一種砂輪表面粗糙度和磨粒分布狀態的檢測及評價方法與流程
2023-04-24 16:40:51 5
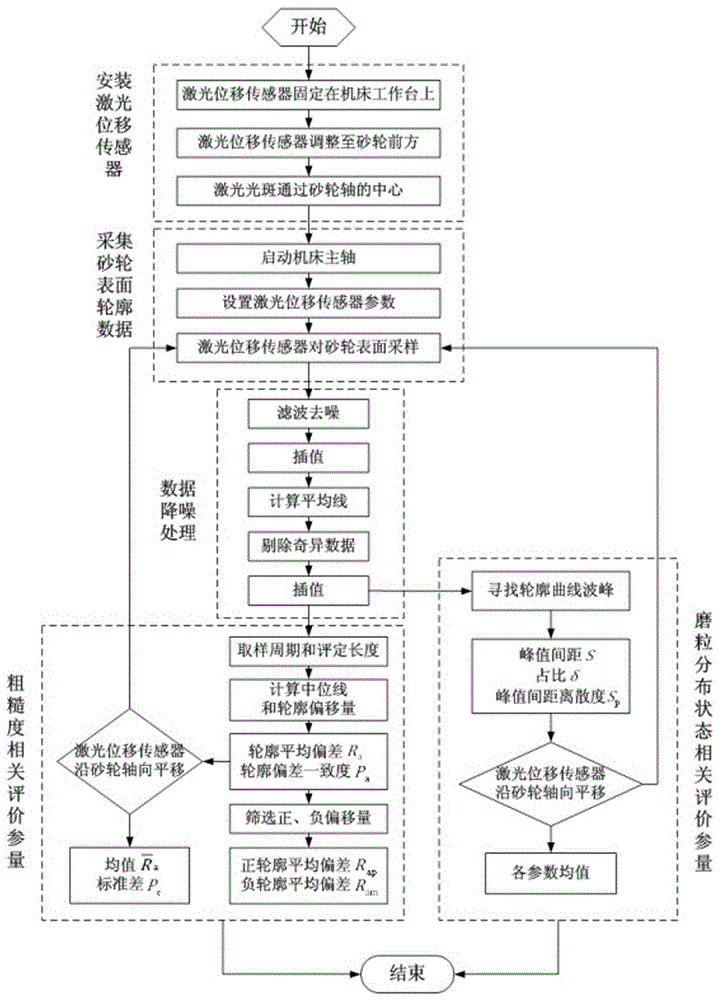
本發明涉及精密超精密加工和精密測試技術領域,尤其涉及一種砂輪表面粗糙度和磨粒分布狀態的檢測及評價方法。
背景技術:
砂輪是用磨料和結合劑等製成的中央有通孔的圓形固結磨具,在使用時高速旋轉,對各種金屬和非金屬材料的外圓、內圓、平面和其它各種型面進行磨削加工;磨削加工是精密加工的主要加工方法,廣泛應用於各類工業生產中,而砂輪作為磨削加工的工具,其磨削性能直接關係到磨削加工的精度和質量;砂輪表面的粗糙程度、磨粒分布的密度以及均勻性等參數對砂輪的磨削力、磨削熱和工件表面質量都有重要影響,快捷有效地檢測並評價砂輪表面粗糙度、磨粒分布密度和均勻性為砂輪製造、修整工藝的優化和磨削工藝參數的調整提供了重要的參考依據,對磨削加工質量和精度的提高有著重要的導向作用。
目前對砂輪表面粗糙度和磨粒分布狀態進行檢測的方法主要包括:
①利用輪廓儀等接觸式量儀對砂輪表面的輪廓進行測量;這種方法雖然理論上可以測量砂輪表面粗糙度,但由於量儀的測頭需要接觸砂輪粗糙表面,測量時極易造成測頭磨損從而損壞量儀,尤其是在砂輪粒度大、尺寸大的條件下,情況更為惡劣,而且這種方法耗時費力,受限因素多,也無法實現在機檢測。
②利用超景深三維顯微鏡、白光幹涉儀等檢測砂輪表面的三維形貌;這種方法可以獲得砂輪表面的三維輪廓高度數據,從中分析出砂輪表面的粗糙度和磨粒分布狀態,但由於測量範圍多為砂輪表面極小的一塊區域,檢測結果不全面,如果採用多次測量重構的方法則工作量和數據量巨大,檢測成本過高,同時由於砂輪表面非均質、磨粒透光折射等因素會給檢測結果引入較大誤差,而且這種方法也需要將砂輪從工具機上取下,無法實現在機檢測。
③憑藉視覺和觸覺人為感知砂輪表面的粗糙度和磨粒分布狀態,這種方法簡單易行,但無法對具體結果量化分析,而且受人為因素影響極大,檢測準確性無法保證。
由於砂輪表面結構的複雜性和工具機實際加工的局限性,目前仍主要採用人為的視覺和觸覺感知能力來評估砂輪表面粗糙度和磨粒分布狀態,還沒有一種快捷、有效、精確的砂輪表面粗糙度和磨粒分布狀態的檢測及評價方法。
技術實現要素:
本發明的目的是提供一種砂輪表面粗糙度和磨粒分布狀態的檢測及評價方法,能夠快捷有效地檢測砂輪表面圓周方向的粗糙度、磨粒分布密度和分布均勻性,克服目前砂輪表面粗糙度和磨粒分布狀態的檢測成本高、耗時費力且難以全面評價的困難。
本發明採用的技術方案為:一種砂輪表面粗糙度和磨粒分布狀態的檢測及評價方法,包括如下步驟:
步驟1:檢測裝置的準備工作;被測砂輪安裝在工具機主軸上;檢測裝置包括雷射位移傳感器、控制器、數據電纜線、磁力支撐架和計算機,雷射位移傳感器設置在磁力支撐架上,且雷射位移傳感器位於被測砂輪正前方,雷射位移傳感器和被測砂輪非接觸,雷射位移傳感器通過數據電纜線與控制器連接,控制器通過數據電纜線與計算機連接;啟動檢測裝置,工具機工作檯帶動雷射位移傳感器移動,使雷射位移傳感器位於被測砂輪表面的前方,雷射光斑通過被測砂輪軸的中心;
步驟2:利用雷射位移傳感器採集砂輪表面圓周方向輪廓數據,具體包括步驟2.1-2.3;
步驟2.1:啟動工具機主軸,帶動被測砂輪勻速旋轉;
步驟2.2:設置雷射位移傳感器參數;根據砂輪直徑、砂輪轉速和磨粒直徑這些條件參量,通過控制器設置雷射位移傳感器的採樣頻率f和採樣長度l;採樣頻率f和採樣長度l滿足式(1)所示關係:
式(1)中,ns是被測砂輪轉速,單位r/min;ds是被測砂輪直徑,單位mm;dm是被測砂輪表面磨粒直徑,單位mm;雷射位移傳感器採樣頻率f單位為hz,採樣長度l單位為個;
步驟2.3:雷射位移傳感器對旋轉的被測砂輪外圓表面掃描採樣,將採樣點的相對高度,即被測砂輪表面圓周方向輪廓數據,傳輸至計算機;
