一種提高鋼液中鎂元素收得率的方法與流程
2023-06-01 21:06:17 1
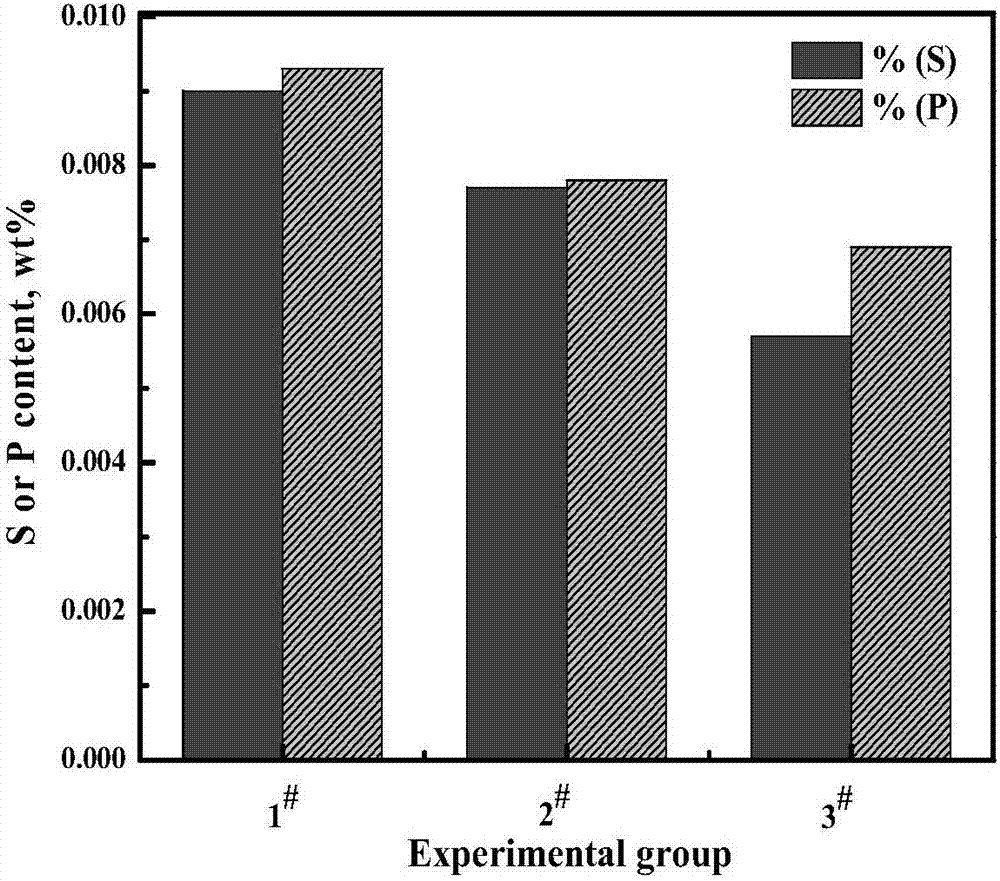
本發明屬於冶金技術領域,涉及一種高鎂合金結構鋼,特別涉及一種提高鋼液中鎂元素收得率的方法。
背景技術:
鎂元素對去除鋼液中的夾雜物具有顯著的作用,主要是由於鎂與硫、氧都有很強的親合力,易形成含鎂的夾雜物,有助於加速夾雜物的上浮,改善鋼的潔淨度;其次鎂可以對夾雜物變性,使夾雜物無害化;此外鎂還可以淨化晶界、改善鋼的晶界強度從而提高鋼的性能。
由於金屬鎂的蒸氣壓很高,且在煉鋼溫度下鎂的反應十分劇烈,至今尚未開發出比較好的向鋼中加鎂的工藝手段。目前,向鋼液中加入的鎂量都比較少且收得率都比較低,已有的加鎂工藝手段主要有以下幾種。
(1)衝入法
衝入法的操作最為簡單,通常是採用塊狀含鎂鐵合金(一般為fesimg合金,即fesi合金中含有3~5wt%的mg)。
在初煉爐出鋼前加在鋼包內,出鋼過程中利用鋼水衝擊將含鎂鐵合金混衝入鋼水。目前,人們所嘗試的鋼中加鎂處理通常採用這一方法,但是這種方法並不成功,存在的主要問題是鎂劇烈燃燒,造成出鋼過程白光沖天,致使出鋼過程無法操作,浪費嚴重,鎂的吸收率極低且很不穩定,因此衝入法的實際效果不佳。
(2)餵線法
餵線法是將密度較小,容易氧化的精煉劑做成線材,用餵線機將其投入鋼水深處,對鋼水進行爐外精煉的一種方法,該方法在目前的球鐵生產中已有應用。使用餵線法加鎂,採用的合金線可以是鎂及鎂合金線也可以是各種含鎂包芯線,芯劑可以是稀土鎂合金、高鎂合金、鈍化鎂粒等。方法存在的主要問題是在餵線過程中,鎂提前熔化汽化,造成鎂大量的以蒸氣形式外溢,致使鋼水劇烈翻滾,輕則與空氣接觸造成二次氧化,重則導致鋼水大翻事故,同樣無法在鋼水鎂處理中得到應用,較早出現的壓入法也存在同樣問題。
(3)鎂合金加入法
目前市面上銷售的鎂合金一般鎂含量較高(15%以上)。加入到鋼液中以後會發生劇烈的反應,操作的安全性低,鋼水的翻滾劇烈甚至發生噴濺、爆炸。因此,使用目前市面上銷售的金屬鎂,勢必要降低合金的原始投入量,同樣無法有效提高鋼液中的鎂含量。
鋼水鎂處理工藝的核心問題是,如何保證鋼水對加入的鎂具有較高的吸收率,即提高鎂在鋼液中的收得率,降低鎂在鋼液中的燒損量。這樣就不會造成鎂以蒸氣的形式大量溢出和燒損,鋼水也就不會劇烈翻滾,既保障了操作安全又保證了處理效果,還不會造成浪費。為達到高的吸收率,就必須保證鎂蒸氣與鋼水保持較長的接觸時間,因此鎂的氣化過程應該被控制在鋼水的深處,這樣鎂蒸氣氣泡在上升的過程中能夠與鋼水充分接觸反應,最理想狀況是在鎂蒸氣氣泡溢出鋼水之前,已經與鋼中氧及夾雜物完全反應而形成新的夾雜物。因此,如何將鎂元素成功加入到鋼液中並提高其在鋼液中的收得率是至關重要的關鍵技術,也是亟待解決的技術難題。
技術實現要素:
根據目前鎂元素在鋼液中收得率低且加入技術所存在的缺點和不足,本發明通過使用加壓感應爐裝置,以fe-ni-mg的合金形式將易揮發元素鎂加入鋼液中,從而增加鎂與鋼液的接觸時間。
