一種帶水分回收系統的用低階煤生產輕質芳烴的系統及方法與流程
2023-10-22 06:46:17 2
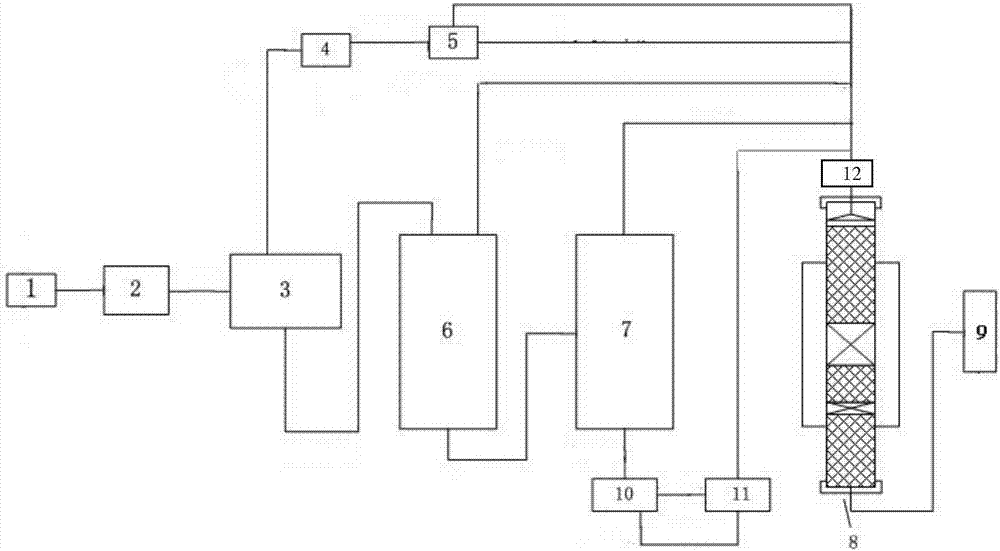
本發明涉及由低階煤製備輕質芳烴的組合工藝,更具體地,涉及一種用低階煤生產輕質芳烴的系統及方法。
背景技術:
我國的能源格局一直是富煤、貧油、少氣。煤炭儲量可達世界煤炭儲量的17%。其中褐煤、長焰煤等低階煤資源儲量豐富,佔我國煤炭儲量及煤炭產量50%以上,但由於低階煤水含量高,直接燃燒或氣化效率低且現有技術無法充分利用其資源價值,導致了煤炭資源的巨大浪費。2015年4月國家能源局發布了《煤炭清潔高效利用行動計劃(2015-2020)》,將煤炭分質分級利用地位顯著提高,大力倡導低階煤提質技術的研發和示範。因此,開發低階煤的清潔高效利用新途徑具有十分重大的現實意義。
苯、甲苯和二甲苯等輕質芳烴都是非常重要的化工基礎原料,廣泛應用於生產橡膠、纖維、塑料和染料等化工產品。目前,芳烴主要來源於石油化工中的催化重整和烴類熱解,僅有約10%來源於煤炭化工。但是目前石油資源越來越匱乏,因此,開發新的由低階煤生產苯等輕質芳烴的技術勢在必行。
現有技術中利用煤乾餾產物煤焦油製取輕質芳烴的方法,該方法將煤焦油切割成200℃重質餾分,輕質餾分進入兩個固定床加氫反應器進行選擇性加氫,所得的產物經氣提、蒸餾、溶劑萃取等過程得到苯、甲苯、二甲苯等輕質芳烴。該方法用煤焦油替代石油製取輕質芳烴,是芳烴生產的有利補充。但是,煤乾餾所得的煤焦油產量較低,一般小於5%,而煤焦油中<200℃餾分不到30%,高溫煤焦油中輕質組分含量更低,因此該方法所產輕質芳烴產量較少,沒有充分利用煤炭資源來生產芳烴,不能從根本上解決石油資源匱乏帶來的芳烴產量降低問題。
因此,為了克服現有技術中的技術缺陷,需要一種由中或低階煤生產苯等輕質芳烴的技術。
技術實現要素:
針對上述問題,本發明的目的是提供一種用低階煤生產輕質芳烴的系統及方法。
為達到上述目的,本發明採用如下技術方案:
一種帶水分回收系統的用低階煤生產輕質芳烴的系統,包含:
混合器,該混合器包含第一物料進口和第二物料出口;
旋轉床熱解裝置,包括第二物料進口,第三物料出口和第一氣體出口,第二物料進口與第二物料出口相連;
電石爐,該電石爐包含第三物料進口、第四物料出口和第二氣體出口,電石爐的三物料進口與旋轉床熱解裝置的第三物料出口相連;
乙炔發生器,該乙炔發生器包含第四物料進口、第三氣體出口和第五物料出口,乙炔發生器的第四物料進口與電石爐的第四物料出口相連;乙炔發生器的第三氣體出口用於排出生成的乙炔;
乙炔制芳烴反應器,該乙炔制芳烴反應器具有進料管線、氣體分布器、反應套管、加熱爐和出料管線;進料管線設置有入口和出口,入口用於通入包含第三氣體的氣體物料;氣體分布器設置在反應套管的內部且位於反應套管的上端並且與進料管線的出口連通;反應套管內填充用於蓄熱的陶瓷蜂窩體;反應套管貫穿加熱爐,加熱爐正對反應套管的中部;出料管線與反應套管的下端連通;
水分回收系統,包括自然沉降器和蒸發濃縮器,自然沉降器具有第五物料進口和第六物料出口,第五物料進口與乙炔發生器的第五物料出口相連;蒸發濃縮器具有第六物料進口和第四氣體出口,第六物料進口與自然沉降器的第六物料出口相連。
進一步地,第二物料進口與第二物料出口之間設置有壓球裝置,壓球裝置用於對第二物料壓球。
進一步地,乙炔制芳烴反應器的進料管線的入口可斷開式地連接混合罐,混合罐用於混合通入乙炔制芳烴反應器的氣體。
進一步地,蒸發濃縮器的第四氣體出口與乙炔制芳烴反應器的進料管線的入口設置為可斷開式連接。
進一步地,乙炔制芳烴反應器的反應套管的內徑、反應套管的長度和加熱爐的長度的比例為(2-10):70:40。
另一方面,本發明提供一種使用如上所述的系統生產芳烴的方法,包括以下步驟:
