圓形鋸片及用圓形鋸片加工的方法與流程
2023-12-11 06:15:42 7
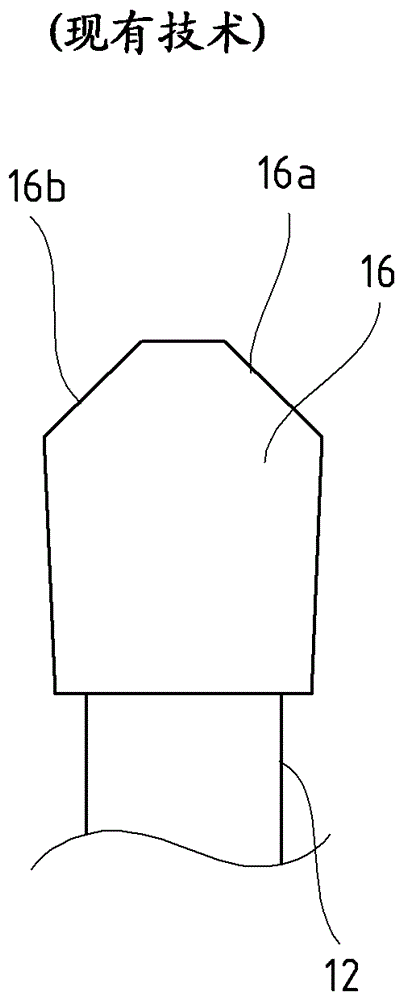
本發明涉及圓形鋸片及用圓形鋸片加工的方法,在使用具有粘結到盤形基底金屬的外周的尖端的圓形鋸片來切割合成樹脂、鋁合金等的工件時,該圓形鋸片能夠高效地抑制切屑沿圓形鋸片的旋轉軸線的方向向右和向左散落。
背景技術:
圓形鋸片普遍作為用於切斷並切割各種材料的工件(在下文中,被稱為「切割加工」)的手段。圓形鋸片包括(1)具有以預定的間隔直接地形成於盤形基底金屬的外周上的切割齒部的圓形鋸片和(2)具有以預定的間隔形成於盤形基底金屬的外周的鋸溝(gullet)且具有在圓形鋸片的單個的鋸溝中沿旋轉方向向後釺焊到基底金屬的尖端的圓形鋸片。尖端的材料可以根據將被切割的各種工件的材料而適當地選自諸如硬質金屬之類的材料,使得圓形鋸片(帶有尖端的鋸片)是本領域中的主流。
現有技術文獻
專利文獻
未經審查的日本專利公開No.2002-347005。
技術實現要素:
發明要解決的問題
在將被設置有尖端的圓形鋸片切割的工件是諸如以合成樹脂或鋁合金作為材料的擠壓型材或拉擠型材之類的空心部件(圓管、方管等)時,切割的聲音不利地非常嘈雜。因此,為了降低切割時的噪聲,使用交替地設置有在一側上使遠端成斜邊的尖端和在兩側上使遠端成斜邊的尖端的圓形鋸片。例如,圖3A至圖3C圖示在圓形鋸片的旋轉方向朝向背部的情況下從前部觀察時的粘結到圓形鋸片的盤形基底金屬12的尖端16,並且,圖3A圖示向右傾斜的右側斜邊16a設置於尖端16的遠端上的狀態。圖3B圖示向左傾斜的左側斜邊16b設置於尖端16的遠端上的狀態,並且,圖3C圖示兩側斜邊16a、16b設置於尖端16的遠端的相應的側面上的狀態。在兩側上成斜邊的尖端16的中心平坦部分具有比單側成斜邊的平坦部分的半徑更大0.2 mm的半徑。
確認到,在使用在上面交替地設置有單側成斜邊的尖端和雙側成斜邊的尖端的圓形鋸片來切割以前面提到的樹脂、鋁合金等作為材料的工件時,顯著地降低切割時的噪聲。該方法對降低噪聲非常有效。然而,有人指出,在切割工件時,切屑沿圓形鋸片的旋轉軸線的方向向右和向左散落,使得大量的切屑到處散落,切屑的散落被假定為起源於圓形鋸片的單個的尖端的遠端的右側斜邊、左側斜邊以及兩側斜邊。尤其是,在將被切割的工件是空心管時,在切割的期間沿圓形鋸片的旋轉軸線的方向向右和向左散落的切屑必然地進入工件的空心部分並殘留在其中。因此,在殘留的切屑從加工過的空心工件掉落之後,有必要進入下一個加工。然而,理想的是,使殘留的切屑的量從一開始就較少,以便減少這樣的麻煩的掉落加工。
而且,即使切屑掉落,靜電也可以防止細小的切屑全部掉落,使得切屑殘留於工件的空心部分中。空心工件內側的這樣的殘留的切屑可能導致在切割之後將塗料塗敷於切割工件或執行精密的後加工時的各種不利的行為。因此,在生產的點上,強烈地要求儘量抑制在用圓形鋸片切割工件時使切屑向右和向左散落的現象。
用於解決問題的方案
為了解決問題並實現期望的目的,權利要求1中所闡述的本發明的要點如下:圓形鋸片具有在沿鋸溝的旋轉方向向後粘結到基底金屬的尖端,該鋸溝在基底金屬的外周以預定的間隔凹入,鋸溝的鋸溝底部呈直線地成形,並且,鋸溝的面向尖端的前刀面的背部部分呈直線地成形,由背部部分相對於經過圓形鋸片的旋轉中心和旋轉方向上的鋸溝底部的前部部分的直線而形成的傾斜角Φ處於-5°與35°之間,由直線鋸溝底部相對於經過圓形鋸片的旋轉中心和旋轉方向上的鋸溝底部的後部部分的直線而形成的傾斜角θ處於45°與100°之間,並且,鋸溝底部的直線長度處於3.5 mm與7.5 mm之間。
