一種大溫差固井用水泥漿稠化時間的實驗方法與流程
2023-10-09 21:15:14 3
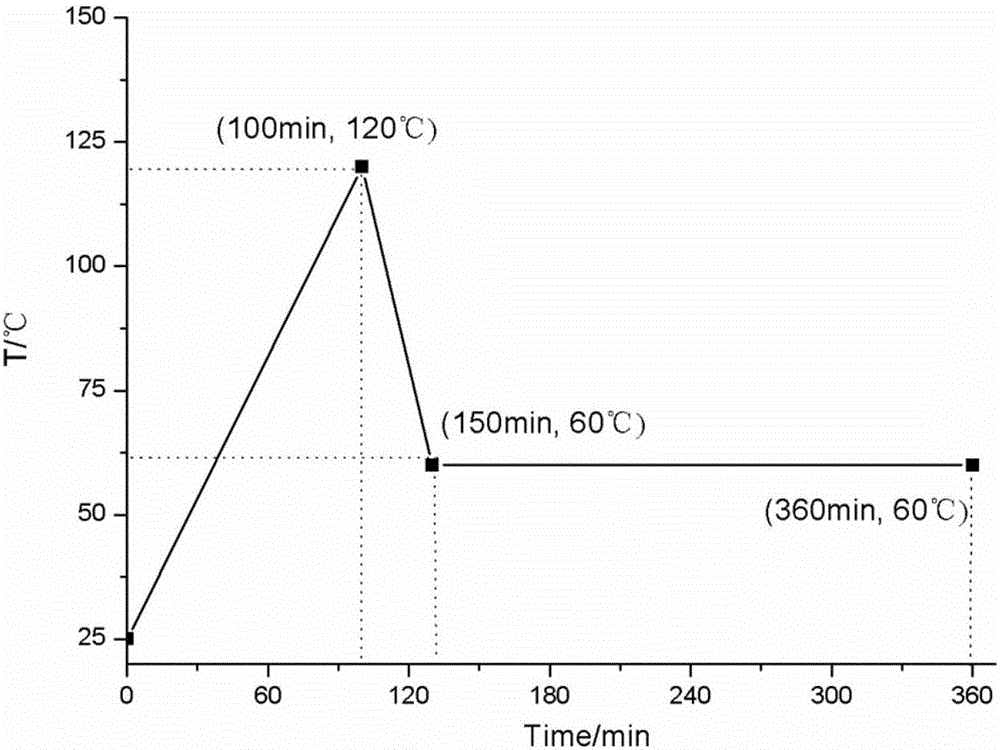
本發明涉及固井用水泥漿的稠化時間的測量方法,具體涉及一種大溫差固井用水泥漿稠化時間的實驗方法。
背景技術:
稠化時間是固井施工中的重要參數之一,它決定了固井作業的成敗。稠化時間是指油井水泥在一定溫度與壓力條件下,從開始拌漿到稠度達到100個稠度單位(Bc-伯登)時所需要的時間,它是模擬現場注水泥過程所得到的室內實驗值。在固井時,為了保證有絕對安全的泵入時間,避免「灌香腸」等事故發生,必須對使用的水泥漿進行稠化時間實驗。
在大溫差固井施工中,API標準稠化時間的測定方法,並未模擬大溫差固井的真實環境,儘管GB/T 19139-2012《油井水泥試驗方法》中明確指出(見GB/T19139-2012第9章水泥漿稠化時間試驗9.5.4.9~9.5.4.13),如有可靠的水泥柱頂部溫度數據,水泥漿可在預計井底循環溫度和井底壓力條件下保持特定時間(未明確規定),作為固定安全係數,然後將水泥漿溫度和壓力改為水泥柱頂部溫度和頂部壓力條件下,直到稠化時間試驗結束。但在實際操作中這一要求並未嚴格執行,而只是簡單地採用常規稠化時間測量方法。
對於大溫差固井,常規稠化時間評價方法並未做到緩凝劑的適宜摻量,只是單一的通過增大緩凝劑加量來保證井底高溫條件下水泥漿的可泵送時間,當水泥漿由井底返至預定頂部低溫井段時,由於過量緩凝劑的緩凝作用不能及時消除,使得頂部水泥石出現超緩凝現象。因此,與工程實際不相符合的稠化方法無法真正模擬大溫差固井的稠化時間及頂部水泥石抗壓強度,不但無法正確指導固井施工作業,還可能造成固井事故,降低勘探開發效益。
技術實現要素:
針對上述技術問題,本發明提供了一種大溫差固井用水泥漿稠化時間的實驗方法,以達到在滿足井底高溫施工安全時間的要求,同時又做到緩凝劑的合理加量,從而有效減小大溫差施工環境下由緩凝劑帶來的頂部水泥石強度發展緩慢問題,提高固井質量。
本發明解決其技術問題所採用的技術方案是:
在依據API標準的實驗方法基礎上,模擬實際固井的施工情況將稠度儀上的溫度和壓力設計成四個階段。
具體的技術方案為:
1、按照API標準的配漿方法及其他操作步驟進行操作;
2、將稠度儀上的溫度壓力設計分三個階段,第一階段由實驗室的常溫常壓到模擬井底靜止時的高溫高壓環境,所述第一階段的高溫溫為90~180℃,所述第一階段的高壓壓強為30~100Mpa;第二階段由模擬井底靜止的高溫高壓環境到低溫低壓環境,所述第二階段的低溫溫度為30~60℃,所述第二階段的低壓壓強為5~30Mpa;第三階段在低溫低壓條件下保持恆溫恆壓直至水泥漿稠化;
3、記錄實驗數據,分析水泥漿稠化時間的實驗結果。
上述方案是本發明的一種實驗方法,模擬了完整的固井施工過程,為一種理想狀態,但是考慮到整個固井施工泵送過程和安全係數,本發明的另一種方法還可以在上述方法中第一階段中的高溫高壓環境下保持恆溫恆壓兩小時。
本發明的有益效果為:
本發明的實驗方法綜合考慮了固井的實際工況,在稠度儀上設置不同階段的溫度和壓力梯度值不僅模擬了水泥漿的泵送過程,同時也考慮到了整個固井施工的安全係數。考慮到了固井施工中可能發生的意外情況,在高溫高壓環境下設置恆溫兩小時,以確保施工作業的安全進行。該實驗方法對實際工程具有貼切的指導意義,減少了施工風險,具有非常好的經濟效益;同時經過該方法稠化的水泥漿,在模擬頂部溫度條件下後期養護的水泥石均未出現超緩凝現象,強度滿足施工要求。
附圖說明
圖1為模擬井底120℃高溫、頂部60℃低溫的理想狀態下的稠化方式圖。
圖2為模擬井底120℃高溫、頂部60℃低溫考慮泵送和其他情況的稠化方式圖。
圖3為對比例(採用現有API標準方法)中水泥漿的稠化圖。
