一種電解分離高碳鋼中夾雜物的原貌分析方法與流程
2023-05-30 00:50:21 5
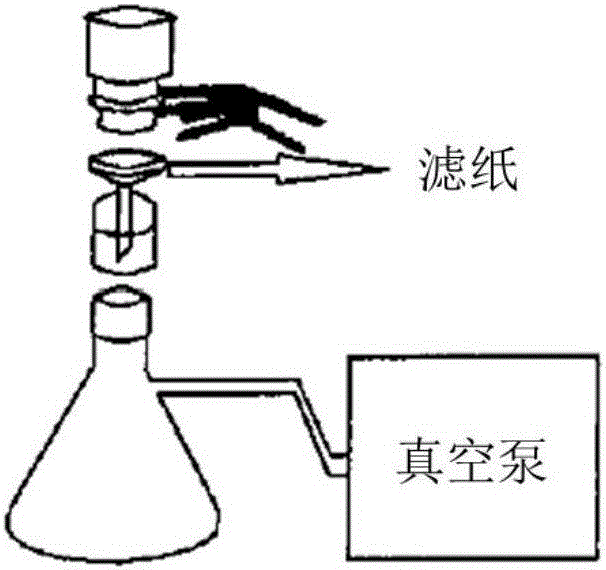
本發明屬於鋼中夾雜物電解分離及三維形貌觀察領域,具體涉及一種電解分離高碳鋼中夾雜物的原貌分析方法。
背景技術:
隨著我國各高精尖行業的發展,例如航空航天、高速鐵路等,所需高碳鋼(如軸承鋼、齒輪鋼、彈簧鋼等)的質量要求也越來越高。以高鐵為例,目前300km/h時速以上的高鐵所用軸承還完全依賴於進口,國內軸承鋼產量雖大,但質量不能滿足高要求,還需進一步對國內軸承鋼生產工藝進行優化。
影響鋼材質量的一個重要因素是鋼中夾雜物。因此,採用合適的工藝手段,最大程度的去除鋼中各類夾雜物,實現鋼水潔淨化對冶金行業生產高品質鋼至關重要。通過對電解手段對鋼中夾雜物進行原貌分析,掌握鋼中夾雜物的三維形貌、性質和生成條件,得到去除鋼中夾雜物的相應措施,成為實現鋼中夾雜物的高效根本去除的重要手段。
目前,使用電解法對鋼中夾雜物進行原貌觀察的方法主要有兩種,一種使用有機電解液電解,一種使用無機電解液電解。使用無機電解液電解容易破壞部分類型夾雜物的原始形貌,不利於鋼中夾雜物的精確提取;然而使用有機電解液電解可以完整的保留鋼中全部夾雜物的原始形貌,但是對於高碳鋼使用電解法進行夾雜物原貌分析時,由於鋼中碳含量高,電解過程中不可避免產生碳化物,碳化物會隨著電解的進行與夾雜物一起進入電解液中,而不會在電解中被溶解。且碳化物通常顆粒較大,使用抽濾的手段處理電解產物時不易被抽濾掉,與尺寸較小的夾雜物混在一起,極大的影響了夾雜物的觀測和提取。
現有技術中有申請號為CN201510239355.0的一種高碳鋼夾雜物的提取及分析方法,該方法仍採用原有的有機溶液電解法,無法從根本上消除碳化物對高碳鋼電解過程中帶來影響,極大影響電解高碳鋼中夾雜物的分離效率以及有效提取。而本方法提供了一種全新的方法,克服了電解後高碳鋼中大量碳化物對夾雜物觀察的影響,極大的降低了對高碳鋼中夾雜物原貌分析的難度與工作量,通過在電解之前對鋼樣的預處理,嚴格控制鋼中碳化物的尺寸,使大部分碳化物在抽濾過程中與夾雜物分離,同時嚴格控制通電電流、電解時間及鋼樣尺寸,實現較精確的定量電解,並於抽濾時採用不同孔徑的濾紙,對夾雜物按尺寸進行分級抽濾,最終實現高碳鋼中各類夾雜物的有效電解分離,達到易於觀察的目的。並且該方法簡單可靠,效率高,縮短了鋼樣電解時間,夾雜物損失少,能夠有效的提取高碳鋼中各類夾雜物,最終對高碳鋼中各類夾雜物形貌進行有效觀察和準確判斷,為鋼中夾雜物去除工藝的改進與優化提供指導。
技術實現要素:
為了解決上述問題,本發明提供提供一種分離高碳鋼夾雜物簡單可靠、損失少,碳化物對夾雜物的觀察及分離影響小的夾雜物原貌分析法,所述方法先電解之前在加熱爐中對加工好的待電解鋼樣進行預處理,控制鋼中碳化物的尺寸,使大部分碳化物在抽濾過程中與夾雜物分離,同時控制通電電流、電解時間及鋼樣尺寸,以進行精確的定量電解,並於抽濾時採用不同孔徑的濾紙,對夾雜物按尺寸進行分級抽濾,最終實現高碳鋼中各類夾雜物的電解分離,完成原貌分析;
