一種自動金屬制粉裝置及方法與流程
2023-09-18 08:56:00 3
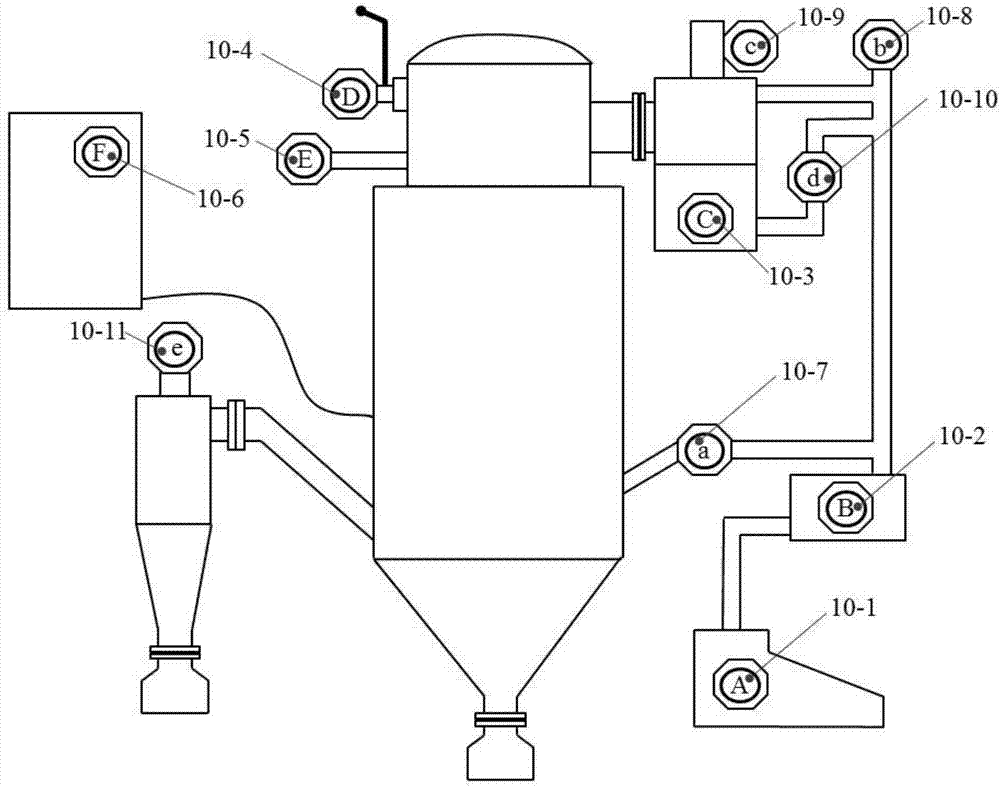
本發明屬於3d列印增材製造領域以及粉末冶金領域,具體涉及一種自動金屬制粉裝置及方法。
背景技術:
金屬粉末是材料產業的重要分支,因粉末具有大的比表面積和特殊的表面性能,其理化性質與普通材料有很大差異,利用金屬粉末,可以製備出性能優異的工件。因此,金屬粉末在冶金、能源、電子、醫療、航空航天等領域的應用日益擴大。3d列印技術的革新,使得製造領域對金屬粉末的需求更為迫切,金屬粉末已成為一類重要的工業原料。與此同時,對粉末的性能要求也不斷提高,高性能的金屬粉末應用而生。高性能的金屬粉末具有質量好、成本低等特點。目前,金屬粉末質量評價指標主要有球形度、粒度、純度、流動性。球形度佳、粒度範圍窄可以保證在3d列印過程中,熔融的金屬顆粒保持基本相同的狀態,否則,太大的顆粒在列印時仍處於固態,太小的顆粒則早已蒸發;純度高的粉末不僅可以保證金屬成形部件的質量,還有助於保證成形過程的可靠性和穩定性;流動性好的粉末更有利於在3d列印過程中粉末的均勻鋪設。然而,質量好的金屬粉末需要採用先進的製備技術才能獲得,國內目前的霧化制粉技術水平與國外差距較大,加之實際生產過程中,操作人員的技能水平差異,導致生產的粉末質量參差不齊,同一生產商生產不同批次粉末質量的穩定性難以保證,不同生產商生產的粉末質量更是千差萬別。致使大量高性能金屬粉末依賴進口,成本居高不下,嚴重製約國內金屬3d列印增材製造行業的發展。
降低金屬粉末的生產成本、提高粉末質量的穩定性,將利於3d列印向應用領域的拓展,推動工業領域的規模化生產。為助力3d列印增材製造產業的發展,提高金屬粉末的製備水平及工藝、降低粉末的生產成本具有重要的現實意義。本發明提供一種自動金屬制粉裝置及方法,實現了制粉工序的自動化,避免了人工操作造成的粉末品質不穩定,提高了粉末質量的穩定性,同時減少了實際生產過程人員的投入、縮短了各工序的操作時間,從而提高了生產效率。
技術實現要素:
本發明的其中一個目的是提出一種自動金屬制粉裝置及方法,解決了現有技術存在生產效率低下的技術問題。本發明提供的諸多技術方案中的優選技術方案所能產生的諸多技術效果詳見下文闡述。
為實現上述目的,本發明提供了以下技術方案:
一種自動金屬制粉裝置,包括用於熔鍊金屬的熔煉室,以及設置在所述熔煉室下部的霧化室,所述霧化室底部設置有粗粉收集罐,與所述霧化室連通設置有旋風分離器,所述旋風分離器底部設置有細粉收集罐;還包括通過線路總成對所述自動金屬制粉裝置進行控制的控制系統。
優選地,還包括依次串聯的機械泵、羅茨泵與擴散泵,以及管路總成,所述管路總成包括:
連接所述機械泵與所述羅茨泵的第一管路;
連接所述羅茨泵與所述擴散泵的第二管路;
連通所述擴散泵與所述熔煉室的第三管路;
連通所述擴散泵與所述第二管路的第四管路;
連接所述霧化室與所述第二管路的第五管路。