根據權利要求1中所闡述的本發明,許可在用圓形鋸片切割時產生的切屑集中地掉落於圓形鋸片的旋轉方向上的正下方,因而有效地抑制切屑沿圓形鋸片的旋轉軸線的方向向右和向左散落的不便。
為了解決與上文的問題類似的問題並實現期望的目的,權利要求2中所闡述的本發明的要點如下:圓形鋸片具有沿鋸溝的旋轉方向向後粘結到基底金屬的尖端,該鋸溝在基底金屬的外周以預定的間隔凹入,鋸溝的鋸溝底部呈直線地成形,鋸溝的面向尖端的前刀面的背部部分呈直線地成形,由背部部分相對於經過圓形鋸片的旋轉中心和旋轉方向上的鋸溝底部的前部部分的直線而形成的傾斜角Φ處於-5°與35°之間,鋸溝中的尖端的前刀面和面向前刀面的背部部分設定為基本上彼此平行,並且,由直線鋸溝底部相對於經過圓形鋸片的旋轉中心和旋轉方向上的鋸溝底部的後部部分的直線而形成的傾斜角θ處於45°與60°之間。
根據權利要求2中所闡述的本發明,許可在用圓形鋸片切割時產生的切屑集中地掉落於圓形鋸片的旋轉方向上的正下方,因而有效地抑制切屑沿圓形鋸片的旋轉軸線的方向向右和向左散落的不便。另外,降低在切割工件時產生的切割聲音。
權利要求3中所闡述的本發明的要點如下:尖端的前刀面具有沿相對於圓形鋸片的旋轉方向而後退的方向凹陷的空心面。
根據權利要求3中所闡述的本發明,除了權利要求1或權利要求2的本發明之外,空心面還形成於尖端的前刀面上,由此更有效地抑制切屑從圓形鋸片向右和向左散落。
權利要求4中所闡述的本發明的要點如下:根據權利要求1至3中的任一項的圓形鋸片切割以鋁合金作為材料的擠壓型材或拉擠型材。
根據權利要求4中所闡述的本發明,有可能顯著地減少切割空心部件時的包括擠壓型材等的空心部件內側的切屑的可能的散落。
發明的效果
本發明證實如下的效果:在用圓形鋸片切割各種材料的工件時,不但降低切割噪聲,而且還高效地抑制切割切屑(切屑)沿圓形鋸片的旋轉軸線的方向向右和向左散落的現象。
附圖說明
圖1A是根據本發明的第一實施例的圓形鋸片的齒部部分的局部放大平面圖,並且,圖1B是圖1A中所圈住的部分的放大圖。
圖2是根據本發明的第二實施例的圓形鋸片的齒部部分的局部放大平面圖。
圖3A至圖3C各自是常規地用於降低切割工件時的噪聲的尖端的「前刀面」的正視圖,圖3A至圖3C圖示應用於尖端的遠端的各種類型的斜邊。
用於執行本發明的模式
接下來,參考附圖而經由優選的實施例來描述根據本發明的圓形鋸片和用圓形鋸片切割工件的加工方法。體現本發明的圓形鋸片是具有在單個的鋸溝中粘結到基底金屬的尖端的上述的所謂的帶有尖端的鋸片。
第一實施例
圖1A和圖1B圖示根據本發明的圓形鋸片10的第一實施例,圓形鋸片10是上文所提到的所謂的帶有尖端的鋸片。即,鋸溝14 在圓形鋸片10的盤形基底金屬12的外周以所要求的間隔凹入,並且,以硬質金屬等作為材料的尖端16釺焊到單個的鋸溝14。尖端16在鋸溝14中粘結到基底金屬12的位置是沿相對於圓形鋸片10的旋轉方向而後退的方向,即沿旋轉方向向後的鋸溝14的徑向延伸的部分。
在根據本發明的圓形鋸片10中,鋸溝14中的鋸溝底部18和背部部分20 (稍後將對此進行描述)中的每個都配置成呈直線地延伸。換句話說,關於凹入基底金屬12中的鋸溝14,被稱為鋸溝底部18的離圓形鋸片的旋轉中心最近的底部以所要求的距離沿切向方向呈直線地延伸。鋸溝底部18中的該直線距離D (從前部部分24至後部部分26的距離,稍後將對此進行描述)優選處於3.5 mm與7.5 mm之間。關於鋸溝14,被稱為背部部分20的面向粘結到基底金屬12的尖端16的前刀面22的部分也以預定的距離呈直線地延伸。背部部分20的上端與尖端16的粘結到沿圓形鋸片的旋轉方向設置的下一個鋸溝14的粘結部分連續。前刀面22是用來在圓形鋸片10的尖端16的旋轉方向前面擦過(rake)切屑的面。
