一種高精度極高頻率彎波導加工方法與流程
2023-11-12 03:05:27 2
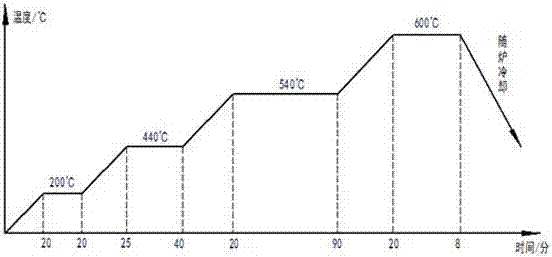
本發明涉及彎波導加工的技術領域,特別是一種高精度極高頻率彎波導加工方法。
背景技術:
對於極高頻率波導,bj900/wr10波導頻率為73.8g~112g,波導口徑為2.54×1.27mm的鋁波導,由于波導口徑極小,無法進行有效的扭彎。超小口徑極高頻波導主要應用於毫米波頻段的電子器件,毫米波波速窄,解析度高,可用頻帶寬,抗多徑效應和抗幹擾能力強,制導精確等,因此要求波導腔體內壁粗糙度低,內腔尺寸和位置精度高。
然而,彎波導結構具有一定的特殊性,其結構尺寸,表面質量和位置精度很難保證,利用傳統方法加工無法達到設計的特殊要求。傳統彎波導製作一般採用加入填充材料或加熱扭彎,在扭彎時會引起波導管截面尺寸發生變化,波導尺寸精度和內腔表面粗糙度很難保證。填充材料扭彎波導成品率低,波導管內外表面容易氧化,高溫時難以實現手工裝夾,並且扭彎操作時需要控制降溫的時間,導致口徑尺寸很難控制,變形的隨意性較大,腔體內的填充材料扭彎後又難清洗乾淨。超小口徑波導與法蘭盤採用傳統火焰釺焊時,由於火焰釺焊集中加熱,波導和法蘭盤尺寸較小,極易發生焊接變形,焊接變形大,無法保證波導口徑尺寸。
技術實現要素:
本發明的目的在於克服現有技術的缺點,提供一種保證波導裝配精度、簡化大量的生產工序、提高生產效率、波導型腔內壁表面粗糙度低、防腐性能高、減小焊接變形的高精度極高頻率彎波導加工方法。
本發明的目的通過以下技術方案來實現:一種高精度極高頻率彎波導加工方法,它包括以下步驟:
s1、上蓋板的加工:水切割備料;數控粗銑備料的六個面;在備料底表面銑削加工出上部型腔,並預留加工餘量2~5mm;在250~280℃溫度下進行退火處理以消除應力;採用線切割精切上部型腔;數控精銑備料六個面;在備料的底表面精銑加工出繞上部型腔環形布置的凹槽;去毛刺;最終實現上蓋板的加工;
s2、下蓋板的加工:水切割備料;數控粗銑備料的六個面;在備料頂表面銑削加工出下部型腔,並預留加工餘量2~5mm;在250~280℃溫度下進行退火處理以消除應力;採用線切割精切下部型腔;數控精銑備料六個面;在備料的頂表面精銑加工出繞下部型腔環形布置且與凹槽相配合的凸肩;去毛刺;最終實現下蓋板的加工;
s3、上下蓋板焊前表面處理:將步驟s1中的上蓋板和步驟s2中的下蓋板放入溫度為60~80℃、濃度為8~10%的naoh水溶液中浸蝕1~2min;鹼洗結束後利用熱水反覆衝洗上蓋板和下蓋板;衝洗結束後放入由濃度為10%的hno3溶液和濃度為0.25%的hf溶液組成的混合液中浸蝕3~5min;浸蝕結束後利用冷水反覆衝洗上蓋板和下蓋板;衝洗結束後對上下蓋板進行烘乾處理;最終實現上下蓋板焊前表面處理;
s4、釺料的製作:根據高彎波導內腔尺寸,採用雷射切割製作釺料,釺料選用0.05mm厚度規格,釺料的外形尺寸與彎波導內腔尺寸一致並確保釺料能夠平整均勻的鋪展在上蓋板和下蓋板之間;
s5、焊前裝配:將釺料放置於上蓋板與下蓋板相接觸位置;將下蓋板的凸肩裝配於上蓋板的凹槽內以自動定位,保證了後續焊接精度,裝配後形成波導,其中上部型腔與下部型腔構成波導型腔,實現了焊前波導的裝配;
s6、真空釺焊:將步驟s5中裝配好的波導放入真空鋁釺焊爐內;利用工裝夾具裝配波導;設定真空釺焊溫度工藝曲線;將真空鋁釺焊爐抽粗真空隨後抽高真空;按設定真空釺焊溫度工藝曲線對波導和釺料加熱;在600℃溫度下保溫8min;保溫結束後隨爐冷卻,實現上蓋板與下蓋板連為一體,最終實現真空釺焊;
s7、真空釺焊完成後對波導進行線切割外形、數銑加工外形,加工出法蘭盤,最終加工出高精度極高頻率彎波導。
本發明具有以下優點:
