設備和方法與流程
2023-12-06 12:15:01 2
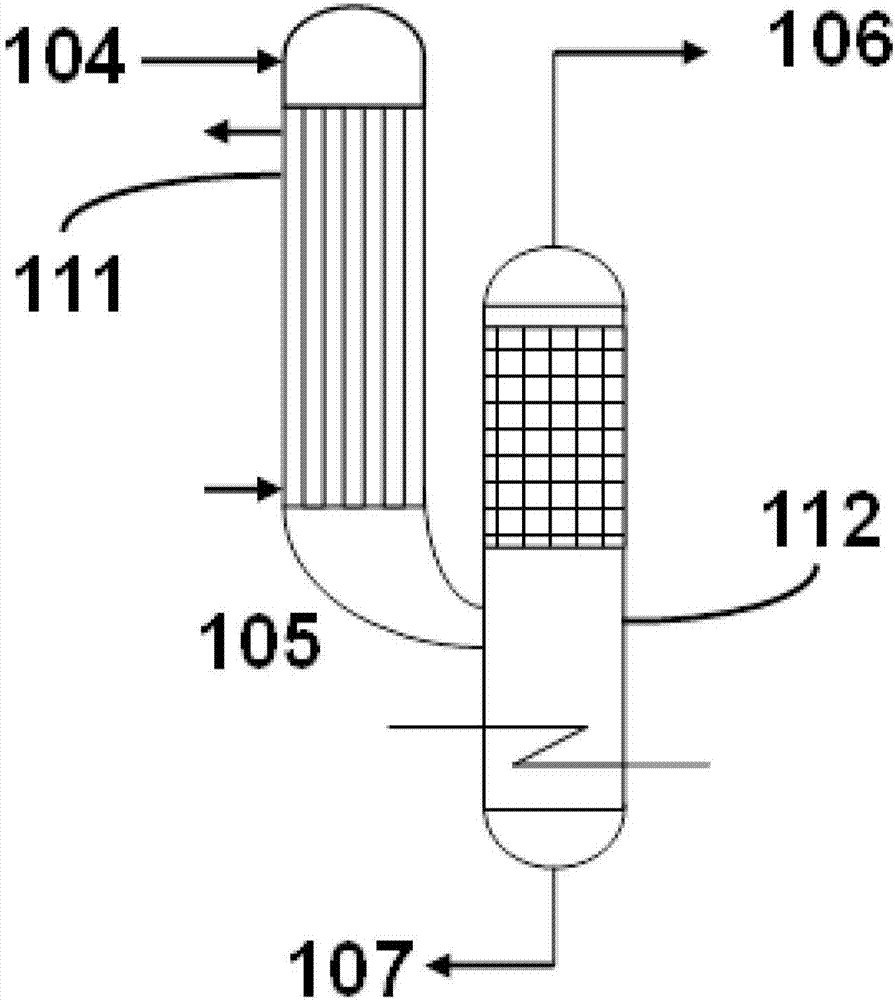
本發明涉及用於回收均相催化劑以再循環至反應器的設備和方法。更特別地,本發明涉及用於從包含醛的流中回收均相催化劑的設備和方法。還更特別地,本發明涉及用於從回收自加氫甲醯化反應器的流中回收均相銠催化劑的設備和方法。
在加氫甲醯化反應中,烯烴與合成氣反應,即與包含一氧化碳和氫氣的氣體混合物反應,以形成醛。所述反應通常在均相催化劑的存在下進行。適合的催化劑包括基於銠的催化劑,其通常以具有一個或多個磷配體的絡合物形式提供。適合的配體的實例包括有機亞磷酸酯配體和有機膦配體。
因為這些催化劑是昂貴的,所以通常將它們從含有產物醛的流中回收並且再循環至反應器。因為這些催化劑可以是溫度敏感的,如果它們暴露於高溫下,使得它們的失活速率增加,所以加氫甲醯化反應通常在適度條件下進行以保護催化劑。即使在這些溫和條件下,隨著催化劑連續地與產物流分離並且再循環至反應器,催化劑的活性也以緩慢但可感知的速率降低。
催化劑與含醛的流的分離通常需要蒸發醛,使得其可以在氣體/液體分離器中與催化劑分離。然後將含有催化劑的液體流再循環至加氫甲醯化反應器。這種類型的方法的一個實例可見於us4148830中。us6100432描述了類似的布置。
然而,在這種類型的方法中,需要高溫以蒸發醛。事實上,通常,溫度會使得蒸發器中的環境比加氫甲醯化反應器中所採用的環境更加嚴苛,其可以導致催化劑的失活速率加速。不期望受任何理論的限制,據信這種失活是由於形成無活性或活性較差的銠物質,所述銠物質在持續暴露於蒸發器中的條件時易於沉澱。
已經提出各種建議來應對該問題。例如,可以在一個以上的階段中於所選條件下進行蒸發,使得從反應器流中去除揮發性逐漸變低的連續部分。在該布置方案中,連續蒸發階段在減壓下進行操作。然而,通常,這將導致具有升高的溫度的連續階段,所述升高的溫度將增加催化劑的失活速率。
在us4166773中,描述了以下方法:其中將降膜蒸發器用於蒸發醛,以便減少催化劑暴露於升高的溫度的時間。在該方法中,將蒸發的醛和加熱的液體供給至分離塔,在所述分離塔中,將蒸發的產物作為塔頂餾出物(overheads)從所述塔中去除。在所述塔的底部收集液體流,其從所述塔的底部流過所述塔外部的冷卻系統。儘管降低了催化劑在蒸發器中的時間段,但是其依然在高溫下保持一段時間。此外,該系統確實增加了所述系統的資本和操作成本。此外,該系統可以需要複雜的控制,因為維持分離塔的底部與冷卻系統之間的冷卻循環是重要的,即使已經中止向反應器的再循環時。
在us5672766中考慮了用於蒸發的溫度與催化劑的亞磷酸酯配體的分解之間的關係,其中注意到限制催化劑暴露於高溫的要求,並且提出了計算使失活的風險最小化的溫度和停留時間的可接受組合的手段。
在us6500991中討論了其它布置方案。此處,將從氣體/液體分離器的底部回收的液體部分冷卻成低於反應器溫度,並且在該溫度下存儲,直到其需要再循環至反應器。
cn12030622描述了在蒸氣-液體分離內布置冷卻裝置的系統。然而,並未討論管束(bundles)的目的或如何操作它們。