為實現上述目的,本發明的技術解決方案是提供一種提高鋼液中鎂元素收得率的方法,該方法包括以下步驟:
a.將適量鐵粉與鎳粉按質量比1:4~1:1混合,再與鎂粉混合,並壓鑄成型,獲得fe-ni-mg合金,其中鎂在合金中的質量百分比為4~6%;
b.依據目標鋼種的元素成分,計算所需原料的重量,配製冶煉原料,將冶煉原料裝入加壓感應爐的坩堝中;其中冶煉原料包括工業純鐵、工業矽、金屬錳、金屬鉻、金屬鉬和釩鐵;原料的具體成分如表1所示
c.啟動外部抽氣系統,對系統進行抽真空;
d.待冶煉原料融化後通入氬氣,加壓至0.5~2mpa,然後將步驟a製得的fe-ni-mg合金由料倉加料口分批次加入,每次加入不超過25g;每噸鋼液fe-ni-mg合金的加入量為13~16kg;
e.保壓30~40min後減壓出爐。待鋼樣完全冷卻後,對其成分進行檢測。
表1實驗原料成分/wt,%
本發明的提高鋼液中鎂元素收得率的方法,有益效果為:
(1)採用fe-ni-mg合金的加入形式,有效地節約了成本,同時也能使合金較好地進入鋼液深處,以便鎂蒸氣氣泡在上升的過程中能夠與鋼水充分接觸反應,可有效提高鎂在鋼液中的收得率。
(2)利用加壓感應爐加壓有效地控制了鋼液中的鎂含量,提高了鎂在鋼液中的收得率,使整個操作過程能夠更加安全平緩的進行,所製備的高鎂合金結構鋼晶粒細化,網狀碳化物減少,在降低成本的情況下提高了鋼的耐磨性、強度韌性及疲勞壽命等性能。
附圖說明
圖1是氧含量隨時間變化規律圖。
圖2是各爐鋼硫、磷含量對比圖。
具體實施方式
為了使本領域技術人員更好地理解本發明的技術方案能予以實施,下面結合具體實施例1~3對本發明進一步說明,但所舉實施例不作為對本發明的限定。本實驗中所選鋼種為合金結構鋼(30crni2mova),屬於低合金中碳結構鋼,是一種亞共析鋼,具體成分如表2所示。
表2實驗鋼種成分/wt,%
實施例1
一種提高鋼液中鎂元素收得率的方法包括以下步驟:
a.首先將鐵粉與鎳粉按1:4與鎂粉混合,並壓鑄成小塊狀,其中鎂佔合金的6%。
b.將冶煉原料裝入加壓感應爐的mgo坩堝中,原料包括工業純鐵、工業矽、金屬錳、金屬鉻、金屬鉬和釩鐵;
c.啟動外部抽氣系統,對系統進行抽真空,真空度控制在10pa以內;
d.待冶煉原料全部融化後開始通入氬氣,加壓至0.5mpa,然後將a中事先處理好的fe-ni-mg合金由料倉加料口分批次加入,每次加入不超過25g,每噸鋼液fe-ni-mg合金的加入量為13kg;
e.保壓30min後減壓出爐,待鋼樣1#完全冷卻後,對其成分進行檢測,結果如表3所示;
f.將剩餘的坯料重新加熱到900℃,保溫1h,隨爐冷卻到600℃,再將坯料加熱到1050℃,保溫3h,取出用油冷卻至室溫後重新加熱到350℃,保溫3h,後隨爐冷卻至室溫。
實施例2
一種提高鋼液中鎂元素收得率的方法包括以下步驟:
a.首先將鐵粉與鎳粉按1:1與鎂粉混合,並壓鑄成小塊狀,其中鎂佔合金的4%。
