元件晶片的製造方法以及元件晶片與流程
2023-06-11 08:13:06 1
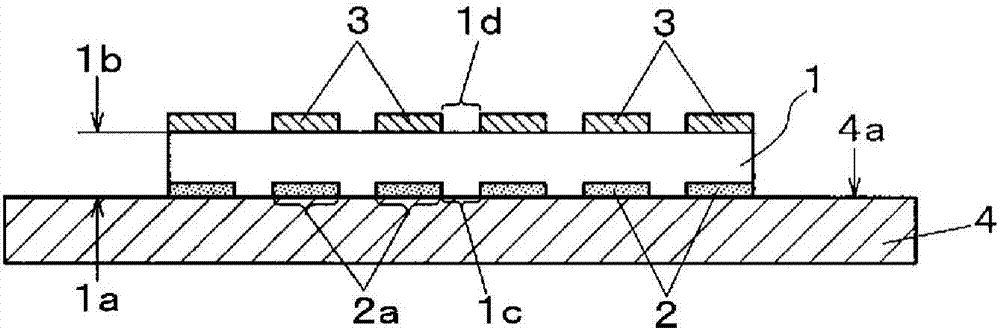
本公開涉及將具有多個元件區域的基板按每個元件區域進行分割來製造元件晶片的元件晶片的製造方法以及元件晶片。
背景技術:
半導體元件等元件晶片通過將具有多個元件區域的晶片狀的基板分割為單片而進行製造(例如,參照專利文獻1)。在該專利文獻所示的現有技術中,首先,以形成有電路的晶片的表面粘附於背面研磨膠帶的狀態對晶片的背面進行研磨,進而通過蝕刻將晶片薄化。然後,在相當於元件區域的部分形成抗蝕劑層而進行遮蓋,並實施等離子體蝕刻,從而將晶片分離為單片的半導體元件。
現有技術文獻
專利文獻
專利文獻1:日本特開2002-93752號公報
技術實現要素:
像上述那樣從晶片狀的基板切出的單片狀的元件晶片除了實施封裝而用作器件裝置以外,有時以wlcsp(waferlevelchipsizepackage:晶片級晶片尺寸封裝)等元件晶片的形態直接被送往電子部件安裝工序。在這種情況下,元件晶片以使電路形成面與接合用的焊糊、銀膏等導電性材料直接接觸的方式進行安裝。
本公開的目的在於,提供一種能夠抑制安裝過程中的導電性材料的爬升的元件晶片的製造方法。
本公開的元件晶片的製造方法是將具備具有用分割區域劃分的多個元件區域的第一面和第一面的相反側的第二面的基板在分割區域進行分割來形成多個元件晶片的元件晶片的製造方法,具有以下的特徵。該元件晶片的製造方法包括準備工序和在準備工序之後進行的等離子體處理工序。準備工序是準備基板的工序,基板的第一面側被載體支承,並且基板形成有耐蝕刻層,使得覆蓋與元件區域對置的第二面的區域且使與分割區域對置的第二面的區域露出。等離子體處理工序是對被載體支承的基板實施等離子體處理的工序,包括分割工序和在分割工序之後進行的保護膜形成工序。在分割工序中,將第二面暴露於第一等離子體,從而將未被耐蝕刻層覆蓋的區域的基板在該基板的深度方向上蝕刻至到達第一面而將基板分割為元件晶片。而且,成為具備第一面、第二面、以及連結第一面和第二面並且形成有多個凸部的側面的元件晶片彼此隔開間隔保持在載體上的狀態。在保護膜形成工序中,在彼此隔開間隔保持在載體上的狀態下,將元件晶片暴露於第二等離子體,從而在元件晶片的側面形成保護膜。在保護膜形成工序中,保護膜至少對凸部進行被覆。
本公開的元件晶片的製造方法是將具備具有用分割區域劃分的多個元件區域的第一面和第一面的相反側的第二面的基板在分割區域進行分割來形成多個元件晶片的元件晶片的製造方法,具有以下的特徵。元件晶片的製造方法包括準備工序和在準備工序之後進行的等離子體處理工序。準備工序是準備基板的工序,基板的第二面側被載體支承,並且基板形成有耐蝕刻層,使得覆蓋元件區域且使分割區域露出。等離子體處理工序是對被載體支承的基板實施等離子體處理的工序,包括分割工序和在分割工序之後進行的保護膜形成工序。在分割工序中,將第一面暴露於第一等離子體,從而將未被耐蝕刻層覆蓋的區域的基板在該基板的深度方向上蝕刻至到達第二面而將基板分割為元件晶片。而且,成為具備第一面、第二面、以及連結第一面和第二面並且形成有多個凸部的側面的元件晶片彼此隔開間隔保持在載體上的狀態。保護膜形成工序在分割工序之後,在彼此隔開間隔保持在載體上的狀態下,將元件晶片暴露於第二等離子體,從而在元件晶片的側面形成保護膜。在保護膜形成工序中,保護膜至少對凸部進行被覆。
