罐體用鋁合金板的製作方法
2023-10-04 23:30:29 3
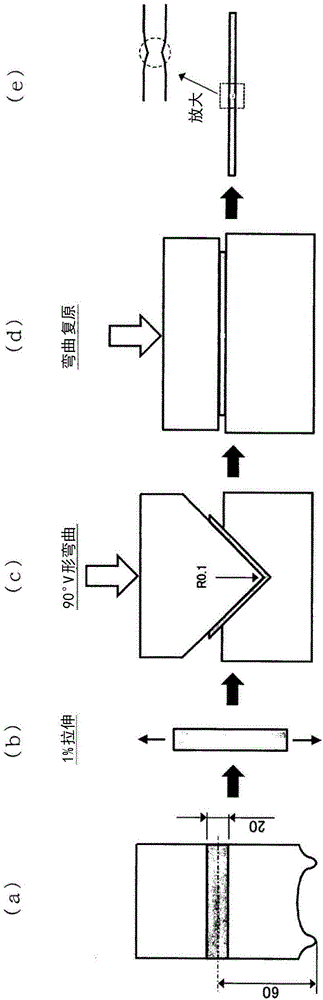
本發明涉及進行DI(draw&ironing:深衝及減薄拉深)成形而成形二片罐的罐體所使用的鋁合金板,特別是涉及在DI成形後,對罐壁實施二次加工時所適用的罐體用鋁合金板。
背景技術:
為了提高鋁罐的圖案設計性,而對於進行了DI成形的罐壁賦予壓花加工和金剛石刻磨圖案這樣的二次加工的需求增加,要求二次加工性優異的罐體用鋁合金板。另外,為了減輕環境負擔,罐體用鋁合金板的薄壁化和DI成形後的罐壁的薄壁化也在推進。
例如專利文獻1中,記述有一種在0.2%屈服強度的15%左右的應力的施加狀態下,對於罐壁進行彎曲半徑1.0mm的90°反覆彎曲時的斷裂極限周期為6個循環以上,且薄壁的、罐壁的二次加工性優異的罐體用鋁合金板。
【現有技術文獻】
【專利文獻】
【專利文獻1】特開2005-248275
對罐壁實施了壓花加工和金剛石刻磨圖案這樣的二次加工的罐,在包含內容物的填充在內的製造階段、填充後的流通階段、及交給消費者的階段等之中,因所述二次加工變形的地方從外部反覆接觸硬而尖銳的異物,該處有進一步發生塑性變形的情況。若由於所述二次加工和其後的塑性變形導致所述之處板厚局部性地減少(縮頸發生),則接著罐受到衝擊或罐壁接觸異物等之時,板厚減少之處承受過大的應力,而存在發生罐壁斷裂,內容物的洩漏的情況。
專利文獻1的評價方法談不上設想到如下實際狀態,即,由於所述二次加工和其後的塑性變形導致罐壁的板厚局部性地減少,而這裡承受過大的應力,出現罐壁斷裂的情況。於是,就要求在二次加工後,即使相當於比專利文獻1的評價方法更進一步嚴格的條件(小的彎曲半徑)的塑性變形施加於罐壁時,所述罐壁仍可均勻變形,局部的板厚減少得到抑制。
技術實現要素:
本發明基於這樣的要求而形成,因此其目的在於,提供一種罐體用鋁合金板,其DI加工和烘烤處理後的罐壁,經過二次加工及其後的塑性變形,可均勻變形,並可抑制罐壁的局部性的板厚減少。
本發明的罐體用鋁合金板,其特徵在於,含有Si:0.1~0.5質量%、Fe:0.3~0.6質量%、Cu:0.1~0.35質量%、Mn:0.5~1.2質量%、Mg:0.7~2.5質量%,餘量由Al和不可避免的雜質構成,進行200℃×20分鐘的烘烤之後的屈服強度為240~290MPa,在罐壁的加工率為60~70%的DI成形後,對於實施了200℃×20分的烘烤的罐的所述罐壁,施加1%的拉伸後,沿罐周向以彎曲半徑為0.1mm進行90°V形彎曲-彎曲復原加工時的0.2%屈服強度的增量(本發明中也稱為加工硬化能力)為10MPa以上。
上述鋁合金,根據需要,能夠還含有Cr:0.10質量%以下、Zn:0.40質量%以下、Ti:0.10質量%以下之中一種以上。
本發明的罐體用鋁合金板,在DI加工和烘烤處理後,對罐壁實施壓花加工和金剛石刻磨圖案這樣的二次加工時,顯示出優異的DI加工性和罐壁二次加工性。另外,本發明的罐體用鋁合金板其加工硬化能力高,受到了二次加工的罐壁再受到塑性變形時,罐壁會均勻地變形,局部性的板厚減少(縮頸的形成)得到抑制。因此,在罐受到衝擊或罐壁接觸異物等之時,能夠防止罐壁局部性地承受大的應力,能夠防止填充後的罐壁的斷裂,並防止洩漏的發生。
