一種晶片及其製造方法與流程
2024-03-29 00:39:05 1
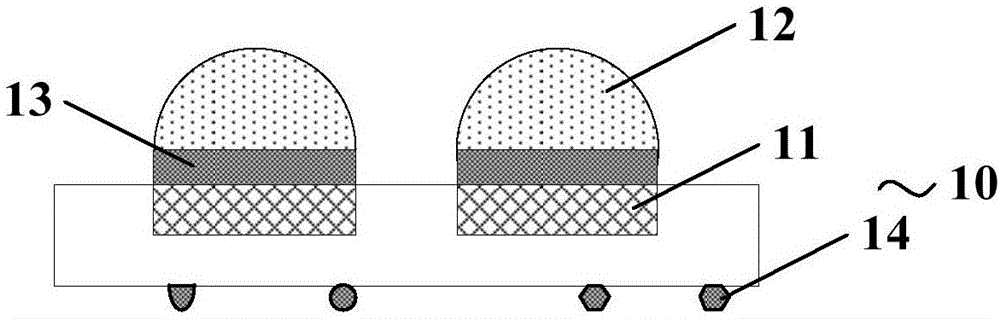
本發明實施例涉及晶片製造技術,尤其涉及一種晶片及其製造方法。
背景技術:
晶片是指內含集成電路的矽片,體積很小,常常是計算機或其他電子設備的一部分,安裝在計算機或其他電子設備中的的晶片是已經封裝完成的晶片。晶片的封裝流程主要包括晶片製造、晶片切割、晶片貼裝和晶片互連。
晶片貼裝工藝是指將晶片用有機膠和金屬焊料粘接在基板上,起到熱、電和機械連接的作用。然而,現有晶片貼裝工藝中,將晶片貼裝到基板之前,如圖1所示給晶片10的電極11上塗覆焊料12時,焊料12形狀不可控,焊料12易受擠壓進而容易與相鄰的電極11形成短路。
技術實現要素:
本發明實施例提供一種晶片及其製造方法,以解決現有晶片貼裝工藝中,焊料形狀不可控且易受擠壓進而容易與相鄰的電極形成短路的問題。
第一方面,本發明實施例提供了一種晶片的製造方法,該製造方法包括:
提供一超薄晶片,所述超薄晶片的功能面上具有多個電極,在所述超薄晶片的功能面上形成鈍化層,所述鈍化層具有與所述多個電極分別對應設置的多個第一開口;
在所述鈍化層上形成掩膜層,所述掩膜層具有與所述多個第一開口分別對應設置的多個第二開口,所述第二開口大於所述第一開口;
在所述第二開口中形成導電凸點;
去除所述掩膜層。
進一步地,在所述第二開口中形成導電凸點的具體執行過程為:採用電鍍工藝在所述第二開口中形成導電凸點。
進一步地,形成掩膜層之前,該製造方法還包括:在所述鈍化層上形成導電種子層;以及,去除所述掩膜層之後,還包括:去除暴露的所述導電種子層。
進一步地,所述導電種子層包括依次層疊形成的鈦金屬層和銅金屬層。
進一步地,所述鈦金屬層的厚度為100nm,所述銅金屬層的厚度為300~500nm。
進一步地,所述導電凸點包括依次層疊形成的鎳金屬層和焊盤,其中,所述焊盤的組成材料包括錫或錫銀合金。
進一步地,所述鎳金屬層的厚度為2~3μm;所述焊盤的厚度為6~15μm。
進一步地,所述超薄晶片包括相對的功能面和非功能面,該製造方法還包括:採用研磨工藝對所述超薄晶片的非功能面進行研磨減薄。
進一步地,該製造方法還包括:切割以形成多個晶片。
第二方面,本發明實施例還提供了一種晶片,該晶片採用上述晶片製造方法進行製造。
本發明實施例中提供一種晶片及其製造方法,在超薄晶片的功能面上形成具有多個第一開口的鈍化層,在鈍化層上形成具有多個第二開口的掩膜層,再第二開口中形成導電凸點則導電凸點與電極接觸,最後去除掩膜層。本發明實施例中,通過設置具有多個第一開口的鈍化層和具有多個第二開口的掩膜層,將導電凸點形成在第一開口和第二開口中,實現了精確控制導電凸點的形狀;形成導電凸點時,任意相鄰兩個電極上的導電凸點之間採用掩膜層進行間隔,則形成的導電凸點不易擠壓變形而避免了相鄰導電凸點之間的短路現象,便於一次性、高精度的成型導電凸點。
附圖說明
為了更清楚地說明本發明實施例或現有技術中的技術方案,下面將對實施例或現有技術描述中所需要使用的附圖做一簡單地介紹,顯而易見地,下面描述中的附圖是本發明的一些實施例,對於本領域普通技術人員來講,在不付出創造性勞動的前提下,還可以根據這些附圖獲得其他的附圖。
圖1為現有技術提供的晶片示意圖;
圖2為現有技術提供的第二種晶片示意圖;
圖3是本發明實施例一提供的晶片製造方法的流程圖;
圖4A~圖4D是本發明實施例一提供的晶片製造工藝的示意圖;