本公開的元件晶片具備具有元件區域的第一面、第一面的相反側的第二面、以及連結第一面和第二面的側面,元件晶片在側面形成有多個凸部,側面的至少凸部被保護膜所被覆。
發明效果
根據本公開,能夠抑制安裝過程中的導電性材料的爬升。
附圖說明
圖1a是本公開的一個實施方式的元件晶片的製造方法中的第一實施例的工序說明圖。
圖1b是本公開的一個實施方式的元件晶片的製造方法中的第一實施例的工序說明圖。
圖1c是本公開的一個實施方式的元件晶片的製造方法中的第一實施例的工序說明圖。
圖2a是本公開的一個實施方式的元件晶片的製造方法中的第一實施例的工序說明圖。
圖2b是本公開的一個實施方式的元件晶片的製造方法中的第一實施例的工序說明圖。
圖2c是本公開的一個實施方式的元件晶片的製造方法中的第一實施例的工序說明圖。
圖3是在本公開的一個實施方式的元件晶片的製造方法中使用的等離子體蝕刻裝置的結構說明圖。
圖4a是本公開的一個實施方式的元件晶片的製造方法中的蝕刻槽形成過程的說明圖。
圖4b是本公開的一個實施方式的元件晶片的製造方法中的蝕刻槽形成過程的說明圖。
圖4c是本公開的一個實施方式的元件晶片的製造方法中的蝕刻槽形成過程的說明圖。
圖4d是本公開的一個實施方式的元件晶片的製造方法中的蝕刻槽形成過程的說明圖。
圖5a是本公開的一個實施方式的元件晶片的製造方法中的元件晶片的側面形狀的說明圖。
圖5b是本公開的一個實施方式的元件晶片的製造方法中的元件晶片的側面形狀的說明圖。
圖6是本公開的一個實施方式的元件晶片的製造方法中的元件晶片的側面形狀的說明圖。
圖7a是本公開的一個實施方式的元件晶片的製造方法中的第二實施例的工序說明圖。
圖7b是本公開的一個實施方式的元件晶片的製造方法中的第二實施例的工序說明圖。
圖7c是本公開的一個實施方式的元件晶片的製造方法中的第二實施例的工序說明圖。
圖8a是本公開的一個實施方式的元件晶片的製造方法中的第二實施例的工序說明圖。
圖8b是本公開的一個實施方式的元件晶片的製造方法中的第二實施例的工序說明圖。
圖8c是本公開的一個實施方式的元件晶片的製造方法中的第二實施例的工序說明圖。
圖9a是通過本公開的一個實施方式的元件晶片的製造方法製造的元件晶片的結構說明圖。
圖9b是通過本公開的一個實施方式的元件晶片的製造方法製造的元件晶片的結構說明圖。
圖9c是通過本公開的一個實施方式的元件晶片的製造方法製造的元件晶片的結構說明圖。
圖9d是通過本公開的一個實施方式的元件晶片的製造方法製造的元件晶片的結構說明圖。
符號說明
1:基板
1a:第一面
1b:第二面
1c:分割區域
2:元件部
2a:元件區域
3:耐蝕刻層
4:載體
10、10a、10b、10c、10d:元件晶片
10a:第一面
10b:第二面
10c:側面
12a、12b、12c、12d:保護膜
e:凸部
具體實施方式
在對本公開的實施方式進行說明之前,先對以往的裝置中的問題進行簡單說明。
如上所述,在將wlcsp等元件晶片以按其原樣的形態送往電子部件安裝工序的情況下,元件晶片以使電路形成面與接合用的焊糊、銀膏等導電性材料直接接觸的方式進行安裝。在該安裝過程中,有時會產生所謂的「爬升」,即,在搭載元件晶片時擴展的導電性材料不只浸潤擴展至電路形成面的接合部位,還浸潤擴展至元件晶片的側面、背面。這種導電性材料的爬升會成為導致鄰接的電極間的短路、在元件晶片的側面形成不需要的電路而增大消耗電流等各種不良情況的原因。因此,要求抑制這種安裝過程中的導電性材料的爬升。
