流體噴射設備的製作方法
2023-12-11 02:12:32 1
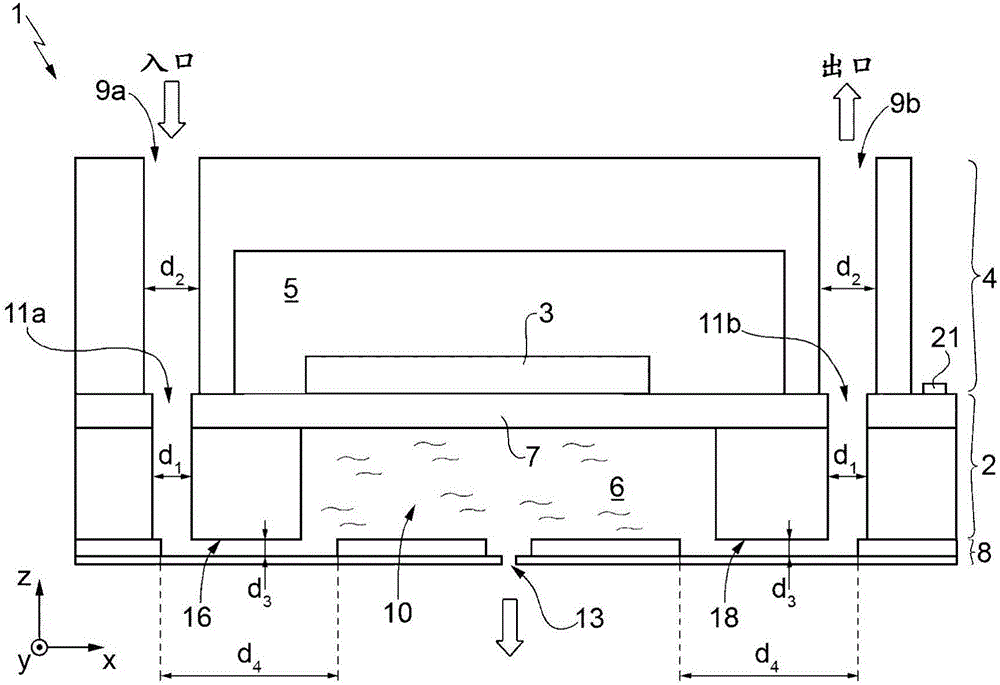
本實用新型涉及具有限制通道的流體噴射設備。
背景技術:
在現有技術中,已知多種類型的流體噴射設備,尤其是用於列印應用的噴墨頭。具有適當修改的類似頭可進一步用於除墨水之外的流體的噴射,例如用於生物或生物醫學領域的應用,用於在製造用於生物分析的傳感器期間生物材料(例如,DNA)的局部應用。
已知方案設想經由大量的預處理晶圓的膠合或接合來進行耦合。該方案成本較高並且要求高精度。組裝期間晶圓之間的任何可能的未對齊都會引起完成的設備的結構弱化和非最佳操作。
技術實現要素:
本實用新型的目的在於提供一種具有限制通道的流體噴射設備,其將不具有現有技術的缺陷。
根據本實用新型的一個方面,提供一種流體噴射設備,其特徵在於,包括:第一半導體本體,包括:致動器,操作性地耦合至室,所述室用於包含流體並被配置為在所述噴射設備的操作條件期間引起所述流體的噴射;以及用於所述流體的入口通道,在第一方向上延伸並具有第一尺寸的截面;以及第二半導體本體,耦合至所述第一半導體本體,具有與所述室流體連接且被配置為朝向所述噴射設備外部的環境排出一定量的所述流體的噴射噴嘴,其中所述第二半導體本體還包括第一限制通道,所述第一限制通道流體地耦合至所述入口通道、在與所述第一方向垂直的第二方向上延伸並具有小於所述第一尺寸的第二尺寸的相應截面,所述限制通道針對所述流體形成將所述入口通道與所述室耦合的流體路徑。
在一個實施例中,所述入口通道的截面的尺寸在所述入口通道的整個延伸中是恆定的。
在一個實施例中,所述第一限制通道的截面的尺寸在所述第一限制通道的整個延伸中是恆定的。
在一個實施例中,所述入口通道的截面的尺寸包括在20μm和200μm之間,並且所述限制通道的截面的尺寸包括在2μm和300μm之間。
在一個實施例中,所述第一限制通道與所述入口通道直接流體連接;以及所述第一限制通道的截面的尺寸可變,並且在所述第一限制通道流體連接到所述入口通道的情況下為呈現最大值。
在一個實施例中,所述噴射噴嘴被配置為在與所述第一方向平行且垂直於所述第二半導體本體的所在平面的噴射方向上噴射所述流體,所述第二方向與所述第二半導體本體的所在平面平行。
在一個實施例中,所述第一半導體本體還包括用於所述流體的出口通道,所述出口通道在離所述入口通道的一距離處延伸且與所述入口通道平行並且流體地耦合至所述室,以實現對未經由所述噴射噴嘴被排出的所述流體的再循環;以及所述第二半導體本體還包括第二限制通道,所述第二限制通道與所述第一限制通道共面並且被配置為將所述室與所述出口通道流體耦合,所述限制通道的相應截面的尺寸小於所述出口通道的截面的尺寸。
在一個實施例中,流體噴射設備還包括第三半導體本體,所述第三半導體本體被布置在所述第一半導體本體上,所述第三半導體本體包括入口歧管,所述入口歧管在所述第一方向中延伸作為所述入口通道的延長並具有第三尺寸的相應截面,所述第三尺寸大於所述入口通道的截面的第一尺寸且大於所述限制通道的截面的第二尺寸。