b.將冶煉原料裝入加壓感應爐的mgo坩堝中,原料包括工業純鐵、工業矽、金屬錳、金屬鉻、金屬鉬和釩鐵;
c.啟動外部抽氣系統,對系統進行抽真空,真空度控制在10pa以內,然後通入氬氣加壓至1.0mpa;
d.待冶煉原料融化後通入氬氣,加壓至1.0mpa,然後將a中事先處理好的fe-ni-mg合金由料倉加料口分批次加入,每次加入不超過25g,每噸鋼液fe-ni-mg合金的加入量為16kg;
e.保壓40min後減壓出爐,待鋼樣2#完全冷卻後,對其成分進行檢測,結果如表3所示;
f.將剩餘的坯料重新加熱到800℃,保溫2h,隨爐冷卻到500℃,再將坯料加熱到950℃,保溫2h,取出用油冷卻至室溫後重新加熱到450℃,保溫1h,後隨爐冷卻至室溫。
實施例3
一種提高鋼液中鎂元素收得率的方法包括以下步驟:
a.將鐵粉與鎳粉按1:1與鎂粉混合,並壓鑄成小塊狀,其中鎂佔合金的4%。
b.將冶煉原料裝入加壓感應爐的mgo坩堝中,原料包括工業純鐵、工業矽、金屬錳、金屬鉻、金屬鉬和釩鐵;
c.啟動外部抽氣系統,對系統進行抽真空,真空度控制在10pa以內,然後通入氬氣加壓至2.0mpa;
d.待冶煉原料融化後通入氬氣,加壓至2.0mpa,然後將a中事先處理好的fe-ni-mg合金由料倉加料口分批次加入,每次加入不超過25g,每噸鋼液fe-ni-mg合金的加入量為16kg;
e.保壓40min後減壓出爐,待鋼樣3#完全冷卻後,對其成分進行檢測,結果如表3所示;
f.將剩餘的坯料重新加熱到700℃,保溫4h,隨爐冷卻到400℃,再將坯料加熱到800℃,保溫1h,取出用油冷卻至室溫後重新加熱到200℃,保溫2h,後隨爐冷卻至室溫。
表3實驗鋼成分分析/wt,%
由表3可以看出,三個爐次的鋼樣在2.0mpa以內隨著壓力的增大鎂元素在鋼液中的收得率會顯著提高,通過加壓冶煉和凝固,有效地控制了鋼中的鎂含量,提高其利用率,進一步發揮了鎂元素淨化鋼液、夾雜物變性和微合金化作用。
表4實施例性能測試結果
對各組實驗的過程樣進行氧含量分析,得到氧含量隨取樣時間變化規律如圖1,發現3組鋼起始氧含量相近,約為0.0070%,隨著取樣時間的延長,3組中氧含量均呈現下降趨勢。2#、3#的氧含量要明顯低於3#組,且氧含量趨於穩定的時間要早於1#組。這是由於2#、3#組採用鎂處理,鎂的脫氧能力要遠遠優於鋁,可以使2#、3#組的氧含量在短時間內降到很低值,且鎂含量越高,脫氧效果越好。
分析1#、2#、3#實驗組中硫、磷的含量,如圖2所示。發現向鋼中加入鎂具有一定的脫硫、脫磷效果,且鎂含量越高,脫磷、脫硫的效果越好。
對實施例製備的30crni2mova鋼試樣進行性能測試,測試結果如表4所示,由於鋼中加入了鎂,鋼的硬度、耐磨性、衝擊韌性、以及抗拉強度等性能得到了明顯的改善。
綜上所述,以上實施例僅用以說明本發明的技術方案,而非對其限制,本發明的保護範圍不限於此,任何熟悉本技術領域的技術人員在本發明披露的技術範圍內,可顯而易見地得到的技術方案的簡單變化或等效替換,均屬於本發明的保護範圍。