接著,參照附圖對本公開的實施方式進行說明。
(第一實施例)
首先,參照圖1a~圖1c以及圖2a~圖2c對本實施方式的元件晶片的製造方法中的第一實施例進行說明。在此示出的元件晶片的製造方法將具備具有用分割區域劃分的多個元件區域的第一面和該第一面的相反側的第二面的基板在分割區域進行分割來形成多個元件晶片。
如圖1a所示,基板1是形成有多個具有元件部2的元件晶片10(參照圖1c)的晶片狀的基板。在基板1中,在作為形成有元件部2的元件面的第一面1a設定有用分割區域1c劃分的多個元件區域2a。基板1被送往元件晶片製造用的準備工序,像以下說明的那樣,被載體4支承並形成掩模。作為載體4,能夠例示被切割架保持的切割膠帶、在保持面4a具備粘接層的支承基板。
在該準備工序中,如圖1b所示,在第二面1b由在等離子體切割中作為掩模發揮功能的抗蝕劑掩模、表面保護膜等形成耐蝕刻層3。即,在第二面1b形成耐蝕刻層3,使得覆蓋與元件區域2a對置的第二面1b的區域,且使與分割區域1c對置的第二面1b的區域1d露出。此外,基板1的第一面1a側被載體4的保持面4a支承。另外,準備工序中的掩模形成可以在被載體4支承之前進行,也可以在被載體4支承之後進行。
在像這樣進行準備工序之後,為了對被載體4支承的基板1實施等離子體處理,載體4被送往等離子體處理工序。參照圖3對在該等離子體處理工序中使用的等離子體蝕刻裝置20的結構進行說明。在圖3中,作為真空容器的腔室21的內部是用於進行等離子體處理的處理室21a,在處理室21a的底部配置有載置對作為處理對象的基板1進行支承的載體4的載置臺22。在腔室21的頂部的上表面配置有作為上部電極的天線23,天線23與第一高頻電源部24電連接。處理室21a內的載置臺22還具有作為等離子體處理用的下部電極的功能,載置臺22與第二高頻電源部25電連接。
在腔室21經由排氣口21c連接有真空排氣部27,通過驅動真空排氣部27,從而對處理室21a內進行真空排氣。進而,處理室21a經由氣體導入口21b連接有等離子體產生用氣體供給部26。在本實施方式所示的等離子體蝕刻裝置20中,能夠根據等離子體處理的目的,選擇性地供給多種等離子體產生用氣體。在此,作為等離子體產生用氣體的種類,能夠選擇第一氣體26a、第二氣體26b、第三氣體26c以及灰化用氣體26d。
作為第一氣體26a,可使用sf6等以矽為對象的蝕刻效果優異的氣體。在本實施方式中,第一氣體26a用於產生通過等離子體蝕刻對基板1進行分割的第一等離子體p1。作為第二氣體26b,可使用包含c4f8、c2f6、cf4、c6f6、c6f4h2、chf3、ch2f2等氟化碳的氣體。這些氣體可用作通過等離子體處理形成皮膜的等離子體cvd用的氣體,在本實施方式中,用作在對基板1進行了分割的元件晶片10的側面形成保護膜的目的。
作為第三氣體26c,可使用sf6氣體、氧氣、氬氣等物理蝕刻效果優異的氣體。在本實施方式中,用於除去前述的保護膜中的不需要的部分的濺射用途。而且,灰化用氣體26d是氧氣,在本實施方式中,用作除去結束了掩模功能之後的耐蝕刻層3等樹脂膜的目的。