圖5A~圖5B是本發明實施例二提供的導電種子層製造工藝的示意圖;
圖6是本發明實施例二提供的導電凸點製造工藝的示意圖;
圖7是本發明實施例二提供的晶片減薄工藝的示意圖。
具體實施方式
為使本發明的目的、技術方案和優點更加清楚,以下將參照本發明實施例中的附圖,通過實施方式清楚、完整地描述本發明的技術方案,顯然,所描述的實施例是本發明一部分實施例,而不是全部的實施例。基於本發明中的實施例,本領域普通技術人員在沒有做出創造性勞動前提下所獲得的所有其他實施例,都屬於本發明保護的範圍。
如圖2所示為現有技術提供的另一種晶片的示意圖。現有晶片貼裝工藝中,將晶片貼裝到基板之前,如圖2所示會在晶片10的電極11上依次形成金屬凸點13和焊料12。通常採用「化學鍍」鎳金的方式形成金屬凸點13,然而化學鍍溶液中的離子會附著在晶片10的非功能面,導致晶片10的非功能面上形成有一定厚度的金屬雜質14。在後續的晶片減薄工序中,晶片10的非功能面上的金屬雜質14會影響磨輪的行程動作,導致減薄過程中磨輪電壓異常而使晶片10燒結或破裂。此外,在金屬凸點13上塗覆焊料12時,焊料12形狀不可控,焊料12易受擠壓進而容易與相鄰的電極11形成短路。
為了解決現有技術的問題,本發明實施例一提供一種晶片製造方法,如圖3所示,該晶片製造方法具體包括如下步驟:
步驟110、如圖4A所示提供一超薄晶片201,超薄晶片201的功能面201a上具有多個電極202,在超薄晶片201的功能面201a上形成鈍化層203,鈍化層203具有與所述多個電極202分別對應設置的多個第一開口203a。
本實施例中所述超薄晶片201為設置有電極202的晶圓,晶圓是指常規半導體集成電路製作所用的晶片,因多為圓形故稱為晶圓。本實施例中可選晶圓為矽晶圓,本領域技術人員可以理解,任意一種可用於集成電路製作中的晶片均落入本發明的保護範圍,不僅限於矽晶圓。本實施例中晶圓上絕緣設置有多個電極202,可選該電極202為Al焊盤,本領域技術人員可以理解,任意一種可用於電極製作的材料均落入本發明的保護範圍,不僅限於Al。
具體的,在超薄晶片201的功能面201a上形成鈍化膜層並刻蝕該鈍化膜層以形成具有多個第一開口203a的鈍化層203,鈍化層203的多個第一開口203a與所述多個電極202分別對應設置且第一開口203a的底部延伸至電極202的表面。可選的,鈍化層203的厚度為5~10μm,可選的第一開口203a的最大口徑等於電極202開口。本領域技術人員可以理解,晶片實際生產中,相關從業人員可根據工藝條件和產品所需自行控制第一開口的口徑尺寸,在本發明中不對第一開口的尺寸進行具體限制。
在本實施例中可以採用多種方法形成鈍化層203,例如可採用化學氣相沉積法、真空蒸鍍法、濺射法等多種工藝方法形成鈍化膜層,再採用溼法刻蝕或幹法刻蝕工藝在電極202上方形成第一開口203a。本實施例中可選鈍化層203的組成材料包括聚苯並惡唑(PBO)或聚醯亞胺(PI),具有成本低、高絕緣等優勢。本發明中鈍化層的組成材料有多種,任意一種已知的易成膜的絕緣材料均落入本發明的保護範圍,例如多種高絕緣的聚合物薄膜。
步驟120、如圖4B所示在鈍化層203上形成掩膜層204,掩膜層204具有與所述多個第一開口203a分別對應設置的多個第二開口204a,第二開口204a大於第一開口203a。