1)原料混合和熱解:將生石灰粉末和低階煤粉末在混合器中混合得混合粉料,混合粉料進入旋轉床熱解裝置進行熱解,得到熱解油氣和提質後物料;
2)生產電石:提質後物料進入電石爐中生產電石和一氧化碳;
3)生產乙炔:將步驟2)得到的電石在乙炔發生器中與水反應,得到乙炔和電石渣漿;
4)回收電石渣漿中的水分:使步驟3)所得的電石渣漿進入自然沉降器經過自然沉降後得到上清液,使上清液進入蒸發濃縮器進行蒸發濃縮得到水蒸氣;
5)連續生產輕質芳烴:向乙炔制芳烴反應器通入,包含來自步驟3)的乙炔在內的氣體,進行熱反應和催化反應,製得芳烴。
進一步地,當方法在步驟5)芳烴的生產連續進行一段時間且乙炔制芳烴反應器中產生積炭時,方法還包括步驟6)乙炔制芳烴反應器的再生過程:停止通入反應氣,通入步驟4)得到的水蒸氣,水蒸汽高溫下與積炭反應,去除積炭後,可繼續通入反應氣重複步驟5)的過程。
進一步地,步驟1)中,混合粉料進入旋轉床熱解裝置之前,先通過壓球裝置對混合粉料進行壓球。
進一步地,步驟5)中,熱反應的溫度為850~1100℃;催化反應的溫度為350~600℃。
進一步地,步驟5)中向乙炔制芳烴反應器通入包含步驟3)中得到的乙炔在內的氣體,包括:使步驟3)中得到的乙炔在混合罐中與氫氣、甲烷和二氧化碳混合得反應氣,並將反應氣通入乙炔制芳烴反應器中。
本發明中「可斷開式連接」是指非固定連接,這樣的連接方式是指:當需要連接時能夠連接,需要斷開時能夠斷開。
根據本發明的具體實施方式,提供一種用低階煤生產輕質芳烴的系統,包含:
混合器,該混合器包含第一進口和第一出口;
壓球機,該壓球機包含第二進口和第二出口,壓球機的第二進口與混合器的第一出口相連;
旋轉床熱解裝置,該旋轉床熱解裝置包含第三球團進口、第三球團出口和第三氣體出口,旋轉床熱解裝置的第三球團進口與壓球機的第二出口相連;
電石爐,該電石爐包含第四球團進口、第四電石出口和第四氣體出口,電石爐的第四球團進口與旋轉床熱解裝置的第三球團出口相連;第四氣體出口用於排出一氧化碳;
乙炔發生器,該乙炔發生器包含第五進口、第五出口和電石渣漿出口,乙炔發生器的第五進口與電石爐的第四電石出口相連;乙炔發生器的第五出口用於排出生成的乙炔;
油氣分離器,該油氣分離器包含第六進口、第六出口和煤焦油出口,油氣分離器的第六進口與旋轉床熱解裝置的第三氣體出口相連;
淨化裝置,該淨化裝置包含第七進口和多個第七出口,多個第七出口用於排出淨化分離出的氫氣、甲烷和二氧化碳氣體,淨化裝置的第七進口與油氣分離器的第六出口相連;
乙炔制芳烴反應器,該乙炔制芳烴反應器具有進料管線、氣體分布器、反應套管、加熱爐和出料管線;進料管線設置有入口和出口,入口用於通入從淨化裝置分離出的氫氣和甲烷以及二氧化碳、從電石爐排出的一氧化碳以及從乙炔發生器製得的乙炔;氣體分布器設置在反應套管的內部且位於反應套管的上端並且與進料管線的出口連通;反應套管內填充用於蓄熱的陶瓷蜂窩體;反應套管貫穿加熱爐,加熱爐正對反應套管的中部;出料管線與反應套管的下端連通;
分離系統,該分離系統與乙炔制芳烴反應器的出料管線相連,用於分離乙炔制芳烴反應器的產物;
自然沉降器,該自然沉降器具有第九進口、濃縮液進口、電石渣出口和上清液出口,自然沉降器的第九進口與乙炔發生器的電石渣漿出口相連;
蒸發濃縮器,該蒸發濃縮器具有上清液進口、濃縮液出口和水蒸汽出口,蒸發濃縮器的上清液進口與自然沉降器的上清液出口相連,蒸發濃縮器的濃縮液出口與自然沉降器的濃縮液進口相連。
進一步地,蒸發濃縮器的水蒸汽出口與乙炔制芳烴反應器的進料管線的入口可斷開式連接。
進一步地,電石爐的第四氣體出口處設置分流閥,分流閥具有第一分流口和第二分流口,其中電石爐的第四氣體出口通過分流閥的第一分流口將一氧化碳通入乙炔制芳烴反應器的進料管線的入口,分流閥的第二分流口用於為系統輸送燃料氣。