而且,根據第一實施例,從各種實驗的結果證明,將由呈直線地延伸的背部部分20相對於經過圓形鋸片10的旋轉中心的直線而形成的傾斜角規定為某一範圍,由此,能夠將切割工件時所產生的切屑的散落方向控制成屬於有利的散落範圍內。即,由背部部分20相對於直線L1而形成的傾斜角Φ選自-5°至35°的範圍,其中,直線L1經過圓形鋸片10的旋轉軸線(未示出)的中心和鋸溝底部18處的旋轉方向(稍後將描述)上的前部部分24。在實施例中,由背部部分20相對於直線L1而形成的傾斜角Φ是34°。另外,由鋸溝14的直線鋸溝底部18相對於直線L2而形成的傾斜角θ處於45°與100°之間,其中,直線L2經過圓形鋸片的旋轉中心和鋸溝底部18處的旋轉方向上的後部部分26。
參考圖1B而描述上文所提到的「前部部分24」。圖1B是圖1A中的鋸溝14的所圈住的部分的放大圖,並且,鋸溝底部18的作為直線的向右延伸線與背部部分20的也作為直線的向下延伸線的交叉區域被稱為「前部部分24」。因此,直線L1被限定為經過圓形鋸片10的旋轉中心和前部部分24的直線,該前部部分24是鋸溝底部18與背部部分20的個別的延伸線的交叉區域。
在第一實施例的圓形鋸片10中,如從上文顯而易見的,鋸溝14處的鋸溝底部18和背部部分20以預定的距離呈直線地延伸,由背部部分20相對於直線L1而形成的傾斜角Φ設定於-5°至35°的範圍內,其中,直線L1經過圓形鋸片的旋轉中心和鋸溝底部18處的旋轉方向上的前部部分24,由鋸溝14的直線鋸溝底部18 相對於直線L2而形成的傾斜角θ設定為45°至100°,其中,直線L2經過圓形鋸片的旋轉中心和鋸溝底部18處的旋轉方向上的後部部分26,並且,鋸溝底部18的長度D設定為 3.5 mm至7.5 mm,由此與圖3A至圖3C中所圖示的常規的圓形鋸片相比,殘留於例如以鋁合金作為材料的空心工件的內側的切屑的散落量減少92%。換句話說,用圓形鋸片10切割工件的過程導致工件的切屑集中地掉落於圓形鋸片10的旋轉方向的正下方,因而高效地抑制切屑沿圓形鋸片的旋轉軸線的方向向右散落和向左散落的現象。
所謂的空心面沿相對於圓形鋸片10的旋轉方向而後退的方向形成於圖1A中所圖示的尖端16的前刀面22上。如段落[0003]中的專利文獻1中所描述的,當從外周的退刀側(escaping side)沿與前刀面22平行的方向觀察尖端16時,該空心面是尖端16的如下的牙痕:通過在前刀面22形成左右對稱的凹痕,從而形成為大體上弓狀的前刀面。而且,在根據第一實施例的圓形鋸片10的尖端16的前刀面22上形成空心面的過程能夠減少以99%的高效率切割例如以鋁合金作為材料的工件時的切屑的散落量。
實驗
使用外徑為510 mm、尖端的鋸溝寬度為3.5 mm且鋸溝的數量為100的帶有尖端的鋸片,以旋轉速度3600 rpm和進給速度6m/min切割厚度為50 mm x 1.5 mm的鋁合金制方管。在切割之後,測量殘留於每個方管中的切屑的總重量,並且,對測量結果進行比較。
表1
。
考慮
在鋸溝的鋸溝底部設定為直線且旋轉方向上的向前傾斜角Φ設定於-5°至35°的範圍內時,由於卡門渦流(Karman's vortex)(稍後將描述)而導致切屑殘留於鋸溝中,使得防止切屑散落的效果變高。確認到,鋸溝底部處的有利的直線長度(從前部部分至後部部分的長度)是3.5mm至7.5 mm。
第二實施例