附圖說明
圖1是測量罐壁的90°V形彎曲-彎曲復原加工後的斷面板厚減少率的試驗的概念圖。
圖2A是說明罐的耐壓強度試驗的步驟的圖,是用於耐壓強度試驗的罐的側視圖。
圖2B是說明罐的耐壓強度試驗的步驟的圖,耐壓試驗機的要部側視圖。
圖2C是說明罐的耐壓強度試驗的步驟的圖,是耐壓試驗機的要部平面圖。
圖3A是說明罐的耐壓強度試驗的步驟的圖,是將罐固定在支架上時的側視圖。
圖3B是說明罐的耐壓強度試驗的步驟的圖,是罐底因內壓而壓曲時的側視圖。
具體實施方式
以下,對於本發明的罐體用鋁合金板及其製造方法,詳細地加以說明。
<鋁合金的成分組成>
(Si:0.1~0.5質量%)
Si含量低於0.1質量%時,在DI成形時0-180°制耳變高,減薄拉深時邊緣裂縫及由此引起的撕裂容易發生。另一方面,若Si含量高於0.5質量%,則熱帶卷殘存未再結晶晶粒,因此在DI成形時45°制耳變高,減薄拉深時邊緣裂縫及由此引起的撕裂容易發生。
(Fe:0.3~0.6質量%)
Fe含量低於0.3質量%時,熱帶卷殘存未再結晶,因此在DI成形時45°制耳變高,減薄拉深時邊緣裂縫及由此引起的撕裂容易發生。另一方面,若Fe含量高於0.6質量%,則Al-Fe-Mn系金屬間化合物變多,減薄拉深時容易發生撕裂。另外,在罐壁的二次加工時以所述金屬間化合物為起點的裂紋容易發生。
(Cu:0.1~0.35質量%)
Cu含量低於0.1質量%時強度不足,罐的耐壓強度不足。另一方面,若Cu含量高於0.35質量%,則強度過大,減薄拉深時容易發生撕裂。
(Mn:0.5~1.2質量%)
Mn含量低於0.5質量%時強度不足,罐的耐壓強度不足。另一方面,若Mn含量高於1.2質量%,則Al-Fe-Mn系金屬間化合物變多,減薄拉深時容易發生撕裂。另外,在罐壁的二次加工時以所述金屬間化合物為起點的裂紋容易發生。
(Mg:0.7~2.5質量%)
Mg含量低於0.7質量%時,強度不足,罐的耐壓強度不足。另外,鋁合金板的加工硬化能力不足,罐壁二次加工時容易發生縮頸。另一方面,若Mg含量高於2.5質量%,則強度過大,減薄拉深時容易發生撕裂。
(Cr:0.10質量%以下)
如果Cr為0.10質量%以下的含量,則對於鋁合金板的材料特性、DI成形後的罐特性不會造成影響。Cr是不可避免的雜質,但為了追求成本削減,例如也能夠提高原料中的廢料(大量含有Cr的廢料等)調合比等,在上述範圍內積極添加Cr。但是,若Cr含量高於0.10質量%,則熱帶卷有未再結晶殘存,在DI成形中45°制耳變高,減薄拉深時邊緣裂縫及由此引起的撕裂容易發生。因此,鋁合金中的Cr含量限制在上述範圍內。還有,通常,不可避地包含的Cr的含量為0.050質量%以下。
(Zn:0.40質量%以下)
如果Zn為0.40質量%以下的含量,則不會對鋁合金板的材料特性、DI成形後的罐特性造成影響。Zn是不可避免的雜質,但是為了追求成本削減,例如也能夠提高原料中的廢料(熱交換器用包覆材的廢料等)調合比等,在上述範圍內積極添加Zn。還有,通常,不可避免地包含的Zn的含量為0.30質量%以下。
