一種輸送高熔點介質保溫型多級超高溫屏蔽泵的製作方法
2023-12-11 23:32:47 2
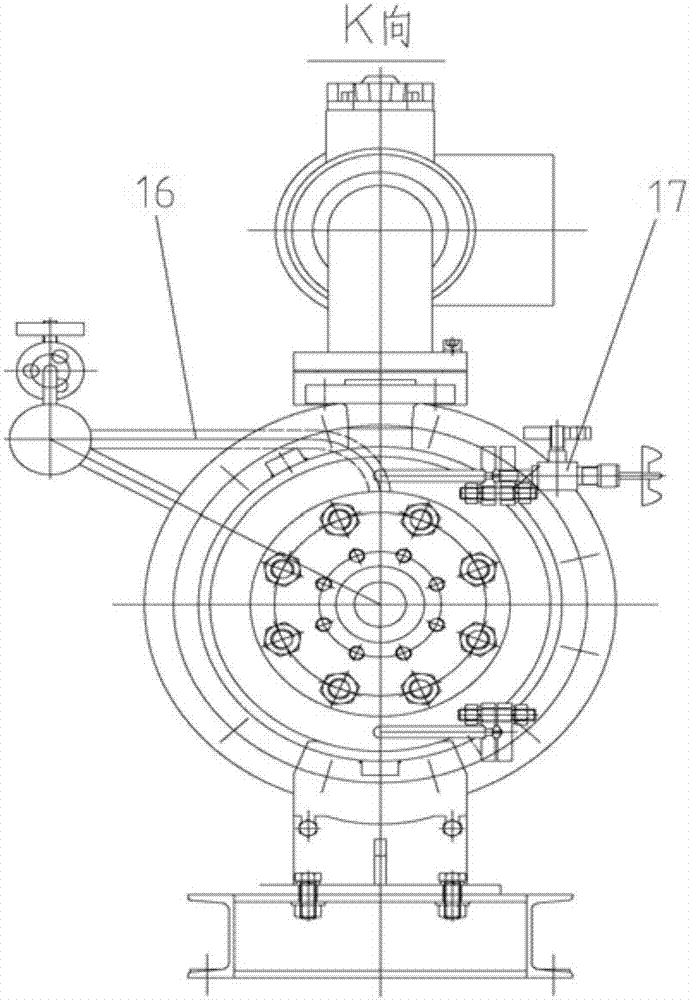
本發明涉及一種輸送高熔點介質保溫型多級超高溫屏蔽泵。
背景技術:
現有技術中,使用多級屏蔽電泵輸送高熔點介質時應選用超耐熱型多級屏蔽泵。超耐熱型多級屏蔽電泵與普通多級泵屏蔽電泵相比較,泵體部分、電機、後軸承座以及循環管需加保溫套以便通蒸汽和熱水,確保內部介質為液態,循環方式與普通多級屏蔽電泵相似:液體從泵入口部分進入,大部分液體由泵出口部分排出,少量液體經過電機內腔,從尾部循環管返回入口。由於其結構要求,採用超耐熱型多級屏蔽電泵的工作現場必須安裝有輸送保溫蒸汽或熱水的配管,配管一端與蒸汽或熱水源頭接口相連,另一端與屏蔽電泵保溫夾套上接口相連。在實際使用過程中,基於現有屏蔽電泵本身結構,加上現場條件的限制,泵在安裝使用時存在以下缺陷:1)、臥式超耐熱多級屏蔽泵結構複雜、保溫配管多、密封結合處多,會影響泵的性能;2)、由於該泵配管多且長,使用空間大,保溫不方便,難度大,成本高。
技術實現要素:
針對現有技術存在的高熔點整體式泵段帶保溫結構超耐熱型多級屏蔽泵結構複雜,零件數量較多,保溫不方便、難度大,增加成本,佔用空間大的問題,本發明提供一種輸送高熔點介質保溫型多級超高溫屏蔽泵,可以完美解決此種情況電泵工作。
本發明解決技術問題採用如下技術方案:
本發明涉及一種輸送高熔點介質保溫型多級超高溫屏蔽泵,包括泵體及與泵體連接的電機,所述泵體包括泵入口、泵前段外筒、泵出口和泵後段外筒,所述泵體內設有第一級葉輪組和第二級葉輪組;所述電機包括前軸承座、後軸承座、接線盒、定子組件、轉子軸和轉子組件;所述轉子軸通過所述前軸承和所述後軸承設於電機體的中心,所述轉子軸的輸出端外伸至泵體內,所述泵體的泵後段外筒的一側法蘭上設有外循環管進口,所述電機體的後軸承座的徑向設有外循環管出口,所述外循環管進口和外循環管出口之間設有連通兩者的外循環管,所述轉子軸後端軸身內設有軸向中心長孔,所述轉子軸後端軸身上設有的徑向十字過液通孔。
優選地,所述中心長孔的一端開口位於轉子軸的後端面且與電機體的後軸承座內腔相通,另一端與所述徑向十字過液通孔連通。
優選地,所述十字過液通孔處的轉子軸軸身上套設加壓副葉輪。
優選地,所述泵體的泵前段外筒的一側法蘭軸上設有第一排氣閥。
優選地,所述電機體的後軸承座的上部一側設有第二排氣閥。
優選地,所述泵前段外筒、泵出口和泵後段焊接為一個整體。
優選地,所述接線盒底座內裝有矽膠,可防止在屏蔽套損壞時,高溫液體進入接線盒內,保護了接線盒。
與現有技術相比,本發明具有如下的有益效果:
(1)本發明所述輸送高熔點介質保溫型多級超高溫屏蔽泵,通過將泵體外筒組件與泵出水段焊接成一個整體,不僅減少了密封結合面的數量,提高了泵的密封性能,而且減少了保溫夾套的數量,進而減少了保溫配管的數量。
(2)通過把泵外筒組件後段法蘭與後軸承座用循環管相連,減少了循環管的長度,另外在轉子軸後部增加副葉輪,二者保證了泵所需循環液的流動暢通。
(3)通過在泵前段外筒法蘭處以及電機後軸承座的高點處設置兩個排氣閥,確保了對泵工作中可能堆積或者產生的氣體進行排除,保證了泵的可靠、安全運行。
(4)本發明所述屏蔽泵使得冷卻電機的循環液順暢回到泵後段外筒法蘭上的循環管入口,防止循環介質氣化,控制回到泵體葉輪低壓區的循環介質的量,防止葉輪汽蝕。
附圖說明
通過閱讀參照以下附圖對非限制性實施例所作的詳細描述,本發明的其它特徵、目的和優點將會變得更明顯:
圖1為本發明所述輸送高熔點介質保溫型多級超高溫屏蔽泵的結構示意圖;