在利用等離子體蝕刻裝置20進行的等離子體處理中,首先,將作為處理對象的基板1和載體4一同載置在載置臺22上,驅動真空排氣部27對處理室21a內進行真空排氣。與此同時,通過等離子體產生用氣體供給部26將與等離子體處理的目的相應的等離子體產生用氣體供給到處理室21a內並維持給定壓力。然後,在該狀態下通過第一高頻電源部24對天線23供給高頻電力,從而在處理室21a內產生與供給的等離子體產生用氣體的種類相應的等離子體。此時,通過第二高頻電源部25對作為下部電極的載置臺22施加偏置電壓,從而能夠對在處理室21a內產生的等離子體帶來促進向載置臺22的方向的入射的偏置作用,能夠加強所希望的特定方向的等離子體處理效果而進行各向異性蝕刻。
在等離子體處理工序中,首先,利用使用了前述的第一氣體26a的第一等離子體p1執行處理。如圖1c所示,將基板1的第二面1b暴露於上述的第一等離子體p1,從而將未被耐蝕刻層3覆蓋的區域1d(參照圖1b)的基板1在該基板1的深度方向上蝕刻至到達第一面1a(參照箭頭e),形成將每個元件晶片10隔開的蝕刻槽11(參照圖2a),從而將基板1分割為單片的元件晶片10。即,成為具備在基板1的狀態下為第一面1a的第一面10a、在基板1的狀態下為第二面1b的第二面10b、以及連結第一面10a和第二面10b的側面10c的元件晶片10彼此隔開間隔保持在載體4上的狀態(分割工序)。
分割工序中的蝕刻條件能夠根據基板1的材質適當地進行選擇。在基板1為矽基板的情況下,分割工序中的蝕刻能夠使用所謂的波希法(boschprocess)。在波希法中,依次重複對形成基板1的矽進行蝕刻的矽蝕刻步驟、使沉積膜沉積在通過矽蝕刻步驟進行了蝕刻的部分的內壁的沉積膜沉積步驟、以及對沉積的沉積膜進行蝕刻的沉積膜蝕刻步驟。由此,能夠對未被耐蝕刻層3覆蓋的區域1d在基板的深度方向上垂直地進行挖入。
參照圖4a~圖4d對利用了該波希法的蝕刻槽11的形成過程進行說明。圖4a示出矽蝕刻步驟中的等離子體蝕刻。即,將基板1的第二面1b暴露於第一等離子體p1,從而通過第一等離子體(箭頭a)的各向同性蝕刻作用在第二面1b中的未被耐蝕刻層3覆蓋的區域形成大致橢圓截面的除去部1e。作為該矽蝕刻步驟的條件,例如,只要一邊作為原料氣體以200~400sccm供給sf6,一邊將處理室21a內的壓力調整為5~15pa,並且將第一高頻電源部24對天線23的投入功率設為1500~2500w,將第二高頻電源部25對下部電極的投入功率設為50~200w,將處理時間設為10~20秒即可。在此,sccm是表示氣體的流量的單位。即,1sccm是指,一分鐘流過1cm3的0℃、一個大氣壓(標準狀態)的氣體的流量。
接下來,執行沉積膜沉積步驟用的等離子體處理。即,如圖4b所示,將除去部1e內暴露於沉積膜沉積用的等離子體(箭頭b),從而在除去部1e的內表面形成沉積膜1f。作為沉積膜沉積步驟的條件,例如,只要一邊作為原料氣體以150~250sccm供給c4f8,一邊將處理室21a內的壓力調整為15~25pa,並且將第一高頻電源部24對天線23的投入功率設為1500~2500w,將第二高頻電源部25對下部電極的投入功率設為0w,將處理時間設為5~15秒即可。
接著,執行沉積膜蝕刻步驟。即,如圖4c所示,使沉積膜蝕刻用等離子體(箭頭c)只作用於在除去部1e內位於下表面的區域的沉積膜1f,通過各向異性蝕刻除去該區域的沉積膜1f。由此,在除去部1e的底面形成暴露了矽的部分除去部1g。作為沉積膜蝕刻步驟的條件,例如,只要一邊作為原料氣體以200~400sccm供給sf6,一邊將處理室21a內的壓力調整為5~15pa,並且將第一高頻電源部24對天線23的投入功率設為1500~2500w,將第二高頻電源部25對下部電極的投入功率設為100~300w,將處理時間設為2~10秒即可。