在cn203464572中,描述了替代布置方案,其中兩個冷卻管束位於蒸發器之後的蒸氣-液體分離器內,使得液體部分經過冷卻管束。該實用新型的細節涉及用於提供冷卻水的閉環系統,並且在蒸發器或分離器內幾乎沒有操作的公開內容。
對用於回收均相催化劑的簡單且有效的設備及方法依然存在需求,在所述設備及方法中,使催化劑的失活速率最小化,但是不需要複雜的冷卻系統。已經發現,這可以通過使催化劑對於高溫的暴露最小化、然後快速冷卻催化劑來實現。特別地,已經發現,這可以通過使冷卻裝置位於與蒸發區直接接觸來實現,並且其中操作所述方法以使得:維持含催化劑的流的液體水平以使冷卻裝置浸入含催化劑的流中。已經發現,通過在蒸氣-液體分離器中提供冷卻,催化劑在高溫下不存在大的停留。
因此,根據本發明的第一方面,提供了用於從包含均相催化劑和分離組成的進料流中分離均相催化劑的設備,所述分離組成可以通過蒸發從所述進料流中分離,所述設備包括:
蒸發區;
用於將進料流供應至所述蒸發區的裝置,使得在使用中可以蒸發所述分離組成,將所述蒸發區配置為使得所述進料流在所述蒸發區中具有第一停留時間;
用於從所述蒸發區去除所述蒸發的分離組成的裝置;
蒸氣-液體分離器,其位於與所述蒸發區直接連通以收集包含所述均相催化劑的液體,將所述蒸氣-液體分離器配置為允許約10秒至約60分鐘的停留時間;
位於所述蒸氣-液體分離器內的冷卻裝置;
用於從所述蒸氣-液體分離器去除包含所述均相催化劑的液體的裝置;
其中所述設備被配置為使得包含所述均相催化劑的液體的體積維持在冷卻裝置基本上浸入包含所述均相催化劑的液體中的水平。
本發明的設備的結構使得:均相催化劑暴露於使蒸發區中的分離組成進行蒸發所需的高溫的時間可以保持為最小值。此外,當冷卻裝置所位於的蒸氣-液體分離器與蒸發區直接連通時,均相催化劑在蒸發後非常迅速地與冷卻裝置接觸。
在一個布置方案中,在蒸氣-液體分離器中的停留時間可以比所述流在蒸發區中的時間段更長。通過使用這種設備,基本上降低了催化劑失活,使得催化劑在其失活和需要替換之前可以再循環比迄今為止已經可實現的次數更多的次數。
蒸發區可以具有任何適合的配置,條件是其包含蒸發器。可以使用任何適合的蒸發器,條件是其能夠使分離組成優選以最小的停留時間從包含均相催化劑的液體中蒸發。適合的蒸發器包括降膜蒸發器、薄膜蒸發器、刮膜蒸發器、釜式蒸發器等。
蒸氣-液體分離器與蒸發區直接連通。通過『直接連通』,應理解,蒸氣/液體能夠在蒸發區與蒸氣-液體分離器之間行進,並且不經過冷卻裝置。在一個布置方案中,蒸氣-液體分離器可以與蒸發區呈整合的,使得所述蒸氣-液體分離器位於蒸發區的底部部分或形成其底部部分。然而,在一個布置方案中,蒸氣-液體分離器可以是與蒸發區連接的分離容器。在該布置方案中,分離容器緊鄰蒸發器,使得包含均相催化劑的液體可以在蒸發後儘可能快地與冷卻裝置接觸。
