一種5-羥甲基糠醛的生產工藝的製作方法
2023-06-07 07:05:51 1
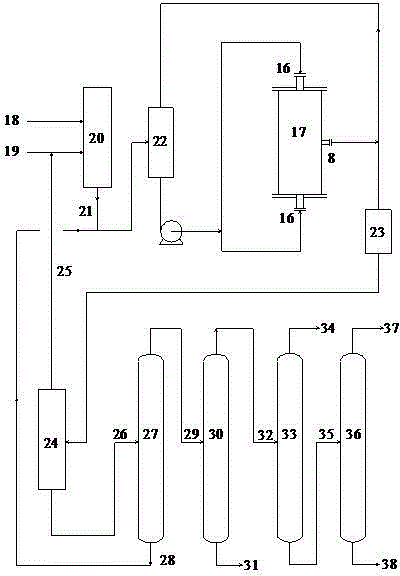
本發明屬於化工領域,涉及5-羥甲基糠醛生產技術,特別是一種採用撞擊流反應器連續生產5-羥甲基糠醛的工藝。
背景技術:
生物質是一種取之不盡、用之不竭的可再生資源,同時也是唯一一種可再生的碳源。經過幾十年的探索,目前人們已經形成共識:生物質生產生物基化學品,逐步替代化石資源是目前最可行、最佳或唯一選擇。如何高效的從生物質糖平臺製取生物基平臺化學品已經世界各國學者研究的熱點。
5-羥甲基糠醛常壓下沸點183℃,熔點35.2℃,其分子結構中存在醛基、雙烯、環醚等官能團,所以它兼具醛、醚、二烯和芳香烴化合物的性質,可參與多種不同類型的反應,合成很多種化工產品,廣泛應用於國民經濟中的各個領域,因此被美國能源部視為十大生物基平臺化學品。
纖維素經高溫水解可製取葡萄糖,葡糖糖在高溫、催化劑條件下反應即可生成5-羥甲基糠醛。由於5-羥甲基糠醛分子中含有一個呋喃環和一個醛基,其化學性質比較活潑,在其反應生成條件下比較容易發生副反應造成5-羥甲基糠醛收率降低,因此為了獲得較高的收率,就必須儘可能快的把反應生成的5-羥甲基糠醛轉移出反應體系。
反應萃取製取5-羥甲基糠醛技術被認為是最具工業前景的葡萄糖製取5-羥甲基糠醛技術。反應萃取製取5-羥甲基糠醛技術是指在葡萄糖反應生成5-羥甲基糠醛過程加入一種與水不互溶而對5-羥甲基糠醛具有高選擇性的溶劑,靠溶劑不斷把5-羥甲基糠醛從水相反應體系萃取到溶劑相,從而大大降低副反應提高5-羥甲基糠醛收率。
中國專利CN101628902A公開了一種由葡萄糖製取5-羥甲基糠醛的方法,該方法首先將一定量的葡萄糖溶液裝入高壓反應釜中,升溫至120-250℃,然後通入超臨界二氧化碳,控制壓力10-25MPa;反應的同時不斷排出溶解了5-羥甲基糠醛的超臨界二氧化碳,然後5-羥甲基糠醛再與二氧化碳分離,再經脫水、結晶等工序獲得5-羥甲基糠醛產品。上述發明實際上屬於間歇生產過程,而且工藝複雜,操作壓力高、能耗大,在工業上很難實現。
在木質纖維素高溫條件下水解製取葡萄糖的過程中,同時伴有副產物甲酸和醋酸生成,因此所得葡萄糖溶液中同時含有甲酸和乙酸,如果反應後水溶液不進行環保處理而直接排放,不僅會造成嚴重的環境汙染,還會造成寶貴資源的浪費,在現有的由葡糖糖溶液製取5-羥甲基糠醛的技術中,還沒有關於能夠從反應液中同時回收甲酸和醋酸的報導。
撞擊流是實現快速混合的一種十分有效的方法。它利用兩股高速流體相向撞擊,在反應器中形成一個高度湍動的撞擊區,能夠有效降低傳遞過程中的外部阻力,促進混合,強化傳質傳熱。撞擊流反應器已經廣泛用於吸收、混合、傳熱、結晶等化工過程。開發高效的適用於反應萃取工藝製備5-羥甲基糠醛過程的撞擊流反應器是提高5-羥甲基糠醛收率的有效手段。
20世紀90年代以來,撞擊流領域的研究明顯轉向以液體連續相撞擊流(Liquid-continuous Impinging Streams,LIS)為重點。專利CN 100364656C在反應器殼體中設置兩個正對的導流筒,液體通過泵的驅動作用分別流經兩側導流筒後,在中心處發生相向撞擊。這種反應器雖然結構簡單,但是只注重了兩端導流筒流體的撞擊效果,未考慮液體撞擊後在反應器中的流動狀況,容易造成反應器兩側存在死區。如果兩撞擊流體中存在固相催化劑,則容易造成催化劑沉降、滯留,直接影響反應深度和產品質量。