此後,將形成了部分除去部1g之後的基板1作為對象,再次執行矽蝕刻步驟。即,如圖4d所示,將在沉積膜蝕刻步驟中形成的部分除去部1g與圖4a同樣地暴露於第一等離子體(箭頭d)。由此,通過第一等離子體(箭頭d)的各向同性蝕刻作用,形成與除去部1e的底面連通的大致橢圓截面的除去部1h。這樣,通過重複矽蝕刻步驟、沉積膜沉積步驟、沉積膜蝕刻步驟,從而能夠以10μm/分鐘的速度對矽基板進行挖入。此時,在除去部1e過渡到下一個除去部1h的邊界部分形成從蝕刻槽11的內壁面(基板1被分割為元件晶片10的狀態下的側面10c)突出的凸部e。
即,在本實施方式所示的等離子體處理工序中,成為上述的分割工序包括重複工序的方式,該重複工序交替地重複對基板1進行蝕刻的矽蝕刻步驟、使沉積膜沉積在通過該矽蝕刻步驟進行了蝕刻的部分的內壁的沉積膜沉積步驟。圖5a和圖5b示出在該重複工序中形成的多個凸部e的形成形態。
即,每重複一次形成一個凸部e,如圖5a所示,在分割工序中,在元件晶片10的側面10c形成多個凸部e。圖5b示出圖5a中的a-a向視圖,在元件晶片10的側面10c,多個凸部e沿著第二面10b(或者,與第二面10b平行的第一面10a)形成為多條線狀。
此後,進行除去在單片的元件晶片10中覆蓋著第二面10b的狀態的耐蝕刻層3的灰化。即,如圖2a所示,在等離子體蝕刻裝置20中,在處理室21a內使用灰化用氣體26d產生灰化用等離子體,通過灰化除去以樹脂為主成分的耐蝕刻層3。由此,分割為單片的元件晶片10的第二面10b成為暴露的狀態。
灰化的條件能夠根據耐蝕刻層3的材料適當地進行選擇。例如,在耐蝕刻層3為抗蝕劑膜的情況下,只要一邊作為原料氣體以150~250sccm供給氧並以0~50sccm供給cf4,一邊將處理室21a內的壓力調整為5~15pa,並且將第一高頻電源部24對天線23的投入功率設為1500~2500w,將第二高頻電源部25對下部電極的投入功率設為0~30w即可。在該條件下,能夠以1μm/分鐘左右的速度除去耐蝕刻層3。
接下來,在上述的分割工序之後執行保護膜形成工序。即,在等離子體蝕刻裝置20中,在處理室21a內使用作為包含氟化碳的氣體的第二氣體26b產生第二等離子體p2,並如圖2b所示,在彼此隔開間隔保持在載體4上的狀態下,將元件晶片10暴露於第二等離子體p2。由此,在元件晶片10的第二面10b、側面10c分別形成保護膜12b、12c。而且,與此同時,在載體4的上表面也附著組成相同的保護膜12d。
這些保護膜是以抑制將元件晶片10直接接合到封裝基板等的安裝過程中的導電性材料的爬升為目的形成的,因此優選吸溼性少且組成緻密。在本實施方式中,作為為了形成這些保護膜而使用的第二等離子體p2的原料氣體,使用包含氟化碳的氣體,因此作為保護膜形成以包含氟和碳的碳氟化合物為主成分的膜,能夠形成吸溼性少、組成緻密且粘合性優異的保護膜。另外,在該保護膜形成工序中,對載置載體4的載置臺22(參照圖3)施加高頻偏置。由此,可促進離子向元件晶片10的入射,能夠形成更緻密且粘合性更高的保護膜。
