射出成型機及其注射螺杆的製作方法
2023-06-02 00:14:46 1
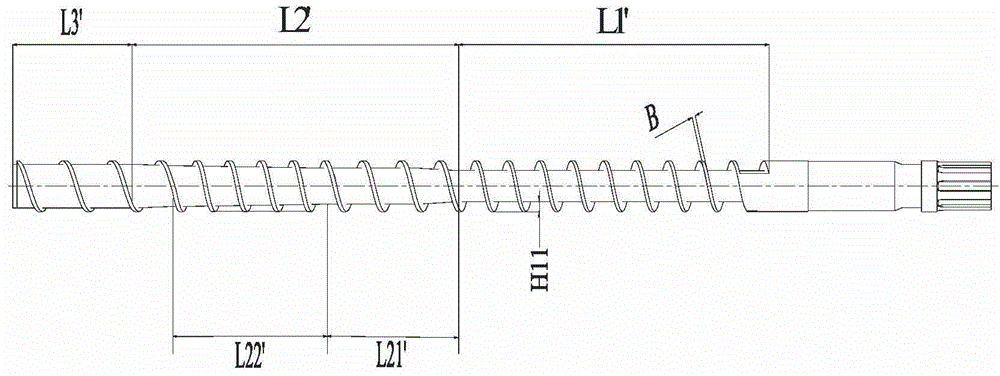
本發明涉及成型設備,尤其涉及一種射出成型機及其注射螺杆。
背景技術:
目前,常用的注射螺杆為傳統的三段式單螺紋螺杆,通用型變距螺杆,屏障型高混煉螺杆,分離型雙螺紋螺杆。
如圖1所示,其為傳統的三段式單螺紋螺杆。該三段式單螺紋螺杆包括螺紋部分和聯接部分,螺紋部分包括進料段L1'、壓縮段L2'和均化段L3'。進料段L1'由深為H11的平直牙底外螺紋構成,壓縮段L2由傾斜牙底的外螺紋構成,均化段L3'由深為H12的平直牙底外螺紋構成。其工作原理是:塑料原料通過料筒入口進入進料段L1',螺杆受馬達驅動旋轉,使原料由螺旋輸送。輸送過程中受料筒壁預熱,經壓縮段L2'因牙底變淺影響而受到強烈擠壓塑化(註:不同的塑料受到不同的壓縮比限制,壓縮比等於H11/H12)。塑化的塑料熔體進入均化段進一步熔融。為了保證產量需要增大H12和縮短均化段L3',這往往導致熔融塑化不徹底而含有未熔融的固相,削弱了均化段的職能。尤其在螺杆提高轉速之後更加明顯。為了充份熔融和提高混合效果,必須減小H12和增大均化段L3',但其結果剪切速率增大,熔體溫升提高,產量減小和能量消耗增大。高溫的熔體對於熱敏性塑料有可能造成熱分解。所以傳統的三段式單螺紋螺杆,塑化效果較差,為提高塑化效果會劇烈降低塑化效率。
如圖2所示為通用型變距螺杆。變距螺杆在壓縮段L2'起始和收尾採用了螺紋牙變距結構,包括第一牙距變化段L21'和第二牙距變化段L22'。這種螺杆均化段L3'牙距以熔體輸送最佳升角(接近30°)確定,通常是進料段L1'牙距的1.5倍。變化的牙距解決了兩個問題:相同的壓縮比可以把均化段L3'深度做小,增大剪切提高塑化效果,同時把進料段L1'深度H11做大,能提高塑化效率;當熔料自進料段L1'末進入壓縮段,受變距作用會減小壓縮比例,使熔料有一個平緩的壓縮切換點,壓縮過程也可以通過變距平緩吸收剪切熱能,防止溫升。所以變距螺杆比傳統螺杆提高了塑化效果的 同時也可以提高塑化效率。但變距螺杆減小了均化段的有效牙數,實踐中對一些難熔或混色要求較高生產情況不能滿足。
如圖3所示,其為屏障型高混煉螺杆。該屏障型高混煉螺杆與傳統的三段式單螺紋螺杆相比,多了一個屏障段L4'。在L4的外徑上交替開出數量相等的進、出料槽。按螺杆轉動方向,進入出料槽前面的凸稜比螺杆外半徑小一徑向間隙值,這是每一對進、出料槽的唯一通道。這條凸稜稱為屏障稜。當物料從壓縮段進入均化段後,含有未熔融固體顆粒的熔料流到達屏障型混煉段時,被分成若干股料流進入屏障段的進料槽,熔料和粒度小於屏障間隙的固態小顆粒料越過屏障稜進入出料槽。未塑化的小顆粒料在屏障間隙受到了剪切作用,大量的機械能轉變為熱能,使小顆粒料熔融。屏障型螺杆解決了普通螺杆塑化品質難提高的問題,其熔體溫度相對均勻,相同產量下熔體質量高。但是屏障型螺杆產量與屏障間隙值的3次方成正比,因此小的屏障間隙值也使螺杆產量降低。
