一種改良的燃燒器的製作方法
2023-09-18 22:16:05 1
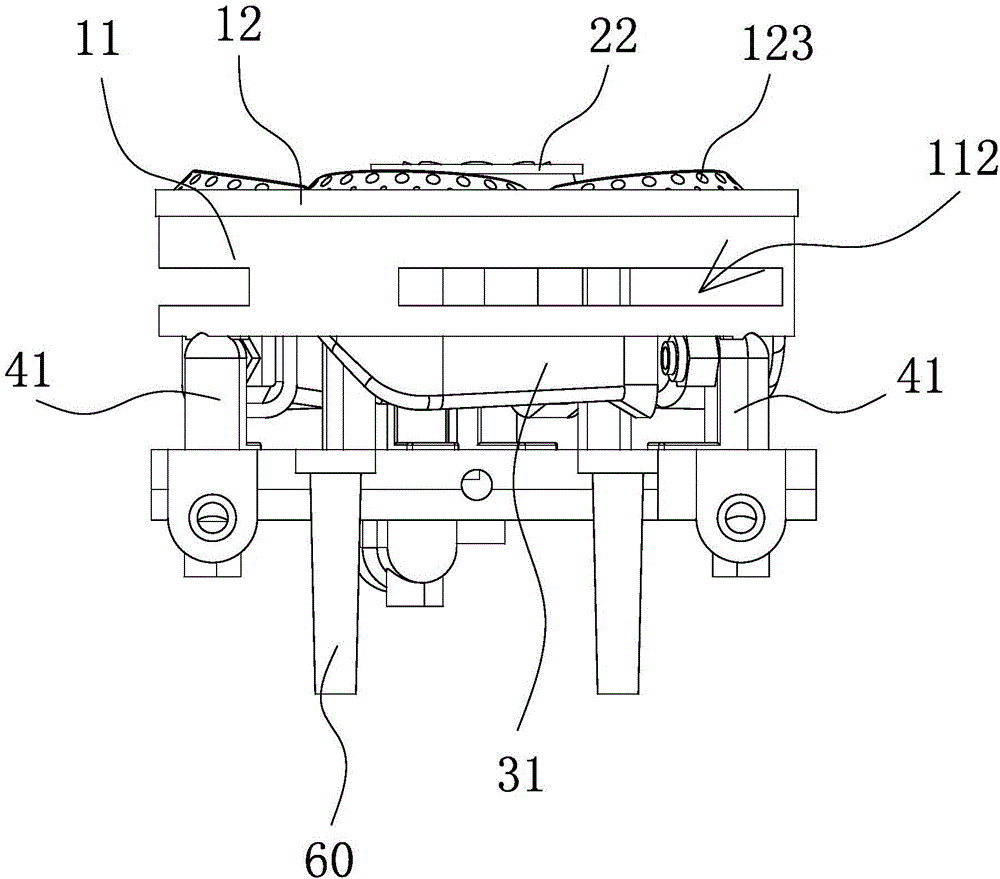
本發明屬於燃氣器具技術領域,涉及一種改良的燃燒器,特別是一種用於燃氣灶的改良的燃燒器。
背景技術:
燃氣灶是指以液化石油氣、人工煤氣、天然氣等氣體燃料進行直火加熱的廚房用具。燃氣灶主要由燃燒器、點火裝置、爐架、進氣管、閥體等裝置組成,
燃燒器包括爐頭、內外火蓋等結構,工作時,燃氣從進氣管進入灶內,經過燃氣閥的調節進入爐頭中,同時混合一部分空氣(這部分空氣稱之為一次空氣),這些混合氣體從分火蓋的火孔中噴出同時被點火裝置點燃形成火焰(燃燒時所需的空氣稱之為二次空氣),進而用來加熱置於爐架上的炊具。
爐頭內部往往設置特定結構的流通通道,燃氣在爐頭內流通之後經點火裝置點燃,然而現有的燃氣灶大都設置一個進氣口(進氣管)供燃氣進入爐頭,短時間內燃氣在爐頭內部流通不暢,從而容易導致燃氣燃燒不夠充分,燃燒效果差且安全性較低。
而現有技術中燃氣灶的材料為一般的合金鋼、鋁合金或銅合金,不僅強度一般,且耐溫性、耐腐蝕性能也較差,影響著燃氣灶的使用壽命。
綜上所述,為解決現有用於燃氣灶的燃燒器結構上的不足,需要設計一種設計合理、燃燒效果好的改良的燃燒器。
技術實現要素:
本發明的目的是針對現有的技術存在上述問題,提出了一種設計合理、燃燒效果好的改良的燃燒器。
本發明的目的可通過下列技術方案來實現:一種改良的燃燒器,包括:
外爐頭,呈圓環狀設置,在外爐頭上扣合有外火蓋且外火蓋與外爐頭合圍形成外混合腔,在外爐頭底部設置有與外混合腔聯通的若干主通道,主通道的橫截面呈方形設置;
內爐頭,穿設在外爐頭中部,在內爐頭上扣合有內火蓋且內火蓋與內爐頭合圍形成內混合腔,在內爐頭底部設置有與內混合腔聯通的次通道;
管道組件,位於外爐頭下方,在管道組件上設置有與次通道對應的次進氣管以及與各主通道一一對應的若干主進氣管;
點火柱,設置為多個,每個點火柱均與管道組件聯通,所述點火柱豎直向上延伸並抵靠在內爐頭外周側壁上;
支柱,設置為多個,各支柱豎直安裝在管道組件下方;
所述的點火柱、支柱均由鎂合金製成,所述鎂合金的組成元素及質量百分比為:Zn:1.00%-1.60%、Mn:0.38%-0.68%、B:0.18%-0.28%、Zr:0.20%-0.30%、Ce:0.05%-0.12%,餘量為Mg及不可避免的雜質。
本發明點火柱、支柱所用的鎂合金中添加有適量的Zn、Mn、B、Zr、Ce,通過各元素之間的合理配置以及產生的協同作用,顯著提高鎂合金點火柱、支柱的力學性能和機械性能,尤其是顯著提高點火柱、支柱的強度、耐熱性、耐腐蝕,進而延長點火柱、支柱的使用壽命。
在本發明點火柱、支柱鎂合金中加入適量的鋯,可以細化晶粒,減少熱烈傾向,提高力學性能。因為鋯的化學活潑性高,易與其他元素如鋁、矽、鐵、錫和錳等元素形成難熔金屬間化合物,而喪失鋯的細化晶粒左右,因此,本發明鎂合金中儘量減少上述元素的含量。鋯細化晶粒的原因在於在液態鎂中鋯的溶解度隨溫度降低而減少,在凝固過程中,鋯首先以α-Zr結晶析出,其點陣結構與鎂相似,起非自發形核作用從而能夠細化晶粒。另外,鋯還能夠提高鎂合金的熔點,從而有效改善點火柱、支柱的耐溫性和耐腐蝕性。