(Ti:0.10質量%以下)
Ti是以鑄塊晶粒的微細化為目的而根據需要添加。鑄造時若使鑄塊組織微細化,則鑄造性提高,可以進行高速鑄造。這一效果能夠通過0.01質量%以上的添加而取得。另一方面,若添加Ti高於0.10質量%,則過濾器的篩眼很快堵塞,鑄造中熔液逐漸難以通過過濾器,最後不得不中止鑄造。因此,鋁合金中的Ti含量限制在上述範圍內。還有,添加Ti時,因為將Ti與B的質量比為5:1的鑄塊細化劑(Al-Ti-B),以餅或棒的形態添加到鑄造前的熔融金屬中,所以與含有比例相應的B也必然被添加。還有,通常,不可避免包含的Ti的含量為0.050質量%以下。
(其他的不可避免的雜質)
關於上述元素以外的不可避免的雜質(V、Na、Zr、Ni、Ca等),分別為0.10%以下,優選為0.05%以下,且合計0.30%以下,優選為0.15%,即使含有,也不妨礙本發明的效果。還有,關於這些元素,如果不超過所述含量,則不僅作為不可避免的雜質含有時,即使有意識地提高含有這些元素的廢料的調合比等,即積極地添加時,也不會妨礙本發明的效果。
<鋁合金板的特性>
(烘烤後的屈服強度:240~290MPa)
200℃×20分鐘的烘烤後的鋁合金板的屈服強度低於240MPa時,強度不足,DI成形和烘烤後的罐的耐壓強度不足。另一方面,若烘烤後的鋁合金板的屈服強度高於290MPa,則強度過大,減薄拉深時撕裂多發,使生產率降低。還有,烘烤後的強度與烘烤前的強度聯動,烘烤後的強度大的鋁合金板,烘烤前(減薄拉深時)的強度也大。
(加工硬化能力:10MPa以上)
在本發明中,對於罐壁的加工率為60~70%的DI成形後,又實施了200℃×20分鐘的烘烤的罐的罐壁,再施加1%(永久應變)的拉伸後,沿罐周向以彎曲半徑為0.1mm進行90°V形彎曲-彎曲復原加工,將這時的0.2%屈服強度的增量定義為加工硬化能力。還有,DI成形的加工率60~70%,是在罐的DI成形中標準的加工率。
設所述DI成形和烘烤後的罐壁的0.2%屈服強度為σ1,所述拉伸和V形彎曲-彎曲復原加工後的罐壁的0.2%屈服強度為σ2時,加工硬化能力以σ2-σ1表示。如果該加工硬化能力(σ2-σ1)為10MPa以上,則罐壁在二次加工和其後的塑性變形中均勻變形,可抑制罐壁的局部性的板厚減少。另一方面,加工硬化能力低於10MPa時,罐壁在二次加工及其後的塑性變形中難以均勻變形,罐壁發生局部性的板厚減少而容易發生縮頸。因此,罐受到衝擊或罐壁接觸異物等之時,薄壁化的地方承受過大的應力,而容易發生罐壁斷裂,內容物洩漏。
<鋁合金板的製造方法>
本發明的鋁合金板,能夠以鑄造、均質化熱處理、熱軋及冷軋的各工序製造。不進行熱軋後的中間退火及冷軋後的最終退火。而且,本發明的鋁合金板的製造方法,其特徵在於,特別是以規定的條件進行冷軋。
以下,對於各工序進行說明。
首先,也可以通過DC(Direct-Chill,直冷)鑄造法等的公知的半連續鑄造法鑄造鋁合金。