在一個實施例中,所述第三半導體本體還包括出口歧管,所述出口歧管與所述第一方向平行延伸作為所述出口通道的延長並具有比所述出口通道的截面的尺寸大的尺寸的相應截面。
在一個實施例中,所述致動器包括被布置在所述室上的薄膜和被布置在所述薄膜上的壓電元件,其中所述壓電元件可以被驅動用於引起所述薄膜朝向所述室的偏移或者可選的遠離所述室的偏移。
根據本實用新型的方案,提供了具有限制通道的流體噴射設備。
附圖說明
為了更好地理解本實用新型,現在僅參照附圖通過非限制性實例來描述優選實施例,其中:
圖1A是根據本公開一個實施例的流體噴射設備的橫向截面圖;
圖1B是圖1A的流體噴射設備的一部分的立體圖;
圖2至圖20示出了用於製造圖1A和圖1B的流體噴射設備的步驟;以及
圖21是根據本公開又一實施例的流體噴射設備的橫向截面圖。
具體實施方式
基於壓電技術的流體噴射設備可以通過將預先採用通常用於製作MEMS(微機電系統)器件的微加工技術處理的多個晶圓接合或膠合到一起來製造。具體地,圖1A示出了根據本公開一個方面的流體噴射設備1。流體噴射設備1在笛卡爾軸X、Y、Z的三軸系統中定向。參照圖1A,位於與平面XY平行的平面中的第一晶圓2具有一個或多個壓電致動器3,壓電致動器3被設計為被驅動來生成薄膜7的偏轉,其中薄膜7部分地懸置在室10上方延伸,室10被設計為限定用於包含在使用中將被排出的流體6。
以圖1A中未詳細示出但如下描述的方式,壓電致動器3包括:導電材料的第一電極,其在薄膜7上方延伸;壓電元件,在在第一電極上方延伸並且電耦合至第一電極;以及導電材料的第二電極,在壓電元件上方延伸並且電耦合至壓電元件。在使用中,驅動第一電極和第二電極以致動壓電元件,由此生成薄膜7的偏轉。
用於流體6進入室10的中間通道11a以及用於流體6從室10中流出的中間通道11b延伸穿過晶圓2的整個厚度。
在使用中,當壓電致動器3被驅動時,通過設置在不同於第一晶圓2的又一晶圓中的噴嘴13來排出流體6的液滴。中間入口通道11a和中間出口通道11b都具有圓形或多邊形形狀,其直徑d1(沿方向X測量)包括在20μm和200μm之間(例如,100μm),並且截面的尺寸A1包括在20μm和200μm之間(例如,80μm)。根據一個實施例,中間入口通道11a和中間出口通道11b的截面在其沿著Z的整個延伸中是均勻的。
位於與平面XY平行的平面中並且布置在第一晶圓2上的第二晶圓4具有用於包含壓電致動器3的一個或多個室5,諸如在使用中將壓電致動器3與將被排出和來自環境的流體6隔離。第二晶圓4還具有用於流體6的入口的通道9a和用於沒有通過噴嘴13被噴射的流體6的出口的通道9b,因此能夠再循環流體6。入口通道9a和出口通道9b是穿過第二晶圓4製作的孔。入口通道9a和出口通道9b都具有圓形或多邊形形狀,其中直徑d2(沿方向X測量)大於直徑d1,並且包括在30μm和1000μm之間,例如180μm。
入口通道9a和出口通道9b還具有尺寸A2包括在50μm和1000μm之間(例如200μm)的截面,其中A2被選擇大於A1。根據一個實施例,入口通道9a和出口通道9b的截面在其沿著Z的整個延伸中是均勻的。