圖2圖示根據本發明的圓形鋸片10的第二實施例,其基本配置與第一實施例的上述的配置相同。根據第二實施例的圓形鋸片10的尺寸以這樣的方式設定,使得在鋸溝14粘結到基底金屬12的尖端16的前刀面22與各自面向前刀面22的背部部分20基本上彼此平行,其中,鋸溝14位於前刀面22與背部部分20之間。在這種情況下,尖端16的基本上彼此平行的前刀面22與背部部分20之間的分離距離優選處於3.5 mm與7.5 mm之間;並且,在該實施例中,距離是7.2 mm。
而且,根據第二實施例的圓形鋸片10通過將由鋸溝14處的鋸溝底部18和經過圓形鋸片10的旋轉中心的直線形成的傾斜角規定為某一範圍,從而能夠將切割工件時所產生的切屑的散落方向控制成屬於有利的散落範圍內。即,由鋸溝14的鋸溝底部18相對於直線 L2而形成的傾斜角θ選自45°至60°的範圍,其中,直線 L2經過圓形鋸片10的旋轉軸線(未示出)的中心和鋸溝底部18處的旋轉方向(與旋轉方向相反的方向)上的後部部分26。在該實施例中,傾斜角θ是52.5°。
在第二實施例的圓形鋸片10中,如從上文顯而易見的,鋸溝14處的尖端16的前刀面22和面向前刀面22的背部部分20設定為基本上彼此平行,並且,由鋸溝14的鋸溝底部18相對於經過圓形鋸片的旋轉中心和鋸溝底部18處的旋轉方向上的後部部分26的直線 L2形成的傾斜角θ設定為45°至60°,導致與圖3A至圖3C中所圖示的常規的圓形鋸片相比,殘留於鋁合金制工件內側的切屑的散落量有可能減少90%。與不具有尖端的基底金屬相比,第一實施例中的怠速噪聲是94 dB,然而,第二實施例中的怠速噪聲降低至92 dB。
而且,如第一實施例的所圖示的圓形鋸片10中那樣在尖端16的前刀面22上形成空心面的結構能夠將前面提到的鋁合金的工件的切屑的散落量減少至97%。
應當注意到,圖2中的尖端16的前角是5°至25°。對於該實施例的圓形鋸片10,前角是10°。
實驗
使用外徑為510 mm、尖端的鋸溝寬度為3.5 mm且鋸溝的數量為100的帶有尖端的鋸片來以旋轉速度3600 rpm和進給速度6m/min切割厚度為50 mm x 1.5 mm的鋁合金制方管。在切割之後,測量殘留於每個方管中的切屑的總重量,並且,對測量結果進行比較。
表2
。
考慮
在鋸溝的鋸溝底部設定為直線且旋轉方向上的向前傾斜角Φ設定於-5°至35°的範圍內時,由於卡門渦流(稍後將描述)而導致切屑殘留於鋸溝中,使得防止切屑散落的效果變高。確認到,鋸溝底部處的有利的直線長度(從前部部分至後部部分的長度)是3.5 mm至7.5 mm。
看來,第一實施例和第二實施例的圓形鋸片10的使用能夠降低切屑沿圓形鋸片10的旋轉軸線的方向向右和向左散落的比率,以有效地控制由於卡門渦流而導致的散落方向。「卡門渦流」在學術上被解釋為如下的流體行為:隨著柱狀物體以適當的速度移動於流體中,從該物體的右側和左側產生反向的渦流,這兩個渦流整齊地對準成兩條線。在本發明的情況下,雖然將被圓形鋸片10切割的工件當然是固體,但由於切割加工而產生的大量的切屑的集合體可以被認為是流體。因此,看來,切割切屑作為流體而停留於圓形鋸片10的鋸溝14中,但第一實施例和第二實施例中所規定的圓形鋸片10的鋸溝14的形狀導致隨著圓形鋸片10旋轉而在鋸溝14中產生卡門渦流,由此抑制切屑沿圓形鋸片10的旋轉軸線的方向向右和向左散落。確認到,切割工件時的噪聲也被抑制得較低。
如從上文顯而易見的,根據本發明的圓形鋸片高效地抑制切割工件時所產生的切屑從圓形鋸片向右和向左散落,使得在將被切割的物體是空心工件時,例如,有可能顯著地減少切屑在工件的空心部分內側的不理想的散落和切屑在其中的殘留。
參考標號的描述
12 基底金屬
14 鋸溝
16 尖端
18 鋸溝底部
20 背部部分
22 前刀面
24 前部部分
26 後部部分
L1、L2 直線。