在其中蒸氣-液體分離器位於蒸發區的底部或形成其底部的一個布置方案中,蒸氣-液體分離器可以具有比蒸發區的橫截面更小的橫截面。通過這種手段,使維持冷卻裝置被基本上浸沒的液體水平所需的包含均相催化劑的液體的體積最小化。可以通過配置外殼來實現較小的橫截面,或者在一個布置方案中,外殼的橫截面可以保持恆定並且蒸氣-液體分離器可以位於所述殼(shell)內的殼體(housing)中,使得所述殼體提供較小的直徑。
在殼體存在的情況下,其可以配置成圍繞冷卻裝置。
蒸發器可以包括將包含均相催化劑的液體導向冷卻裝置的裝置。此類裝置包括一個或多個板或擋板。
可以使用任何適合的冷卻裝置。適合的裝置包括具有適合的冷卻劑流經其中的冷卻管、冷卻盤管或冷卻板,使得包含均相催化劑的液體與冷卻裝置接觸,通過與冷卻劑的熱交換發生冷卻。在一個布置方案中,冷卻裝置可以是被稱為『刺束(stab-inbundle)』熱交換器的類型的管束。『刺束』是用於描述一系列的管的術語,所述管通常可以被安裝以及從所述管經由法蘭插入其中的容器中移除。在使用中,所述管通常位於液體池中。通常,將所述系列的管提供為單個單元,使得各個管的入口和出口與單個管板連接,使得將冷卻劑從由一個或若干個擋板分離的同一頭部供應至管中。所述管通常是u型的,但是可以使用任何形狀的管,條件是所得的束具有可以通過法蘭引入的束。
可以使用兩個或更多個冷卻裝置來增加液體的冷卻。在存在兩個或更多個冷卻裝置的情況下,所存在的冷卻裝置可以是相同或不同的。冷卻裝置可以選自冷卻管、冷卻盤管、冷卻板或其組合。因此,例如,可以使用兩個或更多個管束。在另一實例中,可以將中心管束與位於其周圍的冷卻盤管一起使用。
為了增加可用於與液體接觸的表面,冷卻裝置可以包括鰭片、凹坑等。可以使用可增加表面可用性的裝置的混合體(mixture)。因此,例如,可以使用鰭片和凹坑的混合體。
裝置可以位於蒸氣-液體分離器中以攪拌液體,使得實現與冷卻裝置的接觸的增強。
所述冷卻裝置或各個冷卻裝置可以是可移除的。
在一個布置方案中,可以提供裝置以將蒸氣-液體分離器分成液體與冷卻裝置接觸的區域和存儲冷卻液體的腔(volume)。在殼體存在的情況下,這可以額外地提供用於對存儲區分離出接觸區域的裝置。
一定體積的液體保持在蒸氣-液體分離器的單個腔中或單獨的存儲區中,其用作整合的冷卻緩衝槽。
冷卻的液體的存儲與蒸氣-液體分離器的整合提供了多種優勢。特別地,其將使傳輸線的需求最小化,減少單元的佔用面積(footprint)和降低資本成本。此外,一定體積的冷卻的液體在蒸氣-液體分離器中的存在為泵提供了穩定的吸入壓力,所述泵用於將含有均相催化劑的冷卻的液體回流至反應器。由於用於回流的泵需要恆定的液體進料,因此,起緩衝罐作用的蒸氣-液體分離器的存在將被用作緩衝槽,它的存在將有助於使泵壽命最大化。通常,可以操作用於回流的泵,使得包含均相催化劑的液體的體積維持在其為泵提供穩定吸入和避免泵送氣體的水平。
根據本發明的第二方面,提供了用於從包含均相催化劑和分離組成的進料流中分離均相催化劑的方法,所述分離組成通過蒸發從所述進料流中分離,所述方法包括以下步驟:
將所述進料流提供至以上第一方面所述的設備中;
操作蒸發區使得所述分離組成被蒸發,並且使得所述進料流在所述蒸發區中具有第一停留時間;
從所述蒸發區中去除蒸發的組成;