作為保護膜的形成條件,例如,只要一邊作為原料氣體以150sccm供給c4f8並以50sccm供給he,一邊將處理室21a內的壓力調整為15~25pa,並且將第一高頻電源部24對天線23的投入功率設為1500~2500w,將第二高頻電源部25對下部電極的投入功率設為50~150w即可。通過在該條件下處理300秒,從而能夠形成厚度為3μm的保護膜。
在本實施方式中,作為原料氣體,使用氟化碳和氦的混合氣體,這是因為,通過混合氦,從而可促進等離子體中的原料氣體的離解,其結果是,能夠形成緻密且粘合性高的保護膜。
另外,在上述的條件例中,he流量相對於原料氣體的全部流量的比率為25%(=50/(150+50)×100)。像以下說明的那樣,該比率優選在10%至80%之間。即,當he流量相對於原料氣體的全部流量的比率大於10%時,容易促進等離子體中的原料氣體的離解,其結果是,容易形成更緻密且粘合性更高的保護膜。另一方面,當he流量相對於原料氣體的全部流量的比率大於80%時,在原料氣體中c4f8所佔的比率減少,因此有助於形成保護膜的等離子體中的成分(c、f以及它們的化合物)向基板表面的供給不足,基板表面的保護膜的沉積速度變慢,生產性降低。
圖6示出在保護膜形成工序中對形成在圖5a和圖5b所示的側面10c的多個凸部e進行被覆而形成的保護膜12c的詳細形狀。如圖6所示,保護膜12c形成為至少覆蓋側面10c中的凸部e。而且,保護膜12c形成為,對凸部e進行被覆的保護膜12c的膜厚te大於相鄰的兩個凸部e的中間(在此為形成在凸部e之間的凹部的底部b)處的膜厚tb。
即,保護膜12c形成為,與側面10c中的凸部e的頂部與凹部的底部b的階差d1相比,對凸部e進行被覆的保護膜12c的頂部與對底部b進行被覆的保護膜12c的表面的階差d2更大。由此,形成保護膜之後的側面10c中的凸部e與底部b的階差擴大。因此,能夠增大側面10c的實質性的表面積而提高元件晶片10的安裝過程中的導電性材料的爬升抑制效果。
接著,執行用於除去在保護膜形成工序中形成的保護膜中的不需要的部分的保護膜除去工序。在上述的保護膜形成工序中,在元件晶片10的側面10c形成保護膜的同時,在第二面10b也形成了保護膜12b(參照圖2b)。因為不需要該保護膜12b,所以使用第三等離子體p3進行用於除去該保護膜12b的等離子體處理。
即,在等離子體蝕刻裝置20中,在處理室21a內使用成分為氬氣、氧氣的第三氣體26c產生第三等離子體p3,並如圖2c所示,在彼此隔開間隔保持在載體4上的狀態下,將元件晶片10暴露於第三等離子體p3。由此,使形成在元件晶片10的側面10c的保護膜12c殘留,並通過第三等離子體p3的蝕刻作用除去在元件晶片10中暴露在上表面的形成在第二面10b的保護膜12b。由此,彼此隔開間隔保持在載體4上的元件晶片10的第二面10b成為暴露的狀態,附著在載體4的上表面的保護膜12d也被除去。
在上述的保護膜除去工序中,對載置載體4的載置臺施加高頻偏置。由此,能夠提高第三等離子體p3的蝕刻作用的各向異性。因此,能夠可靠地除去暴露在上表面的第二面10b的保護膜12b,並且能夠抑制作用於元件晶片10的側面10c的保護膜12c的蝕刻作用而使保護膜12c殘留。
作為除去保護膜的條件,例如,只要一邊作為原料氣體以150~250sccm供給ar並以0~150sccm供給o2,一邊將處理室21a內的壓力調整為0.2~1.5pa,並且將第一高頻電源部24對天線23的投入功率設為1500~2500w,將第二高頻電源部25對下部電極的投入功率設為150~300w即可。在該條件下,能夠以0.5μm/分鐘左右的速度對暴露在上表面的保護膜進行蝕刻。