其次,以端面切削除去鑄塊表層的作為不均勻的組織的區域後,基於常規方法實施均質化熱處理。這時也可以採用二段均質化熱處理或2次均質化熱處理。在此所謂二段均質化熱處理,意思是將鑄塊在高溫下保持規定時間(第一段的均質化熱處理)之後,不冷卻至室溫,而是在高於200℃的溫度下停止冷卻,在此溫度下保持規定時間(第二段均質化熱處理)。另外,所謂二次均質化熱處理,意思是將鑄塊在高溫下保持規定時間(第一次均質化熱處理)後,先冷卻至包含室溫在內的200℃以下的溫度,再加熱而在規定的均質化處理溫度中保持規定時間(第二次均質化熱處理)。
均質化熱處理後,不要將鑄塊的溫度冷卻至低於450℃而連續進行熱軋,優選在300℃以上結束熱軋。進行所述二段均質化熱處理時,第二均質化熱處理後,根據需要加熱至更高溫之後,進行熱軋。所製作的熱軋材為再結晶組織。
接著冷軋以連軋機。以連軋機進行冷軋,能夠加大1次通板中的軋制率。由此,加工放熱變大,冷軋材的動態的恢復和卷取後的恢復得到促進。其結果是,在對於冷軋材(本發明的鋁合金板)進行DI成形和烘烤的罐中,罐壁的加工硬化能力提高。
冷軋的總軋制率為80~90%。該軋制率由連軋機的1次通板達成。冷軋的總軋制率低於80%時,鋁合金板的強度不足,DI成形和烘烤後的罐的耐壓強度不足。另一方面,若總軋制率高於90%,則強度過大,且招致45°制耳的增加,減薄拉深時邊緣裂縫發生及由此引起的撕裂容易發生。
冷軋後的卷取溫度在120~180℃的範圍內。使卷取溫度在所述溫度範圍內,會促進鋁合金板(冷軋材)的動態恢復及卷取後的恢復,成為最終的罐時的罐壁的加工硬化能力提高。
卷取溫度低於120℃時,恢復的效果不充分,罐壁的加工硬化能力不足,在二次加工及其後的塑性變形中難以均勻變形,罐壁會局部性地發生板厚減少而容易產生縮頸。卷取溫度的下限優選為150℃。
若卷取溫度高於180℃,則加工放熱造成的鋁合金板的軟化變大,軋制中容易發生碎板片。其結果是,鋁合金板的生產率大幅降低,因此實用上不為優選。
卷取後的卷材,在120℃以上的溫度保持4小時以上。由此鋁合金板(冷軋材)的恢復得到促進,在DI成形和烘烤後的罐中,罐壁的加工硬化能力提高。另一方面,120℃以上的溫度下的保持時間低於4小時時,鋁合金板(冷軋材)的恢復不充分,無助於罐壁的加工硬化能力的提高。
【實施例】
以下,將確認到本發明的效果的實施例,與不滿足本發明的要件的比較例加以對比而具體地進行說明。還有,本發明不受該實施例限定。
熔煉表1、2所示的組成的鋁合金,使用半連續鑄造法製作厚度600mm的鑄塊(比較例的No.12除外)。對於該鑄塊的表層進行端面切削,並實施均質化熱處理後,接著進行熱軋。其後不實施中間退火,而對於熱軋材進行冷軋(連軋機或單架軋機),作為板厚0.30mm的鋁合金板,並進行卷取。不進行冷軋後的最終退火(比較例的No.20除外)。還有,比較例的No.12,因為過濾器的篩眼堵塞,所以不能進行鑄造。
表1、2中記述冷軋所用的軋機的種類、冷軋的總軋制率、冷軋後的卷取溫度、在120℃以上保持卷取後的卷材的時間、冷軋後有無最終退火的和條件。
(表1)
(表2)