進一步地,乙炔制芳烴反應器的進料管線連接混合罐用於混合通入乙炔制芳烴反應器的氣體。
進一步地,乙炔制芳烴反應器的反應套管的內徑、反應套管的長度和加熱爐的長度的比例為(2-10):70:40。這裡,反應套管的內徑、反應套管的長度和加熱爐的長度的比例優選為1:14:8。在本發明中,反應套管的內徑、反應套管的長度和加熱爐的長度的比例確定了,並且反應溫度確定了之後,加熱爐對反應套管加熱時反應套管中的溫度場就確定了。
反應套管內填充用於蓄熱的陶瓷蜂窩體。反應套管內填滿了陶瓷蜂窩體,陶瓷蜂窩體具有較高的蓄熱能力,可提高能量利用效率,保證氣體在熱反應區有均勻的熱場。陶瓷蜂窩體具有熱容較大,蓄熱效果好的優點。
進一步地,乙炔制芳烴反應器還包括第一密封元件和第二密封元件,第一密封元件設置在進料管線與反應套管的連接處,第二密封元件設置在出料管線與反應套管的連接處。
進一步地,當加熱爐對反應套管加熱時,反應套管內自上而下根據溫度場依次劃分為預熱區、熱反應區、蓄熱區、催化反應區和冷卻區。
在本發明中,乙炔制芳烴反應器的加熱爐正對反應套管的中部指的是加熱爐對應反應套管的中部,與反應套管上端之間的距離和下端之間的距離相同。這樣的設置有利於保持反應溫度的恆定,且加熱爐在熱反應區中心位置設置控溫點。
進一步地,其特徵在於,預熱區、熱反應區、蓄熱區、催化反應區和冷卻區的長度比例為(20-40):(8-12):(8-12):(1-3):(18-20)。
進一步地,反應套管為內襯陶瓷的不鏽鋼反應套管。不鏽鋼套管內襯採用陶瓷是因為乙炔在高溫下接觸不鏽鋼將發生大量副反應,內襯陶瓷可避免乙炔和不鏽鋼的接觸,防止副反應。
另外,使用如上的系統生產輕質芳烴的方法,包括以下步驟:
1)原料壓球和熱解:將生石灰粉末和低階煤粉末在混合器中混合,進入壓球機進行壓球處理,球團進入旋轉床熱解裝置進行熱解提質,得到熱解油氣和提質後的球團,熱解油氣經過油氣分離器後得到熱解氣和煤焦油,熱解氣進入淨化裝置得到氫氣、甲烷和二氧化碳;
2)生產電石:提質後的球團熱裝進入電石爐中生產電石和一氧化碳;
3)生產乙炔:將步驟2)得到的電石在乙炔發生器中與水反應,得到乙炔和電石渣漿;
4)回收電石渣漿中的水分:使步驟3)所得的電石渣漿進入自然沉降器經過自然沉降後得到上清液,使上清液進入蒸發濃縮器進行蒸發濃縮得到水蒸氣,水蒸氣用於乙炔制芳烴反應器的再生過程;
5)連續生產輕質芳烴:將步驟1)中得到的二氧化碳、氫氣和甲烷、步驟2)得到的一氧化碳和步驟3)中得到的乙炔混合作為反應氣通入乙炔制芳烴反應器進行熱反應和催化反應,生產輕質芳烴,副產物為乙烯和重質芳烴。
進一步地,二氧化碳:氫氣:甲烷:一氧化碳:乙炔質量配比為:0.2-0.4:1:2-3:2-4:4-6。
進一步地,方法在步驟5)生產輕質芳烴連續進行一段時間且乙炔制芳烴反應器中產生積炭後,還包括乙炔制芳烴反應器的再生過程:停止通入反應氣,通入步驟4)得到的水蒸氣,水蒸汽高溫下與積炭反應,去除積炭後,可繼續通入反應氣重複上述步驟5)的過程。
進一步地,步驟5)中,當加熱爐對反應套管加熱時,反應套管內,根據溫度場由上而下依次劃分為:預熱區、熱反應區、蓄熱區、催化反應區和冷卻區;在熱反應區進行熱反應,熱反應溫度為850~1100℃;在催化反應區進行催化反應,催化反應溫度為350~600℃。
進一步地,催化反應區中包含有催化劑,催化劑為負載金屬釕的蜂窩陶瓷體。催化溫度為350~600℃,釕催化劑既能在步驟4)的反應過程中催化乙炔三聚生成苯等輕質芳烴,又能在步驟5)的再生過程中,催化一氧化碳和水蒸氣發生反應,生成氫氣。該反應器耦合了熱反應和催化反應,提高了乙炔轉化率和輕質芳烴收率,利用了熱反應餘熱,有效提高熱利用率,同時可實現反應器在線再生,並額外產生氫氣,用於製備芳烴。為保證芳烴的連續生產,可並聯兩個乙炔制芳烴反應器,分別進行反應過程和再生過程,互相切換。
