一種顆粒增強鋁基複合材料大尺寸厚壁管材的製備方法與流程
2023-10-18 01:30:34 2
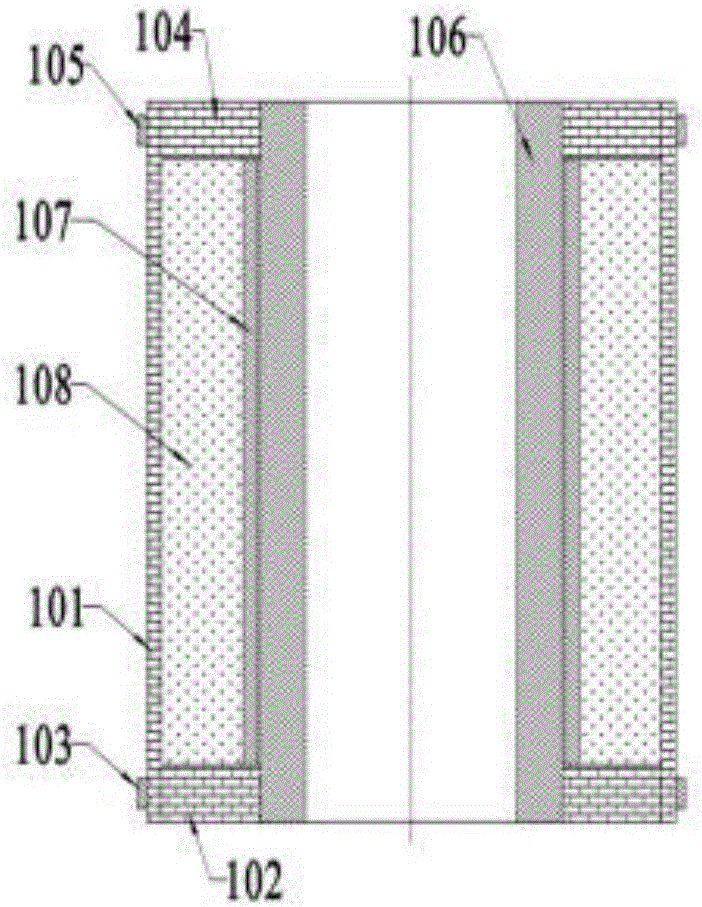
本發明屬於金屬基複合材料管材製備技術領域,具體涉及一種顆粒增強鋁基複合材料大尺寸厚壁管材的製造方法。
背景技術:
顆粒增強鋁基複合材料是近年來發展起來的一種先進結構材料,該材料具有高比強度和比剛度、耐磨、耐疲勞和低密度等優異的性能。從上世紀80年代初開始,世界各國競相對這類材料進行了許多基礎性研究,取得了顯著成績。目前,在美國和歐洲等發達國家,顆粒增強鋁基複合材料已經在一系列重要場合獲得了應用,比如:DWA公司用6092/SiC/17.5p複合材料代替原有的2214鋁合金蒙皮,用於F-16戰鬥機的腹鰭,使剛度提高50%,壽命由原來的數百小時延長到至少6000h飛行時間。
顆粒增強鋁基複合材料屬於輕質高強、高模量材料,該材料製成的大尺寸薄壁管材可以應用於水下航行器殼體,解決鋁合金剛度低、鋼密度大等問題。經對現有技術文獻的檢索發現,中國專利公開報導有關顆粒增強鋁基複合材料大尺寸薄壁管材的製造方法旋壓為主,其旋壓用大尺寸厚壁管材的製造方法為鑄造或粉末冶金坯錠+反擠壓,該方法工藝路線長、成本高,需要大型擠壓機。
技術實現要素:
本發明針對現有大尺寸厚壁管材的製造方法的不足,提供了一種顆粒增強鋁基複合材料大尺寸厚壁管材的製備方法,所述管材尺寸為:外徑200~1000mm、壁厚20~150mm、長度200~1500mm,其特徵是,採用粉末冶金和熱等靜壓技術製備,該方法包括下述步驟:
(1)將增強體顆粒與鋁合金粉末按照比例加入到混料機中,加入鋼球後進行均勻混合,製成混合粉末;
(2)將混合粉末封裝於冷等靜壓包套組件中進行冷等靜壓成型;
(3)去除管坯外面的冷等靜壓包套組件,得到帶有冷壓定形芯模的管坯;
(4)將帶有冷壓定形芯模的管坯封裝入金屬包套組件中進行高溫真空除氣處理;
(5)將經高溫真空除氣處理的管坯進行熱等靜壓緻密化處理;
(6)經緻密化處理後的管坯通過機加工去掉金屬包套和冷壓定形芯模,得到顆粒增強鋁基複合材料管材。
步驟(1)中,所述增強體顆粒為Al2O3、SiC、B4C、TiC、Si3N4、AlN中的一種,平均粒度為2~20μm,增強體顆粒在混合粉末中體積百分含量為5%~15%;所述鋁合金粉末為2×××和6×××中的任意一種合金,平均粒度為5~75μm,鋁合金粉末在混合粉末中的體積百分含量為95%~85%。
步驟(1)中,所述混合用鋼球材質為軸承不鏽鋼,規格為Φ10~Φ20mm,球料重量比為(5~15):1,混料機轉速為30~60r/min,混合時間為24~48小時。
步驟(2)中,所述冷等靜壓的壓力為100~200MPa,保壓時間為10~30min。
步驟(2)中,所述冷等靜壓包套組件由冷壓橡膠包套、冷壓第一密封塞子、冷壓第一密封卡箍、冷壓第二密封塞子、冷壓第二密封卡箍、冷壓密封芯模、冷壓定形芯模組成;封裝順序為:首先用冷壓第一密封卡箍將冷壓橡膠包套的一端、冷壓第一密封塞子和冷壓密封芯模的一端裝配密封,然後把冷壓定形芯模裝配到冷壓密封芯模內部,將複合材料混合粉末填充到冷壓橡膠包套和冷壓定形芯模之間,最後用冷壓第二密封卡箍將冷壓橡膠包套的另一端、冷壓第二密封塞子和冷壓密封芯模的另一端裝配密封。