在鎂合金中,由於形成條件不同,鐵相在合金中的存在形式可能為單質、固溶體或者金屬間化合物。由於鎂的平衡電位和穩定電位都非常負,而鐵的析氫電位較低,則鐵相的存在會嚴重影響點火柱、支柱的耐腐蝕性;同時,鐵相的存在會嚴重損害鎂合金的組織和力學性能,導致其柔韌性降低,脆性增加。儘管因為本發明點火柱、支柱鎂合金中含有Zr,應避免鋁、矽、鐵、錫和錳等元素的存在,但為了有效抑制鐵相的有害影響,本發明點火柱、支柱鎂合金中加入了1.00%-1.60%Zn、0.38%-0.68%Mn和0.18%-0.28%B。Zn可以減少Fe、Ni、Cu等有害雜質對於合金耐腐蝕性能的影響,但Zn的加入量需要嚴格控制,若Zn含量過高則會增大合金的熱裂傾向,並影響Zr的作用。Mn與B共同作為除鐵劑,在鎂液中與雜質Fe相互作用,形成溶解度極小、熔點高且密度大的金屬間化合物如MnFe、FeB等沉澱,達到除去雜質Fe的目的。
本發明點火柱、支柱鎂合金中還加入有0.05%-0.12%稀土元素Ce,Ce的原子半徑為0.183mm,電負性為1.12,Ce的原子半徑與鎂原子的相對差值在15%之內,電負性差值均小於0.4,因此可以形成有限的固溶體以及穩定的化合物,從而更好的實現它們在鎂合金中的作用。Ce在鎂合金中具有良好的固溶強化效應,可有效阻止高溫下鎂合金晶粒的長大和晶界的滑移,
在本發明點火柱、支柱所用的鎂合金中,加入適量的Zn、Mn、B、Zr、Ce,並且進一步限制雜質元素Si、Fe、Ni、Cu的含量,通過它們的合理配置以及協同作用,顯著提高點火柱、支柱的耐熱性、耐腐蝕性能。
作為優選,Zn:1.20%-1.40%、Mn:0.48%-0.52%、B:0.18%-0.25%、Zr:0.20%-0.28%、Ce:0.08%-0.10%,餘量為Mg及不可避免的雜質。
所述的雜質包括Si≤0.002%、Fe≤0.002%、Ni≤0.002%、Cu≤0.002%。
在上述的一種改良的燃燒器中,點火柱、支柱均可通過如下方法製備:
S1、熔煉前處理:按上述鎂合金的組成元素及其質量百分比配製爐料,將爐料預熱至150-180℃後備用,再將坩堝在500-580℃下預熱至暗紅色後備用;
S2、熔煉:將配製好的爐料在700-730℃熔化成鎂液,攪拌均勻後繼續升溫至750-760℃,在氬氣保護下進行精煉、扒渣;
S3、壓鑄:將精煉、扒渣處理後的鎂液先冷卻到680-720℃,然後壓鑄到模具型腔中,得壓鑄件;
S4、熱處理:將壓鑄件先在300-320℃下保溫10-15h,隨爐冷卻,然後以3-4℃/s的速度升溫至380-400℃保溫2-4h,隨爐冷卻,接著以1-2℃/s的速度升溫至440-460℃保溫3-5h,隨後空冷至室溫,接著在200-220℃下保溫5-10h,空冷至室溫製得點火柱、支柱成品。
本發明點火柱、支柱通過四階段加熱方法進行熱處理,進一步提高點火柱、支柱的力學性能和加工性能。其中前三階段的加熱處理(類似於固溶處理)可以有效提高點火柱、支柱的強度並獲得較大的韌性和抗衝擊性,最後一階段的時效處理則可以明顯提高其硬度以及屈服強度。固溶處理和時效處理的溫度和時間都直接影響最終點火柱、支柱成品的質量,溫度過高或過低都達不到固溶處理和時效處理的目的。而由於鎂合金中的合金元素的擴散和合金相的分解過程都非常緩慢,一般的固溶處理和時效處理的時間都相對較長,但是本發明通過多階段的加熱處理,提高了加熱處理的效率,縮短了加熱時間。