優選地,所述控制系統包括:
用於啟動所述自動金屬制粉裝置的按鈕總成;
還包括對所屬機械泵進行控制的機械泵控制模塊、對所述擴散泵進行控制的進行控制的擴散泵控制模塊以及對所述羅茨泵進行進行控制的羅茨泵控制模塊。
優選地,所述第五管路上設置有第三真空閥;所述第二管路連接所述擴散泵的一端至所述第四管路連接所述第二管路的一端之間設置有第二真空閥;所述第四管路上設置有第四真空閥;所述擴散泵上設置有第一真空閥。
優選地,還包括與所述熔煉室聯通設置的充氣檢測閥,以及用於控制所述熔煉室啟停的熔煉控制模塊。
優選地,所述旋風分離器上設置有排氣檢測閥。
優選地,還包括用於對放置在熔煉室中的金屬液滴旋轉的旋轉機構總成。
本發明還提供了一種自動金屬制粉方法,包括:
s10裝料完成後,通過控制系統的按鈕總成啟動設備;
s21控制系統向機械泵控制模塊、擴散泵控制模塊發出啟動信號,機械泵啟動,擴散泵預熱。延時第一時間後,機械泵控制模塊向控制系統反饋信號;
s22控制系統接收機械泵控制模塊的延時反饋型號,向第一真空檢測-閥控制總成、第一真空閥控制總成發出啟動信號,第二真空閥、第三真空閥開啟,機械泵開始對設備抽真空。真空抽至500pa,第一真空檢測-閥控制總成向控制系統反饋信號;
s23控制系統接收第一真空檢測-閥控制總成的真空度反饋型號,向第二真空閥控制總成、羅茨泵控制模塊發出啟動信號,第四真空閥開啟,羅茨泵開始對設備抽真空;真空抽至5pa以下,第一真空檢測-閥控制總成向控制系統反饋信號。
s24控制系統接收第一真空檢測-閥控制總成的真空度反饋型號,向第二真空檢測-閥控制總成、擴散泵發出啟動信號,第一真空閥開啟,擴散泵9開始對設備抽真空。真空抽至6.63×10-3pa以下,第二真空檢測-閥控制總成向控制系統10反饋信號。
優選地,還包括:
s30控制系統接收第二真空檢測閥控制總成的真空度反饋型號,向充氣檢測閥控制總成發出啟動信號,充氣檢測閥控制總成開啟充氣檢測閥,向設備內充入惰性氣體。氣體充入量達0.06mpa,充氣檢測閥控制總成向控制系統反饋信號。
s40控制系統接收充氣檢測閥控制總成的壓強反饋型號,向熔煉控制模塊發出啟動信號,熔煉室內加熱裝置啟動,開始熔鍊金屬棒料;同時,熔煉控制模塊對金屬的熔煉溫度進行監測,經過系統預設的熔煉時間後,熔煉控制模塊向控制系統反饋信號。
優選地,還包括:
s51控制系統接收熔煉控制模塊的溫度、時間反饋信號,向充氣檢測閥控制總成、排氣檢測閥控制總成發出啟動信號。充氣檢測閥控制總成開啟霧化氣管路,高壓氣路通過霧化器向設備內充入出口壓強在1~5mpa的惰性氣體,排氣檢測閥控制總成開啟引風,將霧化工作氣體排出;
s52充氣檢測閥控制總成、排氣檢測閥控制總成向控制系統反饋信號,同時監測霧化器出口氣體壓強和/或流量和/或時間;
s53控制系統接收到充氣檢測閥控制總成、排氣檢測閥控制總成的反饋信號,向旋轉機構總成發出信號;