(1)本發明打破彎波導傳統的工藝設計方法,放棄由標準波導組合焊接形式,本發明將彎波導拆分為由上蓋板和下蓋板,彎波導的波導型腔尺寸和外導體尺寸均由上蓋板和下蓋板構成,因此通過加工工藝即可控制彎波導的波導型腔的精度,即波導型腔內壁表面粗糙度可達ra1.6μm。
(2)本發明的下蓋板的凸肩裝配於上蓋板的凹槽內以自動定位,以保證裝配精度,尺寸精度可控制在0.015~0.03mm內,同時還保證了後續焊接精度。
(3)本發明採用雷射切割製作釺料,保證釺料尺寸準確均勻性,能夠實現高精度均勻的鋪展在上蓋板與下蓋板之間接觸部分,避免了釺料產生漫流流入型腔內而影響波導內腔尺寸的精度。
(4)本發明採用真空釺焊方式一次將上下蓋板焊接成形,不使用釺劑,既沒有手工火焰釺焊集中加熱引起帶來的焊接變形,而且從根本上避免了傳統扭彎波導加工所帶來的填充材料清洗,不僅使得產品壽命大幅度提高,而且焊接變形概率極低。
(5)本發明利用真空釺焊一次成形還可同時實現多條複雜焊縫、多個零件的焊接等優點,提高生產效率。
附圖說明
圖1為彎波導的結構示意圖;
圖2為真空釺焊溫度工藝曲線圖;
圖中,1-上蓋板,2-下蓋板,3-法蘭盤。
具體實施方式
下面結合附圖對本發明做進一步的描述,本發明的保護範圍不局限於以下所述:
如圖1所示,一種高精度極高頻率彎波導加工方法,它包括以下步驟:
s1、上蓋板的加工:水切割備料;數控粗銑備料的六個面;在備料底表面銑削加工出上部型腔,並預留加工餘量2~5mm;在250~280℃溫度下進行退火處理以消除應力;採用線切割精切上部型腔;數控精銑備料六個面;在備料的底表面精銑加工出繞上部型腔環形布置的凹槽;去毛刺;最終實現上蓋板1的加工;
s2、下蓋板的加工:水切割備料;數控粗銑備料的六個面;在備料頂表面銑削加工出下部型腔,並預留加工餘量2~5mm;在250~280℃溫度下進行退火處理以消除應力;採用線切割精切下部型腔;數控精銑備料六個面;在備料的頂表面精銑加工出繞下部型腔環形布置且與凹槽相配合的凸肩;去毛刺;最終實現下蓋板2的加工;
s3、上下蓋板焊前表面處理:將步驟s1中的上蓋板1和步驟s2中的下蓋板2放入溫度為60~80℃、濃度為8~10%的naoh水溶液中浸蝕1~2min;鹼洗結束後利用熱水反覆衝洗上蓋板1和下蓋板2;衝洗結束後放入由濃度為10%的hno3溶液和濃度為0.25%的hf溶液組成的混合液中浸蝕3~5min;浸蝕結束後利用冷水反覆衝洗上蓋板1和下蓋板2;衝洗結束後對上下蓋板進行烘乾處理;最終實現上下蓋板焊前表面處理;
s4、釺料的製作:根據高波導內腔尺寸,採用雷射切割製作釺料,釺料選用0.05mm厚度規格,釺料的外形尺寸與彎波導內腔尺寸一致並確保釺料能夠平整均勻的鋪展在上蓋板1和下蓋板2之間;
s5、焊前裝配:將釺料放置於上蓋板1與下蓋板2相接觸位置;將下蓋板2的凸肩裝配於上蓋板1的凹槽內以自動定位,保證了後續焊接精度,裝配後形成波導,其中上部型腔與下部型腔構成波導型腔,實現了焊前波導的裝配;
s6、真空釺焊:將步驟s5中裝配好的波導放入真空鋁釺焊爐內;利用工裝夾具裝配波導,在裝夾的過程中不能對高精度極高頻彎波導約束過度,防止波導內腔高溫熱膨脹後冷卻收縮變形;設定真空釺焊溫度工藝曲線,該工藝曲線如圖2所示;將真空鋁釺焊爐抽粗真空隨後抽高真空;按設定真空釺焊溫度工藝曲線對波導和釺料加熱;在600℃溫度下保溫8min;保溫結束後隨爐冷卻,實現上蓋板與下蓋板連為一體,最終實現真空釺焊。在真空釺焊過程不需要使用含氟腐蝕性釺劑,採用金屬鎂作活化劑,促使鋁的表面氧化膜破裂變質,保證釺料在母材表面的潤溼、鋪展,保證獲得緻密光亮的釺焊接頭,釺焊接頭具有優良的機械性能和抗腐蝕性能;
s7、真空釺焊完成後對波導進行線切割外形、數銑加工外形,加工出法蘭盤3,最終加工出高精度極高頻率彎波導。
整個高精度極高頻率彎波導從零件初始加工到裝配、焊接,再到最後零件成形的整個加工過程,都處於高精度控制之下,變形量極小,波導內腔尺寸精確,焊接質量和電性能都得到了可靠保證,適用於高精度極高頻率彎波導的批量生產。