專利CN 102989404 A在導流筒中設置螺旋槳,利用兩螺旋槳的驅動作用使得反應器中液體在中心處發生撞擊,同時利用導流筒和導流片的作用,解決了撞擊區外的混合的問題。但螺旋槳需要動力驅動,因此需要外設電機,增加了反應器的整體造價;另外,安裝螺旋槳的電機軸在反應器壁上需要安裝軸封結構,長期運轉易造成損壞,影響反應器的長周期運行。
技術實現要素:
針對現有技術的不足,本發明提供一種高效生產5-羥甲基糠醛並同時回收副產物甲酸和醋酸的新方法,以及一種特別適用於該工藝的撞擊流反應器,它通過多次撞擊實現流體混合,具有好的微觀混合效果,混合後的液體在撞擊區外平推流動,為物料提供充足的停留時間,實現梯級反應,並通過流道和液體流速設計達到目標轉化率,克服了目前撞擊流反應器無法通過單一反應器實現高轉化率的缺點。
本發明的一種5-羥甲基糠醛的生產工藝,包括以下內容:
(1)提供一種液相撞擊流反應器,包括反應器外殼和導流筒;反應器外殼包括筒體和封頭;在封頭外壁的中央位置設置兩個正對的進料管;在反應器外殼內部與進料管相連接的是第一導流筒,第一導流筒由兩個圓臺形殼體組成,兩殼體正對放置,第一導流筒的軸線與反應器軸線重合,圓臺狀殼體的粗端與進料管相接,經進料管進入的液體經加速後在細端的出口發生撞擊混合。第一導流筒的外側是第二導流筒,其形狀為圓筒形,第二導流筒的兩端與封頭間留有縫隙,第二導流筒軸線與反應器軸線重合。在第二導流筒的外側是第三導流筒,第三導流筒由兩個圓臺形殼體構成,兩殼體正對放置,第三導流筒軸線與反應器軸線重合,第三導流筒的粗端與封頭連接,細端出口相對放置。第三導流筒的外側是第四導流筒,第四導流筒為圓筒形,第四導流筒的兩端與封頭間留有通道,導流筒軸線與反應器軸線重合;
(2)將脫去半纖維素後的生物質原料與水按照質量比0.05~1混合後進入水解釜,在180~240℃條件下水解0.2~1 h,得到葡萄糖糖、醋酸和甲酸混合溶液;
(3)以步驟(2)得到的含葡萄糖混合溶液為原料,採用撞擊流反應器,將混合溶液與萃取劑通過輸送設備分別通入步驟(1)的撞擊流反應器,反應所用催化劑為甲酸和/或醋酸,在葡萄糖脫水生成5-羥甲基糠醛的反應條件下進行混合接觸反應;
(4)步驟(3)得到的反應流出物進行冷卻靜置分層,上層為水相,含有微量的5-羥甲基糠醛、醋酸、甲酸及微量的未反應的葡萄糖,下層為萃取相,含有5-羥甲基糠醛、醋酸、甲酸以及微量的水;
(5)步驟(4)得到的萃取相進入萃取劑再生塔進行分離,塔頂得到含微量水的5-羥甲基糠醛、甲酸、醋酸的混合物,塔釜得到再生的萃取劑,所述萃取劑進入反應器循環使用;
(6)步驟(5)中塔頂得到的含微量水的5-羥甲基糠醛、醋酸和甲酸的混合物進入5-羥甲基糠醛成品塔進行分離,塔釜得到5-羥甲基糠醛,其純度大於99.5%,塔頂得到含少量水的醋酸和甲酸混合物;
