自動上板機雙板上板系統的拉板機構的製作方法
2023-10-19 18:29:37
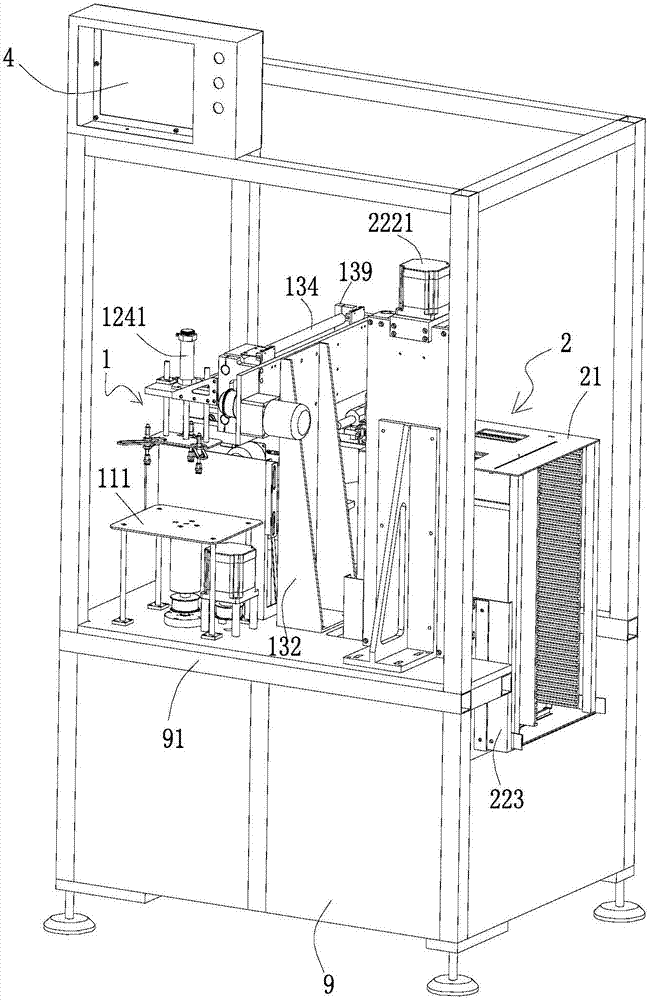
本實用新型涉及自動化領域,特別是一種能適用多種規格PCB板、PCBA板上板自動上板機雙板上板系統的拉板機構。
背景技術:
目前,在PCB板及PCBA板的加工過程中,通常需要人工將待加工的PCB板或PCBA板一塊一塊地上料至工作檯或流水線的軌道上,浪費人力、效率低下,同時操作者手部接觸PCB板、PCBA板,容易造成PCB板或PCBA板的汙染,不利於後續工序的加工,影響產品質量,也嚴重影響生產的自動化進程。針對PCB板的上板,現有技術中也出現了單一的PCB板上板機,但是如果PCB板上板機發生故障,則包括PCB板上板機的整條生產線必須全部停止運行,等待維修,嚴重影響生產效率,造成相關設備的極大浪費,而PCBA板目前則完全依靠手工一片一片上板,效率很低。
技術實現要素:
本實用新型要解決的技術問題是提供一種節約空間、節省人力、提高生產效率、且能適用多種規格PCB板、PCBA板的自動上板機雙板上板系統的拉板機構。
為解決上述技術問題,本實用新型採用以下技術方案:
一種自動上板機雙板上板系統的拉板機構,可將水平放置於上板箱內的PCB板或PCBA板拉到到送板系統上的拉板機構固定於機箱9內水平設置的承重板上;所述上板箱、拉板機構、送板系統沿送板系統上的導軌長度方向依次設置,拉板機構的尾端與送板系統的輸入工位相接;
所述拉板機構包括拉板組件以及豎直設置在承重板上的拉板組件固定架,拉板組件固定架設置在導軌輸入工位的端部且位於導軌外軌的同側。
優選地,所述拉板組件包括第二電機以及固定在拉板組件固定架上部的電機固定架,第二電機的輸出端通過直齒條齒輪與直齒條導軌適配連接,直齒條導軌水平地穿過電機固定架,隨第二電機的正轉、反轉沿導軌長度方向相應的前進或後退,直齒條導軌的遠送板系統端設有拉片固定板,直齒條導軌的近送板系統端設有導軌固定板,可自上板箱中穿過、將放置於卡槽中的PCB板或PCBA板拉到傳送帶上的拉片連接在拉片固定板上,拉片的底端超出拉片固定板底面的長度小於相鄰的兩個卡槽之間的距離。
更優選地,所述電機固定架的下方連接有拉杆固定座,拉杆固定座上開有兩個與直齒條導軌平行的拉杆孔,兩根拉杆活動地穿過對應拉杆孔,拉杆的一端固定在拉片固定板上,另一端固定在導軌固定板上。
更優選地,所述直齒條導軌的內側面為帶直齒條的面。
與現有技術相比,本實用新型自動上板機雙板上板系統的拉板機構具有以下突出的益處:
(1)可將水平放置於上板箱內的PCB板或PCBA板拉到到送板系統上的拉板機構包括拉板組件以及豎直設置在承重板上的拉板組件固定架,拉板組件固定架設置在導軌輸入工位的端部且位於導軌外軌的同側,使得待上板的PCB板或PCBA板自導軌輸入工位進入送板系統。操作員在上板箱內水平放置PCB板或PCBA板之後,上板機可自動進行上板作業,使得PCB板、PCBA板自動上板機的自動上板得以實現,操作員可進行其他工作,極大的節約人工。
(2)拉片可將上下間隔放置的PCB板及PCBA板逐個送到送板系統上,從根本上解決了PCBA板只能人工一片一片上板的問題。
(3)可進行多種寬度規格的PCB板及PCBA板的上板,實用性廣。
本實用新型結構巧妙、替代人力、提高生產效率、可適用多種規格PCB板及PCBA板的自動上板,自動化程度高。
附圖說明
下面結合附圖和具體實施方式對本實用新型作進一步詳細地解釋。
圖1是實施例PCB板、PCBA板自動上板機整體立體示意圖一
圖2是實施例PCB板、PCBA板自動上板機整體立體示意圖二