將所製造的實施例No.1~19和比較例No.1~11、13~20的鋁合金板作為供試材,按以下所示的要領測量烘烤後屈服強度。
接著,使用實施例No.1~19和比較例No.1~11、13~20的鋁合金板,製作DI罐。作為製作方法,首先由鋁合金板衝孔直徑140mm的坯體,對該坯體進行深衝成形而製作直徑90mm的杯體。對於所得到的杯體,以通用的鋁罐體成形機(由再深衝、第一次減薄拉深、第二次減薄拉深、第三次減薄拉深的4個階段構成)實施DI成形,作為DI罐。還有,第三次減薄拉深率為40%。該減薄拉深率,與一般的減薄拉深率、即35~38%左右相比是更嚴格的條件。
製作的罐(修整開口部之後)的側視圖顯示在圖1的(a)中。罐的外徑為66.3mm,高度124mm,罐壁的最薄壁部(至罐底60mm的高度)壁厚為95μm,同部位的加工率68.3%(最初板厚:0.3mm)。
由所述鋁罐體成型機,對於各實施例和比較例共10000個罐進行連續成形,按以下所示要領進行減薄拉深性的評價。接著,使用該成形的罐,按以下所示的要領,測量罐壁的加工硬化能力、罐壁的90°V形彎曲-彎曲復原加工後的斷面板厚減少率、和耐壓強度。以上的結果顯示在表3中。
*脫離本發明的規定之處或特性差的地方
(鋁合金板的烘烤後屈服強度)
對於供試材(鋁合金板)實施200℃×20分鐘的烘烤後,沿軋制平行方向提取JIS5號試驗片,依據JIS Z 2241(2011年改定版)的規定進行拉伸試驗,測量0.2%屈服強度。該0.2%屈服強度在240~290MPa的範圍內時,評價為合格。
(減薄拉深性)
連續成形的10000個罐之中,發生撕裂等缺陷的罐在3個罐以下的評價為合格(○),4個罐以上的評價為不合格(×)。
(罐壁的加工硬化能力)
對於製作的罐實施200℃×20分鐘的烘烤之後,使距罐底的高度60mm的高度為寬度方向的中心,軋制0°方向為長度方向的中心,如此沿著罐的圓周方向提取JIS13號B試驗片(第一試驗片)。
另外,對於製作的罐實施200℃×20分鐘的烘烤後,使距罐底的高度60mm的高度為寬度方向的中心,軋制0°方向為長度方向的中心,如此沿著罐的圓周方向切下寬20mm×長100mm的短棒狀試驗片(參照圖1的(a))。對此短棒狀試驗片,以拉伸試驗機施加1%的拉伸後(參照圖1的(b)),使用前端的彎曲半徑R為0.1mm的夾具,實施90°V形彎曲加工(參照圖1的(c)),接著,在相反方向上實施彎曲復原加工(參照圖1的(d))。從該短棒狀試驗片上提取JIS13號B試驗片(第二試驗片)。使V形彎曲-彎曲復原加工部位於該JIS13號B試驗片的長度方向中央。
還有,所述第一試驗片和第二試驗片,在如下方面有所不同,即,前者不會受到1%的拉伸和V形彎曲-彎曲復原加工,後者會受到這些加工。
接著,對於所述第一、第二試驗片,依據JIS Z 2241(2011年改定版)的規定實施拉伸試驗,求得各自的0.2%屈服強度。第二試驗片的最初板厚視為與第一試驗片相同的95μm。設第一試驗片的0.2%屈服強度為σ1,第二試驗片的0.2%屈服強度為σ2時,兩者的差(σ2-σ1),即拉伸與V形彎曲-彎曲復原加工後的0.2%屈服強度的增量,定義為罐壁的加工硬化能力。加工硬化能力(σ2-σ1)為10MPa以上的評價為合格。如前述,若罐壁的加工硬化能力高,則罐壁在二次加工及其後的塑性變形時均勻變形,罐壁的局部性的板厚減少(縮頸的形成)得到抑制,罐受到衝擊或罐壁接觸異物等之時,能夠防止罐壁局部性地承受大的應力。
