一種活塞環壓裝裝置的製作方法
2023-10-20 06:35:07 2
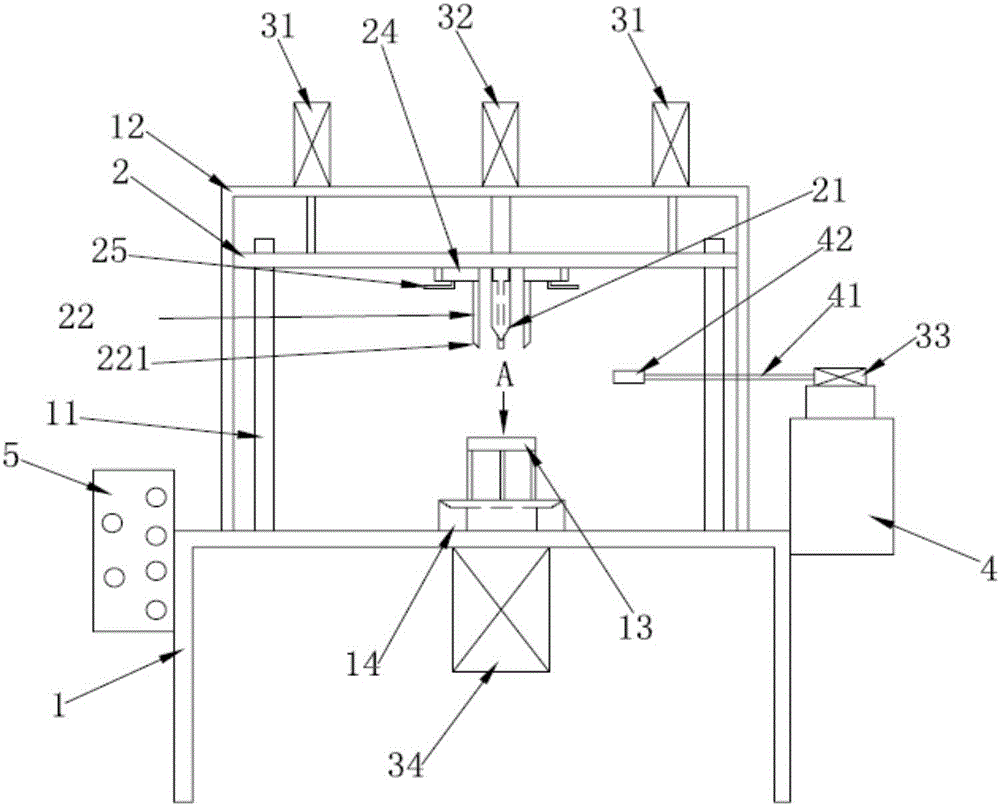
本實用新型涉及夾具製造技術領域,特別涉及一種活塞環壓裝裝置。
背景技術:
活塞環是一種具有較大向外擴張變形的金屬彈性環,它被裝配到剖面與其相應的活塞的環形槽內。目前,不管是汽油機還是柴油機在活塞環的裝配上多採用手動裝配方式,這種的裝配方式一是使得工人的勞動強度較大,二是在裝配時,手動擴開活塞環,活塞環開口處向上翹,容易劃傷活塞,導致活塞損壞。於是,有些廠家就採用專用的機器對活塞環進行安裝,但是體積太大,佔地寬,並且這樣的專用設備在維修時也很複雜。
技術實現要素:
本實用新型要解決的技術問題是提供了一種拆裝便捷、裝配效率高的活塞環壓裝裝置。
本實用新型的技術方案如下:
一種活塞環壓裝裝置,包括底座和控制臺,在所述底座上設有支架,在所述支架上對稱設有兩個第一氣缸,兩個所述第一氣缸之間設有一個第二氣缸,在所述底座的左、右兩端對稱設有導向杆,該底座的上方設有壓板,所述壓板上端面的左、右兩端與對應端第一氣缸的輸出端連接,該壓板左、右兩端還套設在對應位置的導向杆上;
在所述壓板的中部設有導向軸,所述導向軸的上端與第二氣缸連接,沿所述導向軸為中心的圓周方向上還設有三個漲形杆,三個所述漲形杆均活動連接在壓板上;在所述底座的一側還設有升降臺,所述升降臺上設有連接杆,所述連接杆的一端連接有第三氣缸,該連接杆的另一端設有擋塊;
在所述底座上設有第一置物槽,所述第一置物槽的中部還設有載物臺,三個所述漲形杆均穿設過載物臺,該載物臺的下端連接有第四氣缸,所述升降臺以及四個氣缸均與控制臺連接。
採用以上結構,根據不同規格活塞環的內徑尺寸,選用對應規格尺寸的導向軸,以導向軸的中心位置為準,使三個漲形杆都靠緊抵接在導向軸的外側壁上,然後把三個漲形杆的位置固定,利用第二氣缸收回導向軸;接著,把活塞環放上置物臺,兩個第一氣缸推送壓板向下移動,三個漲形杆也隨之向下移動,並從活塞環的內側穿設而過,直到活塞環被三個漲形杆完全地漲開,第四氣缸向下收回置物臺,然後,在底座的第一置物槽上放入對應規格的待裝件,三個漲形杆再向下移動,把活塞環挪到裝配位置的水平面,升降臺調整高度,第三氣缸水平朝漲形杆方向推動連接杆,並使連接杆上的推塊抵接對應位置的漲形杆外側壁,同時,再調整升降臺的高度,使推塊的下端面與活塞環的上端面抵接,最後,第一氣缸的輸出端帶動壓板向上移動,漲形杆向上移動,並從活塞環的內側抽出,活塞環在推塊的抵接作用下,不會向上移動,而保持在裝配位置,待漲形杆完全抽離,活塞環的內徑回縮,套入裝配位置對應的環槽,第三氣缸收回連接杆,取出已裝件即完成一次裝配,然後,再向上伸出置物臺,放入活塞環,重複上述步驟即可有序完成活塞環的裝配。
漲形杆活動連接在壓板上,適用於多種規格的活塞環裝配,對應的,除了兩個第一氣缸是純移動功能外,其餘三個氣缸輸出端連接的部件都是要根據裝配需要進行調整更換的,因此,這些部件之間的結構是可拆式的,拆裝便捷,維護成本低,由此也提高了裝配效果的準確度,適用範圍廣。