進一步地,步驟5)中,催化反應的催化劑為金屬催化劑,金屬催化劑負載在陶瓷蜂窩體上。
進一步地,金屬催化劑為鎳、鉬、鈀、釕或銠中的一種或幾種。
進一步地,金屬催化劑的質量百分比為0.1%-5%。
進一步地,步驟1)中低階煤與生石灰的混合質量比為(1:1.1)~(1:1.4)。
進一步地,步驟1)中的低階煤指的是揮發分大於35%的低品質煤。
進一步地,低階煤與生石灰的混合粉料進入壓球裝置得到的球團粒徑為10~40mm,將球團的粒徑控制在合適範圍內有利於傳熱,提高熱效率。
進一步地,步驟1)中球團送入旋轉床熱解裝置進行提質,旋轉床熱解溫度為600~800℃,熱解時間1~2h。經過熱解提質後得到提質球團和熱解油氣,熱解油氣經過冷卻等步驟分離出熱解氣和煤焦油。熱解氣經過淨化分離可得到氫氣、甲烷、二氧化碳、一氧化碳、輕質烴類等可燃組分,其中甲烷、氫氣和二氧化碳可作為步驟4)中乙炔制芳烴反應器的原料,其餘的一氧化碳、輕質烴類等可燃氣體可為乙炔制芳烴反應器的加熱爐提供熱源,實現資源的有效利用。
進一步地,步驟1)的生石灰和低階煤應粉碎至20μm以下;優選粒徑10μm以下。將生石灰和煤粉混合,可有效增加反應物的接觸面積,提高反應效率,同時先壓球後熱解,可利用低階煤本身具有的粘結性,減少壓球的難度。
進一步地,步驟3)中的電石粉碎至80mm以下,優選粒徑為50~80mm。
進一步地,步驟3)的電石渣漿中固含量約為12%,主要成分為氫氧化鈣,工業中一般將電石渣漿自然沉降,上清液中仍含有一定量的氫氧化鈣,不符合直接排放要求,而循環利用存在著結垢嚴重的問題,因此本方法中將上層清液蒸發濃縮,水蒸氣通入乙炔制芳烴反應器中用於積炭再生過程,濃縮液冷卻後循環回自然沉降單元進行固液分離。
進一步地,步驟4)的反應過程中乙炔在高溫下聚合反應生成芳烴;步驟5)的再生過程中,水蒸氣與高溫的積炭接觸生成一氧化碳和氫氣,並富餘一部分水蒸氣。
為保證芳烴的連續生產,可並聯兩個乙炔制芳烴反應器,一個乙炔制芳烴反應器進行乙炔高溫下催化聚合反應;另一個乙炔制芳烴反應器進行再生反應,互相切換。
再生反應過程為:蒸發濃縮器中產生的水蒸氣,通入乙炔制芳烴反應器,在熱反應區,水蒸氣與高溫積炭反應生成一氧化碳和氫氣,熱反應區溫度為1000℃以上,例如1000-1100℃;在催化反應區,一氧化碳和水蒸氣在催化劑的作用下反應生成氫氣和二氧化碳,得到的氫氣分離淨化後可作為乙炔制芳烴的原料氣,實現資源的有效利用。
本發明的有益效果是:
本發明由煤制芳烴,解決了由於石油資源有限帶來的芳烴產量限制的問題,實現了從低價值的低階煤到高附加值的芳烴的轉變過程。
本發明的低階煤和生石灰球團進入旋轉床提質,氣體產物可作為燃料氣和乙炔制芳烴反應原料氣;提質煤與生石灰生產電石,製備乙炔,作為乙炔制芳烴反應器的原料氣,實現了低階煤的清潔高效利用。
本發明的乙炔制芳烴裝置耦合了熱反應和催化反應,提高了輕質芳烴產率。同時利用電石渣漿的上清液實現在線再生。
附圖說明
圖1是按照本發明的實施例的用低階煤生產輕質芳烴的系統的示意圖;
圖2是按照本發明的實施例的乙炔制芳烴反應器的示意圖;
圖3是按照本發明的實施例的用低階煤生產輕質芳烴的工藝流程圖。附圖標記
1混合器、2壓球機、3旋轉床熱解裝置、4油氣分離器、5淨化裝置、6電石爐、7乙炔發生器、8乙炔制芳烴反應器、82反應套管、83加熱爐、84第一密封元件、85第二密封元件、86氣體分布器、87進料管線、88出料管線、89預熱區、810熱反應區、811蓄熱區、812催化反應區、813冷卻區、9分離系統、10自然沉降器、11蒸發濃縮器、12混合罐。
具體實施方式