s60熔煉控制模塊向控制系統反饋裝料重量的監測信號,金屬液流至裝料重量的3%,控制系統依次向各功能模塊發出以上步驟的反向指令,設備停機。
基於上述技術方案,本發明實施例至少可以產生如下技術效果:
本發明提供的金屬制粉裝置,通過控制系統對人工操作進行自動控制,提高了金屬制粉的生產效率。
附圖說明
此處所說明的附圖用來提供對本發明的進一步理解,構成本申請的一部分,本發明的示意性實施例及其說明用於解釋本發明,並不構成對本發明的不當限定。在附圖中:
圖1為本發明實施例所提供的自動金屬制粉裝置的示意圖;
圖2為本發明實施例所提供的裝置控制系統分布的示意圖;
圖3為本發明實施例所提供的自動金屬制粉裝置控制方法的控制框圖。
附圖標記:熔煉室1;霧化室2;旋風分離器3;細粉收集罐4;粗粉收集罐5;機械泵6;羅茨泵7;管路總成8;第一管路8-1;第二管路8-2;第三管路8-3;第四管路8-4;第五管路8-5;擴散泵9;控制系統10;機械泵控制模塊10-1;羅茨泵控制模塊10-2;擴散泵控制模塊10-3;熔煉控制模塊10-4;充氣檢測閥控制總成10-5;按鈕總成10-6;第一真空檢測-閥控制總成10-7;第一真空閥控制總成10-8;第二真空檢測-閥控制總成10-9;第二真空閥控制總成10-10;排氣檢測閥控制總成10-11;線路總成11;旋轉機構總成12;第一真空閥13;第二真空閥14;第三真空閥15;第四真空閥16。
具體實施方式
下面可以參照附圖圖1~圖3以及文字內容理解本發明的內容以及本發明與現有技術之間的區別點。下文通過附圖以及列舉本發明的一些可選實施例的方式,對本發明的技術方案(包括優選技術方案)做進一步的詳細描述。需要說明的是:本實施例中的任何技術特徵、任何技術方案均是多種可選的技術特徵或可選的技術方案中的一種或幾種,為了描述簡潔的需要本文件中無法窮舉本發明的所有可替代的技術特徵以及可替代的技術方案,也不便於每個技術特徵的實施方式均強調其為可選的多種實施方式之一,所以本領域技術人員應該知曉:可以將本發明提供的任一技術手段進行替換或將本發明提供的任意兩個或更多個技術手段或技術特徵互相進行組合而得到新的技術方案。本實施例內的任何技術特徵以及任何技術方案均不限制本發明的保護範圍,本發明的保護範圍應該包括本領域技術人員不付出創造性勞動所能想到的任何替代技術方案以及本領域技術人員將本發明提供的任意兩個或更多個技術手段或技術特徵互相進行組合而得到的新的技術方案。
本發明實施例提供了一種自動金屬制粉裝置及方法。
下面結合圖1~圖3對本發明提供的技術方案進行更為詳細的闡述。