本實施例中在鈍化層203上形成掩膜層204且掩膜層204具有多個第二開口204a,第二開口204a與第一開口203a對應設置,則第二開口204a與第一開口203a暴露出對應的電極202的表面。掩膜層204可選為光刻膠,便於在後續工藝中去除。本領域技術人員可以理解,任意一種便於去除且不容易產生雜質的掩膜材料均落入本發明的保護範圍。具體的可採用曝光、顯影和刻蝕工序形成具有第二開口204a的掩膜層204。
本實施例中第二開口204a大於第一開口203a,具體的,第二開口204a的最小口徑大於或等於第一開口203a的最大口徑,便於後續形成的導電凸點與電極202充分接觸。本領域技術人員可以理解,晶片實際生產中,相關從業人員可根據工藝條件和產品所需自行控制第二開口的口徑尺寸,在本發明中不對第二開口的尺寸進行具體限制。
步驟130、如圖4C所示在第二開口204a中形成導電凸點205。
本實施例中掩膜層204中的第二開口204a與電極202一一對應設置,在第二開口204a中形成導電凸點205,則導電凸點205的形狀可以控制且導電凸點205通過第二開口204a與第一開口203a直接與電極202接觸。任意相鄰兩個電極202上的導電凸點205之間存在掩膜層204,因此導電凸點205形狀可控且不易受擠壓而變形,相應的也相鄰導電凸點205之間也不會產生短路現象,提高了導電凸點204的形成精度。
可選的,沉積導電凸點材料時,若導電凸點材料覆蓋了掩膜層204,則可以對導電凸點材料膜層進行刻蝕處理並刻蝕至掩膜層204的表面,露出掩膜層204使任意相鄰兩個導電凸點205之間存在掩膜層204作為間隔材料。或者也可以僅對掩膜層204上方的導電凸點材料進行刻蝕以露出掩膜層204使任意相鄰兩個導電凸點205之間存在掩膜層204作為間隔材料。
步驟140、如圖4D所示去除掩膜層204。
在本實施例中形成導電凸點205之後,去除任意相鄰兩個導電凸點205之間的掩膜層204。在本實施例中可以採用刻蝕工藝去除掩膜層204。
本實施例中提供的晶片製造方法,在超薄晶片的功能面上形成具有多個第一開口的鈍化層,在鈍化層上形成具有多個第二開口的掩膜層,再第二開口中形成導電凸點則導電凸點與電極接觸,最後去除掩膜層。本實施例中,通過設置具有多個第一開口的鈍化層和具有多個第二開口的掩膜層,將導電凸點形成在第一開口和第二開口中,實現了精確控制導電凸點的形狀;形成導電凸點時,任意相鄰兩個電極上的導電凸點之間採用掩膜層進行間隔,則形成的導電凸點不易擠壓變形而避免了相鄰導電凸點之間的短路現象,便於一次性、高精度的成型導電凸點。
本發明實施例二還提供一種晶片的製造方法,該製造方法與上述任意實施例的區別在於,可選步驟130的在第二開口204a中形成導電凸點205的操作的具體執行過程為:採用電鍍工藝在第二開口204a中形成導電凸點205。
現有技術中採用化學鍍工藝形成金屬凸點,化學溶液中的離子會附著在晶片非功能面上形成金屬雜質,導致減薄過程中磨輪電壓異常而使晶片燒結或破裂。
為了解決該問題,本實施例中可選採用電鍍工藝在第二開口204a中形成導電凸點205。電鍍工藝是藉助外界直流電的作用,利用電解原理使導電體的表面沉積一層金屬或合金層,因此本實施例中電鍍導電凸點205時導電凸點205僅會形成在第一開口203a底部露出的電極202表面上。如圖4A所示超薄晶片201的非功能面201b上沒有導電體,因此電鍍過程中超薄晶片201的非功能面201b上不會形成導電雜質,則超薄晶片201的非功能面201b平坦且沒有硬力點,相應的,不會出現減薄過程中硬力點導致磨輪電壓異常而使晶片燒結或破裂的問題。