還有,在此測量試驗中進行的予以1%的永久應變的拉伸,模擬的是對罐壁實施的二次加工(壓花加工和金剛石刻磨圖案的加工)。但是,1%的永久應變,比實際的金剛石刻磨圖案的加工所施加於罐壁的永久應變大,該拉伸與實際的壓花加工和金剛石刻磨圖案的加工相比,可以說是相當嚴酷的加工。另外,V形彎曲-彎曲復原加工,模擬的是在包含內容物的填充在內的製造階段、填充後的流通階段、和交給消費者的階段等之中,偶然性地施加於罐上的塑性變形。該V形彎曲-彎曲復原加工,在彎曲半徑為0.1mm這樣極小的這一點上,可以說比專利文獻1的評價方法(彎曲半徑為1mm)在條件上更嚴格。
(罐壁的90°V形彎曲-彎曲復原加工後的斷面板厚減少率)
對於製作的罐,實施200℃×20分鐘的烘烤後,使距罐底的高度60mm的高度作為寬度方向的中心,軋制0°方向作為長度方向的中心,如此沿罐的圓周方向切下寬20mm×長100mm的短棒狀試驗片(參照圖1的(a))。對於該短棒狀試驗片,以拉伸試驗機施加1%(公稱應變)的拉伸後(參照圖1的(b)),使用前端的彎曲半徑R為0.1mm的夾具,實施90°V形彎曲加工(參照圖1的(c)),接著,朝相反方向實施彎曲復原加工(參照圖1的(d))。將所得到的試驗片埋入樹脂,製作斷面觀察用試料(參照圖1的(e)),觀察試驗片的寬度方向中央部的彎曲-彎曲復原加工部(圖1的(e)中由虛線包圍的部分)的斷面,測量相對於原本的板厚(95μm)的板厚減少率。斷面板厚減少率為5%以下時評價為合格。
(罐的耐壓強度)
使用水壓式的耐壓試驗機(エーステック株式會社制的水壓式加減壓壓曲試驗裝置,型號名WBT-500),在實施了烘烤的罐中負荷內壓,求得罐底壓曲時的最大內壓作為耐壓強度。
如圖2A~C所示,耐壓試驗機具備如下:設置在機臺1上的底板2;設置在底板2之上的圓筒狀的支架3;配置在支架3的兩側的一對固定構件4、4。支架2的高度方向中間位置設置有O-環5。支架2的內部設置有橡皮管6,該橡皮管6通過底板2向下延伸,與通水管路連接,經由水壓計和切換閥等與水力泵連通(均未圖示)。在底板2上形成有孔7,該孔7與通氣管路連接,經由切換閥等與真空泵連通(均未圖示)。固定構件4、4分別藉助未圖示的液壓缸進退。
耐壓試驗以如下方式進行。
(1)如圖2A~C所示,將開口部經修整而高度為100mm的罐8,罐底朝上嵌在支架3上後,使固定構件4、4前進規定的衝程。若固定構件4、4到達規定位置(參照圖3A),則固定構件4、4的前端在O-環5的稍下的位置從兩側按壓罐8的罐壁,將罐8固定在支架3上。由此,罐8的罐壁內面緊貼在O-環5的周圍,除了橡皮管6和孔7的位置,支架3內(罐8內)被密封。
(2)使所述真空泵工作,通過孔7而使支架3內(罐8內)脫氣至9.8kPa(0.1kgf/cm2)以下,接著關閉所述通氣管路。