(第二實施例)
接著,參照圖7a~圖7c和圖8a~圖8c對本實施方式的元件晶片的製造方法中的第二實施例進行說明。在此,第二實施例所示的元件晶片的製造方法與第一實施例中的元件晶片的製造方法同樣地,將具備具有用分割區域劃分的多個元件區域的第一面和該第一面的相反側的第二面的基板在分割區域進行分割來形成多個元件晶片。
如圖7a所示,基板1是形成有具有元件部2的多個元件晶片10(參照圖7c)的晶片狀的基板。在基板1中,在作為形成有元件部2的元件面的第一面1a設定有用分割區域1c劃分的多個元件區域2a。基板1被送往元件晶片製造用的準備工序,在此,像以下說明的那樣,被載體4支承並形成掩模。作為載體4,與第一實施例同樣地,可使用粘合片、支承基板等能夠對薄且易撓曲的基板1進行固定並進行操作的載體。
在該準備工序中,如圖7b所示,在第一面1a形成在等離子體切割中作為掩模發揮功能的耐蝕刻層3。即,在第一面1a形成耐蝕刻層3,使得覆蓋元件區域2a且使分割區域1c露出。基板1的第二面1b側被載體4的保持面4a支承。另外,準備工序中的掩模形成可以在被載體4支承之前進行,也可以在被載體4支承之後進行。
在像這樣進行準備工序之後,為了對被載體4支承的基板1實施等離子體處理,載體4被送往等離子體處理工序。在該等離子體處理工序中,使用在第一實施例中說明的等離子體蝕刻裝置20(參照圖3)。
在等離子體處理工序中,首先,利用使用了第一氣體26a的第一等離子體p1執行處理。如圖7c所示,將基板1的第一面1a暴露於上述的第一等離子體p1,從而將未被耐蝕刻層3覆蓋的分割區域1c(參照圖7c)的基板1在該基板1的深度方向上蝕刻至到達第二面1b(參照箭頭e),形成將每個元件晶片10隔開的蝕刻槽11(參照圖8a),從而將基板1分割為單片的元件晶片10。即,成為具備在基板1的狀態下為第一面1a的第一面10a、在基板1的狀態下為第二面1b的第二面10b、以及連結第一面10a和第二面10b的側面10c的元件晶片10彼此隔開間隔保持在載體4上的狀態(分割工序)。
在該分割工序中,與第一實施例同樣地,交替地重複對基板1進行蝕刻的蝕刻步驟和使沉積膜沉積在通過該蝕刻步驟進行了蝕刻的部分的內壁的沉積膜沉積步驟(重複工序)。然後,在該重複工序中,與第一實施例同樣地,在元件晶片10的側面10c沿著第一面10a呈多條線狀形成凸部e。
此後,進行除去在單片的元件晶片10中覆蓋了第一面10a的狀態的耐蝕刻層3的灰化。即,如圖8a所示,在等離子體蝕刻裝置20中,在處理室21a內使用灰化用氣體26d產生灰化用等離子體,通過灰化除去以樹脂為主成分的耐蝕刻層3。由此,分割為單片的元件晶片10的第一面10a成為暴露的狀態。
接下來,在上述的分割工序之後執行保護膜形成工序。即,在等離子體蝕刻裝置20中,在處理室21a內使用作為包含氟化碳的氣體的第二氣體26b產生第二等離子體p2,並如圖8b所示,在彼此隔開間隔保持在載體4上的狀態下,將元件晶片10暴露於第二等離子體p2。由此,在元件晶片10的第一面10a、側面10c分別形成保護膜12a、12c。
