙道1的煙氣出口與收塵器2的煙氣入口連通,收塵器2的煙氣出口與煙囪3的煙氣入口連通;
吸收式熱泵機組4中取熱器7的煙氣入口與電解槽地下煙道1通過第一煙氣支管8連通,取熱器7的煙氣出口與電解槽地下煙道1通過第一煙氣支管8連通,在第一煙氣支管8與第二煙氣支管9之間的電解槽地下煙道1內設有閥門10;在第一煙氣支管8上設有循環泵11;吸收式熱泵機組4中再熱器12的熱介質出口與熱站18連接,吸收式熱泵機組4中加熱器13的進水口與熱站18回水連接;
煙氣換熱器5設置於第二煙氣支管9下遊的電解槽地下煙道1內;煙氣換熱器5包括支撐架20和固定設於支撐架20上的蛇形管14,蛇形管14的進水口連接水源19,蛇形管14的出水口分別與熱站18和鍋爐6的進水口連接;在支撐架20的下方設有行走輪15,在電解槽地下煙道1內設有與行走輪15對應的軌道16,行走輪15支撐於軌道16上,並可沿軌道16行走,方便換熱器進出電解槽地下煙道1,便於煙氣換熱器5的布置與檢修;
鍋爐6的排汽口與吸收式熱泵機組4中濃縮器17的驅動熱源入口連接。
工作原理:
關閉閥門10,煙氣換熱器5中的供水經換熱後,一部分供給熱站18,另一部分供給鍋爐6產生蒸汽,吸收式換熱泵機組以鍋爐6蒸汽作為驅動熱源,加熱器13與濃縮器17中的連通部分填充有溴化鋰溶液;
取熱器7內一直保持負壓狀態,利用水在一定的低壓環境下,便會低溫沸騰、氣化的原理,將水變為水蒸氣。然後,將水蒸氣引入到加熱器13,再以溴化鋰溶液噴淋,利用溴化鋰溶液強大吸水性的特性,其吸收水蒸氣會產生大量的熱,將加熱器13中循環管路的水加熱,使其溫度升高。
濃縮器17的作用是對吸收水蒸氣後的溴化鋰稀溶液進行濃縮,重新得到具有強大吸水性的溴化鋰濃溶液。
再熱器12是利用濃縮器17內蒸汽加熱濃縮溴化鋰稀溶液變成溴化鋰濃溶液而蒸發出來的二次乏汽,對上述循環管路中經過加熱器13加熱後的熱水進行再加熱,從而達到更高的溫度。
具體的可劃分為如下過程:
過程一:餘熱熱量的提取
在負壓的取熱器7內,利用水在負壓狀態下沸點降低的原理,來自再熱器12的蒸汽凝水噴淋在取熱器7內低溫蒸發,凝水吸收煙氣餘熱,蒸發汽化產生蒸汽進入加熱器13,完成餘熱熱量的提取過程。
過程二:餘熱熱量的轉移
在加熱器13內,利用溴化鋰濃溶液的吸水放熱性能,來自濃縮器17的溴化鋰濃溶液分布在加熱器13換熱管外部,吸收來自供暖換熱器的水蒸汽,溶液的溫度迅速升高,加熱換熱管內需要提高溫度的熱媒,實現了低溫熱源的熱量向被加熱熱媒轉移,同時溴化鋰溶液由濃變稀,不再具有吸水性,需要濃縮後循環使用。
過程三:工質濃縮
在濃縮器17內,利用驅動熱源的熱量,對來自加熱器13的溴化鋰稀溶液進行濃縮,產生的濃溶液繼續回到加熱器13內繼續吸收水蒸汽加熱供熱水,溶液濃縮產生的高溫二次蒸汽去再熱器12。
過程四:二次蒸汽再加熱
在再熱器12內,利用來自濃縮器17的高溫二次蒸汽凝結潛熱的熱量,對來自加熱器13的經過一次加熱的熱媒進行再次加熱,最終達到所需溫度的熱媒,供給熱站18;蒸汽凝結成為凝水輸送到蒸發器繼續進行循環蒸發。
熱站18可繼續為用戶供暖或為電站輸送熱能。
以上所述僅為本實用新型的較佳實施例而已,並不用以限制本實用新型,凡在本實用新型的精神和原則之內,所作的任何修改、等同替換、改進等,均應包含在本實用新型的保護範圍之內。