為了便於控制漲形杆的移動位置,同時,防止漲形杆在裝配位置掉落,作為優選,在所述壓板上對應漲形杆的位置處均設有託板,每根所述漲形杆均連接固定在對應位置的託板上,每個該託板上均設有一段「⊥」形凸塊,在壓板對應所述託板的位置均設有滑槽,每個所述滑槽的截面形狀為「⊥」形,每個所述託板上的「⊥」形凸塊均與對應位置的滑槽滑動連接。
為了更有利於漲形杆的位置調整,也為了便於給移動後的漲形杆定位,作為優選,在每個所述託板上均螺接有鎖緊把手,每個所述鎖緊把手的螺接端上連接有鎖止栓,所述鎖止栓穿設過託板的對應位置,並伸入滑槽內。
為了便於穿設入活塞環的內側壁,漲開活塞環,作為優選,三個所述漲形杆的下端均設有一段上寬下窄的斜面,三個該斜面均背嚮導向軸。
為了使活塞環平穩移出,防止單邊受力造成裝配不到位,作為優選,所述擋塊為半圓形,該擋塊與連接杆螺接連接。
為了便於擺放活塞環,同時也為了便於漲形杆漲開活塞環,作為優選,所述載物臺上設有置物槽,所述置物槽內對應三個漲形杆的位置均設有一個通孔,相鄰兩個所述通孔之間的置物槽槽壁上均嵌設有彈性壓力傳感器,每個所述彈性壓力傳感器均與控制臺連接。
為了便於定位放置多種規格的待裝件,作為優選,所述第一置物槽為多臺階結構。
有益效果:本實用新型利用控制臺來操作四個氣缸,實現漲形、移動、定位和裝配等步驟,準確高效地完成裝配操作,同時,各個部件之間的可拆式連接使得拆裝方便,維護成本降低,應用範圍廣。
附圖說明
圖1為本實用新型的結構示意圖。
圖2為圖1的A向視圖。
圖3為壓板、推板和漲形杆的結構示意圖。
圖4為圖3的B-B向剖視圖。
圖5為擋塊的結構示意圖。
具體實施方式
下面結合附圖對本實用新型作進一步說明。
由圖1和圖2所示,本實用新型由底座1和控制臺5等組成,在所述底座1上設有支架12,在所述支架12上對稱設有兩個第一氣缸31,兩個所述第一氣缸31之間設有一個第二氣缸32,在所述底座1的左、右兩端對稱設有導向杆11,該底座1的上方設有壓板2,所述壓板2上端面的左、右兩端與對應端第一氣缸31的輸出端連接,該壓板2左、右兩端還套設在對應位置的導向杆11上。在所述底座1上設有第一置物槽14,所述第一置物槽14為多臺階結構,該第一置物槽14的中部還設有載物臺13,三個所述漲形杆22均穿設過載物臺13,該載物臺13的下端連接有第四氣缸34;所述載物臺13上設有第二置物槽15,所述第二置物槽15內對應三個漲形杆22的位置均設有一個通孔151,相鄰兩個所述通孔151之間的第二置物槽15槽壁上均嵌設有彈性壓力傳感器6,所述彈性壓力傳感器6、升降臺4以及四個氣缸均與控制臺5連接。
由圖1、圖3和圖4所示,在所述壓板2的中部設有導向軸21,所述導向軸21的上端與第二氣缸32連接,沿所述導向軸21為中心的圓周方向上還設有三個漲形杆22,三個所述漲形杆22的下端均設有一段上寬下窄的斜面221,三個該斜面221均背嚮導向軸21;在所述壓板2上對應漲形杆22的位置處均設有託板24,每根所述漲形杆22均連接固定在對應位置的託板24上,每個該託板24上均設有一段「⊥」形凸塊,在壓板2對應所述託板24的位置均設有滑槽23,每個所述滑槽23的截面形狀為「⊥」形,每個所述託板24上的「⊥」形凸塊均與對應位置的滑槽23滑動連接;在每個所述託板24上均螺接有鎖緊把手25,每個所述鎖緊把手25的螺接端上連接有鎖止栓26,所述鎖止栓26穿設過託板24的對應位置,並伸入滑槽23內。