為了使本發明的目的、技術方案及優點更加清楚明白,下面結合附圖及實施例,對本發明進行進一步詳細說明。應當理解,此處所描述的具體實施例僅用以解釋本發明,並不用於限定本發明。
如圖1所示,用低階煤生產輕質芳烴的系統,包含混合器1、壓球機2、旋轉床熱解裝置3、電石爐6、乙炔發生器7、油氣分離器4、淨化裝置5、乙炔制芳烴反應器8、分離系統9、自然沉降器10、蒸發濃縮器11和混合罐12。
混合器1包含第一進口和第一出口,第一進口用於進行原料裝填;壓球機2包含第二進口和第二出口,壓球機2的第二進口與混合器1的第一出口相連;旋轉床熱解裝置3包含第三球團進口、第三球團出口和第三氣體出口,第三氣體出口用於排出熱解油氣。旋轉床熱解裝置3的第三球團進口與壓球機2的第二出口相連。
電石爐6包含第四球團進口、第四電石出口和第四氣體出口,電石爐6的第四球團進口與旋轉床熱解裝置的第三球團出口相連,第四氣體出口用於排出一氧化碳;電石爐6的第四氣體出口處設置分流閥,分流閥具有第一分流口和第二分流口,電石爐6的第四氣體出口通過分流閥的第一分流口將一氧化碳通入乙炔制芳烴反應器8的進料管線的入口,分流閥的第二分流口將一氧化碳作為燃料氣輸送至系統,例如作為乙炔制芳烴反應器8的加熱爐的燃料氣。
乙炔發生器7包含第五進口、第五出口和電石渣漿出口,乙炔發生器7的第五進口與電石爐的第四電石出口相連,乙炔發生器7的第五出口用於排出生成的乙炔,電石渣漿出口用於排出反應後的電石渣漿;油氣分離器4包含第六進口、第六出口和煤焦油出口,煤焦油出口用於排出分離出的煤焦油;油氣分離器4的第六進口與旋轉床熱解裝置3的第三氣體出口相連。
淨化裝置5包含第七進口和多個第七出口,淨化裝置5的第七進口與油氣分離器4的第六出口相連;多個第七出口用於排出淨化分離出的氫氣、甲烷和二氧化碳氣體。淨化裝置5可以採用本領域技術人員公知的淨化裝置,可以將淨化分離後的各種氣體通過不同的出口進行排出。
乙炔制芳烴反應器8具有進料管線87以及出料管線88,其中進料管線87設置有入口和出口,入口用於通入從淨化裝置5分離出的氫氣和甲烷以及二氧化碳、從電石爐6排出的一氧化碳以及從乙炔發生器7製得的乙炔。從淨化裝置5分離出的氫氣和甲烷以及二氧化碳、從電石爐6排出的一氧化碳以及從乙炔發生器7製得的乙炔先通入混合罐12進行混合,然後將混合氣體再通入乙炔制芳烴反應器。分離系統9用於分離產物,分離系統9與乙炔制芳烴反應器8的出料管線88相連。
自然沉降器10具有第九進口、濃縮液進口、電石渣出口和上清液出口,自然沉降器10的第九進口與乙炔發生器7的電石渣漿出口相連,電石渣漿進入自然沉降器10後,得到上清液和電石渣,上清液從上清液出口排出,電石渣從電石渣出口排出。
蒸發濃縮器11具有上清液進口、濃縮液出口和水蒸汽出口,蒸發濃縮器11的上清液進口與自然沉降器10的上清液出口相連,蒸發濃縮器11的濃縮液出口與自然沉降器10的濃縮液進口相連,即電石渣漿在自然沉降器10中進行沉降得到上清液和電石渣,上清液進入蒸發濃縮器11進行蒸發濃縮,得到水蒸汽和濃縮液,水蒸汽可以通入乙炔制芳烴反應器8,濃縮液可以回到自然沉降器10繼續進行沉降,重複上述過程,達到資源有效利用;其中,蒸發濃縮器11的水蒸汽出口與乙炔制芳烴反應器8的進料管線的入口可斷開式連接。
將水蒸汽輸送至乙炔制芳烴反應器8與積炭進行再生反應,使得積炭被消耗,乙炔制芳烴反應器8能夠循環使用,不必停工進行積炭清理。本文的「可斷開式連接」可以為本領域技術人員公知的可以根據需要閉合和接通的連接方式,例如添加一個閥門,在乙炔制芳烴反應器8反應過程中,關閉閥門使得水蒸汽無法進入乙炔制芳烴反應器8;在乙炔制芳烴反應器8的再生過程中,關閉反應氣,打開閥門使得水蒸汽進入乙炔制芳烴反應器8。
在另一個實施例中,為保證芳烴的連續生產,可並聯兩個乙炔制芳烴反應器,分別進行反應過程和再生過程,互相切換,提高生產效率。
