自動取料機構的取料方法與流程
2023-07-23 06:39:16 1
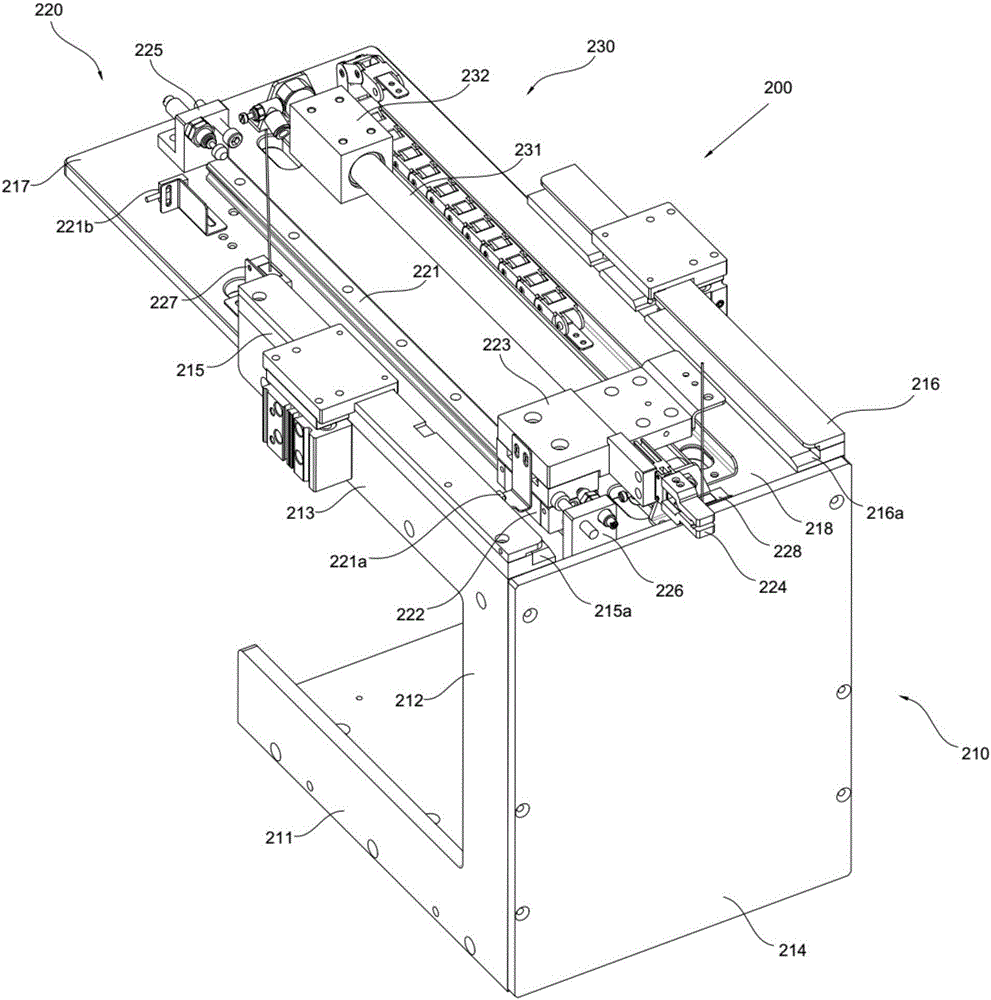
本發明涉及自動化設備領域,特別涉及一種自動取料機構的取料方法。
背景技術:
在機械加工、裝配過程中,工件及零部件的供給、上料及搬運等工序所需費用約佔全部費用的1/3以上,所費工時約佔全部工時的2/3以上,而且絕大多數的事故都發生在這些工序中。尤其是在成批大量生產的場合,當待加工或裝配的零件很小,而加工或裝配精度要求很高且機動工時很短時,取料是一項重複而繁重的作業。所以,為了提高加工與裝配精度、減輕作業者的勞動強度,提高生產效率,實有必要開發一種自動取料機構的取料方法,用以解決上述問題。
技術實現要素:
針對現有技術中存在的不足之處,本發明的目的是提供一種自動取料機構的取料方法,其能夠提高加工與裝配精度、減輕作業者的勞動強度,提高生產效率,保證安全生產。
為了實現根據本發明的上述目的和其他優點,提供了一種自動取料機構的取料方法,該自動取料機構包括:
控制系統;
具有取料平臺的機架,
其中,所述機架頂部的左右兩端分別設有左導軌及右導軌,所述左導軌及右導軌相距一定的距離從而構成位於兩者之間的取料通道,所取料通道中設有夾取組件及驅動組件,所述夾取組件在驅動組件的驅動下可在所述取料通道中往復行走,所述控制系統用於控制所述夾取組件的夾取參數、所述驅動組件的驅動參數,其特徵在於,該方法包括以下步驟:
(a).所述夾取組件從裝有料盤的上料機構中取出裝有零配件的料盤;
(b).所述驅動組件驅動夾取組件將料盤夾送至預定位置等待轉移;
(c).待料盤上所有零配件轉移完後,所述驅動組件驅動所述夾取組件將空料盤送入上料機構中;
(d).可選擇的重複步驟(a)、(b)、及(c),直至將上料機構中的所有零配件轉移完畢。
本發明與現有技術相比,至少包括以下有益效果:
其能夠提高加工與裝配精度、減輕作業者的勞動強度,提高生產效率,保證安全生產。
本發明的其它優點、目標和特徵將部分通過下面的說明體現,部分還將通過對本發明的研究和實踐而為本領域的技術人員所理解。
附圖說明
圖1為根據本發明所述的自動取料機構的三維結構視圖;
圖2為根據本發明所述的自動取料機構與上料機構相互配合的三維結構視圖,圖中夾取組件處於待取料工位;
圖3為根據本發明所述的自動取料機構與上料機構相互配合的三維結構視圖,圖中夾取組件處於取料完成工位;
圖4為根據本發明所述的自動取料機構中託盤組件的三維結構視圖。
具體實施方式
下面結合附圖對本發明做進一步的詳細說明,本發明的前述和其它目的、特徵、方面和優點將變得更加明顯,以令本領域技術人員參照說明書文字能夠據以實施。
參照圖1,自動取料機構200包括:
控制系統(略畫);
具有取料平臺217的機架210,