如圖4所示為屏障螺杆的一個變種,屏障段L4為三角槽型的混煉段,進料槽寬度從寬變窄,出料槽從窄變寬。對進入的物料起壓縮作用,越過屏障稜之後起膨脹作用,有利於混合和塑化。此變種還增加了由螺旋短齒構成的混合段。這種屏障螺杆不僅提高了熔融品質,還提高了對色粉的混合能力。但是這種螺杆也受屏障間隙值限制,產量相對受限。
如圖5所示為屏障螺杆的另一個變種,在傳統三段式螺杆均化段L3增加了一段副螺紋,副螺紋與主螺紋有屏障間隙,作用及優缺點與進、出料槽屏障相同。
如圖6所示為目前應用廣泛的分離型雙螺紋螺杆。雙螺紋螺杆主要在壓縮段自進料段L1'末設置一條起屏障作用的副螺紋,將熔融段的螺槽分開為固相槽和液相槽。設置的副螺紋外徑小於主螺紋,副螺紋與料筒內壁有間隙。當進料段L1'末端的料筒內壁開始出現熔膜,螺稜推進面也開始出現熔料時,固體床迫使熔池中的熔料通過副螺紋頂端的間隙進入液相槽。雙螺紋螺杆因為固液兩相分開,已熔融的熔體及時從固相槽通過副螺稜間隙流入液相槽,新熔化的熔體和未完全塑化的小顆粒在副螺稜間隙中受到剪切作用而塑化。固相槽末端被封死,液相槽中沒有殘留固相,因而塑化品質比普通螺杆高、穩定。但是雙螺紋螺杆固相槽的寬度越來越窄,固相與料筒壁接觸面 越來越來越小,即熱交換面積越來越小,不利於熔融;而液相槽的寬度越來越寬,熔料反而與機筒內壁的熱交換面積越來越大,不利於降低熔料溫度。所以一些對溫度敏感材料如PC、PVC等適用性不好。
以上六種不同結構的注射螺杆,雖然可以在提高塑化品質或者提高塑化效率或者提高混合能力方面有片面的優勢,但均未完整、很好地解決生產效率、剪切塑化效果、混色能力、防止溫升缺陷的綜合特性優勢。
技術實現要素:
本發明提出一種射出成型機及其注射螺杆,解決現有技術中因傳統的單螺紋注射螺杆及常用的幾款或變距或屏障或分離型螺杆不能完整解決生產效率、塑化效果及溫升等性能,以及不能獲得優良綜合性能的問題,使得本發明射出成形機的注射螺杆具有更廣泛的適應性。
為解決上述技術問題,本發明提出一種注射螺杆,用以將塑料在射出成型機中塑化為熔體的部件,所述注射螺杆包括相互連接的螺紋部分和聯接部分,所述螺紋部分上設有外螺紋,所述螺紋部分上的外螺紋牙距和外螺紋牙寬保持不變,所述螺紋部分沿所述外螺紋螺旋方向依次包括進料段、壓縮段和均化段,所述均化段上的外螺紋槽設有一雙螺旋結構,所述雙螺旋結構由螺旋槽和螺旋波峰組成,其中,所述螺旋波峰由所述螺旋槽切割所述外螺紋槽的底面形成。
進一步地,所述螺旋槽的寬度為所述螺杆直徑的0.5~0.7倍。
進一步地,所述螺旋波峰的導程大於所述螺杆直徑,所述螺旋槽的底側邊呈弧形圓角,所述螺旋槽的螺旋升角為30°±10°。
進一步地,所述螺旋波峰的導程為所述螺杆直徑的1.814倍。
進一步地,所述螺旋槽的深度符合公式:
其中,所述螺旋槽的深度為H33,所述螺杆直徑為D。
所述螺旋波峰至所述外螺紋的牙頂距離符合公式:
其中,所述螺旋波峰至所述外螺紋的牙頂距離為H32。
進一步地,所述均化段的長度為所述螺杆直徑的5~7倍,所述螺旋槽分布在所述均化段的長度為所述螺杆直徑的4~6倍。
進一步地,所述均化段的開始端位置包括第一螺旋波峰漸變段,所述均 化段的結尾端位置包括第二螺旋波峰漸變段。
進一步地,所述螺紋部分上的外螺紋牙距大致與螺杆直徑相等,所述螺紋部分上的外螺紋牙寬大致與所述螺杆直徑的0.1倍相等。
進一步地,所述進料段的外螺紋牙底的深度保持不變。
本發明還提供一種射出成型機,包括如上所述的注射螺杆。
與現有技術相比,本發明至少具有如下有益效果:本發明射出成型機的注射螺杆在熔膠時均化段的雙螺旋結構不僅對塑膠熔體產生均勻混沌的混合,還能使熔體與料筒的熱交換更充份,產生均勻溫度的高質熔體。通過合理確定螺旋波峰與料筒間隙,合理確定螺旋槽的深度和螺旋升角,可以實現以較低的剪切量,較高的塑化效率,充份塑化原料。防止熔膠過程中容易產生的溫度非受控升高、螺杆打滑、吃料慢等缺陷。
附圖說明
圖1是現有技術的三段式單螺紋普通螺杆結構示意圖。
圖2是現有技術的變距螺杆結構示意圖。
圖3是現有技術的屏障型高混煉螺杆結構示意圖。
圖4是現有技術的屏障型高混煉螺杆一種變化結構示意圖。
圖5是現有技術的屏障型高混煉螺杆另一種變化結構示意圖。
圖6是現有技術的分離型雙螺紋螺杆結構示意圖。
圖7是本發明射出成型機的結構示意圖。
圖8是本發明射出成型機射膠部件的結構示意圖。
圖9是本發明實施例中注射螺杆的結構示意圖。
圖10是本發明實施例中射膠部件的剖視圖。
圖11是本發明實施例中注射螺杆分段及均化段沿柱面展開結構示意圖。
圖12是本發明實施例中注射螺杆各段深度變化示意圖。
其中,附圖標記說明如下:100、射出成型機;1、射膠部件;2、料管組;3、注射螺杆;4、螺桿頭;5、止逆環;6、止推墊圈;7、料筒;8、驅動馬達;9、傳動部件;10、聯接鍵;11、聯接槽;31、螺紋部分;32、聯接部分;311、外螺紋;312、進料段;313、壓縮段;314、均化段;3141、螺旋槽;3142、螺旋波峰。
具體實施方式
為了進一步說明本發明的原理和結構,現結合附圖對本發明的優選實施例進行詳細說明。
參閱圖7至圖12,本發明提供一種射出成型機100,其包括一射膠部件1,該射膠部件1包括一料管組2,該料管組2包括一注射螺杆3,該注射螺杆3用以將塑料在射出成型機100中塑化為熔體。注射螺杆3的一端通過傳動部件9與驅動馬達8連接,另一端安裝有止逆閥三小件,止逆閥三小件包括螺桿頭4、止逆環5和止推墊圈6。
注射螺杆3包括相互連接的螺紋部分31和聯接部分32。該聯接部分32包括聯接鍵10、聯接槽11、軸頸(圖中未標出)和定位安裝孔(圖中未標出)。