在該保護膜形成工序中,關於對多個凸部e進行被覆並形成在側面10c的保護膜12c的詳細形狀(參照圖5a和圖5b)以及優點、效果,與第一實施例相同。此外,在形成這些保護膜時,作為第二等離子體p2的原料氣體,也可以使用氟化碳和氦的混合氣體,由此帶來的優點、效果也與第一實施例相同。另外,在該保護膜形成工序中,對載置載體4的載置臺施加高頻偏置。由此,可促進離子向元件晶片10的入射,能夠形成更緻密且粘合性更高的保護膜。
接著,執行用於除去在保護膜形成工序中形成的保護膜中的不需要的部分的保護膜除去工序。在上述的保護膜形成工序中,在元件晶片10的側面10c形成保護膜的同時,在第一面10a也形成了保護膜12a(參照圖8b)。因為不需要該保護膜12a,所以使用第三等離子體p3進行除去該保護膜12a的等離子體處理。
即,在等離子體蝕刻裝置20中,在處理室21a內使用成分為氬氣、氧氣的第三氣體26c產生第三等離子體p3,並如圖8c所示,在彼此隔開間隔保持在載體4上的狀態下,將元件晶片10暴露於第三等離子體p3。由此,使形成在元件晶片10的側面10c的保護膜12c殘留,並通過第三等離子體p3的蝕刻作用除去在元件晶片10中暴露在上表面的形成在第一面10a的保護膜12a。由此,彼此隔開間隔保持在載體4上的元件晶片10的第一面10a成為暴露的狀態,附著在載體4的上表面的保護膜12d也被除去。
在上述的保護膜除去工序中,對載置載體4的載置臺施加高頻偏置。由此,能夠提高第三等離子體p3的蝕刻作用的各向異性。因此,能夠可靠地除去暴露在上表面的第一面10a的保護膜12a,能夠抑制作用於元件晶片10的側面10c的保護膜12c的蝕刻作用而使保護膜12c殘留。
接著,參照圖9a~圖9d,示出通過本實施方式所示的元件晶片的製造方法製造的元件晶片10的變形例。這些元件晶片10均具備具有元件區域2a的第一面10a、第一面10a的相反側的第二面10b、以及連結第一面10a和第二面10b的側面10c。而且,如圖5a、圖5b以及圖6所示,是如下結構,即,在側面10c形成有多個凸部e,側面10c的至少凸部e被保護膜12c所被覆。
圖9a和圖9b示出通過圖1a~圖1c以及圖2a~圖2c所示的第一實施例的元件晶片的製造方法製造的元件晶片10a、元件晶片10b。即,圖9a所示的元件晶片10a是如下狀態,即,不僅殘留了形成在側面10c的保護膜12c,而且還在第二面10b殘留有保護膜12b。在圖9b所示的元件晶片10b中,從第二面10b除去了保護膜12b。
此外,圖9c和圖9d示出通過圖7a~圖7c以及圖8a~圖8c所示的第二實施例的元件晶片的製造方法製造的元件晶片10c、元件晶片10d。圖9c所示的元件晶片10c是如下狀態,即,不僅殘留了形成在側面10c的保護膜12c,還在元件部2側的第一面10a殘留有保護膜12a。在圖9d所示的元件晶片10d中,從第一面10a除去了保護膜12a。
在上述結構的元件晶片10a~10d中,至少在側面10c中的在安裝過程中與導電性粘接材料接觸的範圍形成有具有抑制導電性粘接材料的浸潤擴展的表面性狀的保護膜12c,因此能夠抑制安裝過程中的導電性材料的爬升。進而,在本實施方式中,以覆蓋形成在側面10c的多個凸部e的方式形成有保護膜12c,因此能夠增大側面10c的實質性的表面積而提高元件晶片10的安裝過程中的導電性材料的爬升抑制效果。
本公開的元件晶片的製造方法具有能夠抑制安裝過程中的導電性材料的爬升的效果,在將具有多個元件區域的基板按每個元件區域進行分割來製造元件晶片的領域中是有用的。