如圖1~圖2所示,本發明實施例所提供的一種自動金屬制粉裝置,包括用於熔鍊金屬的熔煉室1,以及設置在熔煉室1下部的霧化室2,霧化室2底部設置有粗粉收集罐5,與霧化室2連通設置有旋風分離器3,旋風分離器3底部設置有細粉收集罐4;還包括通過線路總成11對自動金屬制粉裝置進行控制的控制系統10。本發明提供的金屬制粉裝置,避免了人工操作造成的粉末品質不穩定,提高了粉末質量的穩定性。還包括依次串聯的機械泵6、羅茨泵7與擴散泵9,以及管路總成8,管路總成8包括:連接機械泵6與羅茨泵7的第一管路8-1;連接羅茨泵7與擴散泵9的第二管路8-2;連通擴散泵9與熔煉室1的第三管路8-3;連通擴散泵9與第二管路8-2的第四管路8-4;連接霧化室2與第二管路8-2的第五管路8-5。其中,控制系統10包括:用於啟動自動金屬制粉裝置的按鈕總成;還包括對所屬機械泵6進行控制的機械泵控制模塊10-1、對擴散泵9進行控制的進行控制的擴散泵控制模塊10-3以及對羅茨泵7進行進行控制的羅茨泵控制模塊10-2。
第五管路8-5上設置有第三真空閥15;第二管路8-2連接擴散泵9的一端至第四管路8-4連接第二管路8-2的一端之間設置有第二真空閥14;第四管路8-4上設置有第四真空閥16;擴散泵9上設置有第一真空閥13。還包括與熔煉室1聯通設置的充氣檢測閥,以及用於控制熔煉室1啟停的熔煉控制模塊。
自動金屬制粉裝置的工作過程是,s10裝料完成後,通過控制系統10的按鈕總成10-6啟動設備;
s21控制系統10向機械泵控制模塊10-1、擴散泵控制模塊10-3發出啟動信號,機械泵6啟動,擴散泵9預熱。延時第一時間後,機械泵控制模塊10-1向控制系統10反饋信號;第一時間可以設置為10-15s;
s22控制系統10接收機械泵控制模塊10-1的延時反饋型號,向第一真空檢測-閥控制總成10-7、第一真空閥控制總成10-8發出啟動信號,第二真空閥14、第三真空閥15開啟,機械泵6開始對設備抽真空。真空抽至500pa,第一真空檢測-閥控制總成10-7向控制系統10反饋信號;
s23控制系統10接收第一真空檢測-閥控制總成10-7的真空度反饋型號,向第二真空閥控制總成10-10、羅茨泵控制模塊10-2發出啟動信號,第四真空閥16開啟,羅茨泵7開始對設備抽真空。真空抽至5pa以下,第一真空檢測-閥控制總成10-7向控制系統10反饋信號。
s24控制系統10接收第一真空檢測-閥控制總成10-7的真空度反饋型號,向第二真空檢測-閥控制總成10-9、擴散泵9發出啟動信號,第一真空閥13開啟,擴散泵9開始對設備抽真空。真空抽至6.63×10-3pa以下,第二真空檢測-閥控制總成10-9向控制系統10反饋信號。
這樣就可以通過設備自動完成抽真空的流程。進一步地,在旋風分離器3上設置有排氣檢測閥。還包括用於對放置在熔煉室1中的金屬液滴旋轉的旋轉機構總成12。
為了進一步完成自動反充保護氣體的步驟,還包括以下步驟,s30控制系統10接收第二真空檢測-閥控制總成10-9的真空度反饋型號,向充氣檢測閥控制總成10-5發出啟動信號,充氣檢測閥控制總成10-5開啟充氣檢測閥,向設備內充入惰性氣體。氣體充入量達0.06mpa,充氣檢測閥控制總成10-5向控制系統10反饋信號。