如圖2所示,乙炔制芳烴反應器8還包括氣體分布器86、第一密封元件85、第二密封元件86、反應套管82和加熱爐83,氣體分布器86設置在反應套管82的內部且位於反應套管82的上端並且與進料管線87的出口連通;反應套管82內填充陶瓷蜂窩體;反應套管82貫穿加熱爐83,加熱爐83正對反應套管82的中部;出料管線與反應套管82的下端連通。第一密封元件85設置在進料管線87與反應套管82的連接處,第二密封元件86設置在出料管線與反應套管82的連接處。反應套管82內填充陶瓷蜂窩體。由於反應氣在高溫條件下接觸不鏽鋼將發生大量副反應,因此,不鏽鋼反應套管82為內襯陶瓷的不鏽鋼反應管,進料管線87和產物的出料管線溫度宜控制在200℃以下。
其中,加熱爐83正對反應套管82的中部指的是加熱爐83對應反應套管82的中部,與反應套管82上端之間的距離和下端之間的距離相同。這樣的設置有利於保持反應溫度的恆定,且加熱爐83在熱反應區810中心位置設置控溫點。
反應套管82內充滿了陶瓷蜂窩體,反應套管82內填充陶瓷蜂窩體有利於保持反應套管82內的溫度,因為陶瓷蜂窩體的熱容較大,蓄熱效果好。
優選地,反應套管82的內徑、長度和加熱爐83的長度的比例為(2-10):70:40。這裡,反應套管的內徑、反應套管的長度和加熱爐的長度的比例優選為1:14:8。
優選地,當加熱爐83對反應套管82加熱時,反應套管82內根據溫度場自上而下劃分為預熱區89、熱反應區810、蓄熱區811、催化反應區812和冷卻區813。
其中,預熱區89、熱反應區810、蓄熱區811、催化反應區812和冷卻區813均由陶瓷蜂窩體裝填而成,陶瓷蜂窩體具有較高的蓄熱能力,可以提高能量利用效率,保證氣體在熱反應區810有均勻的熱場。催化反應區812由陶瓷蜂窩體負載金屬後的整體式催化劑裝填而成,負載的金屬為鎳、鉬、鈀、釕或銠等金屬,負載量為0.1%~5%,催化反應區812不設單獨的控溫點,乙炔制芳烴反應為放熱反應,可以利用熱反應區810的氣體所帶出的餘熱,將催化劑裝填至溫度為350~600℃的區域。催化反應區812既能充分利用熱反應區810的餘熱,又能通過催化反應提高乙炔轉化率,增加輕質芳烴的收率,改善熱反應所得液相產物的質量,進一步提高輕質芳烴收率。同時採用整裝的陶瓷蜂窩體作為載體,有利於減少流動阻力,避免催化劑裝填密度過大或積炭較多造成的催化劑床層堵塞。陶瓷蜂窩體具有熱容較大,蓄熱效果好的優點。
在乙炔制芳烴反應器中,反應套管82的內徑、反應套管82的長度和加熱爐83的長度的比例確定了,並且反應溫度確定了之後,加熱爐83對反應套管82加熱時反應套管82中的溫度場就確定了。加熱爐83正對的反應套管82的中部溫度最高,中部以上或以下溫度都較低。
優選地,預熱區89、熱反應區810、蓄熱區811、催化反應區812和冷卻區813的長度比例為(20-40):(8-12):(8-12):(1-3):(18-20)。
另外,採用上述乙炔制芳烴反應器製備輕質芳烴的方法,包括:將反應氣按比例進行混合,通入進料管線87至氣體分布器86;通過氣體分布器86的混合氣體在反應套管的預熱區89由200℃以下的初始溫度升溫至熱反應區810的熱反應溫度,在熱反應區810保持恆溫發生熱反應,反應溫度為850~1100℃,優選的熱反應區810溫度為880~920℃;再經過反應套管的蓄熱區811,在蓄熱區811產物從熱反應溫度降低至催化反應溫度,到達催化反應區812,與催化劑接觸,在反應溫度為350℃-600℃條件下發生催化反應製備得到產物輕質芳烴;得到的最終產物經過反應套管的冷卻區813,在冷卻區813溫度降低至200℃以下,然後通過出料管線進入下遊裝置(未示出)中。
在上述方法中,反應氣中乙炔為主要反應氣;氫氣作為部分反應氣,同時抑制乙炔及芳烴的過分縮合,降低積炭;甲烷和一氧化碳可降低積炭的形成;二氧化碳作為稀釋氣,降低乙炔的分壓。