步驟3:對傳輸至計算機的原始採樣數據進行降噪處理,具體包括步驟3.1-3.5;
步驟3.1:將傳輸至計算機的原始採樣數據構建採樣數據數組y1={y1,y2,…,yl},並將y1中數據點逐一進行編號,構建採樣點坐標數組x1={1,2,…,l};
步驟3.2:對步驟3.1中的原始採樣數據數組y1進行濾波去噪,濾波原理為,砂輪表面不超過寬度閾值j範圍內的採樣高度值,其變化幅度不應超過幅度閾值h,寬度閾值j是指雷射位移傳感器採樣數據段中數據點的個數的合理值,幅度閾值h是指雷射位移傳感器採樣數據段中數據點的差值的合理值;
步驟3.3:對步驟3.2濾波去噪後的數據數組進行線性插值處理,以補充濾波去除的數據點,獲得新的數據數組y2={y′1,y′2,…,y′l},y2的坐標數組仍為x1;
步驟3.4:對步驟3.3線性插值處理後獲得的數據數組y2,計算其移動平均數,即截取長度為q的滑動數據段,q為奇數,利用每個數據段的平均數構建平均線數據數組利用每個數據段的中心位置坐標構建平均線坐標數組
步驟3.5:剔除奇異數據點並進行線性插值補充;計算步驟3.3線性插值處理後獲得的數據數組y2相對於步驟3.4計算得到的平均線數據數組ym的偏移量並進行分布統計,將偏離幅度大,且分布概率低的數組y2中的奇異數據點剔除,剔除的數據點採用線性插值補充,獲得新的數據數組y3的坐標數組
步驟4:計算得到與砂輪表面粗糙度相關的評價參量:輪廓平均偏差ra、輪廓偏差一致度pa、正輪廓平均偏差rap、負輪廓平均偏差ram、輪廓平均偏差ra的均值和標準差pc,具體包括步驟4.1-4.5;
步驟4.1:計算得到中位線數據數組yu和中位線坐標數組xu,具體包括步驟4.1.1-4.1.3;
步驟4.1.1:按照取樣周期1/k和評定長度m對步驟3.4中的平均線數據數組ym進行截取;k和m均為正整數;截取方法為:砂輪圓周表面一周的採樣點數為個,從數組ym中截取時,共截取m段,每段長度為個數據點,每段截取的起始點坐標分別為
經過截取後獲得m個數組分別為:
數組ym1、ym2、……、ymm的坐標數組分別為
步驟4.1.2:針對步驟4.1.1中的數組ym1、ym2、……、ymm,利用數學的最小二乘法依次對各數組中數據進行曲線擬合,擬合後獲得ym1、ym2、……、ymm對應的擬合數組分別為:
擬合數組yn1、yn2、……、ynm的坐標數組仍為xm1、xm2、……、xmm;
步驟4.1.3:針對步驟4.1.2中的擬合數組yn1、yn2、……、ynm,依次截取各數組的中間個數據點,構成子集數組yu1、yu2、……、yum;
擬合數組yn1、yn2、……、ynm對應的子集數組分別為:
子集數組yu1、yu2、……、yum的坐標數組分別為:
分別將子集數組yu1、yu2、……、yum的數據點依次順序排列,構成中位線數據數組同樣的,分別將子集數組yu1、yu2、……、yum的坐標數組xu1、xu2、……、xum的數據點依次順序排列,構成中位線坐標數組
步驟4.2:計算步驟3.5中的剔除奇異數據點並插值補充後的數據數組y3相對於步驟4.1.3中的中位線數據數組yu的坐標對應的數據點的偏移量,獲得輪廓偏移量數組輪廓偏移量數組ys的坐標數組xs仍為xu,即
為方便後續表述,將輪廓偏移量數組ys的坐標按順序重新排號,即輪廓偏移量數組ys的坐標數組xs調整為
步驟4.3:利用步驟4.2中的輪廓偏移量數組ys按照取樣周期1/k和評定長度m計算輪廓平均偏差ra以及輪廓偏差一致度pa;
式(2)(3)中,ns是被測砂輪轉速,單位r/min;f是雷射位移傳感器採樣頻率,單位hz;ysi為偏移量數組ys中數據點;
輪廓平均偏差ra用來評價砂輪表面圓周方向的整體或局部的粗糙程度;輪廓偏差一致度pa用來評價砂輪表面圓周方向局部粗糙度的一致性;