圖3是實施例中PCB板上板系統、送板系統、雙板上料系統立體示意圖
圖4是實施例中PCB板上板系統、送板系統的立體示意圖一
圖5是實施例中PCB板上板系統、送板系統的立體示意圖二
圖6是實施例中PCB板上板系統立體示意圖
圖7是實施例中PCB板上板系統、送板系統及雙板上料系統去掉上板箱的立體示意圖
圖8是實施例中上板箱的局部立體圖一
圖9是實施例中上板箱的局部立體圖二
圖10是實施例中上板箱的局部立體圖三
圖11是實施例中拉板機構立體示意圖
具體實施方式
如圖1~11所示,一種PCB板、PCBA板自動上板機(簡稱上板機),包括機箱9、僅能將PCB板輸送到送板系統3上的PCB板上板系統1、能將PCB板或PCBA板輸送到送板系統3上的雙板上板系統2、可將運送到其上的PCB板或PCBA板送到下一工序的送板系統3、可輸入及顯示工藝參數等信息的顯示系統4以及PLC控制系統(圖中未示出)。
如圖1、圖2所示,機箱9內設有水平的承重板91,協調上板機各部件配合工作的PLC控制系統設置於機箱9內,位於承重板91下方,顯示系統4與PLC控制系統電通訊連接地設置於機箱9的上方;雙板上板系統2與導軌長度方向一致地設置在承重板91上,雙板上板系統2的輸出工位與送板系統3的輸入工位流水地相接;PCB板上板系統1與導軌長度方向垂直地固定在承重板91上,PCB板上板系統1的輸出工位對應設置於送板系統3輸入工位的上方。
如圖3、圖4所示,所述送板系統3包括設置在承重板91上的送板系統底座31,送板系統底座31上設有寬度可調整的導軌32,導軌32的內側壁上對應設置傳送帶33,所述PCB板或PCBA板可放置於兩條傳送帶33上隨傳送帶33同步運動,導軌32之間的寬度根據需輸送的PCBA板的寬度調整,確保其所輸送的PCBA板不會掉落、不會損壞。
實施例中,導軌32的內軌與送板系統底座31之間設有兩根垂直送板系統3導軌長度方向的滑杆34,每個滑杆34上活動地套設定位塊35,導軌32的內軌固定放置在定位塊35上隨定位塊35同步運動。定位塊35連接PLC控制系統,根據PCB板或PCBA板的寬度,在PLC控制系統的指令下,定位塊35帶動導軌32的內軌在滑杆34上運動或停止,調整導軌32的寬度,以適應多種規格的PCB或PCBA板通過。
如圖3~圖6所示,所述PCB板上板系統1包括底部固定在承重板91上的上料架11、對應設置在上料架11上方的吸板裝置12、以及可帶動吸板裝置12在上料架11的上方與送板系統3輸入工位上方之間往復運動的第一傳送裝置13。
上料架11的上表面為平板111,平板111的一側設有垂直平板111的定位板112,定位板112確保PCB板放置在吸板裝置12可準確吸取的位置。
實施例中,所述第一傳送裝置13包括垂直送板系統3的送料方向設置在承重板91上的第一固定支架132,第一固定板131對應送板系統3及上料架11固定在第一固定支架132的上部,第一固定板131的兩端分別設有C形導杆架139,C形導杆架139的開口端與第一固定板131連接,兩個C形導杆架139之間設有兩根上下對應的、水平的第一導杆134,第一導杆134上套設可沿第一導杆134在送板系統3及上料架11之間往復運動的滑塊135。第一固定板131兩端的同一高度分別設有主動輪136、從動輪137,主動輪136、從動輪137分別設置在第一導杆134兩端的外側,主動輪136、從動輪137之間適配設置第二皮帶,第一電機138輸出端連接主動輪136地固定在第一固定板131上,滑塊135固定在第二皮帶的上層皮帶上,隨第一電機138的正轉、反轉在送板系統3及上料架11之間往復運動。實施例中,主動輪136、從動輪137分別設置在兩個導杆架139的外側,第二皮帶自C形導杆架139的C形空腔內穿過。