步驟S3中所述的模具先預熱至260-280℃,即將精煉、扒渣處理後的鎂液先冷卻到680-720℃,然後澆注到已預熱至260-280℃的模具型腔中壓鑄成型。模具先預熱可進一步提高鑄件的性能。
步驟S3壓鑄工藝中的澆注溫度為720-730℃、壓射速度為8.2-10.5m/s、壓射比壓為25-35MPa、充型時間為22-25ms。在壓鑄前要將模具先預熱至260-280℃,以防止最終的壓鑄件形成縮孔或者縮松現象。在壓鑄過程中,澆注溫度、壓射速度、壓射比壓以及充型時間這些工藝參數對最終的壓鑄件的質量均有影響。澆注溫度過高或過低都會影響鎂熔體的成型。壓射速度過快,會導致壓鑄件產生氣孔等缺陷,過慢則不能讓鎂液在凝固前填充滿模具型腔中,從而影響壓鑄件的質量。壓射比壓過低或過高都會損害最終壓鑄件的質量。
在上述的一種改良的燃燒器中,各主通道環繞外爐頭軸心線均勻分布,每個主通道均彎折延伸至外爐頭且主通道的內壁通過一坡面與外混合腔的底面平滑連接。
在上述的一種改良的燃燒器中,內火蓋的上表面向內凹陷形成錐面,在內火蓋上開設有與內混合腔聯通的若干內出火孔,所述內出火孔環繞內火蓋軸心線均勻分布且每個內出火孔均垂直貫穿錐面設置。
在上述的一種改良的燃燒器中,外火蓋的上表面部分向外凸起形成首尾依次連接的若干半月形凸塊,每個半月形凸塊的上端面均開設有均勻分布的若干第一外出火孔,每個半月形凸塊的外側面均開設有均勻分布的若干第二外出火孔,各外出火孔均與外混合腔聯通。
在上述的一種改良的燃燒器中,在外爐頭外周側壁貫穿開設有均勻分布的若干進風槽,在內爐頭外周側壁上開設有與內混合腔聯通的輔助槽。
與現有技術相比,本發明結構設計合理,採用多個相互配合的主通道與主進氣管,使通入外爐頭內的燃氣流通混合充分,有利於後續燃燒的進行;次通道與次進氣管的設置,用於供給內爐頭內的燃氣,使燃氣分布均勻;內火蓋與外火蓋的結構設計以及半月形凸塊的設置使得燃燒器造型更加美觀。
附圖說明
圖1是本發明一較佳實施例的結構示意圖。
圖2是圖1另一視角的結構示意圖。
圖3是圖1的部分結構示意圖。
圖4是圖3另一視角的結構示意圖。
圖中,11、外爐頭;111、外混合腔;112、進風槽;12、外火蓋;121、半月形凸塊;122、第一外出火孔;123、第二外出火孔;21、內爐頭;211、內混合腔;212、輔助槽;213、通孔;22、內火蓋;221、錐面;222、內出火孔;31、主通道;311、坡面;32、次通道;41、主進氣管;42、次進氣管;50、點火柱;60、支柱。
具體實施方式
以下是本發明的具體實施例並結合附圖,對本發明的技術方案作進一步的描述,但本發明並不限於這些實施例。
如圖1至圖4所示,本改良的燃燒器包括:
外爐頭11,呈圓環狀設置,在外爐頭11上扣合有外火蓋12且外火蓋12與外爐頭11合圍形成外混合腔111,在外爐頭11底部設置有與外混合腔111聯通的多個主通道31,主通道31的橫截面呈方形設置;
內爐頭21,穿設在外爐頭11中部,在內爐頭21上扣合有內火蓋22且內火蓋22與內爐頭21合圍形成內混合腔211,在內爐頭21底部設置有與內混合腔211聯通的次通道32;