在上述方法中,反應進料空速為2000~6000h-1,基於此確定反應時間的長短。
如圖3所示,使用如上的系統製備輕質芳烴的方法,包括以下步驟:
1)原料壓球和熱解:將破碎後的生石灰和低階煤按混合質量比為(1:1.1)~(1:1.4)在混合器1中混合,進入壓球機2進行壓球處理,低階煤與生石灰的混合粉料進入壓球裝置3得到的球團粒徑為10~40mm,將球團的粒徑控制在合適範圍內有利於傳熱,提高熱效率。球團進入旋轉床熱解裝置進行提質,得到熱解油氣和提質後的球團,熱解油氣經過油氣分離器4後得到熱解氣和煤焦油,熱解氣進入淨化裝置5得到氫氣、甲烷和二氧化碳等;
2)生產電石:提質後的球團熱裝進入電石爐中生產電石和一氧化碳;提質球團熱裝進入電石爐6中生產電石,可有效降低電石爐的能耗,提高系統工藝的熱利用率。同時電石爐產生大量一氧化碳,一部分一氧化碳作為乙炔制芳烴的反應氣,另一部分可為系統的燃料氣,例如加熱爐的燃料氣。
3)生產乙炔:將步驟2)得到的電石冷卻破碎後在乙炔發生器7中與水反應,得到乙炔和電石渣漿;
4)回收電石渣漿中的水分:將步驟3)生產乙炔後的電石渣漿進入自然沉降器10經過自然沉降後得到上清液,上清液進入蒸發濃縮器11進行蒸發濃縮得到水蒸氣,水蒸氣通入乙炔制芳烴反應器8,用於乙炔制芳烴再生過程。
5)連續生產輕質芳烴:將步驟1)中得到的二氧化碳、氫氣和甲烷、步驟2)得到的一氧化碳和步驟3)中得到的乙炔混合進入乙炔制芳烴反應器8,生產輕質芳烴,副產物為乙烯和重質芳烴。
優選地,二氧化碳:氫氣:甲烷:一氧化碳:乙炔質量配比為:0.2-0.4:1:2-3:2-4:4-6。
優選地,方法在步驟5)生產輕質芳烴連續進行一段時間且乙炔制芳烴反應器8中產生積炭後,還包括乙炔制芳烴反應器8的再生過程:停止通入反應氣,通入步驟4)得到的水蒸氣,水蒸氣高溫下與積炭反應,去除積炭後,可繼續通入反應氣重複上述步驟5)的過程。
優選地,步驟2)得到的一氧化碳被分流閥分為兩部分,一部分通入乙炔制芳烴反應器8中用於生產輕質芳烴,另一部分用作系統的燃料氣。
優選地,步驟5)中,當加熱爐對反應套管加熱時,反應套管內,根據溫度場由上而下依次劃分為:預熱區、熱反應區、蓄熱區、催化反應區和冷卻區;在熱反應區進行熱反應,熱反應溫度為850~1100℃;在催化反應區進行催化反應,催化反應溫度為350~600℃。
優選地,步驟5)中,催化反應的催化劑為金屬催化劑,金屬催化劑負載在陶瓷蜂窩體上。
優選地,步驟1)中的低階煤指的是揮發分大於35%的低品質煤。
步驟1)中球團送入旋轉床熱解裝置3進行提質,旋轉床熱解溫度為600~800℃,熱解時間1~2h。經過熱解提質後得到提質球團和熱解油氣,熱解油氣經過冷卻等步驟分離出熱解氣和煤焦油。熱解氣經過淨化分離可得到氫氣、甲烷、二氧化碳、一氧化碳、輕質烴類等可燃組分,其中甲烷、氫氣和二氧化碳可作為步驟4)中乙炔制芳烴反應器8的原料,其餘的一氧化碳、輕質烴類等可燃氣體可為各步驟加熱爐提供熱源,實現資源的有效利用。
步驟5)的乙炔熱反應溫度為850~1100℃,優選的熱反應溫度為880~920℃。
步驟1)的生石灰和低階煤應粉碎至20μm以下;優選粒徑10μm以下。將生石灰和煤粉末混合,可有效增加反應物的接觸面積,提高反應效率,同時先壓球後熱解,可利用低階煤本身具有的粘結性,減少壓球的難度。
步驟3)中的電石粉碎至80mm以下,優選粒徑為50~80mm。
步驟3)的電石渣漿中固體含量約為12%,主要成分為氫氧化鈣,工業中一般將電石渣漿自然沉降,上清液中仍含有一定量的氫氧化鈣,不符合直接排放要求,而循環利用存在著結垢嚴重的問題,因此本方法中將上層清液蒸發濃縮,水蒸氣通入乙炔制芳烴反應器8中用於積炭再生過程,濃縮液冷卻後循環回自然沉降單元進行固液分離。