第一固定板131上還設有兩個用來感應滑塊135運動起、始位置的第一感應器1314和第二感應器1315,所述第一感應器1314和第二感應器1315為U形,第一感應器1314對應設置在上料架11的上方,第二感應器1315對應設置在送板系統3輸入工位的上方,滑塊135的頂壁裝有水平的第一夾片1313,第一夾片1313的一端連接滑塊135,另一端運行軌跡穿過第一感應器1314、第二感應器1315的U形槽。
如圖6所示,滑塊135的上設有吸板裝置固定板133,吸板裝置固定板133隨滑塊135同步運動,吸板裝置12固定在吸板裝置固定板133上。
所述吸板裝置12包括若干個吸嘴121、與吸嘴121一一對應設置的吸嘴支架122、用來固定吸嘴支架122的吸嘴支架固定板123、以及可帶動吸嘴支架固定板123上下移動的吸嘴豎移組件124。
實施例中,所述吸嘴豎移組件124包括固定在吸板裝置固定板133上的直線氣缸1241,直線氣缸1241內設有可感知氣缸杆運動位置的壓力感應器,直線氣缸1241的氣缸杆穿過吸板裝置固定板133豎直向下地設置,吸嘴支架固定板123固定在氣缸杆的末端,隨氣缸杆的上下往復同步運動。吸嘴支架固定板123的上表面還固定有兩個頂端可活動地穿過吸板裝置固定板133的第三導杆126,兩個第三導杆126與直線氣缸1241的氣缸杆平行地分設於氣缸杆的兩側。確保吸嘴支架固定板123在豎直方向上下直線運動,不發生偏斜。
吸嘴支架122位置可調整地連接在吸嘴支架固定板123上,吸嘴121位置可調整地連接在吸嘴支架122上,即吸嘴121相對吸嘴支架固定板123前、後、左、右的位置均可根據PCB板的大小進行調整,確保吸嘴121接觸PCB板上實心的區域、且能將PCB板順利的吸住;實施例中,兩個(也可為根據需要設置的若干個)吸嘴支架122均為長圓形的金屬框,金屬框的固定端可轉動地連接在吸嘴支架固定板123上,自由端向外伸出吸嘴支架固定板123,每個吸嘴121上間隔設有上下兩個可將吸嘴豎直固定在吸嘴支架122上的定位螺母,吸嘴121穿過金屬框,兩個定位螺母分別貼合金屬框的上端面、下端面,調整兩個定位螺母相對金屬框及相對吸嘴的位置,即可調整吸嘴121沿金屬框移動。根據PCB板的形狀規格,調整金屬框與吸嘴支架固定板123之間的角度、調整吸嘴121在金屬框中的相對位置,以適合多種規格的PCB板的上板。
優選地,吸嘴121接觸PCB板的一端包覆軟膠,另一端連通真空裝置(圖中未示出),所述真空裝置優選為真空泵,吸嘴121在真空裝置工作時可吸起PCB板,在真空裝置停止工作時放開PCB板。
初始狀態下,直線氣缸1241位於待上料的PCB板上方,第一夾片1313位於第一感應器1314的U形槽中。
所述PCB板上板系統1將PCB板輸送到送板系統3的方法如下:
準備工作:
根據PCB板的寬度,在顯示系統4中設置PCB板上板系統1運行的工藝參數,調整導軌32的寬度;
PCB板備料:
將PCB板放置到上料架11的準確位置上,啟動程序開始工作;
PCB板上料:
直線氣缸1241開始工作,氣缸杆向下伸出,帶動固定於氣缸杆上的吸嘴121向下運動,待吸嘴121接觸到PCB板上的實心區域時,直線氣缸1241內的感應器感應氣缸杆已運動到正確位置,真空裝置開始運行,使得PCB板牢固的吸附在吸嘴121上,然後氣缸杆向上縮回帶動吸有PCB板的吸嘴121同步升高,直到與傳送帶33對應的高度;第一電機138開始工作,滑塊135帶動整個直線氣缸1241從第一感應器1314的位置平移到第二感應器1315的位置,當第一夾片1313運動到第二感應器1315