所述冷壓密封芯模與冷壓定形芯模之間的間隙為0.5±0.2mm。
所述冷壓定形芯模材質為不鏽鋼,壁厚5~10mm,外徑比最終管材內徑小4~10mm;所述冷壓密封芯模材質為優質碳素結構用鋼或低碳鋼,壁厚10~20mm。
步驟(4)中,所述高溫除氣溫度為530~590℃,升溫速度為10~50℃/h,封口前真空度≤1×10-2Pa。
步驟(4)中,所述金屬包套材質為純鋁,包套厚度為2~5mm;所述金屬包套組件由金屬包套外筒、金屬包套內筒、金屬包套第一密封蓋、金屬包套第二密封蓋、金屬包套抽氣管組成;封裝順序為:首先將金屬包套外筒和金屬包套內筒分別與金屬包套第一密封蓋裝配焊接密封,形成金屬包套第一焊縫和金屬包套第二焊縫;然後把帶有冷壓定形芯模的管坯置於金屬包套外筒和金屬包套內筒之間;再將金屬包套外筒和金屬包套內筒分別與金屬包套第二密封蓋裝配焊接密封,形成金屬包套第三焊縫和金屬包套第四焊縫;最後將金屬包套抽氣管與金屬包套第二密封蓋焊接相連,金屬包套抽氣管與管坯相通。
步驟(5)中,所述熱等靜壓溫度為530~590℃,壓力為90~130MPa,保壓時間為2~5小時,熱等靜壓溫度和高溫除氣的溫度相同。
本發明的優點在於:
1、採用粉末冶金+熱等靜壓技術,通過優化工藝參數製備的複合材料完全緻密、無孔洞等缺陷,強度高;材料具有較高的延伸率、較好的塑性,非常有利於開展後續熱加工變形。
2、在冷等靜壓包套組件中使用了冷壓定形芯模,該冷壓定形芯模既可保證管材內徑均勻、尺寸偏差小,又能減少加工餘量,節約材料,降低成本。
3、採用熱等靜壓工藝進行最終緻密化成形,在熱等靜壓處理過程中,惰性氣體介質壓力通過包套均勻作用於管坯,管坯收縮均勻、形狀規則、機加工量小。
4、選用超細粉末直接混合製成混合粉末,使各組元粉末在微米尺度上均勻混合,避免了增強體顆粒的偏聚;所製得的複合材料管材的組織細小均勻、完全緻密;增強體顆粒彌散分布於鋁基體中,具有較高的延伸率和較好的熱加工性能。
附圖說明
圖1是製備顆粒增強鋁基複合材料管材的工藝流程圖;
圖2是顆粒增強鋁基複合材料冷等靜壓包套組件結構示意圖;
圖3是顆粒增強鋁基複合材料金屬包套組件結構示意圖。
具體實施方式
本發明提供了一種顆粒增強鋁基複合材料大尺寸厚壁管材的製備方法,下面通過具體實施方法和附圖對本發明做進一步說明,但不意味著對本發明保護範圍的限制。
圖2是顆粒增強鋁基複合材料冷等靜壓包套組件結構示意圖,其中,包括冷壓橡膠包套101,冷壓第一密封塞子102,冷壓第一密封卡箍103,冷壓第二密封塞子104,冷壓第二密封卡箍105,冷壓密封芯模106,冷壓定形芯模107,複合材料混合粉末108。
圖3是顆粒增強鋁基複合材料金屬包套組件結構示意圖,其中,金屬包套外筒201,金屬包套內筒202,金屬包套第一密封蓋203,金屬包套第二密封蓋204,複合材料冷等靜壓管坯205,冷壓定形芯模206,金屬包套第一焊縫207,金屬包套第二焊縫208,金屬包套第三焊縫209,金屬包套第四焊縫210,金屬包套抽氣管211。
實施例1
本實施例所製備的複合材料管材成分為15vol.%SiCp/2009Al,管材尺寸為外徑1000mm、壁厚150mm、長度800mm。