入口通道9a流體地耦合至中間入口通道11a,以及出口通道9b流體地耦合至中間出口通道11b。更具體而言,該入口通道11a和出口通道11b分別在垂直於平面XY的方向Z上與入口通道9a和出口通道9b對齊。
位於平行於平面XY的平面中且布置在第一晶圓2下方的第三晶圓8具有與室10流體連接的用於流體6的噴射的噴嘴13。
第一晶圓2和第三晶圓8的耦合能夠形成室10,該室部分通過第一晶圓2且部分通過第三晶圓8來界定。
根據本公開的方面,第三晶圓8具有第一限制通道16和第二限制通道18,每一個都具有在方向Z的深度上延伸並且在平面XY中縱向延伸其中主要沿著X延伸的溝槽的形式。第一限制通道16和第二限制通道18分別將中間入口通道11a與室10流體連接以及將室10與中間出口通道11b流體連接。更具體地,根據本公開的方面,第一限制通道16和第二限制通道18直接流體連接至室10。第一限制通道16和第二限制通道18具有:深度d3,沿著Z,包括在2μm和300μm之間,例如30μm;主要延伸d4,沿著X,包括在2μm和300μm之間,例如40μm;以及次要延伸(未示出),沿著Y,包括在10μm和1000μm之間,例如400μm。
更具體地,第一限制通道16和第二限制通道18橫斷流體流動方向(在這種情況下為X)具有均勻的截面(面積),其具有包括在2μm和300μm之間(例如,30μm)之間的尺寸A3。
根據不同實施例,第一限制通道16具有不均勻的截面,但是諸如在第一限制通道16和中間入口通道11a之間的交叉處具有最大尺寸值以利於(在製造期間)耦合到一起以及來自中間入口通道11a的流體進入第一限制通道16。可選地或另外地,第二限制通道18也在其與中間出口通道11b的交叉處具有截面的最大尺寸值以利於(在製造期間)耦合到一起。
不管實施例如何,第一限制通道16和第二限制通道18都至少具有分別小於中間入口通道11a和中間出口通道11b的任何截面的相應截面。
此外,第一限制通道16和第二限制通道18分別至少具有小於入口通道9a和出口通道9b的任何截面的相應截面。
在使用中,流體6在方向Z上流過入口通道9a和中間入口通道11a,然後在垂直於方向Z的方向X上流過第一限制通道16,然後進入室10。在使用中,作為由壓電致動器3控制的薄膜7朝向室10內側的偏轉的結果,通過噴嘴13噴射流體6的一部分,而流體6的另一部分被傳輸向出口通道9b,首先在方向X上流過第二限制通道18,然後在方向Z上流過中間出口通道11b和出口通道9b。
第一限制區域和第二限制區域具有在通過噴嘴13噴射流體6期間減少流體6在與先前描述相反的方向上的流動(具體地,減少流體6朝向入口通道的返回)的功能。在第三晶圓8中設置第一限制通道16和第二限制通道18(它們的主要延伸平行於第三晶圓8位於的平面)使得可以限制噴射設備1沿Z方向的厚度並且利於晶圓2、4和8之間的耦合,且不需要滿足通道之間的對齊的精確要求。實際上,這足以使中間入口通道11a和第一限制通道16相互流體連通,以便於不損害噴射設備1的操作的特性。