的U形槽時,第二感應器1315感應到滑塊135已經運行到正確位置,滑塊135停留在此位置,真空裝置暫停運行,吸嘴121放開其吸附的PCB板放置到送板裝置3上,第一電機138帶動直線氣缸1241從第二感應器1315的位置平移到第一感應器1314的位置,當第一夾片1313運動到第一感應器1314的U形槽時,第一感應器1314感應到滑塊135已經運行到正確位置,第一電機138停止工作,使得滑塊135停留在此位置,PCB板的自動上料過程完成;重複所述PCB板上料運行過程,即可完成多塊PCB板的自動上料。
如圖3、4及圖8~10所示,所述雙板上板系統2包括既可放置PCB板又能放置PCBA板的上板箱21、可帶動上板箱21在豎直方向上下運動的上板箱移動裝置22、以及可將水平放置於上板箱21內的PCB板或PCBA板拉到到送板系統3上的拉板機構23。所述上板箱21、拉板機構23、送板系統3在沿導軌的長度方向上依次設置,拉板機構23的尾端與送板系統3的輸入工位相接。
如圖3、圖8~10所示,所述上板箱21為沿導軌長度方向貫通的框架,上板箱21內設有平行箱體側壁的第一卡板213、第二卡板214,第一卡板213與第二卡板214相對的面上分別對應地開設若干條水平的卡槽219,卡槽219為通槽,PCB板或PCBA板可插在對應的兩個卡槽219中且可卡槽219中穿過,第一卡板213豎直固定在箱體的底板上,第二卡板214位置可調整地設置,調整第二卡板214與第一卡板213之間的距離,上板箱21可適配多種PCB板或PCBA板的寬度。
實施例中,上板箱21的箱體內設有垂直箱底的第一固定架215,第一卡板213豎直固定在第一固定架215上;上板箱21的箱體內設有可供第二卡板214相對第一卡板213移動的物料架212,物料架212包括垂直箱體側壁固定在上板箱21底板上的兩根下帶齒滑道2121,每根下帶齒滑道2121的上方對應設有一端固定在第一卡板213上的上帶齒滑道2125,每對對應的上下帶齒滑道之間設有一根豎直的支撐杆2123,支撐杆2123的上下兩端位置可調整的對應連接在上、下帶齒滑道上,第二卡板214固定在物料架212上。
實施例中,每根支撐杆2123的上下兩端分別設有可在對應的帶齒滑道上反覆解鎖、鎖合的上卡件2124、下卡件2122,上、下卡件解鎖後可沿帶齒滑道水平移動。上、下卡件的頂面及底面具有水平面,上板箱21的底面上適配每一根下帶齒滑道2121設有與帶齒滑道2121平行的下通槽216,上板箱21的頂面上適配每一根上帶齒滑道2125設有與上通槽217,上、下卡件通過可在對應的上下通槽內活動的螺栓位置可調整地連接在上、下帶齒滑道上。第二卡板214豎直固定在下卡件2122的頂面與上卡件2124的底面之間,隨上下卡件在帶齒滑道上同步運動。根據不同PCB板或PCBA板的尺寸,解鎖上卡件2124、下卡件2122,調整上下卡件到對應合適的位置,使雙板上板系統2可適用於多規格的PCB板或PCBA板上板。為保證物料架212的穩固性,兩根支撐杆2123之間設有料架穩固杆2126。
在進行PCB板上板時,可將PCB板依次放置在卡槽219中進行上板,對於帶有較高元件的PCBA板,可間隔一個或兩個卡槽219插入一片PCBA板,確保上下相鄰的PCBA板之間互不碰撞。