步驟4.4:計算正輪廓平均偏差rap和負輪廓平均偏差ram;將步驟4.2中的輪廓偏移量數組ys中的正數和負數分別篩選出來,構建正輪廓偏移量數組ysp和負輪廓偏移量數組ysm,將數組ysp和ysm按照取樣周期1/k和評定長度m計算正輪廓平均偏差rap和負輪廓平均偏差ram,
式(4)中,{yspa,yspa+1,…,yspb}為輪廓偏移量數組ys子集數組中的正數,{yspc,yspc+1,…,yspd}為輪廓偏移量數組ys子集數組中的正數,
ysp={yspa,…,yspb,…,yspc,…,yspd};
式(5)中,{ysma1,ysma1+1,…,ysmb1}為輪廓偏移量數組ys子集數組中的負數,{ysmc1,ysmc1+1,…,ysmd1}為輪廓偏移量數組ys子集數組中的負數,
ysm={ysma1,…,ysmb1,…,ysmc1,…,ysmd1};
正輪廓平均偏差rap和負輪廓平均偏差ram用來評價砂輪表面的鈍化狀態;
步驟4.5:計算均值和標準差pc;如果砂輪寬度較大,需要對砂輪表面的平均粗糙度進行綜合評價,將雷射位移傳感器沿砂輪軸向平移,使雷射光斑位於砂輪一側邊緣,然後雷射位移傳感器向另一側平移一段距離e,取樣周期1/k中k取值為1,重複步驟2.3至步驟4.3,計算得到輪廓平均偏差ra2,如此循環往復,直到雷射光斑位於砂輪的另一側邊緣時結束,共測量n-1次,得到ra2、ra3、ra4、…、ran,計算ra2、ra3、ra4、…、ran的均值和標準差pc;
雷射位移傳感器的平移距離e滿足式(8)所示關係:
0.9ws<(n-2)e<ws(8)
式(8)中,ws是被測砂輪軸向寬度,單位mm;
用來綜合評價砂輪表面,兼顧整個軸向寬度的表面,沿圓周方向的平均粗糙程度;pc用來評價砂輪表面圓周方向粗糙度在軸向不同位置的一致性;
步驟5:計算得到與砂輪表面磨粒分布密度和均勻性相關的評價參量:砂輪表面圓周方向輪廓曲線的峰值間距s、磨粒直徑與峰間距佔比δ、峰值間距離散度sp、砂輪表面圓周方向輪廓曲線的峰值間距s的均值磨粒直徑與峰間距佔比δ的均值和峰值間距離散度sp的均值具體包括步驟5.1-5.3;
步驟5.1:尋找輪廓曲線的波峰值及其位置坐標;將步驟3.5中剔除奇異數據點並插值補充後的數據數組y3及其坐標數組x3導入二維直角坐標系,繪製出砂輪表面圓周方向的輪廓曲線,通過差值法和閾值法尋找輪廓曲線的波峰值及其位置坐標;
差值法和閾值法尋找輪廓曲線波峰的原理為:輪廓曲線中後一位置採樣點和前一位置採樣點的差值可以重新形成一個新的差值波形,差值波形中由正轉負過零位置對應輪廓曲線中的採樣點為準波峰值,如果差值波形中由正轉負過零位置前的正值數據長度超過一定長度閾值r且正值數據幅度超過一定幅度閾值i,並且該位置後的負值數據長度超過一定長度閾值r且負值數據幅度超過一定幅度閾值i,即認定該位置對應輪廓曲線中的採樣點為波峰值;
步驟5.2:計算砂輪表面圓周方向輪廓曲線的峰值間距s、磨粒直徑與峰間距佔比δ以及峰值間距離散度sp;根據步驟5.1中尋找得到的數據數組y3中所有的波峰值及其在坐標數組x3中對應的位置坐標,從坐標數組x3中截取砂輪表面一個圓周的波峰值所對應的位置坐標,構建數組xp={n1,n2,…,nt};由數組xp中相鄰兩元素的差值,計算砂輪表面圓周方向輪廓曲線的峰值間距s、磨粒直徑與峰值間距佔比δ以及峰值間距離散度sp,
式(9)(10)(11)中,ns是被測砂輪轉速,單位r/min;ds是被測砂輪直徑,單位mm;dm是被測砂輪表面磨粒直徑,單位mm;f是雷射位移傳感器採樣頻率,單位hz;
峰值間距s用來評價砂輪表面圓周方向磨粒分布的平均間距;磨粒直徑與峰間距佔比δ用來評價砂輪表面磨粒分布的密度;峰值間距離散度sp用來評價砂輪表面磨粒分布的均勻性;