進一步地,所述方法包括:
S1:將鋼樣加工至要求尺寸後,然後將加工好的待電解鋼樣置於加熱爐中進行預處理,預處理工藝為改良後的球化退火工藝;
S2:連接電解裝置,其中所使用電源為直流電源,接線連通後,電解過程採用恆壓控制模式;
S3:電解結束後將鋼樣、鋼樣與導線連接段、陰極等進行衝洗,所有衝洗液及電解液全部收集,倒入抽濾瓶進行抽濾,抽濾首先使用孔徑2μm的聚碳酸酯濾膜,抽濾重複進行2-4遍,再使用孔徑0.45μm的聚碳酸酯濾膜將第一次抽濾後得到的濾液再次重複抽濾2-4遍;
S4:將兩次抽濾所用的不同孔徑濾膜置於乾燥箱中烘乾,然後將烘乾後濾膜使用導電膠粘於導電基體上;
S5:對固定在導電基體上的濾膜進行噴金或噴碳導電處理,使用掃描電鏡和能譜分析手段對濾膜上分離出的夾雜物進行三維形貌的觀察;
進一步地,S1中所述改良後的球化退火工藝為:首先將置於爐內鋼樣加熱至780℃-820℃,保溫3h-5h,然後隨爐以30℃/h緩冷至680℃-720℃,保溫2h-4h,再以30℃/h緩冷至650℃,取出空冷至室溫,並對鋼樣待電解截面進行打磨;
進一步地,所述S1具體包括:
S11:首先將鋼樣加工至φ(5-10)mm×(30-50)mm的圓棒或(5-20)mm×(5-20)mm×(5-20)mm的方塊作為待電解鋼樣;
S12:將加工好的待電解鋼樣置於加熱爐中進行預處理,處理工藝為改良後的球化退火工藝;
S13:對處理後的待電解鋼樣的待電解截面進行打磨,採用金相制樣的方法,分別採用200#、400#和600#砂紙將鋼樣待電解截面進行打磨均勻;
進一步地,所述S2具體包括:
S21:將陰極浸入電解液,電解液為AA溶液,所述為AA溶液為無水甲醇/乙醇-(5~15)%乙醯丙酮-(0.5~1.5)%四甲基氯化銨,所述陰極材質為鋼板,陰極形狀為閉合圈,陰極通過金屬導線連接直流電源負極;
S22:將待電解鋼樣四周使用絕緣膠帶密封,並通過金屬導線連接直流電源正極,僅留待電解截面裸露,電解時浸入電解液;
S23:接線連通後,電解過程採用恆壓控制模式,電壓選取
120mV-160mV範圍內固定值控制,並保持電流控制在0.04A-0.07A範圍內,電解時間2~5h;
進一步地,所述S3包括:
S31:將電解結束後的鋼樣、鋼樣與導線的連接段、陰極進行衝洗,衝洗所用試劑為無水甲醇/乙醇有機溶液,
S32:將所有衝洗液及電解液全部收集,倒入抽濾瓶進行抽濾,抽濾首先使用孔徑2μm的聚碳酸酯濾膜,抽濾重複進行2-4遍,再使用孔徑0.45μm的聚碳酸酯濾膜將第一次抽濾後得到的濾液再次重複抽濾2-4遍;
進一步地,所述S4具體為將兩次抽濾所用的不同孔徑濾膜置於乾燥箱中烘乾,乾燥箱溫度控制在150±2℃,乾燥時間1h-3h,然後將烘乾後濾膜使用導電膠粘於導電基體上,所述導電基體材質為金屬材質,該金屬材質為鋼塊,銅板或鋁板;
