一種用於發動機的油軌鍛件的加工方法與流程
2024-03-29 11:54:05 2
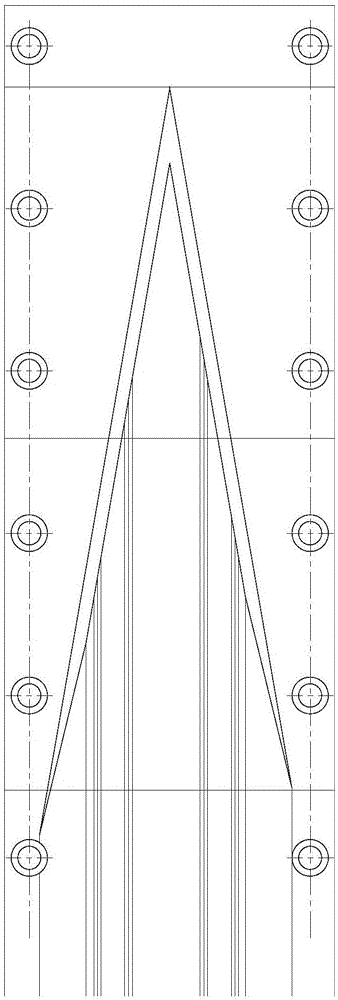
本發明涉及發動機配件加工技術領域,尤其涉及一種用於發動機的油軌鍛件的加工方法。
背景技術:
油軌作為發動機導油系統的核心部件,其加工方法、材料構成等越來越多地受到人們的關注。目前,主要的加工方法為熱鍛和雷射焊接,利用熱鍛進行油軌的生產時,需要預留比較多的坯料,並且加工時間比較長,這樣造成了材料的浪費,生產效率低下,成品率低;而雷射焊接需要採用比較先進的製造設備,增加了生產成本,因此,需要對目前的加工方法做相應的改進,以滿足市場的需求。
技術實現要素:
本發明提供了一種用於發動機的油軌鍛件的加工方法,解決現有的加工技術中材料浪費、加工效率低、成品率低的問題。
本發明可通過以下技術方案實現:
一種用於發動機的油軌鍛件的加工方法,包括以下步驟:
Ⅰ)利用切料設備截取所需要的坯料;
Ⅱ)將所述坯料進行加熱,使其表面溫度達到熱鍛溫度;
Ⅲ)將達到熱鍛溫度的坯料進行楔橫軋工序,將所述坯料加工成油軌鍛件的雛形;
Ⅳ)將所述油軌鍛件的雛形進行熱鍛加工,使其達到所述油軌鍛件的鍛壓尺寸,成為半成品;
Ⅴ)熱鍛後,將符合鍛壓尺寸的半成品進行切邊整形,完成所述油軌鍛件的加工。
進一步,所述步驟Ⅲ)包括設置設置軋輥標尺的步驟;開啟楔橫軋設備,並進行楔橫軋模具水冷,將所述坯料放入楔橫軋設備的入口,開始楔橫軋作業的步驟和進行楔橫軋作業,使所述坯料在產生徑向壓縮的同時也產生軸向的延伸,通過徑向壓縮產生的不同臺階以適應所述油軌鍛件表面的尺寸要求,通過軸向的延伸使坯料的長度增加以滿足所述油軌鍛件的長度要求,完成楔橫軋作業後成為所述油軌鍛件的雛形並取出的步驟。
進一步,所述步驟Ⅳ)的熱鍛包括預鍛工序和終鍛工序,所述預鍛工序用於對所述雛形進行粗鍛壓,所述終鍛工序用於完成粗鍛壓後到所述油軌鍛件的鍛壓尺寸加工。
進一步,還包括將整形後的所述油軌鍛件進行控溫冷卻的步驟和將冷卻後的所述油軌鍛件進行熱處理的步驟。
進一步,所述坯料的長度為300~500毫米,直徑為28~35毫米,所述加熱溫度為1100~1180℃,所述軋輥標尺設置為-10.5~-9.5毫米,所述終鍛溫度大於等於850℃,所述控溫冷卻的溫度不大於600℃。
本發明有益的技術效果在於:
本發明在現有的熱鍛加工方法之前增加了楔橫軋工序,提高材料利用率,減少加工時間,提高生產效率,增加營業收益。另外,坯料經過預鍛工序後,改善了坯料金屬在終鍛型腔中的流動條件,使金屬易充滿終鍛型腔,減少了產生缺陷的機率,同時也減少終鍛模具的磨損,提高了模具的壽命。
附圖說明
圖1為本發明的總體流程圖;
圖2為本發明的楔橫軋工序的模具展開的主視圖;
圖3為本發明的油軌鍛件的雛形和楔橫軋模具的配合示意圖,其中A為油軌鍛件的雛形,B為楔橫軋模具;
圖4為本發明的油軌鍛件的俯視圖;
圖5為本發明的油軌鍛件的軸向剖視圖;
圖6為本發明的油軌鍛件的仰視圖;
圖7為本發明的油軌鍛件的A-A的剖視圖;
圖8為本發明的油軌鍛件的B-B的剖視圖;
其中,圖7和圖8是針對圖5中標示的剖視圖。
具體實施方式
下面結合附圖及較佳實施例詳細說明本發明的具體實施方式。
目前,針對油軌的加工方法主要有熱鍛和雷射焊接,本發明在現有熱鍛加工方法的基礎上做了改進,提供了一種用於發動機的油軌鍛件的加工方法,如圖1所示,主要包括以下步驟:
Ⅰ)利用切料設備截取所需要的坯料;
Ⅱ)將坯料進行加熱,使其表面溫度達到熱鍛溫度;