使包含所述均相催化劑的液體從所述蒸發區傳行進至蒸氣-液體分離器;
將所述蒸氣-液體分離器中的液體通過位於所述蒸氣-液體分離器內的冷卻裝置進行冷卻;包含所述均相催化劑的液體在所述蒸氣-液體分離器中的停留時間為約10秒至約60分鐘;以及
回收包含所述均相催化劑的液體。
在一個布置方案中,蒸氣-液體分離器中的停留時間可以比蒸發區中的停留時間更長。
本發明的方法可以用於通過蒸發從包含均相催化劑的流中分離任何組成。在一個布置方案中,進料流可以是從自加氫甲醯化反應中回收的流。因此,均相催化劑可以是任何適用於加氫甲醯化反應的催化劑。所述催化劑可以是可與一個或多個配體組合使用的銠催化劑。所述配體可以是膦或亞磷酸酯。在一個布置方案中,其可以是三苯基膦。
可以在任何適合的溫度和壓力下進行分離組成的蒸發,並且以上第一方面的設備將據此進行配置。所選的溫度和壓力將降取決於待蒸發的組成。在一個布置方案中,可以將蒸發在約90℃至約160℃、或約120℃至約140℃的溫度下進行。可以使用任何適合的壓力,條件是所述壓力低於反應器的壓力。所述壓力可以為約1mmhg至約7600mmhg。所選的壓力將取決於包含在供給至蒸發區的流中的組分。例如,在所述流包含醛的情況下,在存在較重的醛而不是存在較輕的醛時,通常將選擇較低的壓力。因此,例如,在醛具有2至5個碳原子的情況下,所述壓力可以選擇為約1bara至約8bara,而對於具有5個以上碳原子的醛,至多約1bara的壓力可以是適合的,並且所述壓力通常為約0.5bara至約0.7bara。
進料流在蒸發區中的停留時間將通常選擇為儘可能短的。可以使用幾秒至幾分鐘的量級的停留時間。適合的時間包括2秒至60秒,並且可以為10、20、30、40或50秒,儘管其可以更長。
可以在蒸氣-液體分離器中使用任何適當的停留時間。在一個布置方案中,停留時間可以比用於蒸發區的停留時間更長。蒸氣-液體分離器中的停留時間通常將具有幾分鐘的量級。適合的時間包括1分鐘至60分鐘,並且可以為2、5、10、20或30分鐘。可以使用更長的時間。
在蒸發後,催化劑在液體中的濃度可以為約50ppmwt至約1000ppmwt。催化劑的濃度可以為約100ppmwt至約500ppmwt,或者為約250ppmwt至約400ppmwt。每摩爾催化劑中的配體的濃度可以為約1摩爾至約500摩爾。
可以在蒸發區中使用任何適合的溫度。在一個布置方案中,其可以為約60℃至約90℃、約70℃至約85℃、約65℃至約80℃。
儘管將液體流冷卻以使催化劑的損壞風險最小化是重要的,但是通常防止溫度下降過低也是重要的,因為這可以導致催化劑沉澱。如果催化劑從液體部分中沉澱析出,則難以將催化劑在工藝條件下再溶解。因此,沉澱可以導致催化劑的永久損失。應當理解,對『催化劑』的提及包括含有可以存在的任何配體的整個催化劑體系。
催化劑從液體部分中沉澱析出的溫度將取決於所使用的催化劑及其在蒸氣-液體分離器的液體中的濃度。為了減少催化劑沉澱的可能性,將冷卻裝置維持在比發生催化劑沉澱的溫度高至少5℃的溫度是優選的。