圖2為本發明所述圖1的側視圖;
圖3為本發明所述轉子組件後端部分結構示意圖;
其中圖中標號:1為泵入口、2為泵前段外筒、3為第一級葉輪組、4為泵出口、5為第二級葉輪組、6為泵後段外筒、7為外循環管進口、8為前軸承座、9為定子組件、10為轉子軸、11為轉子組件、12為外循環管出口、13為後軸承座、14為接線盒、15為第二排氣閥、16為外循環管、17為第一排氣閥、18為副葉輪、19為副葉輪蓋板、20為中心長孔、21為十字過液通孔、22為後軸承、23為前軸承。
具體實施方式
下面結合具體實施例,進一步闡述本發明。這些實施例僅用於說明本發明而不用於限制本發明的範圍。
如圖1和圖2所示,本發明優選實施例的一種輸送高熔點介質保溫型多級超高溫屏蔽泵,包括泵體及與泵體連接的電機,泵體主要包括泵入口1,泵前段外筒2,泵出口4,泵後段外筒6,第一級葉輪組3、第二級葉輪組5、套裝在轉子軸10輸出端上;電機部分主要包括定子組件9、轉子組件11和接線盒14,定子組件前、後兩端分別裝有前軸承座8和後軸承座13,在前、後軸承座中分別裝設前軸承22和後軸承23。其中,泵後段外筒6一側法蘭上設有外循環進口7,後軸承座13徑向設有外循環出口12,兩者由外循環管16連通;泵前段外筒2安裝第一排氣閥17;後軸承座13的上部高點處安裝第二排氣閥15。
如圖3所示,轉子組件在轉子軸10的後端沿軸方向鑽有中心長孔20,孔深度到達副葉輪18的安裝位置;副葉輪18安裝在轉子軸10的後部,安裝位置的軸身上設有的徑向十字過液通孔21,中心長孔20的一端開口與電機體的後軸承座內腔相通,另一端與十字過液通孔21連通;以四片葉輪的副葉輪為例,副葉輪18的內側面上均布設有四片副葉片呈十字形排布,副葉輪18的外側面上設有副葉輪蓋板19。
當屏蔽泵工作時,如圖1中箭頭的方向所示,高熔點介質由泵入口進入,通過第一級葉輪組3,到達泵後段外筒6位置處,其中絕大部分液體會經過前軸承座8前方並經過第二級葉輪組5(反葉輪),最終抵達泵出水段的泵出口4。一小部分液體會在泵後段外筒6處分流經過外循環管16,抵達後軸承座13的內腔,並經過軸後段的中心長孔20,從靠近副葉輪18的十字過液通孔21中流出,經過副葉輪18的增壓,流經定子組件和轉子組件的空隙,並從前軸承23的縫隙處流至前軸承座8的前方,再通過外循環管進口處進入外循環管,如此循環。本發明比現有超耐熱多級屏蔽泵,減少了外部逆循環配管長度與保溫配管數量。
副葉輪18對流過的液體增壓,一方面提供循環液體動力,驅動其從副葉輪處流向前軸承座8處,另一方面對液體壓力的增加,使得該液體在流經電機進行冷卻時,受熱情況下,相比現有裝置更不容易氣化。
本發明所述輸送高熔點介質保溫型多級超高溫屏蔽泵通過將泵體外筒組件與泵出水段焊接成一個整體,不僅減少了密封結合面的數量,提高了泵的密封性能,而且減少了保溫夾套的數量,進而減少了保溫配管的數量;通過把泵外筒組件後段法蘭與後軸承座用循環管相連,減少了循環管的長度,另外在轉子軸後部增加副葉輪,二者保證了泵所需循環液的流動暢通;通過在泵前段外筒法蘭處以及電機後軸承座的高點處設置兩個排氣閥,確保了對泵工作中可能堆積或者產生的氣體進行排除,保證了泵的可靠、安全運行;本發明所述屏蔽泵使得冷卻電機的循環液順暢回到泵後段外筒法蘭上的循環管入口,防止循環介質氣化,控制回到泵體葉輪低壓區的循環介質的量,防止葉輪汽蝕。具有較好的應用價值。
以上對本發明的具體實施例進行了描述。需要理解的是,本發明並不局限於上述特定實施方式,本領域技術人員可以在權利要求的範圍內做出各種變形或修改,這並不影響本發明的實質內容。