步驟5.3:分別計算砂輪表面圓周方向輪廓曲線的峰值間距s、磨粒直徑與峰間距佔比δ以及峰值間距離散度sp的均值和將雷射位移傳感器沿砂輪軸向平移,使雷射光斑位於砂輪一側邊緣,然後雷射位移傳感器向另一側平移一段距離,平移規則與步驟4.5中的相同,重複步驟2.3至步驟3.5,以及步驟5.1和步驟5.2,計算得s2、δ2以及sp2,如此循環往復,計算得s3、δ3、sp3,s4、δ4、sp4,……,最後計算各參數均值
峰值間距s、磨粒直徑與峰間距佔比δ以及峰值間距離散度sp的均值和用來針對砂輪表面,兼顧整個軸向寬度的表面,沿圓周方向磨粒分布的密度和均勻性進行評價。
進一步地,步驟3.2中,針對原始採樣數據數組y1進行濾波去噪時,根據砂輪表面磨粒直徑dm、雷射位移傳感器採樣頻率f和砂輪轉速ns砂輪直徑ds設置寬度閾值j和幅度閾值h,寬度閾值j為砂輪外圓一周採樣點數的幅度閾值h為砂輪表面磨粒直徑dm的0.8~1.5倍。
進一步地,步驟3.4中,針對數據數組y2進行移動平均,截取滑動數據段的長度q時根據砂輪轉速ns和雷射位移傳感器採樣頻率f進行設置,q為f/ns的2倍。
進一步地,步驟3.5中,剔除的奇異數據點數量不超過數組y2中數據總數量的3%。
進一步地,步驟4.1.1、步驟4.3、步驟4.4和步驟4.5中,關於取樣周期1/k和評定長度m的取值,當需要評定砂輪表面圓周方向的整體粗糙程度時,取樣周期中k取值為1;當需要評定砂輪表面圓周方向的局部粗糙程度時,取樣周期中k取值為大於1的正整數,評定長度m取值為1;當需要評價砂輪表面粗糙度沿圓周方向的一致性時,取樣周期中k和評定長度m相等,且均為大於1的正整數。
進一步地,步驟5.1中,長度閾值r設置為2~4,幅度閾值i為砂輪磨粒直徑的
本發明的有益效果主要為:
(1)本發明利用雷射位移傳感器高速率、高精度的掃描採集能力以及計算機的高效數據處理能力,實現砂輪表面粗糙度和磨粒分布狀態的檢測及分析評價,並分別針對砂輪表面圓周方向的粗糙度、磨粒分布密度和分布均勻性計算出相應的評價參量,克服了目前砂輪表面粗糙度和磨粒分布狀態的檢測成本高、且耗時費力又難以全面評價的困難,為砂輪製造和修整工藝的改進提供準確依據,對提高磨削加工質量和效率具有重要意義。
(2)本發明採用非接觸式檢測方法,檢測過程中不會損耗量儀,檢測成本極低;檢測對象可以是陶瓷、樹脂、金屬等各種結合劑類型的砂輪,不受砂輪直徑、寬度等尺寸條件的限制,還可以檢測各種粒度型號的砂輪,檢測適應性好、通用性強。
(3)本發明可以在工具機不停機、不拆卸砂輪的條件下進行檢測,不受工具機特性限制,實現在機檢測;檢測裝置的安裝和操作方便快捷,計算機快速處理數據,檢測效率高。
(4)本發明不僅可以通過輪廓平均偏差ra評價砂輪圓周方向的整體和局部粗糙度,通過正輪廓平均偏差rap和負輪廓平均偏差ram評價砂輪表面的鈍化狀態,通過峰值間距s、磨粒直徑與峰間距佔比δ、峰值間距離散度sp評價砂輪表面圓周方向磨粒分布的密度和均勻性,還可以利用各參量的均值及標準差評價砂輪表面,兼顧整個軸向寬度的表面,各參量的平均水平及離散狀態。
附圖說明
圖1為本發明所述的檢測裝置的組成原理示意圖;
圖2為本發明的流程圖。
具體實施方式
下面結合附圖和實施例對本發明的具體實施方式做進一步詳細說明,如圖1所示,本發明的檢測裝置包括:雷射位移傳感器1、控制器2、數據電纜線3、磁力支撐架、計算機4,同時包括在labview、matlab等編程環境下形成的實現本發明所述檢測及評價方法的數據處理軟體;具體做法是:雷射位移傳感器1通過磁力支撐架固定在工具機工作檯上,工具機工作檯帶動雷射位移傳感器1移動並將雷射位移傳感器1固定於被測砂輪5的正前方,雷射位移傳感器1和被測砂輪5非接觸,雷射位移傳感器1通過數據電纜線3與控制器2連接,控制器2通過數據電纜線3與計算機4連接,計算機4中包含數據處理軟體,可以快速完成對雷射位移傳感器1檢測數據的處理。
通過以上檢測裝置支撐,本實施例實現了一種砂輪表面粗糙度和磨粒分布狀態的檢測及評價方法,具體包括如下步驟:
步驟1:檢測裝置的準備工作;將被測砂輪5安裝在工具機主軸6上,將上述檢測裝置安裝連接完畢;啟動檢測裝置,工具機工作檯帶動雷射位移傳感器1移動,使雷射位移傳感器1位於被測砂輪5表面的前方,雷射光斑通過被測砂輪5軸的中心。
步驟2:利用雷射位移傳感器1採集砂輪5表面圓周方向輪廓數據,具體包括步驟2.1-2.3;
步驟2.1:啟動工具機主軸6,帶動被測砂輪5勻速旋轉。
步驟2.2:設置雷射位移傳感器1的參數;根據被測砂輪5的直徑、被測砂輪5的轉速和磨粒直徑這些條件參量,通過控制器2設置雷射位移傳感器1的採樣頻率f和採樣長度l;採樣頻率f和採樣長度l滿足式(1)所示關係:
式(1)中,ns是被測砂輪5的轉速,單位r/min;ds是被測砂輪5的直徑,單位mm;dm是被測砂輪5的表面磨粒直徑,單位mm;採樣頻率f單位為hz;採樣長度l單位為個;
本實施例中被測砂輪5的直徑ds為150mm、被測砂輪5的轉速ns為500r/min、磨粒直徑為0.1mm;根據這些條件參量通過控制器2設置雷射位移傳感器1的採樣頻率f=200khz,採樣長度l=300000。
步驟2.3:雷射位移傳感器1對旋轉的被測砂輪5的外圓表面掃描採樣,將採樣點的相對高度,即被測砂輪5的表面圓周方向輪廓數據,傳輸至計算機4。
步驟3:對傳輸至計算機4的原始採樣數據進行降噪處理,具體包括步驟3.1-3.5;
步驟3.1:將傳輸至計算機4的原始採樣數據構建採樣數據數組y1={y1,y2,…,yl},並將y1中數據點逐一進行編號,構建採樣點坐標數組x1={1,2,…,l}。
步驟3.2:對步驟3.1中的原始採樣數據數組y1進行濾波去噪,濾波原理為,砂輪表面不超過寬度閾值j範圍內的採樣高度值,其變化幅度不應超過幅度閾值h,寬度閾值j是指雷射位移傳感器1採樣數據段中數據點的個數的合理值,幅度閾值h是指雷射位移傳感器1採樣數據段中數據點的差值的合理值,寬度閾值j和幅度閾值h優選地根據砂輪表面磨粒直徑dm、雷射位移傳感器採樣頻率f和砂輪轉速ns進行設置,寬度閾值j一般設置為砂輪外圓一周採樣點數的幅度閾值h一般設置為砂輪磨粒直徑的0.8~1.5倍,具體值可以依據濾波效果和實際經驗進行微調後確定。
雷射光斑照射到砂輪表面磨粒的邊緣或兩磨粒交界處等材料介質非均質的位置時,雷射位移傳感器1會輸出過大或過小的噪點數據,為濾除噪點數據,本實施例中採用以下濾波去噪方法:首先將數組y1中的每個採樣點數據與相鄰j個採樣點數據依次構成數據段,計算各數據段的極差值,然後將極差值與幅度閾值h比較,若超出幅度閾值h,則認為該數據段中存在噪點數據並捨棄,否則認為該數據段中所有數據點均為有效數據,然後提取各個數據段中的有效數據點並按照其對應坐標進行排列重組,其中坐標相同的同一數據點不重複提取,即可將噪點數據置為空值,獲得濾波後數據;本實施例中,j取值50,閾值h取值0.1。
步驟3.3:對步驟3.2濾波去噪後的數據數組進行線性插值處理,以補充濾波去除的數據點,獲得新的數據數組y2={y′1,y′2,…,y′l},y2的坐標數組仍為x1;線性插值的方法為:如插值在(xj,yj)和(xj+1,yj+1)兩個點之間,則在連接兩點的線段間進行插值,插值點(x,yj(x))滿足下式所示關係,
步驟3.4:對步驟3.3線性插值處理後獲得的數據數組y2,計算其移動平均數,即截取長度為q的滑動數據段,q為奇數,截取滑動數據段的長度q時優選地根據砂輪轉速ns和雷射位移傳感器1的採樣頻率f進行設置,一般設置為f/ns的2倍,但q的設置值一般不影響計算結果;利用每個數據段的平均數構建平均線數據數組利用每個數據段的中心位置坐標構建平均線坐標數組本實施例中q的取值799。