管道組件,位於外爐頭11下方,在管道組件上設置有與次通道32對應的次進氣管42以及與各主通道31一一對應的多個主進氣管41;
點火柱50,設置為多個,每個點火柱50均與管道組件聯通,點火柱50豎直向上延伸並抵靠在內爐頭21外周側壁上;
支柱60,設置為多個,各支柱60豎直安裝在管道組件下方;
所述的點火柱、支柱均由鎂合金製成,所述鎂合金的組成元素及質量百分比為:Zn:1.00%-1.60%、Mn:0.38%-0.68%、B:0.18%-0.28%、Zr:0.20%-0.30%、Ce:0.05%-0.12%,餘量為Mg及不可避免的雜質。
爐頭內部往往設置特定結構的流通通道,燃氣在爐頭內流通之後經點火裝置點燃,然而現有的燃氣灶大都設置一個進氣口(進氣管)供燃氣進入爐頭,短時間內燃氣在爐頭內部流通不暢,從而容易導致燃氣燃燒不夠充分,燃燒效果差且安全性較低。
為此,本發明設計了一種改良的燃燒器,通過設置多個配合作用的主進氣管41與主通道31,使得燃氣在燃燒器內流通混合充分,便於後續的燃燒工作。
本實施例中優選主通道31與主進氣管41的數量均為三個,用於供給外爐頭11內的燃氣,內爐頭21則通過次通道32與次進氣管42配合輸送燃氣。由於燃燒時,火焰往往會沿著鍋具向外側延伸,此處獨立供給內爐頭21燃氣可以確保鍋具受熱均勻。
工作時,一部分燃氣經主進氣管41進入對應的主通道31,進入外爐頭11內的外混合腔111,最終由外火蓋12輸出進行燃燒;部分燃氣經次進氣管42進入次通道32,進入內爐頭21的內混合腔211,最終由內火蓋22輸出進行燃燒。
內火蓋22與外火蓋12的設置一方面控制燃氣的輸出,另一方面能夠避免外部物質流入對應的爐頭內,影響燃燒器工作。
燃燒時,外部控制點火柱50進行點火,具體的,在點火柱50內設置有點火針(圖中未示出),通過控制點火針對燃氣進行點火燃燒。點火柱50抵靠在內爐頭21外周側壁上,便於快速點燃燃氣,此處優選點火柱50的數量為兩個。
燃燒器往往是安裝在燃氣灶內進行工作的,燃燒器通過設置在底部的支柱60與燃氣灶固定連接,本實施例中,支柱60的數量優選為四個,均勻分布在管道組件下方,給予燃燒器支撐作用。
進一步地,各主通道31環繞外爐頭11軸心線均勻分布,每個主通道31均彎折延伸至外爐頭11且主通道31的內壁通過一坡面311與外混合腔111的底面平滑連接。
具體的,三個主通道31均勻分布在外爐頭11底部。由於主通道31的橫截面呈方形設置,為了保證燃氣進入外混合腔111是流通通暢,主通道31的內壁通過一坡面311與外混合腔111的底面平滑連接,使燃氣流通混合充分。
優選地,內火蓋22的上表面向內凹陷形成錐面221,在內火蓋22上開設有與內混合腔211聯通的多個內出火孔222,內出火孔222環繞內火蓋22軸心線均勻分布且每個內出火孔222均垂直貫穿錐面221設置。
內出火孔222的設置便於控制燃氣均勻輸出,而錐面221的設置使得燃氣輸出時較為集中,有利於點火燃燒,其中內出火孔222均垂直貫穿錐面221設置則進一步確保燃氣朝著中心輸出,保證中心火焰的集中性,燃燒效果好。