其中,機架210頂部的左右兩端分別設有左導軌215及右導軌216,左導軌215及右導軌216相距一定的距離從而構成位於兩者之間的取料通道218,取料通道218的寬度大於料盤的寬度,取料通道218中設有夾取組件220及驅動組件230,夾取組件220在驅動組件230的驅動下可在取料通道218中往復行走,夾取組件220及驅動組件230均與所述控制系統電連接。在一實施方式中,機架210由水平底框211、豎直支撐框212、及水平頂框213依次相接而成,且水平底框211、豎直支撐框212、及水平頂框213固接成一體式的冂字形結構,豎直支撐框212的前側還固接有加強板214。
再次參照圖1,左導軌215及右導軌216的內側分別設有左導槽215a及右導槽216a,左導槽215a及右導槽216a處於同一水平面上,左導槽215a及右導槽216a用於支撐及引導料盤在取料通道218中往復滑移。
參照圖1,夾取組件220包括:
與左導軌215或右導軌216相平行的夾具導軌221;
與夾具導軌221相配接的夾具滑塊222;
與夾具滑塊222相固接的夾具安裝座223;以及
安裝於夾具安裝座223前端的夾具224,
其中,夾具導軌221用於支撐及引導夾具滑塊222往復水平滑行,夾具導軌221的頂面處於左導槽215a及右導槽216a的所在平面之下,夾具224與所述控制系統電連接。在優選的實施方式中,夾具導軌221的前後兩端分別設有與夾具滑塊222相對的前緩衝柱226及後緩衝柱225,從而使得夾具滑塊222運動到前後兩端時能有個緩衝力對其運動速度進行緩衝,在降低運行噪聲的同時能延長各個部件的工作壽命。在優選的實施方式中,夾具導軌221的前後邊緣的旁側分別設有用於感應夾具滑塊222位置的前端位置傳感器221a及後端位置傳感器221b,前端位置傳感器221a及後端位置傳感器221b均與所述控制系統電連接,從而能夠對夾具滑塊222的運動位置進行精確定位,保證傳動位置及制動的精確性。
驅動組件230包括:
設於夾具導軌221旁側的驅動導向柱231;
套設於驅動導向柱231之上的傳動滑塊232;以及
用於驅動傳動滑塊232滑動的驅動器,
其中,驅動導向柱231與夾具導軌221相平行,驅動導向柱231的頂端低於左導槽215a及右導槽216a的所在平面,傳動滑塊232與夾具安裝座223相固接,所述驅動器與所述控制系統電連接。
再次參照圖1,取料通道218的前端設有前端光電傳感器228,該前端光電傳感器228用於感應滿載料盤的末端邊緣位置或空載料盤的前端邊緣位置,取料通道218的末端設有末端光電傳感器227,該末端光電傳感器227用於感應滿載料盤的前端邊緣位置或空載料盤的末端邊緣位置,前端光電傳感器228及末端光電傳感器227均與所述控制系統電連接。