在冷卻裝置是可移除的情況下,如果任何催化劑都在冷卻裝置的表面上沉澱,則這提供了優勢。通過移除冷卻裝置,確實沉澱的任何催化劑可以被機械地、化學地或通過其它方式回收並且優選重複使用。
根據本發明的第三方面,提供了加氫甲醯化反應,其包括:
將烯烴與合成氣在均相催化劑的存在下於反應器中反應以形成醛;
回收包含所述醛和所述均相催化劑的流,並且根據本發明的以上第二方面所述的方法處理所述流,使得分離組成為所述醛;以及
將包含所述均相催化劑的回收的流回流至所述反應器。
可以將任何適合的烯烴用於加氫甲醯化反應。烯烴可以選自具有2至20個碳原子或3至14個碳原子的α-烯烴。儘管通常使用α-烯烴,但應當理解,可商購獲得的具有四個或更多個碳的烯烴可能含有少量的相應的內烯烴。此外,不考慮碳原子的數目,商用烯烴可能含有一些相應的飽和烴。儘管所述烯烴可以在進行加氫甲醯化之前被純化,但是通常不需要純化。
在適合的反應條件下進行加氫甲醯化反應。例如,加氫甲醯化反應可以在約45℃至約200℃、優選地在約60℃至約140℃的溫度下進行。
加氫甲醯化反應可以在約1psia至約10000psia的總氣壓下進行。優選地,加氫甲醯化反應在小於約1500psia的壓力下進行,更優選地在小於約500psia的壓力下進行。
蒸發器的進料流可以是一些或所有從加氫甲醯化反應中回收的流。在另一布置方案中,蒸發器的進料流可以是已經去除一部分醛產物後的流。
在進料流為從加氫甲醯化反應中回收的流的情況下,所存在的醛的量可以為至多90重量%並且可以甚至更高。在一個布置方案中,所存在的醛的量為約10重量%至約80重量%、或約30重量%至約70重量%。所存在的量將取決於特定的反應條件和加氫甲醯化反應的效率。
至蒸發器的進料流被從加氫甲醯化反應中回收時,其通常可以額外地包含未反應的烯烴。所存在的烯烴的量將取決於加氫甲醯化反應的效率。所存在的未反應的烯烴的量可以為進料流的至多約20重量%。還可以存在來自進料烯烴的雜質,例如相應的烷烴。
此外,可以存在少量加氫甲醯化反應的副產物。這些可以包括未反應的異構化烯烴、氫化烯烴、高沸點醛縮合副產物和烴基(alkyl)取代的膦配體副產物中的一種或多種。此外,可以存在用於加氫甲醯化反應中的任何溶劑或添加劑。
加氫甲醯化反應中的氫氣、一氧化碳和烯烴的總氣壓可以為約1psia至約10000psia,但是更通常在低於約1500psia及任選地在約500psia或更低的壓力下對其操作。所使用的分壓將通常取決於所用的反應物的量和性質。因此,例如,一氧化碳分壓可以為約1psia至約120psia,例如約3psia至約90psia,氫氣分壓可以為約10psia至約200psia,例如約20psia至約160psia。通常,氫氣與一氧化碳的摩爾比可以為約1:10至100:1或更高。摩爾比為約1:1至約10:1。
加氫甲醯化反應可以是連續、半連續或間歇反應。可以將包含均相催化劑的回收的流連續地或增量地回流至反應器。
為了輔助加氫甲醯化反應的熱控制,可以由冷卻裝置將蒸氣-液體分離器中的液體冷卻至低於加氫甲醯化反應溫度的溫度。在一些布置方案中,可以由冷卻裝置將蒸氣-液體分離器中的液體冷卻至比加氫甲醯化反應的溫度低約30℃的溫度、或比加氫甲醯化反應的溫度低約25℃的溫度、或比加氫甲醯化反應的溫度低約20℃的溫度、或比加氫甲醯化反應的溫度低約15℃的溫度。