進一步地,所述高碳鋼為鋼中碳含量在0.5wt%以上的鋼種;
進一步地,所述高碳鋼包括高碳鉻軸承鋼、彈簧鋼、齒輪鋼和硬線鋼;
進一步地,S2所述電解過程中電壓選取(120-160)mV範圍內固定值控制,並保持電流控制在(0.04-0.07)A範圍內,電解時間2~5h;
本發明的有益效果如下:
1)提供了一種有效提取高碳鋼中夾雜物的原貌分析方法;
2)針對高碳鋼,通過熱處理工藝從電解的源頭控制高碳鋼中碳化物的尺寸,極大的減輕了電解時碳化物對夾雜物觀測帶來的影響,降低了夾雜物觀察難度;
3)提高了電解效率,將電解時間縮短至2~5h,提供了高效獲取與分離高碳鋼中夾雜物的原貌分析方法;
4)精確控制鋼樣被電解尺寸,通電參數(電流和電壓)以及通電時間等條件,提高電解精度,並使用不同孔徑的濾膜分級抽濾,減少操作過程中夾雜物損失,實現高碳鋼中夾雜物全尺寸分離與提取。
附圖說明
圖1為本發明所述電解裝置連接示意圖;
圖2為本發明所述抽濾裝置示意圖;
圖3為本發明所述實施例1中電解後觀察到Al-O類夾雜物的顯微形貌圖;
圖4為本發明所述實施例1中電解後觀察到Al-O類夾雜物的能譜分析成分圖;
圖5為本發明所述實施例1中電解後觀察到尖晶石類夾雜物的顯微形貌圖;
圖6為本發明所述實施例1中電解後觀察到尖晶石類夾雜物的能譜分析成分圖;
圖7為本發明所述實施例1中電解後觀察到MnS類夾雜物的顯微形貌圖;
圖8為本發明所述實施例1中電解後觀察到MnS類夾雜物的能譜分析成分圖;
圖9為本發明所述實施例1中電解後觀察到Al-Si-O類夾雜物的顯微形貌圖;
圖10為本發明所述實施例1中電解後觀察到Al-Si-O類夾雜物的能譜分析成分圖;
圖11為本發明所述實施例1中電解後觀察到Ca-Mg-Al-Si-O類夾雜物的顯微形貌圖;
圖12為本發明所述實施例1中電解後觀察到Ca-Mg-Al-Si-O類夾雜物的能譜分析成分圖。
具體實施方式
為了使本發明的目的、技術方案及優點更加清楚明白,以下結合附圖及實施例,對本發明進行進一步詳細描述。應當理解,此處所描述的具體實施例僅僅用於解釋本發明,並不用於限定本發明。相反,本發明涵蓋任何由權利要求定義的在本發明的精髓和範圍上做的替代、修改、等效方法以及方案。進一步,為了使公眾對本發明有更好的了解,在下文對本發明的細節描述中,詳盡描述了一些特定的細節部分。對本領域技術人員來說沒有這些細節部分的描述也可以完全理解本發明。
下面結合附圖和具體實施例對本發明作進一步說明,但不作為對本發明的限定。下面為本發明的舉出最佳實施例:
如圖1-圖7所示,本發明提供一種電解分離高碳鋼中夾雜物的原貌分析方法,所述高碳鋼為鋼中碳含量在0.5%wt以上的鋼種,所述高碳鋼包括高碳鉻軸承鋼、彈簧鋼、齒輪鋼和硬線鋼,所述方法先電解之前在加熱爐中對加工好的待電解鋼樣進行預處理,控制鋼中碳化物的尺寸,使大部分碳化物在抽濾過程中與夾雜物分離,同時控制通電電流、電解時間及鋼樣尺寸,以進行精確的定量電解,並於抽濾時採用不同孔徑的濾紙,對夾雜物按尺寸進行分級抽濾,最終實現高碳鉻軸承鋼中各類夾雜物的電解分離,完成原貌分析。