(7)步驟(6)中所得醋酸和甲酸混合物進入共沸精餾塔與共沸劑接觸後進行分離,塔頂分相器得到水和共沸劑混合物,水從塔頂採出,共沸劑返回塔內,塔釜得到醋酸和甲酸,醋酸和甲酸混合物進入成品塔進一步分離,塔頂得到成品甲酸,塔釜得到成品醋酸,其純度均大於99.5wt%。
本發明的方法中,步驟(1)所述的撞擊流反應器可以為立式或臥式。反應器外殼筒體為圓筒形或矩形,封頭為圓形、橢圓形、蝶形或平蓋形。
本發明的工藝中,步驟(1)所述撞擊流反應器中,所述的導流筒可以設置4個以上,以4~10個為宜,當導流筒形狀為圓臺時,圓臺的母線與軸線夾角優選為1°~80°。
本發明的工藝中,其中在反應器外殼上位於軸線中心處垂面的設置有出料管,出料管一般設置2個以上,優選設置2~6個。所述的出料管沿反應器軸線對稱分布。
本發明的工藝中,步驟(1)所述撞擊流反應器中,第一導流筒兩圓臺形殼體細端出口處距離為細端直徑的0.1~10倍,第二導流筒兩端與封頭距離相等,為第一導流筒圓臺殼體細端直徑的0.1~10倍,第三導流筒兩圓臺形殼體細端出口處距離為第一導流筒細端直徑的0.1~10倍,第四導流筒兩端與封頭距離相等,為第一導流筒圓臺殼體細端直徑的0.1~10倍。
本發明的工藝中,步驟(1)所述撞擊流反應器中,導流筒採用鋼板卷制、焊接而成,導流筒與封頭之間和兩導流筒之間,採用焊接或鉚接固定,圓臺導流筒粗端可開孔,在抽吸作用下使物料回流,加強混合,提高反應轉化率。反應原料由圓臺形導流筒粗端流入,流向細端,在此過程中流體壓力勢能轉化成動能,在細端出口處動能達到最大值並發生撞擊作用,混合後的流體在圓臺導流筒和圓筒隔壁的阻隔和導流作用下平推流動,遇到反應器殼體後折流到下一平推流道,此流道與上一流道結構相似,流體由粗端流向細端,流動過程中液體加速並在細端發生撞擊混合,如此往復,反應器中可通過增加導流筒個數設置多個平推流道。
本發明工藝中,步驟(3)中所用萃取劑可以為本技術領域的常規萃取劑,優選為複合萃取劑,所述複合萃取劑為鄰苯二甲酸二甲酯、碳數大於7的正烷醇(沸點高於200 ℃)以及乙基三苯基膦六氟磷酸鹽組成的組合物,所述乙基三苯基六氟磷酸鹽可以為乙基三苯基六氟磷酸鈉和/或乙基三苯基六氟磷酸鉀。其中,鄰苯二甲酸二甲酯佔10wt%~60wt%,正烷醇佔10wt%~40wt%,乙基三苯基膦六氟磷酸鹽佔10wt%~50wt%。優選,鄰苯二甲酸二甲酯佔20wt%~40wt%,正烷醇佔20wt%~30wt%,乙基三苯基膦六氟磷酸鹽佔20wt%~40wt%。
本發明工藝中,葡萄糖脫水生成5-羥甲基糠醛反應溫度一般為150~280℃,優選為200~240℃;反應停留時間一般為0.1~2 h。
本發明工藝中,葡萄糖脫水反應壓力應大於反應溫度下水相泡點壓力以保證反應在液相狀態下進行,反應壓力範圍在2~10 MPa,優選壓力為2~4 MPa。
本發明工藝中,步驟(2)中所述生物質原料可以為玉米芯、小麥秸稈、玉米稈、高粱稈、水稻秸稈中的一種或幾種。
本發明工藝中,步驟(4)中所述水相可以進入水解釜循環使用。
本發明工藝中,步驟(7)中共沸精餾塔所用共沸劑為環己烷、醋酸乙酯、醋酸異丙酯、醋酸正丁酯中的一種。
本發明工藝中,可以根據裝置的規模和操作條件確定撞擊流反應器的規模。為提高撞擊流反應器的混合效果,可以在撞擊流反應器出口與入口之間建立物料循環。將步驟(3)所得到反應流出物的一部分與含葡萄糖混合溶液原料混合後,循環回撞擊流反應器,其中循環物料量為新鮮進料量的5%~500%。
