閥體組件、活塞單元及油壓減振器的製作方法
2023-07-12 13:31:31 2
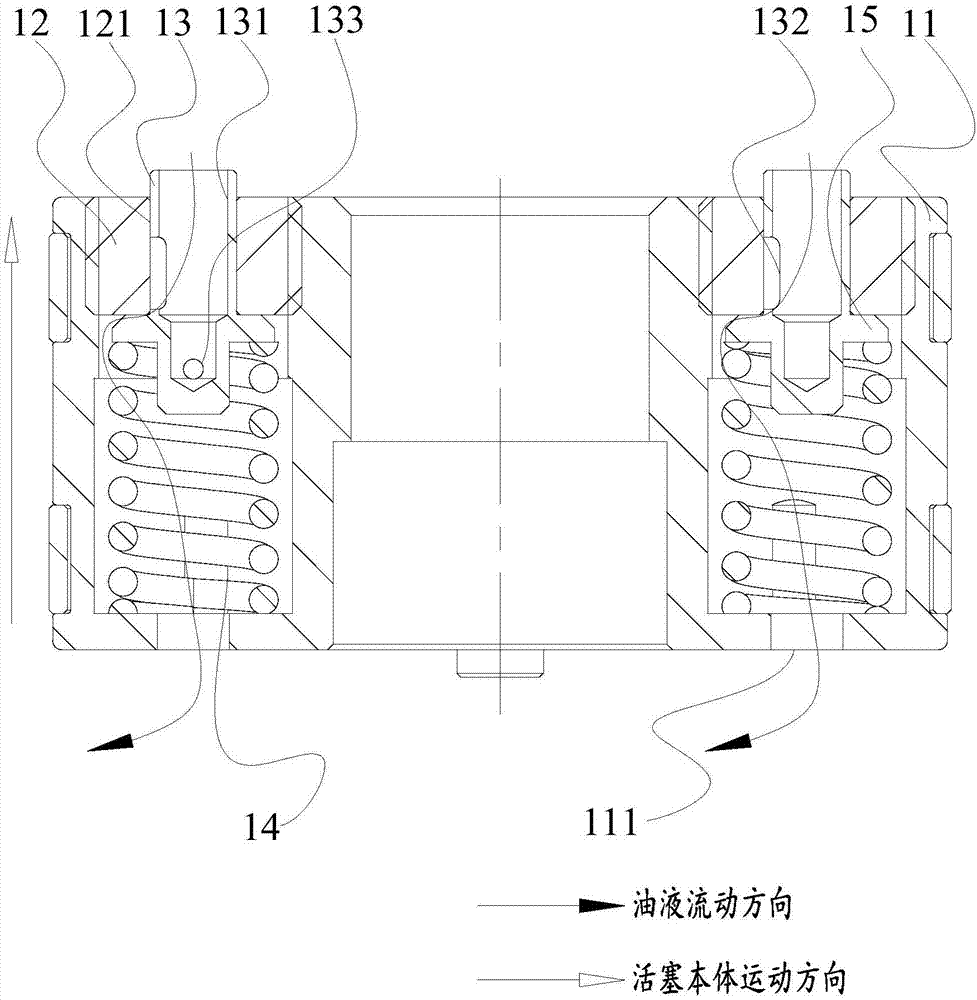
本發明屬於軌道機車車輛用油壓減振器技術領域,尤其涉及一種閥體組件、活塞單元及油壓減振器。
背景技術:
軌道機車車輛用油壓減振器包括工作缸以及置於工作缸中的活塞單元,所述油缸中充注有卸荷油液,參見圖1和圖2,所述活塞單元包括活塞本體11,所述活塞本體11的頂部設置有一個或者多個閥體組件,所述每個閥體組件均包括閥罩12、閥芯13和彈簧14。所述閥罩12和閥芯13均為圓柱狀結構,所述閥罩12軸向設置有通孔121,所述閥芯13軸向設置有盲孔131,所述閥罩12的外表面與所述活塞本體11螺紋連接,所述閥芯13套設於所述閥罩12的通孔121中,所述通孔121對所述閥芯13的運動起導向作用,且所述閥芯13外表面與所述通孔121內表面間隙配合,從而封閉油路;所述閥芯13盲孔131的底部側壁上設置有方形卸荷口132,所述閥芯13頂部通過彈簧14與所述活塞本體11連接以使所述閥芯13能夠上下移動,所述閥芯上設置有封油部15,所述彈簧14可壓迫所述封油部15上表面與所述閥罩12下表面相貼合以封閉油路,所述活塞本體11的底面上與所述閥芯13相對應的位置處設置有排出口111;當所述活塞本體11向上運動時,活塞本體11上方的油液壓力增加,所述閥芯13在油液的壓力下向下移動,所述卸荷口132與所述閥罩12通孔121內表面分離,所述活塞本體11上方油液依次通過所述閥芯13的盲孔131、卸荷口132及活塞本體11的排出口111,從活塞本體11上方流入活塞本體11下方,從而完成卸荷過程,達到減振效果。為了使油壓減振器具有雙向的卸荷和減振效果,所述活塞本體11底部上進一步設置有閥體組件,所述活塞本體11底部的閥體組件與活塞本體11頂部的閥體組件相互背離且交錯設置。
由上述可知,所述閥罩內表面與所述閥芯外表面之間的間隙配合,要保證穩定流暢地導向所述閥芯的上下運動,因此,所述閥罩內表面與所述閥芯外表面之間的配合形位公差對閥體組件和活塞單元,以及對整個油壓減振器的質量穩定性具有非常重要的影響。但是,在加工卸荷口的過程中,不可避免地要夾持住所述閥芯外表面,同時閥芯外表面也受到來自加工刀具的突變力量衝擊,進而影響所述閥芯外表面的圓柱度和垂直度,影響所述閥罩內表面與所述閥芯外表面之間的間隙配合公差,進而影響所述油壓減振器質量和精度的穩定性。
因此,設計出一種具有穩定的質量和精度性能的閥體組件、應用該閥體組件的活塞單元以及應用該活塞單元的油壓減振器,對於本領域技術人員來說是非常必要的。
技術實現要素:
本發明針對現有的油壓減振器質量和精度不穩定的技術問題,提出一種具有穩定的質量和精度性能的閥體組件、應用該閥體組件的活塞單元以及應用該活塞單元的油壓減振器。
為了達到上述目的,本發明採用的技術方案為:
一種閥體組件,設置於油壓減振器的活塞本體上,包括閥罩,以及可活動地套設於所述閥罩內部的閥芯,所述閥罩的外表面與所述活塞本體連接,所述閥罩設置有導向孔,所述閥芯套設於所述導向孔中,所述閥芯與所述導向孔間隙配合以封閉油路;所述閥芯與所述活塞本體彈性連接,所述閥罩背離所述導向孔的一端設置有卸荷孔,所述閥罩上設置所述導向孔的一端進一步設置有流體孔,所述流體孔與所述卸荷孔相連通;所述閥芯進一步套設於所述卸荷孔中,所述閥芯的外表面與所述卸荷孔的內表面間隙配合以流通油液。
作為優選,所述閥芯進一步設置有可與所述閥罩相配合以封閉油路的封油部,所述封油部設置於所述閥罩下方,所述封油部的頂面與所述閥罩的底面貼合。
作為優選,所述閥芯進一步設置有錐形部,所述錐形部套設於所述卸荷孔中,所述錐形部與所述卸荷孔間隙配合以流通油液。
作為優選,所述閥罩進一步設置有儲油腔,所述儲油腔的頂端分別與所述導向孔和流體孔相連通,所述儲油腔的底端與所述卸荷孔相連通。
作為優選,所述閥芯背離所述活塞本體的一端軸向設置有節流孔,所述閥芯的相對另一端軸向設置有第二盲孔,所述節流孔與所述第二盲孔相連通。
本發明進一步提供一種活塞單元,設置於油壓減振器中,包括活塞本體,所述活塞本體上設置有前述的閥體組件。
作為優選,所述閥體組件軸向設置於所述活塞本體的頂部和底部。
作為優選,所述活塞本體頂部的閥體組件與所述活塞本體底部的閥體組件在軸向上相互交錯設置。
作為優選,所述活塞本體頂部的閥體組件沿周向分布於所述活塞本體的頂部;所述活塞本體底部的閥體組件沿周向分布於所述活塞本體的底部。
本發明進一步提供一種油壓減振器,包括工作缸,所述工作缸中設置有前述的活塞單元。
與現有技術相比,本發明的優點和積極效果在於:
1、本發明的閥體組件在所述閥罩上設置流體孔,所述活塞本體上方的油液依次通過所述流體孔和排出口來實現卸荷和減振功能,避免了現有技術中在所述閥芯盲孔側壁上加工卸荷口時對所述閥罩和閥芯之間的形位公差的影響,保證了所述閥罩與閥芯之間的配合精度,進而使本發明閥體組件具有穩定的質量和精度。
2、本發明的閥體組件,所述活塞本體上方的油液分別流過所述卸荷孔與所述閥芯之間的通路、所述封油部的頂面與所述閥罩底面之間的通路時,均是在圓周方向上均勻流過,所述油液對所述閥芯產生的徑向力相互抵消,避免了所述閥芯的局部應力疲勞,進一步地提高了本發明閥體組件的質量和使用壽命。
3、本發明的閥體組件,所述閥芯上設置上設置錐形部,所述錐形部外表面與所述卸荷孔內表面之間形成變截面油液通路,避免了因所述閥芯剛向下運動時即使該處流通較多的油液量而造成瞬間卸荷的情況,使本發明的閥體組件平緩卸荷,進一步提高了質量穩定性,並使本發明的閥體組件滿足阻尼力與卸荷速度呈線性或類線性的要求。
4、本發明的閥體組件,所述閥罩進一步設置有儲油腔,所述儲油腔可緩衝所述閥芯向下運動瞬間所述油液對所述錐形部外表面的衝擊,進一步提高本發明閥體組件的質量穩定性。
5、本發明的閥體組件,所述節流孔設置於所述閥芯的頂端,與現有技術中的節流孔相比,不僅加工方便,而且加工時不會影響所述閥芯外表面與所述通孔內表面的配合精度。
附圖說明
圖1為現有技術油壓減振器活塞單元的結構示意圖;