根據本公開的實施例,前述晶圓2、4、8是諸如矽的半導體材料。可以進一步設置(以已知方式,圖中未示出)摻雜矽或摻雜多晶矽或金屬的導電層,用於將壓電元件電耦合至導電焊盤21,用於驅動壓電元件3以引起薄膜7的偏轉。可根據需要進一步存在介電或絕緣層。
晶圓2、4、8通過界面接合區域和/或膠合區域和/粘合區域組裝到一起。所述區域在圖1A中未詳細示出。
圖1B是圖1A的噴射設備1的一部分的立體圖,其根據圖1A所示的截面來截取。完整的噴射設備1將通過將圖1B所示的部分與相似且鏡像的部分結合到一起來形成。
在圖1B中,在使用中,流體的路徑通過箭頭15表示。噴射設備1的其餘元件由與圖1描述中使用的相同參考標號指定並且不再進行描述。
根據本公開的一個實施例,參照圖2至圖20,現在描述用於製造圖1的流體噴射設備1的處理。
參照圖2至圖10,描述處理第一晶圓2的步驟,其中第一晶圓2在該實例中容納致動器元件(具體為壓電類型),其被設計為在使用中被驅動來將液體/流體排出出噴射設備1。
參照圖2,提供包括襯底201的晶圓2,襯底201例如具有包括在近似50μm和720μm之間(具體地,近似500μm)的厚度。根據本實用新型的實施例,襯底201是諸如矽的半導體材料。襯底201具有第一表面201a和第二表面201b,它們在方向Z上彼此相對。在第一表面201a上形成例如由氧化矽製成的薄膜層202,其具有包括在近似1μm和4μm之間的厚度,具體為2.5μm。在製造步驟的結束,薄膜層202形成圖1A的薄膜7。然後,執行包括壓電元件和用於致動壓電元件的電極的堆疊的形成。為此,在薄膜層202上方,在晶圓200上沉積導電材料的第一層204,其例如為鈦(Ti)或鉑(Pt),具有包括在近似20nm和100nm之間的厚度。接下來,在導電材料的第一層204上沉積壓電材料層206,其例如為PZT(Pb、Zr、TiO3)、具有包括在1.5μm和2.5μm之間的厚度,具體為2μm。然後,在壓電材料層206上沉積導電材料的第二層208,其例如為釕,具有包括在近似20nm和100nm之間的厚度。
接下來,參照圖3,在導電材料的第二層208上形成掩模211,掩模211被設計為覆蓋導電材料的第二層208的一部分,該部分將隨後形成用於致動壓電元件的頂部電極。蝕刻步驟能夠去除導電材料的第二層208不被掩模211保護的部分。使用同一掩模211,但採用不同的蝕刻化學劑,執行晶圓200的蝕刻以去除壓電材料層206的暴露部分,從而形成壓電元件226。在導電材料的第一層204上中斷蝕刻,並且去除掩模211(圖4)。例如通過溼蝕刻執行導電材料的第二層208的蝕刻,並且通過幹蝕刻或溼蝕刻執行壓電層206的蝕刻。
然後(圖5),限定導電材料的第二層208以結束頂部電極的形成。為此,在導電材料的第二層208的一部分上形成掩模213(例如,光致抗蝕劑),用於選擇性去除在壓電元件226的外邊緣上延伸的部分而不去除導電材料的第二層208在壓電元件226的中心處延伸的部分。在圖5的蝕刻步驟之後暴露的壓電元件226的部分在頂視圖中形成完全或部分環繞頂部電極228並且具有寬度P1(例如在方向X上延伸,包括在4μm和8μm之間)的框架。由此形成頂部電極228,其被設計為在使用中被偏置用於致動壓電元件226(以下進行更完整的描述)。