圖4為實施例1(本發明方法中的理想狀態下)中水泥漿的稠化圖。
圖5為實施例2(本發明方法中考慮泵送和其他情況下)中水泥漿的稠化圖。
圖3-5中橫向曲線從上至下依次為溫度變化曲線、壓力變化曲線和稠度變化曲線。
具體實施方式
為使本發明的目的、技術方案及效果更加清楚、明確,以下通過現有API標準的實驗方法及本發明方法得出的數據對比來說明本發明的有益效果。
以模擬井底120℃高溫、頂部60℃低溫為例,具體的實驗方法為:
1、按照API標準的配漿方法及其他操作步驟進行操作;
2、將稠度儀上的溫度壓力設計分三個階段,第一階段由常溫常壓升至模擬井底靜止時的120℃、60Mpa環境;第二階段由模擬井底靜止的120℃、60Mpa降至頂部60℃、30Mpa;第三階段在60℃、30Mpa的恆溫恆壓條件下稠化,直至稠度達到70Bc;
3、記錄並分析實驗數據。
以上方法為一種理想狀態下的稠化時間,在實際固井施工中,考慮到整個固井施工泵送過程和不可預見的情況出現,可在第一階段溫度由室溫升到120℃後保持120℃恆溫兩個小時,然後再進行降溫到60℃,此兩種方式測得的稠化時間隨溫度變化的曲線如圖1和圖2所示。
按上述方法進行以下具體實施例:
對比例,本對比例是按照現有API標準方法進行稠化時間的測定,具體方法為:
1、按照API標準配製水泥漿,具體水泥漿的配比見表1中實施例1的水泥漿配方;
2、整個溫度壓力的設置只有一個階段,即由常溫常壓升至模擬井底靜止時的120℃、60Mpa環境,並在60℃、30Mpa的恆溫恆壓條件下稠化,直至稠度達到70Bc;
3、整個過程的時間即為水泥漿的稠化時間,其測量結果如圖3所示。將本實施例中的水泥漿在60℃的溫度下進行養護48小時,其養護結果見表1中實施例1的頂部抗壓強度。
實施例一,本實施例是模擬固井施工中的理想狀態
1、按照API標準配製水泥漿,具體水泥漿的配比見表1中實施例2的水泥漿配方;
2、將稠度儀上的溫度壓力設計分三個階段,第一階段由常溫常壓升至模擬井底靜止時的120℃、60Mpa環境;第二階段由模擬井底靜止的120℃、60Mpa降至頂部80℃、30Mpa;第三階段在80℃、30Mpa的恆溫恆壓條件下稠化,直至稠度達到70Bc;
3、整個過程的時間即為水泥漿的稠化時間,其測量結果如圖4所示。將本實施例中的水泥漿在60℃的溫度下進行養護48小時,其養護結果見表1中實施例2的頂部抗壓強度。
本實施例根據實際大溫差固井施工過程,在稠度儀上設置階段溫度和壓力,增加了水泥漿從井底安全泵送至頂部的過程。
實施例二,本實施例考慮了固井施工中泵送的不確定性和其他情況
1、按照API標準配製水泥漿,具體水泥漿的配比見表1中實施例3的水泥漿配方;
2、將稠度儀上的溫度壓力設計分為四個階段,第一階段由常溫常壓升至模擬井底靜止時的120℃、60Mpa環境,第二階段在井底120℃、60Mpa環境下恆溫恆壓兩小時,第三階段由模擬井底靜止的120℃、60Mpa降至頂部80℃、30Mpa;第四階段在80℃、30Mpa的恆溫恆壓條件下稠化,直至稠度達到70Bc;
3、整個過程的時間即為水泥漿的稠化時間,其測量結果如圖5所示。將本實施例中的水泥漿在60℃的溫度下進行養護48小時,其養護結果見表1中實施例3的頂部抗壓強度。
表1水泥漿配方及不同稠化方法下的稠化時間
由圖3~5及表1可知,
1、本發明方法中緩凝劑的投放量明顯小於API標準方法中緩凝劑的投放量;
2、在相同養護條件下,API標準方法中頂部水泥漿出現超緩凝現象,而本發明的方法中稠化時間不僅滿足施工要求,並且所需緩凝劑加量較少,頂部水泥石抗壓強度發展良好。
應當理解的是,本發明的應用不限於上述的舉例,對本領域普通技術人員來說,可以根據上述說明加以改進或變換,所有這些改進和變換都應屬於本發明所附權利要求的保護範圍。