與現有技術相比,本發明的一種5-羥甲基糠醛的生產工藝具有以下有益效果:
1、本發明採用的撞擊流液相反應器中,物流經導流筒導入後在撞擊區發生撞擊,並發生高效混合,此區域可以看作是一個全混流反應系統。撞擊混合後的液體流出撞擊區域後,導流筒的隔離和導流下發生平推流動,直至發生二次撞擊,此區域可以看作一個平推流反應系統。本發明反應器中發生多次撞擊混合,強化了傳質、傳熱效果;平推流反應系統流道體積佔比高,物料停留時間長,通過設計可達到目標轉化率,消除過度反應。本發明的反應器克服了傳統撞擊流反應器的不足,使反應均勻、充分,節省了反應器體積,減少了過度反應,通過流道體積設計可達到目標轉化率,減少了設備投資具有很好的經濟效益。另外,導流筒具有阻隔流體和導輸流體的作用,反應器中無需設置專門的流體分配導流系統,與傳統的導流系統相比,具有液體流動順暢、壓降小、無死區的優點。
2、本發明的撞擊流強化了液液撞擊流反應器的撞擊效果,使反應器的微觀混合效果大大增強,混合時間大大縮短,提高了生產效率,並通過良好的平推流道設計避免了死區的存在,使得化學反應在反應器空間各位置的同步性提高,有助於提高產品質量;反應器構造簡單,無需增設其他的導流分配系統,設備加工難度小,設備投資成本低,具有良好的經濟效益。
3、本發明採用所述的撞擊流反應器作為反應萃取製取5-羥甲基糠醛工藝的反應器,極大的強化了微觀混合和微觀傳質,使5-羥甲基糠醛在萃取劑和水兩相瞬間達到分配平衡,提高了生產效率,降低了副反應,提高了5-羥甲基糠醛收率。解決了因萃取劑和葡萄糖溶液混合效果差,反應體系呈兩相,5-羥甲基糠醛在水相反應體系濃度遠高於兩相平衡時5-羥甲基糠醛濃度而造成的副反應嚴重、5-羥甲基糠醛收率低及反應器堵塞等問題。
4、本發明的工藝中,使用複合萃取劑,通過正烷醇和乙基三苯基膦六氟磷酸鹽復配使用大大提高了對5-羥甲基糠醛的選擇性,而且通過乙基三苯基膦六氟磷酸鹽的加入,葡萄糖製取5-羥甲基糠醛反應明顯加快,表明乙基三苯基膦六氟磷酸鹽對葡萄糖製取5-羥甲基糠醛反應具有催化作用,可以使葡萄糖生成5-羥甲基糠醛反應在相對緩和的操作條件下發生,從而降低生產成本。本發明複合萃取劑中,加入正烷醇解決了乙基三苯基膦六氟磷酸鹽與對醋酸和甲酸選擇性高的鄰苯二甲酸二甲酯間互溶性差的問題,因此本發明複合萃取劑對5-羥甲基糠醛、醋酸和甲酸均具有很高的選擇性,能夠在反應萃取製取5-羥甲基糠醛的同時回收副產物甲酸和醋酸,5-羥甲基糠醛收率大於80%,醋酸和甲酸回收率大於90%,反應完的水相可作為系統回用水。
5、本發明的工藝,採用了高沸點的複合萃取劑,萃取劑沸點遠高於5-羥甲基糠醛沸點,可顯著降低萃取劑再生過程能耗。
6、本發明的工藝,大大提高了葡萄糖製取5-羥甲基糠醛的收率和生產效率,簡化了工藝流程、降低了生產成本和設備投資,保證了設備的長周期運行。生產過程中無廢液排放,是一項綠色環保工藝方法。
附圖說明
圖1為本發明反應器的結構示意圖。
圖2為本發明工藝流程圖。
具體實施方式
以下結合具體附圖對本發明的液相撞擊流反應器做更詳細的說明。