所述方法包括:
S1:將鋼樣加工至要求尺寸後,然後將加工好的待電解鋼樣置於加熱爐中進行預處理,預處理工藝為改良後的球化退火工藝;
S2:連接電解裝置,其中所使用電源為直流電源,接線連通後,電解過程採用恆壓控制模式,電壓選取(120-160)mV範圍內固定值控制,並保持電流控制在(0.04-0.07)A範圍內,電解時間2~5h;
S3:電解結束後將鋼樣、鋼樣與導線連接段、陰極等進行衝洗,所有衝洗液及電解液全部收集,倒入抽濾瓶進行抽濾,抽濾首先使用孔徑2μm的聚碳酸酯濾膜,抽濾重複進行2-4遍,再使用孔徑0.45μm的聚碳酸酯濾膜將第一次抽濾後得到的濾液再次重複抽濾2-4遍;
S4:將兩次抽濾所用的不同孔徑濾膜置於乾燥箱中烘乾,然後將烘乾後濾膜使用導電膠粘於導電基體上;
S5:對固定在導電基體上的濾膜進行噴金或噴碳導電處理,使用掃描電鏡和能譜分析手段對濾膜上分離出的夾雜物進行三維形貌的觀察。
所述S1具體包括:
S11:首先將鋼樣加工至φ(5-10)mm×(30-50)mm的圓棒或(5-20)mm×(5-20)mm×(5-20)mm的方塊作為待電解鋼樣;
S12:將加工好的待電解鋼樣置於加熱爐中進行預處理,處理工藝為改良後的球化退火工藝;
S13:對處理後的待電解鋼樣的待電解截面進行打磨,採用金相制樣的方法,分別採用200#、400#和600#砂紙將鋼樣待電解截面進行打磨均勻。S1中所述改良後的球化退火工藝為:首先將置於爐內鋼樣加熱至780℃-820℃,保溫3h-5h,然後隨爐以30℃/h緩冷至680℃-720℃,保溫2h-4h,再以30℃/h緩冷至650℃,取出空冷至室溫,並對鋼樣待電解截面進行打磨。
所述S2具體包括:
S21:將陰極浸入電解液,電解液為AA溶液,所述為AA溶液為無水甲醇/乙醇-(5~15)%乙醯丙酮-(0.5~1.5)%四甲基氯化銨,其中,溶液中百分比為體積分數,所述陰極材質為鋼板,陰極形狀為閉合圈,陰極通過金屬導線連接直流電源負極;
S22:將待電解鋼樣四周使用絕緣膠帶密封,並通過金屬導線連接直流電源正極,僅留待電解截面裸露,電解時浸入電解液;
S23:接線連通後,電解過程採用恆壓控制模式,電壓選取120mV-160mV範圍內固定值控制,並保持電流控制在0.04A-0.07A範圍內,電解時間2~5h。
所述S3包括:
S31:將電解結束後的鋼樣、鋼樣與導線的連接段、陰極進行衝洗,衝洗所用試劑為無水甲醇/乙醇有機溶液,
S32:將所有衝洗液及電解液全部收集,倒入抽濾瓶進行抽濾,抽濾首先使用孔徑2μm的聚碳酸酯濾膜,抽濾重複進行2-4遍,再使用孔徑0.45μm的聚碳酸酯濾膜將第一次抽濾後得到的濾液再次重複抽濾2-4遍,所述S4具體為將兩次抽濾所用的不同孔徑濾膜置於乾燥箱中烘乾,乾燥箱溫度控制在150±2℃,乾燥時間1h-3h,然後將烘乾後濾膜使用導電膠粘於導電基體上,所述導電基體材質為金屬材質,該金屬材質為鋼塊,銅板或鋁板。
