一種電解鋁陰極炭塊磷鐵澆鑄鑄前加熱爐的製作方法
2024-02-12 01:45:15
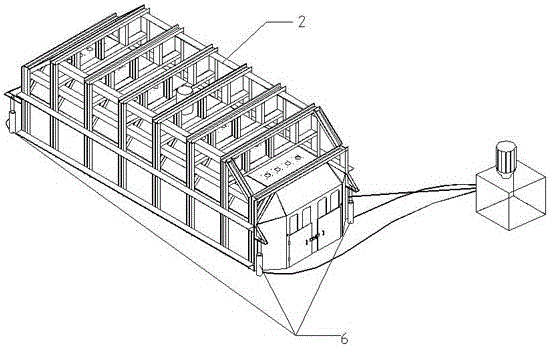
本新型涉及一種電解鋁陰極炭塊磷鐵澆鑄鑄前加熱爐,屬於電解鋁設備技術領域。
背景技術:
研究表明,通過改變電解槽結構、陰極、陽極組裝方式和完善電解控制工藝,是實現大幅降低鋁電解電能消耗的主要途徑。近些年來這些方式和工藝正在逐步得到改進和完善,但陰極炭塊使用磷鐵澆鑄的組裝方式卻沒有在行業內得到有效的推廣,現在大部分鋁廠都還沿用老式的炭糊搗固工藝進行陰極組裝,搗糊工藝雖然方便易操作,但糊料本身電阻率較高。電解槽運行後爐底壓降達到300MV左右。大量電能在此損失。用磷鐵澆鑄的方式雖然節能效果要大大優於搗糊方式,但是由於炭塊和鋼棒在澆鑄過程中的升溫速率及膨脹係數不同,如果不將兩者提前加熱到一定溫度再進行澆鑄,勢必會由於受熱不均產生的應力導致炭塊破裂報廢的情況。
陰極炭塊磷鐵澆鑄技術的鑄前加熱,目前主要有挪威炭塊—鋼棒一體加熱設備和法國炭塊---鋼棒分體加熱設備兩種。這兩種設備針對全石墨化陰極炭塊採用電加熱的方式進行鑄前加熱,效果良好。但全石墨化陰極炭塊造價昂貴,會大大增加電解鋁廠的投資成本,國內鋁廠很少使用。針對使用較多的50%石墨化陰極炭塊和30%石墨化陰極炭塊,由於其導熱性能和膨脹係數不如全石墨化優異,使用以上兩種鑄前加熱技術及設備成品率僅為60%左右,因此需要一種能適應國內情況,防止炭塊破裂成功率高的澆鑄前預熱設備。
新型內容
為了克服上述缺陷,本新型提供一種電解鋁陰極炭塊磷鐵澆鑄鑄前加熱爐。
為了實現上述目的,本新型的技術方案是:一種電解鋁陰極炭塊磷鐵澆鑄鑄前加熱爐,包括升降式加熱窯和陰極炭塊託車,所述加熱窯包括加熱罩和設置在加熱罩下方的底板,所述加熱罩頂部沿炭塊方向設有若干列燃氣噴嘴,所述燃氣噴嘴朝向對應列的陰極炭塊託車所載的鋼棒上表面;所述加熱罩前端和後端兩側架體上分別設有託板,所述託板位於同一水平面上,所述託板與底板之間設有液壓缸,所述液壓缸活塞端頭與託板固定連接,液壓缸底座與底板固定連接;所述底板上設有兩道沿通道方向的道軌,所述陰極炭塊託車沿道軌運行;所述道軌在加熱罩後端向外延伸至少一個陰極炭塊託車車位的長度,位於此位置的兩個道軌外端之間設有固定梁,所述固定梁中心固定有水平方向且與道軌平行的推桿,所述陰極炭塊託車底部設有與推桿另一端位置對應的推動塊。
進一步,作為一種優選,所述的燃氣噴嘴均設有配風組件。
本新型的有益效果是:1、體積小、佔地少,使用靈活;2、液壓系統控制加熱罩升降和託車運動,節省人工,方便連續加工;3、燃氣噴嘴設置於加熱罩頂部且朝向鋼棒上表面,可以通過鋼棒和環境溫度給炭塊傳導熱量,加熱均勻,防止炭塊破裂。
附圖說明
圖1為本新型的立體圖。
圖2為本新型的結構示意圖。
圖3為本新型的俯視圖。
具體實施方式
下面結合具體實施例對本新型做進一步的說明。
如圖1圖2圖3所示的一種電解鋁陰極炭塊磷鐵澆鑄鑄前加熱爐,包括升降式加熱窯和陰極炭塊託車1,所述加熱窯包括加熱罩2和設置在加熱罩2下方的底板3,所述加熱罩2頂部沿炭塊方向設有若干列燃氣噴嘴4,所述燃氣噴嘴4朝向對應列的陰極炭塊託車1所載的鋼棒8上表面;所述加熱罩2前端和後端兩側架體上分別設有託板5,所述託板5位於同一水平面上,所述託板5與底板3之間設有液壓缸6,所述液壓缸6活塞端頭與託板5固定連接,液壓缸6底座與底板3固定連接;所述底板3上設有兩道沿通道方向的道軌7,所述陰極炭塊託車1沿道軌7運行;所述道軌7在加熱罩2後端向外延伸至少一個陰極炭塊託車1車位的長度,位於此位置的兩個道軌7外端之間設有固定梁9,所述固定梁9中心固定有水平方向且與道軌7平行的推桿10,所述陰極炭塊託車1底部設有與推桿10另一端位置對應的推動塊11。
為了使燃氣燃燒充分,燃氣噴嘴4均設有配風組件12。
實際使用時,通過液壓缸6使加熱罩2升起,之後通過推桿10將陰極炭塊託車1推入加熱罩2內,降下加熱罩2,通過燃氣噴嘴4對加熱鋼棒8上表面,可以通過鋼棒8和環境溫度給炭塊13傳導熱量,加熱均勻,防止炭塊13破裂。加熱結束後,加熱罩2升起,推桿10將陰極炭塊託車1推出,並推進帶加熱工件,可實現連續加工。
本新型的技術方案不限於上述具體實施例的限制,凡是根據本新型的技術方案做出的技術變形,均落入本新型的保護範圍之內。