值得一提的是,在錐面221的邊緣環繞內出火孔222開設了一些凹槽,使得錐面221呈現出花瓣狀結構,且每個內出火孔222對應一個花瓣,增強整體的美觀性。
此外,內爐頭21中部貫穿開設有通孔213,且通孔213向上延伸並穿過內火蓋22,便於空氣進入,與燃氣混合充分,有利於燃氣的充分燃燒。
進一步優選地,外火蓋12的上表面部分向外凸起形成首尾依次連接的多個半月形凸塊121,每個半月形凸塊121的上端面均開設有均勻分布的多個第一外出火孔122,每個半月形凸塊121的外側面均開設有均勻分布的多個第二外出火孔123,各外出火孔均與外混合腔111聯通。
外爐頭11內的燃氣最終經由第一外出火孔122、第二外出火孔123輸出,各外出火孔的設置同樣便於控制燃氣均勻輸出,便於燃氣充分燃燒。其中,半月形凸塊121的設置,提高了整體的美觀性。
優選地,在外爐頭11外周側壁貫穿開設有均勻分布的多個進風槽112,在內爐頭21外周側壁上開設有與內混合腔211聯通的輔助槽212。
進風槽112的設置便於空氣進入,進風槽112不與外混合腔111聯通,空氣可經由進風槽112進入輔助槽212,進一步進入內混合腔211內與燃氣混合均勻,便於燃氣的充分燃燒。此處優選進風槽112的數量為三個。
本改良的燃燒器結構設計合理,採用多個相互配合的主通道31與主進氣管41,使通入外爐頭11內的燃氣流通混合充分,有利於後續燃燒的進行;次通道32與次進氣管42的設置,用於供給內爐頭21內的燃氣,使燃氣分布均勻;內火蓋22與外火蓋12的結構設計以及半月形凸塊121的設置使得燃燒器造型更加美觀。
本發明改良的燃燒器中的點火柱、支柱由鎂合金製成,下面通過具體實施例進一步說明本發明改良的燃燒器中的點火柱、支柱。
表1:實施例1-5中點火柱或支柱所用的鎂合金的組成元素及質量百分比
實施例1
熔煉前處理:按表1實施例1所述鎂合金的組成元素及其質量百分比配製爐料,將爐料預熱至160℃後備用,再將坩堝在540℃下預熱至暗紅色後備用;
熔煉:將配製好的爐料在715℃熔化成鎂液,攪拌均勻後繼續升溫至755℃,在氬氣保護下進行精煉、扒渣;
壓鑄:將精煉、扒渣處理後的鎂液先冷卻到700℃,然後澆注到已預熱至270℃的模具型腔中壓鑄成型,得壓鑄件;其中,澆注溫度為725℃、壓射速度為9.2m/s、壓射比壓為30MPa、充型時間為24ms。
熱處理:將壓鑄件先在310℃下保溫12h,隨爐冷卻,然後以3.5℃/s的速度升溫至390℃保溫3h,隨爐冷卻,接著以1.5℃/s的速度升溫至450℃保溫4h,隨後空冷至室溫,接著在210℃下保溫8h,空冷至室溫製得點火柱成品。
實施例2
熔煉前處理:按表1實施例2所述鎂合金的組成元素及其質量百分比配製爐料,將爐料預熱至170℃後備用,再將坩堝在560℃下預熱至暗紅色後備用;
熔煉:將配製好的爐料在720℃熔化成鎂液,攪拌均勻後繼續升溫至752℃,在氬氣保護下進行精煉、扒渣;
壓鑄:將精煉、扒渣處理後的鎂液先冷卻到710℃,然後澆注到已預熱至275℃的模具型腔中壓鑄成型,得壓鑄件;其中,澆注溫度為728℃、壓射速度為8.8m/s、壓射比壓為32MPa、充型時間為25ms。
熱處理:將壓鑄件先在305℃下保溫14h,隨爐冷卻,然後以3.2℃/s的速度升溫至385℃保溫3.5h,隨爐冷卻,接著以1.2℃/s的速度升溫至445℃保溫4.5h,隨後空冷至室溫,接著在208℃下保溫8h,空冷至室溫製得支柱成品。