按照圖1所示的製備方法:(1)將碳化矽粉末與2009Al合金粉末按照體積比15:75均勻混合,碳化矽粉末平均粒度d0.5為5.5μm,2009Al粉末平均粒度d0.5為10μm;混合用鋼球材質為軸承不鏽鋼,規格為Φ20mm,球料重量比為5:1,混料機轉速為30r/min,混合48小時;(2)將各個冷等靜壓包套組件順序組裝,冷壓定形芯模材質選用不鏽鋼,外徑690mm、壁厚10mm、長度820mm;冷壓密封芯模材質材質選用45號鋼,外徑669mm,壁厚20mm;(3)將混合粉末封裝於冷等靜壓包套組件中,封裝順序為:首先用冷壓第一密封卡箍103將冷壓橡膠包套101的一端、冷壓第一密封塞子102和冷壓密封芯模106的一端裝配密封,然後把冷壓定形芯模107裝配到冷壓密封芯模106內部,將複合材料混合粉末108填充到冷壓橡膠包套101和冷壓定形芯模107之間,最後用冷壓第二密封卡箍105將冷壓橡膠包套101的另一端、冷壓第二密封塞子104和冷壓密封芯模106的另一端裝配密封;封裝完成後進行冷等靜壓成型,冷等靜壓壓力為200MPa,冷等靜壓保壓時間為20min;(4)去除管坯外面的冷等靜壓包套101組件,得到帶有冷壓定形芯模的管坯;(5)將帶有冷壓定形芯模的管坯封裝入純鋁包套組件中進行高溫真空除氣處理,封裝順序為:首先將金屬包套外筒201和金屬包套內筒202分別與金屬包套第一密封蓋203裝配焊接密封,形成金屬包套第一焊縫207和金屬包套第二焊縫208;然後把帶有冷壓定形芯模的管坯置於金屬包套外筒201和金屬包套內筒202之間;再將金屬包套外筒201和金屬包套內筒202分別與金屬包套第二密封蓋204裝配焊接密封,形成金屬包套第三焊縫209和金屬包套第四焊縫210;最後將金屬包套抽氣管211與金屬包套第二密封蓋204焊接相連,金屬包套抽氣管211與管坯相通;其中,包套厚度為5mm,除氣溫度590℃,除氣升溫速度為10℃/h,封口前真空度為1×10-2Pa;(6)將經高溫真空除氣處理的管坯進行熱等靜壓緻密化,熱等靜壓溫度為590℃,壓力為90MPa,在此溫度壓力下保持5小時;(7)機加工去掉金屬包套和冷壓定形芯模,得到複合材料管材。
實施例2
本實施例所製備的複合材料管材成分為5vol.%Al2O3/2024Al,管材尺寸為外徑500mm、壁厚80mm、長度500mm。
按照圖1所示的製備方法:(1)將Al2O3粉末與2024Al合金粉末按照體積比5:95均勻混合,Al2O3粉末平均粒度d0.5為2μm,2024Al粉末平均粒度d0.5為5μm;混合用鋼球材質為軸承不鏽鋼,規格為Φ10mm,球料重量比為8:1,混料機轉速為40r/min,混合48小時;(2)將各個冷等靜壓包套組件順序組裝,冷壓定形芯模材質選用不鏽鋼,外徑330mm、壁厚6mm、長度520mm;冷壓密封芯模材質材質選用45號鋼,外徑317mm,壁厚16mm;(3)將混合粉末封裝於冷等靜壓包套組件中,封裝順序為:首先用冷壓第一密封卡箍103將冷壓橡膠包套101的一端、冷壓第一密封塞子102和冷壓密封芯模106的一端裝配密封,然後把冷壓定形芯模107裝配到冷壓密封芯模106內部,將複合材料混合粉末108填充到冷壓橡膠包套101和冷壓定形芯模107之間,最後用冷壓第二密封卡箍105將冷壓橡膠包套101的另一端、冷壓第二密封塞子104和冷壓密封芯模106的另一端裝配密封;封裝完成後進行冷等靜壓成型,冷等靜壓壓力為100MPa,冷等靜壓保壓時間為30min;(4)去除管坯外面的冷等靜壓包套