一種內置連續絮狀耐磨層的碳纖維連續抽油杆的製作方法
2023-12-11 23:12:42
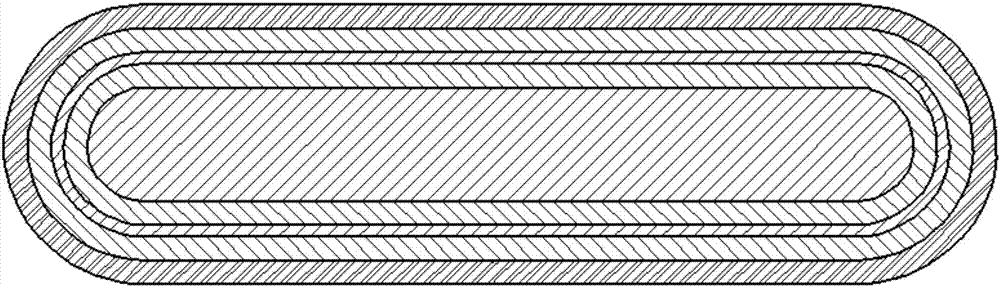
本發明屬於採油設備領域,尤其涉及一種內置連續絮狀耐磨層的碳纖維連續抽油杆。
背景技術:
碳纖維連續抽油杆,是近年來應用於抽油機上的新型抽油杆,與傳統的鋼製抽油杆相比,碳纖維抽油杆具有抗拉強度大,施工工藝簡單,施工周期短,成本低等諸多優點。然而,油田已應用的碳纖維連續抽油杆的耐磨性能較差,使用壽命有待提高。
為解決上述問題,科研人員研發了一系列的新型碳纖維抽油杆,這些新型抽油杆主要通過三種方式來改善抽油杆的耐磨性能:
一是在抽油杆的環氧樹脂內添加耐磨顆粒,通過碳化矽、氮化硼等硬質耐磨顆粒來改善耐磨性,但採用這種方式生產的抽油杆存在明顯不足,因為:向環氧樹脂中摻加耐磨顆粒時難以保證耐磨顆粒在環氧樹脂內分布的絕對均勻性,也就無法保證耐磨層的完整性,因此這種抽油杆存在耐磨性能盲區,嚴重影響抽油杆的整體耐磨性能。
二是在抽油杆的表面增加聚乙烯等外耐磨層,對於此種抽油杆,聚乙烯層雖然具有較好的耐磨性能,但硬度較小,容易在作業過程中受井壁的剮蹭而損壞。同時,聚乙烯層在抽油杆使用過程中存在脫落的可能。
三是在抽油杆內設置耐磨纖維層或耐磨織物層,這種結構的問題在於,成股的纖維或織物的浸膠性能有限,與環氧樹脂的結合度以及環氧樹脂的浸入度均比較差,致使構成耐磨纖維或耐磨織物的耐磨材料的耐磨性能大打折扣。
因此,有必要研發一種新型的碳纖維連續抽油杆來解決現有技術中存在的碳纖維連續抽油杆耐磨性能差的問題。
技術實現要素:
本發明提供一種內置連續絮狀耐磨層的碳纖維連續抽油杆,以解決上述背景技術中提出的問題。
本發明所解決的技術問題採用以下技術方案來實現:本發明提供一種內置連續絮狀耐磨層的碳纖維連續抽油杆,包括碳纖維芯體、耐磨層和環氧樹脂層,碳纖維芯體的外側設置有粗紗層,在粗砂層的外側設置耐磨層,耐磨層的外側設置有細紗層,所述的環氧樹脂層設置在細紗層的外側;
所述的粗紗層由細度為3000d的芳綸纖維製成,所述的耐磨層由棉絮狀的丙綸條包覆而成,所述的細紗層由細度為1100的芳綸纖維製成;所述的碳纖維、芳綸纖維以及丙綸條的長度方向均與抽油杆的軸線方向一致;
抽油杆中碳纖維的質量百分含量為28%-30%,粗紗層中的芳綸纖維的質量百分含量為22%-24%,丙綸條的質量百分含量為3%-4%,細紗層中的芳綸纖維的質量百分含量為10%-12%,其餘成分為環氧樹脂;
所述的碳纖維的規格為t300/6k;
所述的環氧樹脂層內摻加有耐磨顆粒。
優選地,所述的抽油杆的截面形狀為長條形。
優選地,所述的抽油杆的截面形狀為橢圓形。
本發明的有益效果為:本發明創造性地採用了獨特的棉絮狀內置丙綸耐磨層,並同時在環氧樹脂層內摻加了耐磨顆粒,這種抽油杆具有如下優點,