實施例1
首先將鋼樣加工至φ(5-10)mm×(30-50)mm的圓棒或(5-20)mm×(5-20)mm×(5-20)mm的方塊作為待電解鋼樣;(2)將加工好的待電解鋼樣置於加熱爐中進行預處理,處理工藝為改良後的球化退火工藝,所述工藝具體操作步驟如下:首先將置於爐內鋼樣加熱至(780-820)℃保溫(3-5)h,然後隨爐以30℃/h緩冷至(680-720)℃,保溫(2-4)h,再以30℃/h緩冷至650℃,取出空冷至室溫;(3)並對處理後的待電解鋼樣的待電解截面進行打磨,採用金相制樣的方法,分別採用200#、400#和600#砂紙將鋼樣待電解截面進行打磨均勻。
針對某高碳鉻軸承鋼採用本方法進行電解分離顯微夾雜物,該高碳鉻軸承鋼主要成分如附表1。具體實施過程如下:
(1)首先將該軸承鋼加工至10mm×10mm×15mm方塊作為待電解鋼樣;
(2)將加工好的待電解鋼樣置於加熱爐中進行預處理,處理工藝為改良後的球化退火工藝,所述工藝具體操作步驟如下:將置於爐內鋼樣加熱至800℃保溫5h,然後隨爐以30℃/h緩冷至720℃,保溫2h,再以30℃/h緩冷至650℃,取出空冷至室溫;
(3)並對處理後的待電解軸承鋼樣的待電解截面(一個10mm×10mm截面)進行打磨,採用金相制樣的方法,分別採用200#、400#和600#砂紙將鋼樣待電解截面進行打磨均勻;
(4)按附圖1接線連通電解裝置,所使用電源為直流電源。將陰極浸入電解液,電解液為甲醇-10%乙醯丙酮-1%四甲基氯化銨,陰極材質為鋼板,陰極形狀為閉合圈,陰極通過金屬導線連接直流電源負極;將待電解鋼樣四周使用絕緣膠帶密封,並通過金屬導線連接直流電源正極,僅留待電解截面裸露,電解時浸入電解液;接線連通後,電解過程中採用恆壓控制模式,電壓選取130mV範圍內固定值控制,並保持電流控制在(0.04-0.07)A範圍內,電解時間2-5h;
(5)電解結束後將鋼樣、鋼樣與導線連接段、陰極等進行衝洗,衝洗所用試劑為無水甲醇或乙醇有機溶液,將所有衝洗液及電解液全部收集,倒入抽濾瓶進行抽濾,抽濾首先使用孔徑2μm的聚碳酸酯濾膜,抽濾重複進行2遍,再使用孔徑0.45μm的聚碳酸酯濾膜將第一次抽濾後得到的濾液再次重複抽濾2遍;
(6)將兩次抽濾所用的不同孔徑濾膜置於乾燥箱中烘乾,乾燥箱溫度控制在(150±2)℃,乾燥時間1.5h,,然後將烘乾後濾膜使用導電膠粘於鋼塊上;
(7)對固定在鋼塊上的濾膜進行噴金導電處理,使用掃描電鏡和能譜分析手段對濾膜上分離出的夾雜物進行三維形貌的觀察,所觀察到該高碳鉻中各類軸承鋼中夾雜物的三維形貌如附圖3-7所示。
表1電解高碳鉻軸承鋼主要成分/wt%
以上所述的實施例,只是本發明較優選的具體實施方式的一種,本領域的技術人員在本發明技術方案範圍內進行的通常變化和替換都應包含在本發明的保護範圍內。