如圖3、7、11所示,拉板機構23包括拉板組件232以及豎直設置在承重板91上的拉板組件固定架231,拉板組件固定架231設置在導軌32輸入工位的端部且位於導軌32外軌的同側,拉板組件232固定在拉板組件固定架231上,拉板組件232包括固定在拉板組件固定架231上部、水平設置的電機固定架2321,第二電機2322豎直固定在電機固定架2321上,第二電機2322的輸出端通過直齒條齒輪(圖中未示出)與直齒條導軌2323適配連接,直齒條導軌2323的內側面為帶直齒條面。直齒條導軌2323水平地穿過電機固定架2321,隨第二電機2322的正轉、反轉沿導軌長度方向相應的前進或後退,直齒條導軌2323的遠送板系統端設有垂直直齒條導軌2323端面的拉片固定板2324,直齒條導軌2323的近送板系統端上設有垂直直齒條導軌2323端面的導軌固定板2328,拉片固定板2324上設有底部超出拉片固定板2324的拉片2325,拉片2325可自上帶齒滑道2125的下方穿過上板箱21將放置於卡槽219中的PCB板或PCBA板拉到傳送帶33上,拉片2325超出拉片固定板2324底面的長度小於相鄰的兩個卡槽219之間的距離。
優選地,電機固定架2321的下方連接有拉杆固定座2326,拉杆固定座2326上開有兩個與直齒條導軌2323平行的拉杆孔,兩根拉杆2327活動地穿過對應拉杆孔,拉杆2327的一端固定在拉片固定板2324上,另一端固定在導軌固定板2328上,確保直齒條導軌2323前後運動的過程中保持直線運動。
如圖11所示,上板箱移動裝置22包括放置上板箱21的L形支架223、移動組件222以及豎直設置在承重板91上的移動組件支架221。實施例中,移動組件222包括設置在移動組件支架221頂端的第三電機2221,第三電機2221與PLC控制系統電通訊連接,其輸出端連接豎直的絲杆2222,絲杆2222的底端可轉動地放置在承重板91上,絲杆2222上螺紋連接支架固定塊2223,支架固定塊2223隨絲杆2222的正轉、反轉沿絲杆2222上升或下降,L形支架223隨支架固定塊2223同步運動地固定在支架固定塊2223的側壁上。實施例中,L形支架223的底部向下超過承重板91的下表面,支架固定塊2223上設有分設於絲杆2222兩側的兩個第二導杆孔,移動組件支架221的頂端對應所述第二導杆孔設有兩塊頂板2211,第二導杆2224穿過對應的第二導杆孔固定在頂板2211與承重板91之間,確保支架固定塊2223上下運動過程中保持直線。優選地,移動組件支架221上下對應的設有可感應支架固定塊2223上、下移動最大位置的第三感應器2212和第四感應器2213,所述第三感應器2212和第四感應器2213為U形,支架固定塊2223上裝有第二夾片2225,第二夾片2225的另一端運行軌跡穿過第三感應器2212和第四感應器2213的U形槽。在PLC系統控制下,第三電機2221可將上板箱21中裝有PCB板或PCBA板的凹槽219依次上升到與傳送帶33對應的高度。
實施例中,第三電機2221為步進電機。
所述雙板上板系統2將PCB板或PCBA板輸送到送板系統3的方法如下:
在顯示系統4中設置雙板上板系統2運行的工藝參數。
初始狀態下,帶有拉片2325的直齒條導軌2323的前端自上帶齒滑道2125的下方穿過上板箱21,所述上板箱移動裝置22帶動上板箱21上升至內上板箱21最上方的PCB板或PCBA板與傳送帶33高度對應地放置,拉片2325位於所述PCB板或PCBA板的前方,第二電機2322帶動直齒條導軌2323向後運動,拉片2325將所述PCB板或PCBA板拉動到傳送帶33上流向下一工序,第三電機2221帶動上板箱21上升至下一塊PCB板或PCBA板傳送帶33高度對應地放置,第二電機2322帶動直齒條導軌2323回到初始狀態,重複以上工序,直到將上板箱21內所有PCB板或PCBA板全部傳送到傳送帶33上,第三電機2221帶動上板箱21下降至最低位置,操作員將PCB板PCBA板對應的插入卡槽219中,繼續進行上板作業。