為了進一步完成熔煉的步驟,還包括以下步驟,s40控制系統10接收充氣檢測閥控制總成10-5的壓強反饋型號,向熔煉控制模塊10-4發出啟動信號,熔煉室1內加熱裝置啟動,開始熔鍊金屬棒料;同時,熔煉控制模塊10-4對金屬的熔煉溫度進行監測,經過系統預設的熔煉時間後,熔煉控制模塊10-4向控制系統10反饋信號。
為了進一步完成霧化制粉的步驟,還包括以下步驟,s51控制系統10接收熔煉控制模塊10-4的溫度、時間反饋信號,向充氣檢測閥控制總成10-5、排氣檢測閥控制總成10-11發出啟動信號。充氣檢測閥控制總成10-5開啟霧化氣管路,霧化氣管路設置在充氣檢測閥控制總成中10-5連接到熔煉室1的管路,霧化氣管路具有高、低壓充氣功能,高壓實現霧化,出口壓強在1~5mpa的惰性氣體,低壓充入保護氣體,氣體充入量達0.06mpa。高壓氣路通過霧化器向設備內充入出口壓強在1~5mpa的惰性氣體,排氣檢測閥控制總成10-5開啟引風,將霧化工作氣體排出;
s52充氣檢測閥控制總成10-4、排氣檢測閥控制總成10-5向控制系統10反饋信號,同時監測霧化器出口氣體壓強和/或流量和/或時間;
s53控制系統10接收到充氣檢測閥控制總成10-4、排氣檢測閥控制總成10-5的反饋信號,向旋轉機構總成12發出信號;
此外,還設置了設備自動停機的步驟,s60熔煉控制模塊10-4向控制系統10反饋裝料重量的監測信號,金屬液流至裝料重量的3%,控制系統10依次向各功能模塊發出以上步驟的反向指令,設備停機。
上述本發明所公開的任一技術方案除另有聲明外,如果其公開了數值範圍,那麼公開的數值範圍均為優選的數值範圍,任何本領域的技術人員應該理解:優選的數值範圍僅僅是諸多可實施的數值中技術效果比較明顯或具有代表性的數值。由於數值較多,無法窮舉,所以本發明才公開部分數值以舉例說明本發明的技術方案,並且,上述列舉的數值不應構成對本發明創造保護範圍的限制。
如果本文中使用了「第一」、「第二」等詞語來限定零部件的話,本領域技術人員應該知曉:「第一」、「第二」的使用僅僅是為了便於描述上對零部件進行區別如沒有另行聲明外,上述詞語並沒有特殊的含義。
同時,上述本發明如果公開或涉及了互相固定連接的零部件或結構件,那麼,除另有聲明外,固定連接可以理解為:能夠拆卸地固定連接(例如使用螺栓或螺釘連接),也可以理解為:不可拆卸的固定連接(例如鉚接、焊接),當然,互相固定連接也可以為一體式結構(例如使用鑄造工藝一體成形製造出來)所取代(明顯無法採用一體成形工藝除外)。
另外,上述本發明公開的任一技術方案中所應用的用於表示位置關係或形狀的術語除另有聲明外其含義包括與其近似、類似或接近的狀態或形狀。本發明提供的任一部件既可以是由多個單獨的組成部分組裝而成,也可以為一體成形工藝製造出來的單獨部件。
最後應當說明的是:以上實施例僅用以說明本發明的技術方案而非對其限制;儘管參照較佳實施例對本發明進行了詳細的說明,所屬領域的普通技術人員應當理解:依然可以對本發明的具體實施方式進行修改或者對部分技術特徵進行等同替換;而不脫離本發明技術方案的精神,其均應涵蓋在本發明請求保護的技術方案範圍當中。