螺紋部分31為注射螺杆3的主體部分,其上設有外螺紋311,外螺紋牙距P和外螺紋牙寬B保持不變,外螺紋311為右旋或左旋的螺紋,其中,外螺紋牙距P大致與螺杆直徑D相等,外螺紋牙寬B大致等於螺杆直徑的0.1倍。
螺紋部分31包括進料段312、壓縮段313和均化段314。
進料段長度L1由注射螺杆長徑比I決定。注射螺杆長徑比I由射出成型機100的機器參數決定,通常注射螺杆長徑比I在18~25範圍之間。進料段長度L1符合公式:L1=(I-(11~13))×D。通常情況下,進料段長度L1在7~12倍螺杆直徑D之間,大長徑比的注射螺杆的進料段長度L1取大值;小長徑比的注射螺杆的進料段長度L1取小值。
進料段312的外螺紋牙底的深度H1保持不變。優選地,進料段312的外螺紋牙底呈平直牙底,即平面的牙底結構。
對通用型注射螺杆,壓縮段長度L2也是由注射螺杆的長徑比I決定的,具體符合公式:L2=(I-(5~7))×D-L1。
壓縮段313的外螺紋牙底的深度呈逐漸變淺的結構,其中,壓縮段313的外螺紋牙底的初始深度與進料段312的外螺紋牙底的深度H1相同,壓縮段313的外螺紋牙底的結尾深度H3符合公式:
<![CDATA[ H 3 5 × D 83 ]]>
其中,進料段312的外螺紋牙底的深度H1與壓縮段313的外螺紋牙底的 結尾深度H3的比值為壓縮比i。一般來說,對於通用型注射螺杆,壓縮比i大致等於2.5。
均化段長度L3是螺杆直徑D的5~7倍,均化段314的起始端和末端的牙底深度與壓縮段313的外螺紋牙底的結尾深度H3相同。均化段314的中部是大導程的雙螺旋結構,該雙螺旋結構由螺旋槽3141和螺旋波峰3142組成,本實施例中,螺旋槽3141為雙頭螺旋槽,螺旋波峰3142為雙螺旋波峰,螺旋槽3141被外螺紋牙分隔為多段。其中,螺旋波峰3142由螺旋槽3141切割外螺紋槽的底面形成。在本實施例中,螺旋槽3141起始於壓縮段313上的結尾位置,螺旋槽開始段長度L21大致為螺杆直徑D的0.25倍。螺旋槽3141的長度為螺杆直徑D的4~6倍,螺旋槽3141的寬度W是螺杆直徑D的0.5~0.7倍。螺旋槽3141的深度H33符合公式:
<![CDATA[ H 33 9 × D 150 . ]]>
螺旋波峰3142至外螺紋311的牙頂距離H32符合公式:
參見圖11,圖11是本發明實施例中注射螺杆分段及均化段沿柱面展開結構示意圖。在均化段314展開圖中,螺旋槽3141為沿圓周分布的雙頭螺旋,其分布位置決定了螺旋波峰寬度b大致等於螺杆直徑D的0.25~0.5倍。螺旋槽3141的螺旋升角為30°±10°,從熔體得到最大輸送能力考慮,螺旋槽3141的螺旋升角取30°。