圖2為圖1中a-a方向剖視圖;
圖3為本發明閥體組件的結構示意圖;
圖4為本發明閥體組件和活塞單元的俯視圖。
以上各圖中:11、活塞本體;111、排出口;12、閥罩;121、通孔;13、閥芯;131、盲孔;132、卸荷口;133、節流孔;14、彈簧;15、封油部;
21、活塞本體;211、排出口;22、閥罩;221、導向孔;222、卸荷孔;223、流體孔;224、儲油腔;23、閥芯;231、封油部;232、錐形部;233、節流孔;234、第二盲孔;24、彈簧。
具體實施方式
下面,通過示例性的實施方式對本發明進行具體描述。然而應當理解,在沒有進一步敘述的情況下,一個實施方式中的元件、結構和特徵也可以有益地結合到其他實施方式中。
在本發明的描述中,需要說明的是,軸向是指工作缸和活塞本體的軸向,也是活塞本體運動的方向;周向是指工作缸和活塞本體的圓周方向;徑向是指工作缸和活塞本體的半徑方向;術語「頂」、「底」「內」、「外」、「上」、「下」、「前」、「後」等指示的方位或位置關係為基於附圖2和附圖3所示的位置關係,僅是為了便於描述本發明和簡化描述,而不是指示或暗示所指的裝置或元件必須具有特定的方位、以特定的方位構造和操作,因此不能理解為對本發明的限制。此外,術語「第一」、「第二」僅用於描述目的,而不能理解為指示或暗示相對重要性。
參見圖3,圖3為本發明閥體組件的結構示意圖。如圖3所示,一種閥體組件,設置於油壓減振器的活塞本體21上,用於封閉或開啟油路以實現減震效果,所述油壓減振器內充注有油液,本發明的閥體組件包括閥罩22、閥芯23和彈簧24,所述閥罩22的外表面與所述活塞本體21螺紋連接,螺紋連接處打密封膠水以滿足封閉油路的要求;所述閥罩22軸向設置有導向孔221和卸荷孔222,所述閥芯23由上至下依次套設於所述導向孔221和卸荷孔222中,所述閥芯23頂部的外表面與所述導向孔221的內表面精密間隙配合,該間隙配合的精度滿足精確導向功能並且能夠封閉油路,所述閥芯23底部的外表面與所述卸荷孔222的內表面間隙配合以形成可使油液通過的通路;所述閥罩22進一步軸向設置有流體孔223,所述卸荷孔222的頂部分別與所述導向孔221和流體孔223相連通,所述活塞本體21上方的油液可通過所述流體孔223流入所述卸荷孔222與所述閥芯23之間通路中;所述閥芯23底面與所述活塞本體21的底面彈性連接,即所述閥芯23底面通過彈簧24與所述活塞本體21的底面相連,所述活塞本體21的底面與所述閥芯23相對應的位置設置有排出口211;當所述活塞本體21上方油液壓迫所述閥芯23向下運動時,所述彈簧24將被壓縮,所述流體孔223與所述活塞本體21下方油液相連通,從而使所述活塞本體21上方的油液依次通過所述流體孔223和排出口211與所述活塞本體21下方的油液相連通,進而實現卸荷和減振功能。本發明的閥體組件,通過在所述閥罩22上設置流體孔223來實現卸荷和減振功能,避免了現有技術中在所述閥芯13盲孔131側壁上加工卸荷口132時對所述閥罩12和閥芯13之間的形位公差的影響,保證了所述閥罩22與閥芯23之間的配合精度,進而使本發明閥體組件具有穩定的質量和精度性能。