步驟3.5:剔除奇異數據點並進行線性插值補充;對步驟3.3線性插值處理後獲得的數據數組y2和步驟3.4計算得到的平均線數據數組ym之間的偏移量進行分布統計,將偏離幅度大,且分布概率低的數組y2中的奇異數據點剔除,剔除的奇異數據點數量不超過數組y2中數據總數量的3%,本實施例中將分布概率低於2%的奇異數據點剔除;剔除的數據點採用線性插值補充,獲得新的數據數組y3的坐標數組
步驟4:計算得到與被測砂輪5表面粗糙度相關的評價參量:輪廓平均偏差ra、輪廓偏差一致度pa、正輪廓平均偏差rap、負輪廓平均偏差ram、輪廓平均偏差ra的均值和標準差pc,具體包括步驟4.1-4.5。
步驟4.1:計算得到中位線數據數組yu和中位線坐標數組xu,具體包括步驟4.1.1-4.1.3。
砂輪表面粗糙度的評定需要首先確定輪廓測量數據曲線的中位線,採用平均線數據數組ym作為中位線,則粗糙度參數的計算結果易受參數q取值影響,為此,針對平均線數據數組ym作曲線擬合,以擬合曲線作為中位線,則擬合曲線代表了砂輪表面的宏觀輪廓信息,不僅粗糙度參數的計算結果不受參數q取值影響,而且砂輪表面粗糙度的評價也更符合砂輪磨削過程中的實際工況狀態。
在曲線擬合時,由於數據總量有限,會造成數據段的邊緣擬合失真的情況,為解決該問題,數據段的曲線擬合時採用「截多取少」的方法,即針對有效數據段的前後1.5倍長度數據進行曲線擬合,然後截取中部有效數據段的擬合結果,這樣,截取的中部擬合結果中不存在邊緣擬合失真的問題。
步驟4.1.1:按照取樣周期1/k和評定長度m對步驟3.4中的平均線數據數組ym進行截取;k和m均為正整數;截取方法為:砂輪圓周表面一周的採樣點數為個,從數組ym中截取時,共截取m段,每段長度為個數據點,每段截取的起始點坐標分別為
經過截取後獲得m個數組分別為:
數組ym1、ym2、……、ymm的坐標數組分別為
步驟4.1.2:針對步驟4.1.1中的數組ym1、ym2、……、ymm,利用數學的最小二乘法依次對各數組中數據進行曲線擬合,擬合後獲得ym1、ym2、……、ymm對應的擬合數組分別為:
擬合數組yn1、yn2、……、ynm的坐標數組仍為xm1、xm2、……、xmm;本實施例中,選擇最小二乘法進行多項式曲線擬合,多項式階數取值10。
步驟4.1.3:針對步驟4.1.2中的擬合數組yn1、yn2、……、ynm,依次截取各數組的中間個數據點,構成子集數組yu1、yu2、……、yum;
擬合數組yn1、yn2、……、ynm對應的子集數組分別為:
子集數組yu1、yu2、……、yum的坐標數組分別為:
分別將子集數組yu1、yu2、……、yum的數據點依次順序排列,構成中位線數據數組同樣的,分別將子集數組yu1、yu2、……、yum的坐標數組xu1、xu2、……、xum的數據點依次順序排列,構成中位線坐標數組
步驟4.2:計算步驟3.5中的剔除奇異數據點並插值補充後的數據數組y3相對於步驟4.1.3中的中位線數據數組yu的坐標對應的數據點的偏移量,獲得輪廓偏移量數組輪廓偏移量數組ys的坐標數組xs仍為xu,即
為方便後續表述,將輪廓偏移量數組ys的坐標按順序重新排號,即輪廓偏移量數組ys的坐標數組xs調整為
步驟4.3:利用步驟4.2中的輪廓偏移量數組ys按照取樣周期1/k和評定長度m計算輪廓平均偏差ra以及輪廓偏差一致度pa。
式(2)(3)中,ns是被測砂輪5的轉速,單位r/min;f是雷射位移傳感器1的採樣頻率,單位hz;ysi為偏移量數組ys中的數據點;k和m為正整數。
輪廓平均偏差ra用來評價砂輪表面圓周方向的整體或局部的粗糙程度;輪廓偏差一致度pa用來評價砂輪表面圓周方向局部粗糙度的一致性;砂輪表面越粗糙,則輪廓平均偏差ra值越大;砂輪表面圓周方向局部粗糙度的一致性越差,則輪廓偏差一致度pa越大。