步驟4)的反應過程中乙炔在高溫下聚合反應生成芳烴;步驟5)的再生過程中,水蒸氣與高溫的積炭接觸生成一氧化碳和氫氣,並富餘一部分水蒸氣。
本發明實施例使用的粘結劑為本領域公知的粘結劑。
實施例1
如圖1-3所示,將粒徑在20μm以下的生石灰和低階煤按質量比1.1:1混合,加入適量粘結劑進行壓球,控制球團直徑為10~40mm。將球團送入旋轉床熱解裝置,旋轉床煤熱解溫度為800℃,熱解時間1h。得到的提質球團熱裝入電石爐生產電石。所生產的電石冷卻粉碎,將電石的粒徑控制在50~80mm之間,進入乙炔發生器中反應得到乙炔。
經過本系統,1000kg低階煤與1100kg生石灰可得到370kg的乙炔、83kg的氫氣、220kg的甲烷、31kg二氧化碳和420kg一氧化碳。所得的乙炔、氫氣、甲烷、二氧化碳和221kg一氧化碳均通入乙炔制芳烴反應器中進行反應。乙炔制芳烴反應器8的內徑:長度:加熱爐長度=1:14:8,混合氣在熱反應區的停留時間為0.6s,熱反應區反應溫度為900℃,催化反應區的反應溫度為450℃,在催化反應區的停留時間為0.1s。生產得到277kg輕質芳烴和42kg重質芳烴。通入水蒸氣對乙炔制芳烴反應器進行再生,再生過程中熱反應區溫度為1100℃,再生後共生成氫氣2.2kg、二氧化碳23.8kg,分離後供反應過程使用。
實施例2
如圖1-3所示,將粒徑在20μm以下的生石灰和低階煤按質量比1.4:1混合,加入適量粘結劑進行壓球,控制球團直徑為10~40mm。將球團送入旋轉床熱解裝置,旋轉床煤熱解溫度為600℃,熱解時間2h。得到的提質球團熱裝入電石爐生產電石。所生產的電石冷卻粉碎,將電石的粒徑控制在50~80mm之間,進入乙炔發生器中反應得到乙炔。
經過本系統,1000kg低階煤與1400kg生石灰可得到387kg的乙炔、73kg的氫氣、195kg的甲烷、27kg二氧化碳和435kg一氧化碳。所得的乙炔、氫氣、甲烷、二氧化碳和286kg一氧化碳均通入乙炔制芳烴反應器中進行反應。乙炔制芳烴反應器8內徑:長度:加熱爐長度=1:14:8,混合氣在熱反應區的停留時間為0.6s,熱反應區反應溫度為1100℃,催化反應區的反應溫度為600℃,在催化反應區的停留時間為0.1s。生產得到257kg輕質芳烴和91kg重質芳烴。通入水蒸氣對乙炔制芳烴反應器進行再生,再生過程中熱反應區溫度為1000℃,再生後共生成氫氣2.6kg、二氧化碳28.6kg,分離後供反應過程使用。
實施例3
如圖1-3所示,將粒徑在20μm以下的生石灰和低階煤按質量比1.1:1混合,加入適量粘結劑進行壓球,控制球團直徑為10~40mm。將球團送入旋轉床熱解裝置,旋轉床煤熱解溫度為700℃,熱解時間1.5h。得到的提質球團熱裝入電石爐生產電石。所生產的電石冷卻粉碎,將電石的粒徑控制在50~80mm之間,進入乙炔發生器中反應得到乙炔。
經過本系統,1000kg低階煤與1100kg生石灰可得到381kg的乙炔、77kg的氫氣、204kg的甲烷、29kg二氧化碳和430kg一氧化碳。所得的乙炔、氫氣、甲烷、二氧化碳和262kg一氧化碳均通入乙炔制芳烴反應器中進行反應。乙炔制芳烴反應器8內徑:長度:加熱爐長度=1:14:8,混合氣在熱反應區的停留時間為0.6s,熱反應區反應溫度為850℃,催化反應區的反應溫度為350℃,在催化反應區的停留時間為0.1s。生產得到292kg輕質芳烴和36kg重質芳烴。通入水蒸氣對乙炔制芳烴反應器進行再生,再生過程中熱反應區溫度為1100℃,再生後共生成氫氣2.2kg、二氧化碳24.2kg,分離後供反應過程使用。
以上僅為本發明的較佳實施例,並非用來限定本發明的實施範圍;如果不脫離本發明的精神和範圍,對本發明進行修改或者等同替換,均應涵蓋在本發明權利要求的保護範圍當中。