實施例3
熔煉前處理:按表1實施例3所述鎂合金的組成元素及其質量百分比配製爐料,將爐料預熱至155℃後備用,再將坩堝在520℃下預熱至暗紅色後備用;
熔煉:將配製好的爐料在710℃熔化成鎂液,攪拌均勻後繼續升溫至758℃,在氬氣保護下進行精煉、扒渣;
壓鑄:將精煉、扒渣處理後的鎂液先冷卻到690℃,然後澆注到已預熱至265℃的模具型腔中壓鑄成型,得壓鑄件;其中,澆注溫度為722℃、壓射速度為10.2m/s、壓射比壓為28MPa、充型時間為23ms。
熱處理:將壓鑄件先在315℃下保溫12h,隨爐冷卻,然後以3.8℃/s的速度升溫至395℃保溫2.5h,隨爐冷卻,接著以1.8℃/s的速度升溫至455℃保溫3.5h,隨後空冷至室溫,接著在218℃下保溫6h,空冷至室溫製得點火柱成品。
實施例4
熔煉前處理:按表1實施例4所述鎂合金的組成元素及其質量百分比配製爐料,將爐料預熱至150℃後備用,再將坩堝在500℃下預熱至暗紅色後備用;
熔煉:將配製好的爐料在700℃熔化成鎂液,攪拌均勻後繼續升溫至750℃,在氬氣保護下進行精煉、扒渣;
壓鑄:將精煉、扒渣處理後的鎂液先冷卻到680℃,然後澆注到已預熱至260℃的模具型腔中壓鑄成型,得壓鑄件;其中,澆注溫度為720℃、壓射速度為10.5m/s、壓射比壓為35MPa、充型時間為25ms。
熱處理:將壓鑄件先在300℃下保溫15h,隨爐冷卻,然後以3℃/s的速度升溫至400℃保溫2h,隨爐冷卻,接著以1℃/s的速度升溫至440℃保溫5h,隨後空冷至室溫,接著在200℃下保溫10h,空冷至室溫製得點火柱成品。
實施例5
熔煉前處理:按表1實施例5所述鎂合金的組成元素及其質量百分比配製爐料,將爐料預熱至180℃後備用,再將坩堝在580℃下預熱至暗紅色後備用;
熔煉:將配製好的爐料在730℃熔化成鎂液,攪拌均勻後繼續升溫至760℃,在氬氣保護下進行精煉、扒渣;
壓鑄:將精煉、扒渣處理後的鎂液先冷卻到720℃,然後澆注到已預熱至280℃的模具型腔中壓鑄成型,得壓鑄件;其中,澆注溫度為730℃、壓射速度為8.2m/s、壓射比壓為25MPa、充型時間為22ms。
熱處理:將壓鑄件先在320℃下保溫10h,隨爐冷卻,然後以4℃/s的速度升溫至400℃保溫2h,隨爐冷卻,接著以2℃/s的速度升溫至460℃保溫3h,隨後空冷至室溫,接著在220℃下保溫5h,空冷至室溫製得支柱成品。
對比例1
現有技術中普通市售的燃燒器中的點火柱或支柱。
對比例2
採用普通鎂合金通過如實施例1所述的方法製得的燃燒器中的點火柱或支柱。
對比例3
採用如實施例1中的鎂合金通過普通加工方法製得的燃燒器中的點火柱或支柱。
發明改良的燃燒器中的點火柱或支柱採用性能優異的鎂合金製成,其製備方法簡單可行,得到的點火柱、支柱與普通的相比,具有更高的抗拉強度、屈服強度、耐腐蝕性、耐溫性等性能,進而提高燃燒器的綜合性能。
本文中所描述的具體實施例僅僅是對本發明精神作舉例說明。本發明所屬技術領域的技術人員可以對所描述的具體實施例做各種各樣的修改或補充或採用類似的方式替代,但並不會偏離本發明的精神或者超越所附權利要求書所定義的範圍。