1、作為耐磨層的丙綸為條狀扁帶結構,丙綸條沿抽油杆的長度方向設置,丙綸條的寬度等於粗紗層外側圓柱面的周長,與在環氧樹脂內添加耐磨顆粒的耐磨結構相比,以丙綸為核心的耐磨層是均勻的、連續的、完整的,因此有效消除了性能盲區,改善了抽油杆的整體耐磨性能。
2、本發明設置了內外兩層耐磨結構(摻加了耐磨顆粒的環氧樹脂層和耐磨層),摻加了耐磨顆粒的環氧樹脂層雖然有存在性能盲區的可能,但仍可以防止耐磨層局部大範圍磨損,從而保護了耐磨層。
3、本發明採用的丙綸為棉絮狀結構,與現有技術中的成股的耐磨纖維或耐磨織物相比,環氧樹脂可以更充分地浸入到丙綸條內的每根纖維單絲之間,因此耐磨材料與環氧樹脂的結合度以及環氧樹脂的浸入度大大提高,從而使得耐磨材料的耐磨性能得以充分發揮。
另外,在現有的碳纖維抽油杆中,為了增加抽油杆的抗劈裂性能和抗剪切性能,往往要在碳纖維芯體的外側纏繞至少一層玻璃纖維,這種方式無疑會增加產品生產工藝的複雜性和生產難度。然而,對於本發明所述的碳纖維抽油杆來說,在環氧樹脂和丙綸纖維的結合體中,丙綸纖維單絲起到了增強纖維的作用,從而使得環氧樹脂和丙綸纖維的結合體具有較大的比強度和比模量,這一特性使得抽油杆的抗劈裂性能和抗剪切性能均得到了顯著提高,從而簡化了工藝設備,降低了工藝難度。
4、在製造本發明所述的抽油杆時,各工序僅需要通過現有生產設備中的拉擠模具,即可成型,而不再需要配備編織機、纏繞機等機器,進一步改善了本發明的生產工藝性。
附圖說明
圖1是本發明的截面圖;
圖2是本發明的截面為長條形時的截面圖;
圖3是粗紗層與作為耐磨層的丙綸條的位置關係示意圖。
圖中:1-碳纖維芯體,2-粗紗層,3-耐磨層,4-細紗層,5-環氧樹脂層。
具體實施方式
以下結合附圖對本發明做進一步描述:
本實施例包括碳纖維芯體1、耐磨層3和環氧樹脂層5,這是現有技術中碳纖維抽油杆的基本結構。
碳纖維芯體1的外側設置有粗紗層2,在粗砂層2的外側設置耐磨層3,耐磨層3的外側設置有細紗層4,所述的環氧樹脂層5設置在細紗層4的外側。其中,碳纖維芯體1的作用是承受大部分拉力載荷;粗紗層2和細紗層4的作用是與碳纖維芯體1共同分擔拉力載荷,減少碳纖維的用量,從而降低抽油杆的生產升本,同時,組成粗紗層2和細紗層4的芳綸纖維具有較好的耐磨性能,有助於改善抽油杆的耐磨性能。耐磨層3的作用是改善耐磨性能。
所述的耐磨層3由棉絮狀的丙綸條包覆而成。作為耐磨層3的丙綸為條狀扁帶結構,丙綸條沿抽油杆的長度方向設置,丙綸條的寬度等於粗紗層2外側圓柱面的周長,與在環氧樹脂內添加耐磨顆粒的耐磨結構相比,以丙綸為核心的耐磨層3更均勻、更連續、更完整,因此有效消除了性能盲區,改善了抽油杆的整體耐磨性能。本發明採用的丙綸為棉絮狀結構,與現有技術中的成股的耐磨纖維或耐磨織物相比,環氧樹脂可以更充分地浸入到丙綸條內的每根纖維單絲之間,因此作為耐磨材料的丙綸與環氧樹脂的結合度以及環氧樹脂的浸入度大大提高,丙綸和環氧樹脂可以最大程度地結合,從而使得耐磨材料的耐磨性能得以充分發揮。