如圖1所示,本發明的一種用於液-液多效混合的液相撞擊流反應器,包括反應器外殼和導流筒兩個部分。反應器外殼由筒體12和封頭15組成。反應器外殼封頭15外壁的中央位置設置兩個正對的進料管16,在反應器外殼的內側與進料管相連接的是第一導流筒3和14,第一導流筒3和14分別為圓臺形殼體,兩圓臺形殼體正對放置,第一導流筒(圓臺形殼體)的軸線與反應器軸線重合。圓臺狀殼體的粗端與進料管相接,液體經加速後在細端出口發生撞擊混合。第一導流筒3和14的外側是第二導流筒4。第二導流筒4為圓筒狀,其與封頭15間留有縫隙,提供流體流動的通道。第二導流筒4可以通過支撐與封頭15或第一導流筒3和14固定連接。第二導流筒4的軸線與反應器軸線重合。在第二導流筒4外側是第三導流筒5和13,第三導流筒為圓臺形殼體,兩殼體正對放置。第三導流筒的軸線與反應器軸線重合,圓臺形殼體的粗端與封頭15密閉連接,細端出口相對設置。第三導流筒5和13的外側是第四導流筒6,其為圓筒形,軸線與反應器軸線重合。第四導流筒的兩端與封頭15間留有通道(縫隙),提供流體流動的通道。第四導流筒6可以通過支撐與封頭15、筒體12或第三導流筒5和13固定連接。在反應器軸線中心處垂面的外殼上設置出料管8,出料管8一般設置兩個以上,優選設置2至6個出料管。若干個出料管沿反應器軸線對稱分布。
本發明的液相撞擊流反應器形式可以為立式或臥式結構。反應器外殼筒體為圓筒形或矩形,封頭15一般為圓形、橢圓形、蝶形或平蓋形。導流筒可設置4個以上,以4~10個為宜。導流筒形狀為圓臺時,圓臺的母線與軸線夾角一般為1°~80°。第一導流筒3和14中,兩圓臺形殼體細端出口間的距離為細端出口直徑的0.1~10倍。第二導流筒4的兩端與封頭距離相等,一般為第一導流筒的圓臺殼體細端出口直徑的0.1~10倍。第三導流筒5和13中,兩圓臺形殼體細端出口處的距離為第一導流筒細端(出口)直徑的0.1~10倍。第四導流筒6兩端的與封頭的距離相等,一般為第一導流筒的圓臺形殼體細端出口直徑的0.1~10倍。
所述的導流筒一般採用鋼板卷制、焊接而成。導流筒與封頭15之間,相鄰的兩個導流筒之間,一般採用焊接或鉚接7固定。在圓臺導流筒的粗端可以開有若干孔,以在抽吸作用下使物料回流,加強混合,從而提高反應轉化率。
結合圖1,本發明的液相撞擊流反應器的工作原理或工作過程為:反應進料1經原料泵2加壓後,由第一導流筒3和14粗端流入,流向細端,在此過程中流體壓力勢轉化成動能,在細端出口處動能達到最大值並發生撞擊作用,形成第一撞擊面11。混合後的流體在第一導流筒3、14和第二導流筒4的阻隔和導流作用下沿此流道(由第一導流筒和第二導流筒間隔形成)平推流動,遇到封頭15後折流到下一平推流道,此流道與上一流道結構相似,由第二導流筒4和第三導流筒5,13間隔形成,流體由粗端截面流向細端截面,流動過程中液體加速並在細端發生撞擊混合,形成撞擊面10。撞擊後的流體在第三導流筒5、13和第四導流筒6間隔形成的流道中流動,遇到封頭15後進行折流,進入第四導流筒6和筒體12間隔形成的流道,並在出口發生撞擊,形成撞擊面9。撞擊後的流體從出口8流出反應器。
以下結合具體附圖對本發明工藝做更詳細的說明。