進一步地,現有技術中的卸荷口132設置於所述閥芯13盲孔的一側,所述活塞本體11上方的油液均通過該卸荷口132流入所述活塞本體11下方,所述油液流過所述卸荷口132時不可避免地對所述卸荷口132相對一側的閥芯13側壁產生徑向力,進而影響所述閥芯13的使用壽命;本發明的閥體組件,所述活塞本體21上方的油液流過所述卸荷孔222與所述閥芯23之間的通路時,是在圓周方向上均勻流過,所述油液對所述閥芯23產生的徑向力相互抵消,避免了所述閥芯23的局部應力疲勞,進一步地提高了本發明閥體組件的質量和使用壽命。
繼續參見圖3,如圖3所示,所述閥芯23進一步設置有封油部231,所述封油部231位於所述可與所述閥罩22下方,所述封油部231的頂面與所述閥罩22的底面相鄰,調節所述彈簧24的預緊力使所述封油部231的頂面與所述閥罩22的底面貼合,以阻止所述卸荷孔222與所述閥芯23之間的油液與所述閥芯23底部的油液連通。
具體地,初始位置時,所述活塞本體21上方和下方的油液壓力平衡,所述閥芯23套設於所述導向孔221和卸荷孔222中,所述卸荷孔222與所述閥芯23之間通路通過所述流體孔223與所述活塞本體21上方的油液相連通,所述封油部231的頂面與所述閥罩22的底面相配合以封閉油路;當所述活塞本體21向上運動時,所述活塞本體21上方的油液壓力增加,所述活塞本體21上方的油液壓迫所述閥芯23和彈簧24,並使所述閥芯23向下運動和使所述彈簧24壓縮,從而使所述封油部231的頂面與所述閥罩22底面分離,進而打開油路,即,所述活塞本體21上方的油液依次通過所述流體孔223、所述卸荷孔222與所述閥芯23之間的通路、所述封油部231的頂面與所述閥罩22底面之間的通路流入所述閥芯23底部,並最終通過所述排出口211流入所述活塞本體21下方,使所述活塞本體21上方和下方的油液壓力相平衡,達到卸荷和減振效果;當所述活塞本體21停止運動時,所述彈簧24的回覆力使所述閥芯23向上運動,使所述封油部231的頂面與所述閥罩22底面再次貼合,從而使油路再次封閉。
參見圖3和圖4,如圖3和圖4所示,所述流體孔223設置於所述導向孔221圓周外部的周向環體內,且所述流體孔223可設置為一個或者多個,以滿足不同的卸荷和減振要求。當所述流體孔223為多個時,為了使卸荷過程中油液流通均勻,所述多個流體孔223均勻分布於所述導向孔221圓周外部的周向環體內。
繼續參見圖3,如圖3所示,所述閥芯23進一步設置有錐形部232,所述錐形部232套設於所述卸荷孔222中,所述錐形部232的外表面與所述卸荷孔222的內表面之間形成油液通路,並與所述流體孔223中的油液連通,從而可使所述活塞本體21上方的油液流過。所述錐形部232的尖端朝向所述導向孔221,即當所述閥芯23向下運動時,所述錐形部232外表面與所述卸荷孔222內表面之間的油液通路面積逐漸增加,從而使該處流過的油液量逐漸增加,避免了因所述閥芯23剛向下運動時即使該處流通較多的油液量而造成瞬間卸荷的情況,使本發明的閥體組件平緩卸荷,進一步提高了質量穩定性。