參照圖3,在一實施方式中,左導槽215a及右導槽216a中卡接有託盤組件240,具體地,參照圖4,託盤組件240包括託盤底板241、設於託盤底板241左側的左護翼242、設於託盤底板241左側的右護翼244、以及設於託盤底板241後側的後護翼243,左護翼242、後護翼243、及右護翼244依次環繞相接而成的放置通道245,料盤115放置於放置通道245中,其中,左護翼242、後護翼243、及右護翼244的底部內側均設有相應的卡接槽,卡接槽用於卡接料盤115的外周下沿115a,後護翼243中與夾具224相對處設有與夾具224相匹配的夾取槽243a,左護翼242及右護翼244的前端分別設有左引導斜面242a及右引導斜面244a。
圖2及圖3均示出了根據本發明所述的自動取料機構的取料方法200與上料機構100相互配合的三維結構視圖,圖2中夾取組件220位於取料通道218的前端,處於待取料工位,圖3中夾取組件220位於取料通道218的末端,處於取料完成工位。
一種自動取料機構的取料方法,該方法包括以下步驟:
(a).夾取組件220從裝有料盤115的上料機構100中取出裝有零配件的料盤115;
(b).驅動組件230驅動夾取組件220將料盤115夾送至預定位置等待轉移;
(c).待料盤115上所有零配件轉移完後,驅動組件230驅動夾取組件220將空料盤115送入上料機構100中;
(d).可選擇的重複步驟(a)、(b)、及(c),直至將上料機構100中的所有零配件轉移完畢。
工作原理:參照圖2及圖3,上料機構100中設有託盤120,託盤120中設有兩個放箱槽,分別為左放置槽122及右放置槽123,左放置槽122及右放置槽123均放置有載滿裝有待裝配零部件料盤115的彈夾料箱110,為了便於標記,圖1、圖2及圖3中均只示出了一個彈夾料箱110,但是這並不妨礙本領域技術人員的理解。夾取組件220往返於取料通道218的前端與末端之間,從而選擇性地從彈夾料箱110中取出滿載零部件的料盤115到指定工位,或者放入空載的料盤115,如此循環往復,直至將彈夾料箱110中的待裝配零部件全部加工或裝配完畢,當其中一個彈夾料箱110取空後,譬如左放置槽122中的彈夾料箱110取空後,上料機構100將右放置槽123中的彈夾料箱110轉移到取料工位處進行取料作業,直至取完,同時將左放置槽122中的空彈夾料箱110替換上下一個滿載的空彈夾料箱110,如此循環往復直至將所有彈夾料箱110中的待裝配零配件取完。
這裡說明的設備數量和處理規模是用來簡化本發明的說明的。對本發明的應用、修改和變化對本領域的技術人員來說是顯而易見的。
儘管本發明的實施方案已公開如上,但其並不僅限於說明書和實施方式中所列運用,它完全可以被適用於各種適合本發明的領域,對於熟悉本領域的人員而言,可容易地實現另外的修改,因此在不背離權利要求及等同範圍所限定的一般概念下,本發明並不限於特定的細節和這裡示出與描述的圖例。