組件,得到帶有冷壓定形芯模的管坯;(5)將帶有冷壓定形芯模的管坯封裝入純鋁包套組件中進行高溫真空除氣處理,封裝順序為:首先將金屬包套外筒201和金屬包套內筒202分別與金屬包套第一密封蓋203裝配焊接密封,形成金屬包套第一焊縫207和金屬包套第二焊縫208;然後把帶有冷壓定形芯模的管坯置於金屬包套外筒201和金屬包套內筒202之間;再將金屬包套外筒201和金屬包套內筒202分別與金屬包套第二密封蓋204裝配焊接密封,形成金屬包套第三焊縫209和金屬包套第四焊縫210;最後將金屬包套抽氣管211與金屬包套第二密封蓋204焊接相連,金屬包套抽氣管211與管坯相通;其中,包套厚度為2mm,除氣溫度560℃,除氣升溫速度為50℃/h,封口前真空度為1×10-2Pa;(6)將經高溫真空除氣處理的管坯進行熱等靜壓緻密化,熱等靜壓溫度為560℃,壓力為130MPa,在此溫度壓力下保持3小時;(7)機加工去掉金屬包套和冷壓定形芯模,得到複合材料管材。
實施例3
本實施例所製備的複合材料管材成分為10vol.%B4C/6061Al,管材尺寸為外徑200mm、壁厚20mm、長度1500mm。
按照圖1所示的製備方法:(1)將B4C粉末與6061Al合金粉末按照體積比10:90均勻混合,B4C粉末平均粒度d0.5為20μm,6061Al粉末平均粒度d0.5為75μm;混合用鋼球材質為軸承不鏽鋼,規格為Φ15mm,球料重量比為15:1,混料機轉速為60r/min,混合24小時;(2)將各個冷等靜壓包套組件順序組裝,冷壓定形芯模材質選用不鏽鋼,外徑156mm、壁厚4mm、長度1520mm;冷壓密封芯模材質材質選用45號鋼,外徑147mm,壁厚10mm;(3)將混合粉末封裝於冷等靜壓包套組件中,封裝順序為:首先用冷壓第一密封卡箍103將冷壓橡膠包套101的一端、冷壓第一密封塞子102和冷壓密封芯模106的一端裝配密封,然後把冷壓定形芯模107裝配到冷壓密封芯模106內部,將複合材料混合粉末108填充到冷壓橡膠包套101和冷壓定形芯模107之間,最後用冷壓第二密封卡箍105將冷壓橡膠包套101的另一端、冷壓第二密封塞子104和冷壓密封芯模106的另一端裝配密封;封裝完成後進行冷等靜壓成型,冷等靜壓壓力為180MPa,冷等靜壓保壓時間為24min;(4)去除管坯外面的冷等靜壓包套組件,得到帶有冷壓定形芯模的管坯;(5)將帶有冷壓定形芯模的管坯封裝入純鋁包套組件中進行高溫真空除氣處理,封裝順序為:首先將金屬包套外筒201和金屬包套內筒202分別與金屬包套第一密封蓋203裝配焊接密封,形成金屬包套第一焊縫207和金屬包套第二焊縫208;然後把帶有冷壓定形芯模的管坯置於金屬包套外筒201和金屬包套內筒202之間;再將金屬包套外筒201和金屬包套內筒202分別與金屬包套第二密封蓋204裝配焊接密封,形成金屬包套第三焊縫209和金屬包套第四焊縫210;最後將金屬包套抽氣管211與金屬包套第二密封蓋204焊接相連,金屬包套抽氣管211與管坯相通;其中,包套厚度為3.5mm,除氣溫度530℃,除氣升溫速度為20℃/h,封口前真空度為1×10-2Pa;(6)將經高溫真空除氣處理的管坯進行熱等靜壓緻密化,熱等靜壓溫度為530℃,壓力為100MPa,在此溫度壓力下保持1小時;(7)機加工去掉金屬包套和冷壓定形芯模,得到複合材料管材。