當需要評定砂輪5表面圓周方向的整體粗糙程度時,不兼顧軸向,取樣周期中k取值為1;當需要評定砂輪5表面圓周方向的局部粗糙程度時,取樣周期中k取值為大於1的正整數,評定長度m取值為1;當需要評價砂輪5表面圓周方向局部粗糙度的一致性時,取樣周期中k和評定長度m相等,且均為大於1的正整數;本實施例中,ns=500r/min,f=200khz,評定砂輪5表面圓周方向的整體粗糙程度時,k=1,m=3;評定砂輪5表面圓周方向的局部粗糙程度時,k=8,m=1;評價砂輪5表面圓周方向局部粗糙度的一致性時,k=m=8。
步驟4.4:計算正輪廓平均偏差rap和負輪廓平均偏差ram;將步驟4.2中的輪廓偏移量數組ys中的正數和負數分別篩選出來,構建正輪廓偏移量數組ysp和負輪廓偏移量數組ysm,將數組ysp和ysm分別按照步驟4.3中的取樣周期1/k和評定長度m計算正輪廓平均偏差rap和負輪廓平均偏差ram,
式(4)中,{yspa,yspa+1,…,yspb}為輪廓偏移量數組ys子集數組中的正數,{yspc,yspc+1,…,yspd}為輪廓偏移量數組ys子集數組中的正數;
ysp={yspa,…,yspb,...,yspc,…,yspd}。
式(5)中,{ysma1,ysma1+1,…,ysmb1}為輪廓偏移量數組ys子集數組中的負數,{ysmc1,ysmc1+1,…,ysmd1}為輪廓偏移量數組ys子集數組中的負數;
ysm={ysma1,…,ysmb1,...,ysmc1,…,ysmd1}。
正輪廓平均偏差rap和負輪廓平均偏差ram用來評價被測砂輪5表面的鈍化狀態;被測砂輪5修整後,表面磨粒出露高度大且符合正態分布,被測砂輪5較鋒利,此時正輪廓平均偏差rap和負輪廓平均偏差ram基本相等;被測砂輪5磨削鈍化後,表面磨粒脫落或損耗,磨粒出露高度小且基本一致,被測砂輪5不鋒利,此時正輪廓平均偏差rap明顯變小,負輪廓平均偏差ram不變或增大;正輪廓平均偏差rap越小,負輪廓平均偏差ram與正輪廓平均偏差rap的差值越大,則被測砂輪5鈍化狀態越嚴重。
步驟4.5:計算均值和標準差pc;如果被測砂輪5寬度較大,需要對被測砂輪5表面的平均粗糙度進行綜合評價,將雷射位移傳感器1沿被測砂輪5軸向平移,使雷射光斑位於被測砂輪5一側邊緣,然後雷射位移傳感器向另一側平移一段距離e,重複步驟2.3至步驟4.3,計算得輪廓平均偏差ra2,如此循環往復,直到雷射光斑位於砂輪的另一側邊緣時結束,共測量n-1次,得到ra2、ra3、ra4、…、ran,計算ra2、ra3、ra4、…、ran的均值和標準差pc,為了兼顧被測砂輪5圓周方向和軸向,從第2次到第n-1次循環k取值均為1;
雷射位移傳感器的平移距離e滿足式(8)所示關係:
0.9ws<(n-2)e<ws(8)
式(8)中,ws是被測砂輪軸向寬度,單位mm;
用來綜合評價砂輪5表面,兼顧整個軸向寬度的表面,沿圓周方向的平均粗糙程度;pc用來評價被測砂輪5表面圓周方向粗糙度在軸向不同位置的一致性。
步驟5:計算得到與被測砂輪5表面磨粒分布密度和均勻性相關的評價參量:砂輪表面圓周方向輪廓曲線的峰值間距s、磨粒直徑與峰間距佔比δ、峰值間距離散度sp、砂輪表面圓周方向輪廓曲線的峰值間距s的均值磨粒直徑與峰間距佔比δ的均值和峰值間距離散度sp的均值具體包括步驟5.1-5.3。
步驟5.1:尋找輪廓曲線的波峰值及其位置坐標;將步驟3.5中剔除奇異數據點並插值補充後的數據數組y3及其坐標數組x3導入二維直角坐標系,繪製出被測砂輪5表面圓周方向的輪廓曲線,通過差值法和閾值法尋找輪廓曲線的波峰值及其位置坐標。
差值法和閾值法尋找輪廓曲線波峰的原理為:輪廓曲線中後一位置採樣點和前一位置採樣點的差值可以重新形成一個新的差值波形,差值波形中由正轉負過零位置對應輪廓曲線中的採樣點為準波峰值,如果差值波形中由正轉負過零位置前的正值數據長度超過一定長度閾值r且正值數據幅度超過一定幅度閾值i,並且該位置後的負值數據長度超過一定長度閾值r且負值數據幅度超過一定幅度閾值i,可認定該位置對應輪廓曲線中的採樣點為波峰值,長度閾值r是指傳感器採樣數據段中數據點的個數的合理值,幅度閾值i是指傳感器採樣數據段中數據點的差值的合理值,優選地長度閾值r設置為2~4,幅度閾值i為砂輪磨粒直徑的本實施例中,如果差值波形中由正轉負過零位置前的正值數據長度超過2,且幅度超過0.01,並且該位置後的負值數據長度超過2,且幅度超過-0.01,可認定該位置對應輪廓曲線中的採樣點為波峰值。