在本發明中,芳綸纖維分為粗砂和細紗兩種,粗砂和細紗的區別在於:與細紗相比,在用量一定的情況下,採用粗砂時所需的紗線軸較少,佔用的空間也比較少,生產周期也比較短,但由於粗砂的浸膠性能不如細紗,因此粗紗層2的耐磨性能不如細紗層4。在本發明中,粗紗層2由細度為3000d(d為細度單位:旦尼爾)的芳綸纖維製成,所述的細紗層4由細度為1100d的芳綸纖維製成。通過採用兩種細度不同的芳綸纖維,兼顧了生產工藝性和耐磨性能,是抽油杆獲得了較好的綜合性能。
所述的碳纖維、芳綸纖維以及丙綸條的長度方向均與抽油杆的軸線方向一致,這一結構特點可大大簡化抽油杆的生產工藝流程,降低工藝難度,質量穩定性也更容易保證。在製造本發明所述的抽油杆時,各工序僅需要通過現有生產設備中的拉擠模具,即可成型,而不再需要配備編織機、纏繞機、注塑機、噴丸機等機器,對工藝的簡化程度十分顯著。
抽油杆中碳纖維的質量百分含量為28%-30%,粗紗層2中的芳綸纖維的質量百分含量為22%-24%,丙綸條的質量百分含量為3%-4%,細紗層4中的芳綸纖維的質量百分含量為10%-12%,其餘成分為環氧樹脂,通過控制各組成部分的質量百分含量,方可得到綜合性能符合設計要求的抽油杆。
為保證足夠的抗拉強度,現有技術中的碳纖維的規格均為12k的,但在本發明中,為減少紗線軸的數量,降低降低紗線軸對空間佔用,本發明採用的碳纖維的規格為t300/6k,使得紗線軸的數量減少了一半,紗線軸佔用的空間也減少了一半。
所述的環氧樹脂層5內摻加有耐磨顆粒。本發明設置了內外兩層耐磨結構(摻加了耐磨顆粒的環氧樹脂層5和耐磨層3),摻加了耐磨顆粒的環氧樹脂層5雖然有存在性能盲區的可能,但仍可以防止耐磨層3局部大範圍磨損,從而保護了耐磨層3。
優選地,所述的抽油杆的截面形狀為長條形或橢圓形,與現有技術中的截面為圓形的抽油杆結構相比,在截面面積相同的情況下,長條形或橢圓形的截面形狀的抽油杆的最小彎曲半徑更小,從而顯著減小了用於盤繞抽油杆的輪盤的直徑,使得抽油杆的轉運、安裝和施工設備的體積大大減小。
在本發明的設計之初,設計人員也考慮到了如何對現有的碳纖維連續抽油杆生產設備進行簡化的問題。在現有的碳纖維抽油杆中,為了增加抽油杆的抗劈裂性能和抗剪切性能,往往要在碳纖維芯體1的外側纏繞至少一層玻璃纖維,這種方式無疑會增加產品生產工藝的複雜性和生產難度。然而,對於本發明所述的碳纖維抽油杆來說,在環氧樹脂和丙綸纖維的結合體中,丙綸纖維單絲起到了增強纖維的作用,從而使得環氧樹脂和丙綸纖維的結合體具有較大的比強度和比模量,這一特性使得抽油杆的抗劈裂性能和抗剪切性能均得到了顯著提高,從而簡化了工藝設備,降低了工藝難度。