進一步地,均化段314的起始端位置包括第一螺旋波峰漸變段L34,均化段314的末端位置包括第二螺旋波峰漸變段L32,其中,第一螺旋波峰漸變段L34的波峰呈逐漸變高的結構,第二螺旋波峰漸變段L32的波峰呈逐漸變低的結構。在本實施例中,均化段314的末端還包括一個結尾段L31,該結尾段L31上雙螺旋結構已消失,且結尾段L31的牙底深度與壓縮段313的外螺紋牙底的結尾深度H3相同。同樣地,螺旋槽3141的起始和收尾深度也是漸變的,螺旋槽3141底側邊呈弧形圓角,起到平滑過渡的作用。這種結構有助於熔料順暢流動與壓力傳遞,也提升塑化效率,防止熔體滯留降解。
請參見圖9和圖10,本發明實施例中的射出成型機100工作時,當驅動馬達8經傳動部件9驅動注射螺杆3旋轉,塑料原料自注射螺杆3的進料段 312入外螺紋311的螺紋槽,受螺紋的旋轉輸送作用,向注射螺杆3的螺桿頭4移動。在這個過程中,塑料原料受料管傳遞熱量預熱。塑料原料到達壓縮段313,受該段牙底深度的變化由壓縮段313的外螺紋牙底的初始深度H1漸變為壓縮段313的外螺紋牙底的結尾深度H3,及與料筒7的筒壁旋轉摩擦的影響,受到強列壓縮和剪切,釋放大量熱能,開始熔化原料。原料經壓縮段313轉化成粘度不均勻熔體,甚至高轉速下會有固相顆粒進入均化段314。均化段螺旋槽對進入均化段的熔體產生如下有益效果:
第一,是大導程螺旋槽以最優的螺旋升角和較深的通道快速輸送熔體。
第二,是所有熔體必須越過螺旋波峰間隙H32,獲得合適的剪切,熔化未熔固相顆粒。
第三,是越過螺旋波峰的熔體,再次進入較深的螺旋槽,在螺旋槽內產生沿深度方向的渦卷流。經過幾段螺旋波峰和螺旋槽的反覆,熔體與料筒壁的接觸換熱更充份和均勻,熔體也得到渾沌的混合,產生均勻溫度的高質熔體。之後,高質熔體經過安裝於注射螺杆端部的止推墊圈、止逆環、螺桿頭三小件組成的閥門進入料筒熔池,為下一次注射做好準備。
此外,當本發明射出成型機的注射螺杆專門應用於某一類塑料時,可以調整螺旋波峰高度、螺旋波峰的寬度和均化段的長度,使均化段提供最適於這一類塑料的剪切量和塑化效率。例如,當作為尼龍專用注射螺杆時,可以將螺旋波峰高度做到近似屏障螺杆的屏障間隙值,以獲得充分的塑化效果。
本發明射出成型機及其注射螺杆具有如下技術效果:
1、通過在注射螺杆的均化段加設大導程螺旋槽以最優的螺旋升角和較深的通道快速輸送熔體,減少熔膠駐留時間,提高塑化能力。
2、在均化段的螺旋波峰結構,使所有熔體必須越過波峰間隙,獲得合適的剪切,充份熔化未熔固相顆粒。
3、在均化段有數段螺旋槽與螺旋波峰,越過螺旋波峰的熔體,再次進入較深的螺旋槽,在螺旋槽內產生沿深度方向的渦卷流。經過幾段波峰螺槽反覆,熔體與料筒壁的接觸換熱更充份和均勻,熔體也得到渾沌的混合,產生均勻溫度的高質熔體。
4、能夠實現塑化能力與熔體質量雙提高,避免了傳統螺杆中塑化品質、塑化效率與螺杆通用性三項指標不可兼得的缺陷,有效克服熔膠過程中容易 產生的溫度非受控升高、螺杆打滑、吃料慢等缺點。
以上僅為本發明的較佳可行實施例,並非限制本發明的保護範圍,凡運用本發明說明書及附圖內容所作出的等效結構變化,均包含在本發明的保護範圍內。