可選的,如圖4B所示形成掩膜層204之前,還包括:如圖5A所示在鈍化層203上形成導電種子層206;以及去除掩膜層204之後,還包括:如圖5B所示去除暴露的導電種子層206。在鈍化層203上形成一層導電種子層206,能夠提高導電凸點205和電極202的結合力,便於電鍍導電凸點205。而在電鍍完成後需要去除暴露的導電種子層206,使任意相鄰兩個電極202之間斷開電連接,避免超薄晶片201的電極202之間短路。
可選的,導電種子層206包括依次層疊形成的鈦金屬層206a和銅金屬層206b。鈦的導電性比銅差,但鈦的結合力優於銅,因此為了同時保證結合力和高導電性,本實施例中可選導電種子層206包括鈦金屬層206a和銅金屬層206b。鈦金屬層206a直接與電極202接觸,還能夠防止銅向超薄晶片201的晶圓片中擴散,避免銅向晶圓片中擴散而影響器件的性能。
可選的,鈦金屬層206a的厚度為100nm,銅金屬層206b的厚度為300~500nm。鈦金屬層206a的厚度較小,則在起到結合力作用的同時減弱了鈦金屬層206a的鈍化;銅金屬層206b的厚度較大,能夠增加導電種子層206的導電性。
可選的,如圖6所示導電凸點205包括依次層疊形成的鎳金屬層205a和焊盤205b,其中,焊盤205b的組成材料包括錫或錫銀合金。可選鎳金屬層205a的厚度為2~3μm;焊盤205b的厚度為6~15μm。超薄晶片201中採用在電極202和焊盤205b之間設置鎳金凸點結構即鎳金屬層205a,能夠使互連長度更短,互連的電阻和電感更小,器件的電性能得到了明顯提高和改善。採用電鍍工藝形成鎳金屬層205a和焊盤205b,不會在超薄晶片201的非功能面201b上形成雜質,使超薄晶片201的非功能面201b平坦且無硬力點。
示例性的,在上述技術方案的基礎上,可選超薄晶片201包括相對的功能面201a和非功能面201b,該製造方法還包括:如圖7所示採用研磨工藝對超薄晶片201的非功能面201b進行研磨減薄。對超薄晶片201的非功能面201b進行研磨減薄實質上是對超薄晶片201的晶片進行減薄,晶片減薄後能夠提高晶片的散熱性能,還有利於晶片分離,能夠提高晶片的劃片質量和成品率。
可選的,該製造方法還包括:切割以形成多個晶片。超薄晶片201是以晶片為依託形成,因此在製造完成後可切割該超薄晶片201以形成多個小晶片,小晶片可應用在各種集成電路中。
本領域技術人員可以理解,本發明中主要保護的是晶片的製造流程,對晶片中電極、鈍化層、掩膜層、導電凸點和導電種子層等任意一種結構的尺寸參數、材料和形成工藝不進行具體限制,任意一種採用上述製造流程製造的晶片均落入本發明的保護範圍。
本發明實施例還提供了一種晶片,該晶片採用如上任意實施例所述的晶片製造方法進行製造。該晶片可以應用在集成電路中。本領域技術人員可以理解,上述任意實施例僅示出了晶片的部分結構,晶片還包括電路層等結構,在本發明中不對晶片的電路層等結構進行具體說明和圖示。
注意,上述僅為本發明的較佳實施例及所運用技術原理。本領域技術人員會理解,本發明不限於這裡所述的特定實施例,對本領域技術人員來說能夠進行各種明顯的變化、重新調整和替代而不會脫離本發明的保護範圍。因此,雖然通過以上實施例對本發明進行了較為詳細的說明,但是本發明不僅僅限於以上實施例,在不脫離本發明構思的情況下,還可以包括更多其他等效實施例,而本發明的範圍由所附的權利要求範圍決定。