(3)使所述水力泵工作,從橡皮管6向支架3內(罐8內)供給水。支架3內(罐8內)的水壓(以所述水壓計計量),與從供給開始起的經過時間大體成比例上升,在罐底的壓曲發生的瞬間降低。罐底的壓曲發生時的最大內壓,作為罐的耐壓強度。罐底的壓曲發生時的狀態顯示在圖3B中。
此耐壓強度為618kPa以上(6.3kgf/cm2以上)時評價為合格。
如表1、3所示,鋁合金板的成分組成、烘烤後的鋁合金板的屈服強度、和罐壁的加工硬化能力在本發明的規定範圍內的實施例No.1~19,減薄拉深性優異,拉伸和V形彎曲-彎曲復原加工後的罐壁的斷面板厚減少率小,耐壓強度大。所謂所述斷面減少率小,是指罐壁不會局部性地發生板厚減少(縮頸的發生得到抑制),意味著拉伸和V形彎曲-彎曲復原加工中罐壁均勻變形。實施例No.1~19均在前述的條件的範圍內進行冷軋。
另一方面,如表2、3所示,鋁合金板的成分組成、烘烤後的鋁合金板的屈服強度、和罐壁的加工硬化能力的任意一個在本發明的規定範圍外的比較例No.1~11、13~20,減薄拉深性、罐壁的斷面板厚減少率、耐壓強度的任意一個不滿足本發明的標準。
比較例No.1、2因為Si含量在本發明的規定範圍外,所以減薄拉深性差。比較例No.3、4因為Fe含量在本發明的規定範圍外,所以減薄拉深性差。比較例No.5、7、9因為Cu、Mn、Mg含量分別不足,所以烘烤後的鋁合金板的屈服強度不足,罐的耐壓強度差。比較例No.6、10因為Cu、Mg含量分別過剩,所以烘烤後的鋁合金板的屈服強度過大,減薄拉深性差。比較例No.8、11因為Mn、Cr含量分別過剩,所以減薄拉深性差。還有,No.12因為Ti含量過剩,所以如前述,不能進行鑄造。
比較例No.13因為冷軋的總軋制率不足,所以烘烤後的鋁合金板的屈服強度不足,耐壓強度差。比較例No.14因為總軋制率過大,所以鋁合金板的屈服強度過大,減薄拉深性差。比較例No.15其卷取溫度低,動態恢復和卷取後的恢復不充分,從而罐壁的加工硬化能力低,罐壁的斷面板厚減少率大。
比較例No.16,其卷取後的卷材的120℃以上的溫度下的保持時間不足,卷取後的恢復不充分,罐壁的加工硬化能力無法提高,罐壁的斷面板厚減少率大。比較例No.17、19因為以單架軋機實施冷軋,所以卷取溫度低,動態恢復和卷取後的恢復不充分,鋁合金板的屈服強度過大,減薄拉深性差。另外,比較例No.17、19,罐壁的加工硬化能力低,罐壁的斷面板厚減少率大。還有,比較例No.17的合金組成,以專利文獻1的實施例的合金e5的組成為基礎。No.18因為以單架軋機實施冷軋,所以卷取溫度低,動態恢復和卷取後的恢復不充分,罐壁的加工硬化能力低,罐壁的斷面板厚減少率大。No.20因為單架軋機實施冷軋,所以卷取溫度低,動態恢復和卷取後的恢復不充分,最終退火的效果也少,罐壁的加工硬化能力低,罐壁的斷面板厚減少率大。
本電請伴隨以申請日為2014年9月10日的日本國專利申請,專利申請第2014-184681號為基礎申請的優先權主長,專利申請第2014-184681號由於參照而編入本說明書。