進一步地,隨著所述閥芯23繼續向下運動,所述彈簧24的壓縮量增加,即,使本發明的閥體組件產生更大的阻尼效果,同時所述閥芯23的向下運動導致所述錐形部232外表面與所述卸荷孔222內表面之間的油液通路面逐漸增加,該處流過的油液量增加,即達到快速卸荷的效果,使本發明的閥體組件滿足阻尼力與卸荷速度呈線性或類線性的要求。
繼續參見圖3,如圖3所示,所述閥罩22進一步設置有儲油腔224,所述儲油腔224位於所述導向孔221和卸荷孔222之間,且所述儲油腔224的頂端分別與所述導向孔221和流體孔223相連通,所述儲油腔224的底端與所述卸荷孔222相連通,因所述閥芯23與所述導向孔221的精密間隙配合可實現精確導向功能並能夠封閉油路,當所述閥芯23套設於所述導向孔221和卸荷孔222中時,所述活塞本體21上方的油液可通過所述流體孔223與所述儲油腔224相連通,所述儲油腔224可緩衝所述閥芯23向下運動瞬間所述油液對所述錐形部232外表面的衝擊進一步提高本發明閥體組件的質量穩定性。
繼續參見圖3,如圖3所示,所述閥芯23背離所述彈簧24的一端軸向設置有節流孔233,所述閥芯23的相對另一端軸向設置有第二盲孔234,所述節流孔233與所述第二盲孔234相連通。當所述活塞本體21產生細微的向上運動,即所述活塞本體21上方的油液壓力稍有增加,且該油液壓力不足以克服所述彈簧24的彈力時,所述活塞本體21上方的油液可通過所述節流孔233流入所述第二盲孔234中,並通過所述活塞本體21上的排出口211流入活塞本體21下方,從而實現卸荷和減振效果。
需要說明的是,參見圖1和圖2,現有技術中,所述閥芯13的盲孔131的底端徑向設置有節流孔133,所述節流孔133將所述盲孔131中的油液與所述活塞本體11下方的油液連通,當所述活塞本體11產生細微的向上運動時,所述活塞本體11上方的油液可依次通過所述盲孔131和節流孔133流入活塞本體11下方,以實現卸荷和減振效果。但是因所述節流孔133位於所述盲孔132的底面,加工不方便,而且在加工所述節流孔133時,需要夾持住所述閥芯13與所述閥罩12通孔121相配合的外表面,不可避免地會影響所述閥芯13外表面與所述通孔121內表面的配合精度。
進一步地,本發明的閥體組件,通過在所述閥芯23的頂端設置節流孔233,通過所述節流孔233和第二盲孔234使所述活塞本體21上下方的油液相連通,所述節流孔233設置在所述閥芯23的頂端,不僅加工方便,而且在加工所述節流孔233時,只需夾持住所述閥芯23最低端的外表面即可,該處的外表面是非配合表面,進而不會影響本發明閥體組件的配合精度,進一步提高了本發明閥體組件的質量和精度的穩定性。
為了進一步提高本發明閥體組件的密封性能,所述閥罩22與所述活塞本體21螺紋連接的螺紋副處塗抹有螺紋密封膠,以保證所述閥罩22安裝到位後位置穩固,並且提高了螺紋副的密封性能,進一步提高了本發明閥體組件餓質量穩定性。