由圖1和圖5所示,在所述底座1的一側還設有升降臺4,所述升降臺4上設有連接杆41,所述連接杆41的一端連接有第三氣缸33,該連接杆41的另一端螺接連接有擋塊42,所述擋塊42為半圓形。
本實用新型的使用方法如下:
如圖1到圖5所示,根據不同規格活塞環的內徑尺寸,選用對應規格尺寸的導向軸21,以導向軸21的中心位置為準,使三個漲形杆22都在「⊥」凸塊的引導下,沿著「⊥」形的滑槽23移動,並靠緊抵接在導向軸21的外側壁上,然後,鉚緊鎖緊把手25,使鎖止栓26抵緊對應位置滑槽23的槽底,把三個漲形杆22的位置固定,利用第二氣缸32收回導向軸21。
接著,把活塞環(圖2中內圈虛線標示)放上載物臺13的第二置物槽15內,開啟控制臺5,兩個第一氣缸31推送壓板2向下移動,三個漲形杆22也隨之向下移動,漲形杆22下端的斜面伸入到通孔151並切入到活塞環的內側壁,並沿著漲形杆22上的斜面從活塞環的內側穿設而過,直到活塞環被三個漲形杆22完全地漲開,此時,漲開後的活塞環抵接到第二置物槽15的槽壁,即牴觸到彈性壓力傳感器6,當漲形杆22的斜面段完全穿設過活塞環的內側時,活塞環漲形到位並卡套在漲形杆22的外側圓周壁上,且彈性壓力傳感器6受牴觸彈性變形,受力值經控制臺5轉換數據指令,操作第四氣缸34向下收回載物臺13,使載物臺13的上端面與第一置物槽14中最低端的臺階面齊平,然後,在底座1的第一置物槽14上放入對應規格的待裝件,由於第一置物槽14內為多臺階結構,對中以及限位的誤差小,準確度高,待裝件裝配位置的中心與三個漲形杆22包圍所形成範圍的中心在同一直線上,即與導向軸21的中心也相重合,三個漲形杆22再向下移動,把活塞環挪到裝配位置的水平面。
升降臺4調整高度,第三氣缸33水平朝漲形杆22方向推動連接杆41,並使連接杆41上的擋塊42抵接對應位置的漲形杆22外側壁,同時,再調整升降臺4的高度,使擋塊42的下端面與活塞環的上端面抵接,最後,第一氣缸31的輸出端帶動壓板2向上移動,漲形杆22向上移動,並從活塞環的內側抽出,活塞環在擋塊42的抵接作用下,不會向上移動,而保持在裝配位置,待漲形杆22完全抽離,活塞環的內徑回縮,套入裝配位置對應的環槽,第三氣缸33收回連接杆41,取出已裝件即完成一次裝配,然後,再向上伸出載物臺13,放入活塞環,重複上述步驟即可有序完成活塞環的裝配。
導向軸21會根據產品規格進行調換,第二置物槽15內的通孔151的位置始終與對應位置的漲形杆22適配,漲形杆22活動連接在壓板2上,適用於多種規格的活塞環裝配,對應的,除了兩個第一氣缸31是純移動功能外,其餘三個氣缸輸出端連接的部件都是要根據裝配需要進行調整更換的,因此,這些部件之間的結構是可拆式的,拆裝便捷,維護成本低,由此也提高了裝配效果的準確度,適用範圍廣。
本實用新型未描述部分與現有技術一致,在此不作贅述。
以上僅為本實用新型的實施方式,並非因此限制本實用新型的專利範圍,凡是利用本實用新型說明書及附圖內容所作的等效結構,直接或間接運用在其他相關的技術領域,均同理在本實用新型的專利保護範圍之內。