如圖2所示,按照計量比將新鮮水19和脫去半纖維素後的生物質原料18,分別注入到水解釜20中,水解後所得葡萄糖溶液21與萃取劑28匯合後進入中間罐22,進行預混合,然後通過泵或其他液體輸送設備,輸入到撞擊流反應器17兩側對稱的進料口16,原料物流在壓力作用下高速經導流筒流向容器中心,並在中心處相向撞擊,經過撞擊後的物料從出口8流向中間罐22,再通過泵輸入到撞擊流反應器17兩側對稱的進料口16,進行再次撞擊,通過壓力調節器23來控制反應器壓力。從壓力調節器23排出的反應物料直接進入分相罐24進行冷卻靜置分層,上層水相25循環回水解釜20循環使用,下層萃取相26直接進入萃取劑再生塔27進行分離,塔頂得到含微量水的5-羥甲基糠醛、醋酸和甲酸混合物29,塔底得到再生的萃取劑28,再生的萃取劑28與葡萄糖溶液21匯合後循環使用,塔頂產物29然後直接進入5-羥甲基糠醛精製塔30進行分離,塔底得到5-羥甲基糠醛產品31,純度大於99.5%,塔頂得到的甲酸和醋酸混合物32進入共沸精餾塔33進行分離,塔頂採出水相34,塔底得到不含水的醋酸和甲酸混合物35,塔底產物35進入成品塔36,塔頂得到成品甲酸37,塔底得到成品醋酸38,其純度均大於99.5wt%。
下面通過實施例進一步說明本發明的工藝方法和效果。涉及的百分含量為質量百分含量。
實施例中葡萄糖轉化率、5-羥甲基糠醛收率以及酸回收率通過下式進行計算。
。
實施例1
玉米秸稈粉碎後與水按照質量比1:1注入水解釜,預水解溫度240℃,預水解時間20 min,反應後所得溶液中葡萄糖糖、醋酸、甲酸質量濃度分別為4.9 %、2.0%、0.5%。
所用複合萃取劑為鄰苯二甲酸二甲酯、正壬醇、乙基三苯基膦六氟磷酸鹽混合溶劑,其中,鄰苯二甲酸二甲酯佔40wt%,正辛醇佔20wt%,乙基三苯基膦六氟磷酸鹽佔40wt%。
萃取劑與葡萄糖溶液進料比為3:1(體積比),萃取劑與葡萄糖溶液的進料速率等於撞擊流反應器體積(即進料體積空速為1h-1,也即反應時間為1h),循環物料速率為進料量的200%。控制反應溫度為220℃,反應壓力為3 MPa。
實驗結果表明葡萄糖轉化率為97.1wt%,5-羥甲基糠醛收率為82.3wt%,醋酸回收率為90.6wt%,甲酸回收率為89.8wt%。
實施例2
按照實施例1的方法,不同之處為進料速率為撞擊流反應器容積的2倍,即反應時間為0.5 h。
實驗結果表明葡萄糖轉化率為77wt%,5-羥甲基糠醛收率為60.9wt%,醋酸回收率為93.9wt%,甲酸回收率為90.7wt%。
實施例3
按照實施例1的方法,不同之處為進料速率為撞擊流反應器容積的0.67倍,即反應時間為1.5 h。
實驗結果表明葡萄糖轉化率為99%,5-羥甲基糠醛收率為82.4%,醋酸回收率為94.1%,甲酸回收率為90.7%。
實施例4
按照實施例1的方法,不同之處為循環物流為進料量的100%。
實驗結果表明葡萄糖轉化率為96.5%,5-羥甲基糠醛收率為82.3%,醋酸回收率為92.5%,甲酸回收率為90.9%。
實施例5
按照實施例1的方法,不同之處為循環物流為進料量的300%。
實驗結果表明葡萄糖轉化率為96.5%,5-羥甲基糠醛收率為81.2%,醋酸回收率為94.5%,甲酸回收率為92.3%。
實施例6