Ⅲ)將達到熱鍛溫度的坯料進行楔橫軋工序,將坯料加工成油軌鍛件的雛形;
Ⅳ)將油軌鍛件的雛形進行熱鍛加工,使其達到油軌鍛件的鍛壓尺寸,成為半成品;
Ⅴ)熱鍛後,將符合鍛壓尺寸的半成品進行切邊整形,完成油軌鍛件的加工;
Ⅵ)將整形後的油軌鍛件進行控溫冷卻;
Ⅶ)將冷卻後的油軌鍛件進行熱處理。
其中,楔橫軋工序包括以下步驟:
一、設置軋輥標尺;
二、開啟楔橫軋設備,並進行楔橫軋模具水冷,將坯料放入楔橫軋設備的入口,開始楔橫軋作業;
三、進行楔橫軋作業,使坯料在產生徑向壓縮的同時也產生軸向的延伸,完成楔橫軋作業後成為油軌鍛件的雛形並取出。
藉助楔橫軋設備的兩個帶楔形模的軋輥,通過徑向壓縮產生的不同臺階以適應油軌鍛件表面的尺寸要求,通過軸向的延伸使坯料的長度增加以滿足油軌鍛件的長度要求,這樣就可根據油軌鍛件的要求,一次性完成油軌鍛件的雛形加工,同時,楔橫軋工藝可以使金屬纖維流線沿油軌外形連續分布,並且晶粒進一步得到細化,所以其綜合機械性能較好,產品精度也高。因此,增加楔橫軋工藝既減少了坯料的浪費,提高了材料利用率,又提高了生產效率,改善了加工質量。
熱鍛工序分為預鍛工序和終鍛工序,該預鍛工序主要用於對上述雛形進行粗鍛壓,該終鍛工序用於完成粗鍛後到油軌鍛件的鍛壓尺寸加工。該雛形經過預鍛工序後,改善了金屬在終鍛型腔中的流動條件,使金屬易充滿終鍛型腔,減少產生缺陷的機率,同時也減少終鍛模具的磨損,提高終鍛模具的壽命。
利用上述加工方法,我們對某種油軌,如圖4-7所示,實施了加工處理:
首先,藉助高速圓盤鋸截取35×280毫米長度的坯料進行下料;
然後,將坯料放進KGPS-500Kw中頻加熱爐裡進行加熱,使其表面溫度達到1100~1180℃;
然後,開啟楔橫軋設備,並將如圖2所示的楔橫軋模具進行水冷,設置軋輥標尺為-10.5~-9.5毫米,將坯料放進楔橫軋設備的V型槽裡,開始楔橫軋作業;
然後,進行楔橫軋作業,使坯料成為油軌鍛件的雛形後,如圖3所示,將該雛形進行預鍛和終鍛加工,使坯料尺寸達到油軌鍛件的尺寸,終鍛的溫度大於等於850℃;
然後,經過切邊整形去除多餘的毛邊後,將油軌鍛件進行控溫冷卻,控溫冷卻的溫度不大於600℃;
最後,將冷卻後的油軌鍛件進行熱處理,完成整個加工過程。
該楔橫軋模具包括呈圓弧狀的基體部和設置在基體部上的成型部,如圖2所示,該成型部包括按順序排列的楔入部、展開部和精整部,在展開部和精整部設置有與待加工的油軌鍛件的外形臺階相對應的型槽,相對於成型部的長度方向的中心線,該型槽呈非對稱排列,但數量相等,對應位置的型槽的尺寸相同。
該成型部由三段接合而成,分別為前段、中段和後段,每段均呈圓弧狀,每段的弧度小於90度且與基體部的圓弧狀相一致,從楔入部到精整部,前兩段的弧度相同,均為65度。展開部分布在前段的後端、中段和後段的前端。該基體部兩側對稱設置有與楔橫軋設備連接的多個安裝孔。
該成型部的展寬角為10度,成型角為30度。
利用上述楔橫軋模具還可對長度為300~500毫米,直徑為28~35毫米的坯料進行楔橫軋處理;藉助上述方法,我們將原先需要35×325毫米長度的坯料變為35×280毫米,材料利用率提高了10%,加工時間也由原先的25-30秒變為了20-25秒,提高了生產效率,增加了營業收益。
雖然以上描述了本發明的具體實施方式,但是本領域的技術人員應當理解,這些僅是舉例說明,在不背離本發明的原理和實質的前提下,可以對這些實施方式做出多種變更或修改,因此,本發明的保護範圍由所附權利要求書限定。