現在將以實例形式參照附圖來描述本發明,其中:
圖1為本發明的第三方面的方法的示意圖;
圖2為根據本發明的第一方面的設備的示意圖;
圖3為根據本發明的第一方面的替代設備的示意圖;以及
圖4為根據本發明的第一方面的替代設備的示意圖。
為了避免疑義,這些附圖作為輔助僅旨在理解本發明,並不旨在解釋為關於所示例的部件或其位置的精確布置、容器的形狀或任何輔助特徵而限制本發明的範圍。本領域技術人員應理解,附圖是示意性的,並且在商業工廠中可能需要其它裝備項,例如原料罐、泵、真空泵、壓縮機、氣體循環壓縮機、溫度傳感器、壓力傳感器、卸壓閥、控制閥、流量控制器、位面控制器、收集槽、存儲槽等。此類輔助裝備的提供不形成本發明的部分並且與常規的化工實踐相一致。
如圖1所示例,將包含氫氣和一氧化碳的流經過管線1供給至反應區9,並且將包含烯烴的流經過管線2供給至反應區9,在所述反應區9中,加氫甲醯化反應在銠催化劑和膦配體(例如三苯基膦)的存在下發生。將加氫甲醯化反應在高溫和高壓的條件下於反應區9中進行。反應區9可以包含一個或多個加氫甲醯化反應器,並且各個反應器可以位於同一容器或單獨的容器中。將不需要的氣體從反應區9中經管線3去除。
將進料流從反應區9中經管線4回收。使進料流行進至產物回收區11,所述產物回收區11包含未示出的蒸發區和蒸氣-液體分離器。蒸發區包括未示出的熱交換器,在所述熱交換器中加熱所述進料流並且可以蒸發一些醛產物。然後使所述流行進至包括未示出的冷卻裝置的蒸氣-液體分離器中。將醛從產物回收區中經管線6轉移。將包括催化劑的液體流從產物回收區11經管線7回收,然後使用泵12經管線8泵送回流至反應區9。
圖2示例了產物回收區的一個實例。在該布置方案中,將進料流經管線104供給至蒸發區111,其中熱交換器(示為降膜蒸發器)加熱進料流並且蒸發一些醛產物。然後,使來自蒸發區的輸出流經由105行進至蒸氣-液體分離器112,所述蒸氣-液體分離器112包含未示出的防霧沫內部構件和液體冷卻裝置。將醛從產物回收區中經管線106去除。將包括催化劑的液體流從產物回收區中經管線107回收。
圖3示例了產物回收區的蒸氣-液體分離器211的一個實例。在該布置方案中,將來自蒸發區的輸出流經管線205供給至蒸氣-液體分離器,其中將分離組成(例如醛)經管線206去除。未蒸發的液體向下流動至蒸氣-液體分離器211的底部部分,刺束熱交換器215位於所述底部部分。向刺束熱交換器經管線213供應冷卻劑。將溫熱的冷卻劑經管線214去除。將包含均相催化劑的液體流經管線207回收。
圖4示例了產物回收區的蒸氣-液體分離器311的第二個實例。在該布置方案中,將來自蒸發區的輸出流經管線305供給至蒸氣-液體分離器,其中將分離組成(例如醛)經管線306去除。未蒸發的流體向下流動至蒸氣-液體分離器311的底部部分,盤管熱交換器315位於所述底部部分。向盤管熱交換器經管線313供應冷卻劑。將溫熱的冷卻劑經管線314去除。將包含均相催化劑的液體流經管線307回收。