按照實施例1的方法,不同之處為反應溫度變為200℃。
實驗結果表明葡萄糖轉化率為44.5%,5-羥甲基糠醛收率為37.3%,醋酸回收率為94.5%,甲酸回收率為92.3%。
實施例7
按照實施例1的方法,不同之處為反應溫度變為240℃。
實驗結果表明葡萄糖轉化率為99.6%,5-羥甲基糠醛收率為83.9%,醋酸回收率為94.2%,甲酸回收率為91.9%。
實施例8
按照實施例1的方法,不同之處為萃取劑與葡萄糖溶液進料比變為1:1。
實驗結果表明葡萄糖轉化率為97.9%,5-羥甲基糠醛收率為77.8%,醋酸回收率為83.9%,甲酸回收率為80.2%。
實施例9
按照實施例1的方法,不同之處為萃取劑與葡萄糖溶液進料比變為5:1。
實驗結果表明葡萄糖轉化率為97.5%,5-羥甲基糠醛收率為85.8%,醋酸回收率為94.9%,甲酸回收率為93.3%。
實施例10
按照實施例1的方法,不同之處為複合萃取劑組成變為:鄰苯二甲酸二甲酯、正壬醇、乙基三苯基膦六氟磷酸鹽質量比3:1:1。
實驗結果表明葡萄糖轉化率為97.5%,5-羥甲基糠醛收率為75.8%,醋酸回收率為84.9%,甲酸回收率為82.3%。
實施例11
按照實施例1的方法,不同之處為複合萃取劑組成變為:鄰苯二甲酸二甲酯、正壬醇、乙基三苯基膦六氟磷酸鹽質量比1:1:3。
實驗結果表明葡萄糖轉化率為97.8%,5-羥甲基糠醛收率為83.2%,醋酸回收率為77.9%,甲酸回收率為77.3%。
實施例12
按照實施例1的方法,不同之處為複合萃取劑組成變為:鄰苯二甲酸二甲酯、正壬醇、乙基三苯基膦六氟磷酸鹽質量比1:0:1。
實驗結果表明葡萄糖轉化率為97.8%,5-羥甲基糠醛收率為74.6%,醋酸回收率為71.9%,甲酸回收率為70.3%。
實施例13
按照實施例1的方法,不同之處為複合萃取劑組成變為:鄰苯二甲酸二甲酯、正壬醇、乙基三苯基膦六氟磷酸鹽質量比0:1:1。
實驗結果表明葡萄糖轉化率為97.2%,5-羥甲基糠醛收率為83.6%,醋酸回收率為78.9%,甲酸回收率為77.3%。
實施例14
按照實施例1的方法,不同之處為複合萃取劑組成變為:鄰苯二甲酸二甲酯、正壬醇、乙基三苯基膦六氟磷酸鹽質量比1:1:0。
實驗結果表明葡萄糖轉化率為97.4%,5-羥甲基糠醛收率為70.6%,醋酸回收率為88.9%,甲酸回收率為85.6%。
實施例15
按照實施例1的方法,不同之處為複合萃取劑組成變為:鄰苯二甲酸二甲酯、正壬醇、乙基三苯基膦六氟磷酸鹽質量比1:0:0。
實驗結果表明葡萄糖轉化率為96.8%,5-羥甲基糠醛收率為60.6%,醋酸回收率為91.9%,甲酸回收率為89.6%。
實施例16
按照實施例1的方法,不同之處為複合萃取劑組成變為:鄰苯二甲酸二甲酯、正壬醇、乙基三苯基膦六氟磷酸鹽質量比0:0:1。
實驗結果表明葡萄糖轉化率為98.3%,5-羥甲基糠醛收率為84.6%,醋酸回收率為41.9%,甲酸回收率為49.6%。
比較例1
使用常規的撞擊流反應器,如CN 102989404 A中介紹的撞擊流反應器,其他同實施例1。
實驗結果表明葡萄糖轉化率為98.3%,5-羥甲基糠醛收率為79.6%,醋酸回收率為86.9%,甲酸回收率為87.6%。