本發明進一步提出一種活塞單元,設置於油壓減振器中,包括活塞本體21,所述活塞本體21上設置有前述的閥體組件。
繼續參見圖4,如圖4所示,所述閥體組件軸向設置於所述活塞本體21的頂部和底部,所述活塞本體21底部的閥體組件與所述活塞本體21頂部的閥體組件相互背離設置,即,所述活塞本體21頂部的閥體組件與所述活塞本體21底部的閥體組件關於所述活塞本體的中心水平面對稱設置。
為了使本發明的活塞單元順利實現雙向卸荷和減振功能,所述活塞本體21頂部的閥體組件與所述活塞本體21底部的閥體組件在軸向上相互交錯設置。
繼續參見圖4,如圖4所示,所述活塞本體21頂部的閥體組件可設置為一個或者多個,以滿足不同的減振要求。當所述活塞本體21頂部的閥體組件設置為多個時,所述多個閥體組件沿周向均勻分布於所述活塞本體21的頂部,以增加本發明活塞本體21向上運動時,活塞單元卸荷和減振過程中的穩定性。
具體地,當所述活塞本體21向上運動時,所述活塞本體21上方的油液壓力增加並壓迫所述活塞本體21頂部閥體組件的彈簧21壓縮,所述彈簧21帶動所述活塞本體21頂部閥體組件的閥芯23下降,從而使所述閥芯23封油部231頂面與所述閥罩22底面分離,所述活塞本體21上方的油液依次通過所述流體孔223、儲油腔224、錐形部232與卸荷孔222之間通道、排出口211流入所述活塞本體21下方,實現卸荷和減振效果。所述活塞本體21頂部的多個閥體組件中,其中一個或者多個的閥芯23頂部設置節流孔233,當所述活塞本體21向上運動引起的活塞本體21上方油液壓力的增加不足以壓縮彈簧21時,所述活塞本體21上方油液依次通過所述節流孔233和第二盲孔234流入所述活塞本體21下方,以實現卸荷和減振效果。
進一步地,所述活塞本體21底部的閥體組件可設置為一個或者多個,以滿足不同的減振要求。當所述活塞本體21底部的閥體組件設置為多個時,所述多個閥體組件沿周向均勻分布於所述活塞本體21的底部,以增加活塞單元21向下運動時,本發明活塞單元卸荷和減振過程中的穩定性。
具體地,當所述活塞本體21向下運動時,所述活塞本體21下方的油液壓力增加並壓迫所述活塞本體21底部閥體組件的彈簧21壓縮,所述彈簧21帶動所述活塞本體21底部閥體組件的閥芯23上升,從而使所述閥芯23封油部231底面與所述閥罩22頂面分離,所述活塞本體21下方的油液依次通過所述流體孔223、儲油腔224、錐形部232與卸荷孔222之間通道、排出口211流入所述活塞本體21上方,實現卸荷和減振效果。所述活塞本體21底部的多個閥體組件中,其中一個或者多個的閥芯23底部設置節流孔233,當所述活塞本體21向下運動引起的活塞本體21下方油液壓力的增加不足以壓縮彈簧21時,所述活塞本體21下方油液依次通過所述節流孔233和第二盲孔234流入所述活塞本體21上方,以實現卸荷和減振效果。
本發明進一步提出一種油壓減振器,包括工作缸,所述工作缸中設置有前述的活塞單元。在此不再細述。