步驟5.2:計算被測砂輪5表面圓周方向輪廓曲線的峰值間距s、磨粒直徑與峰間距佔比δ以及峰值間距離散度sp;根據步驟5.1中尋找得到的數據數組y3中所有的波峰值及其在坐標數組x3中對應的位置坐標,從坐標數組x3中截取被測砂輪5表面一個圓周的波峰值所對應的位置坐標,構建數組xp={n1,n2,…,nt};由數組xp中相鄰兩元素的差值,計算被測砂輪5表面圓周方向輪廓曲線的峰值間距s、磨粒直徑與峰值間距佔比δ以及峰值間距離散度sp,
式(9)(10)(11)中,ns是被測砂輪5的轉速,單位r/min;ds是被測砂輪5的直徑,單位mm;dm是被測砂輪5的表面磨粒直徑,單位mm;f是雷射位移傳感器1採樣頻率,單位hz;本實施例中ns=500r/min,f=200khz,ds=150mm,dm=0.1mm。
峰值間距s用來評價被測砂輪5表面圓周方向磨粒分布的平均間距;磨粒直徑與峰間距佔比δ用來評價被測砂輪5表面圓周方向磨粒分布的密度;峰值間距離散度sp用來評價被測砂輪5表面圓周方向磨粒分布的均勻性。
步驟5.3:分別計算被測砂輪5表面圓周方向輪廓曲線的峰值間距s、磨粒直徑與峰間距佔比δ以及峰值間距離散度sp的均值和將雷射位移傳感器1沿被測砂輪5軸向平移,使雷射光斑位於砂輪一側邊緣,然後雷射位移傳感器1向另一側平移一段距離,平移規則與步驟4.4中的相同,重複步驟2.3至步驟3.5,以及步驟5.1和步驟5.2,計算得s2、δ2以及sp2,如此循環往復,計算得s3、δ3、sp3,s4、δ4、sp4,……,最後計算各參數均值
峰值間距s、磨粒直徑與峰間距佔比δ以及峰值間距離散度sp的均值和用來針對整個被測砂輪5表面,兼顧整個軸向寬度的表面,沿圓周方向磨粒分布的密度和均勻性進行評價。
通過上述步驟,本實施例可以達到如下技術效果:
(1)本發明利用雷射位移傳感器高速率、高精度的掃描採集能力以及計算機的高效數據處理能力,實現砂輪表面粗糙度和磨粒分布狀態的檢測及分析評價,並分別針對砂輪表面圓周方向的粗糙度、磨粒分布密度和分布均勻性計算出相應的評價參量,克服了目前砂輪表面粗糙度和磨粒分布狀態的檢測成本高、且耗時費力又難以全面評價的困難,為砂輪製造和修整工藝的改進提供準確依據,對提高磨削加工質量和效率具有重要意義。
(2)本發明採用非接觸式檢測方法,檢測過程中不會損耗量儀,檢測成本極低;檢測對象可以是陶瓷、樹脂、金屬等各種結合劑類型的砂輪,不受砂輪直徑、寬度等尺寸條件的限制,還可以檢測各種粒度型號的砂輪,檢測適應性好、通用性強。
(3)本發明可以在工具機不停機、不拆卸砂輪的條件下進行檢測,不受工具機特性限制,實現在機檢測;檢測裝置的安裝和操作方便快捷,計算機快速處理數據,檢測效率高。
(4)本發明不僅可以通過輪廓平均偏差ra評價砂輪圓周方向的整體和局部粗糙度,通過正輪廓平均偏差rap和負輪廓平均偏差ram評價砂輪表面的鈍化狀態,通過峰值間距s、磨粒直徑與峰間距佔比δ、峰值間距離散度sp評價砂輪表面圓周方向磨粒分布的密度和均勻性,還可以利用各參量的均值及標準差評價砂輪表面,兼顧整個軸向寬度的表面,各參量的平均水平及離散狀態。
最後應說明的是:以上實施例僅用以說明本發明的技術方案,而非對其限制;儘管參照前述各實施例對本發明進行了詳細的說明,本領域的普通技術人員應當理解:其依然可以對前述實施例所記載的技術方案進行修改,或者對其中部分或者全部技術特徵進行等同替換;而這些修改或者替換,並不使相應技術方案的本質脫離本發明實施例技術方案的範圍。