接下來(圖6),形成掩模215(例如,光致抗蝕劑),其被設計為保護頂部電極228和壓電元件226,並且相對於壓電元件228橫向延伸距離P2,其中距離P2在方向X上從壓電元件228的邊緣開始測量,距離P2包括在2μm和8μm之間。然後,執行蝕刻步驟以去除導電材料的第一層204沒有被掩模215保護的部分。由此形成底部電極224,用於在使用中致動壓電元件。
接下來(圖7),從晶圓220去除掩模215,並且執行在晶圓200上沉積鈍化層218的步驟。鈍化層例如是利用PECVD技術沉積的氧化矽(SiO2),並且具有包括在近似15nm和495nm之間(例如,近似300nm)的厚度。通過隨後的光刻和蝕刻步驟,鈍化層218在頂部電極228的中心部分上被選擇性地去除,而其保持在頂部電極228的邊緣部分、壓電元件226的邊緣部分、底部電極224的邊緣部分以及薄膜層202的暴露部分的邊緣部分上。
根據至此所描述的,鈍化層218不完全覆蓋頂部電極228,由此可以通過導電路徑電接觸。相反,底部電極224不可電接觸,因為其完全被上覆的壓電元件226和鈍化層218所保護。同時,在對應於底部電極224的區域(具體為底部電極224在平面XY中延伸到壓電元件226的外邊緣外的部分)中執行鈍化層218的一部分的選擇性去除的步驟。以這種方式,底部電極224的區域224』被暴露,並且由此可以通過自身的導電路徑電接觸。可以在同一光刻和蝕刻步驟(具體為使用同一掩模)期間形成用於形成與頂部電極228和底部電極224的電接觸的開口。
在圖8中示出了第一導電路徑221和第二導電路徑223的形成的步驟。為此,執行導電材料(諸如金屬,具體為鈦或金)的沉積步驟,直到該層被形成為具有包括在近似20nm和500nm之間(例如,近似400nm)的厚度為止。通過光刻步驟,由此沉積的導電材料的層被選擇性蝕刻以形成第一導電路徑221和第二導電路徑223,該第一導電路徑221在晶圓200上方延伸並與頂部電極228電接觸,該第二導電路徑223在晶圓200上方延伸並通過先前形成的區域224』與底部電極224電接觸。第一導電路徑221和第二導電路徑223在晶圓200上方延伸直到期望形成導電焊盤21的區域,其中導電焊盤21以已知方式被設計為用作電接觸點,用於在使用中偏置頂部電極228和底部電極224以致動壓電元件226。
最後(圖9),在通過底部電極224、壓電元件226和頂部電極228形成的堆疊件旁邊延伸的對應區域中選擇性地蝕刻鈍化層218和薄膜層202,以形成暴露襯底201的表面部分的對應溝槽225a、225b。溝槽225a、225b在頂視圖中具有四邊形形狀或圓形形狀,在任何情況下都具有最大直徑d1,諸如以被參照圖1A描述的通道9a、9b完全包含(當沿著Z對齊時,在頂視圖中)。具體地,根據一個實施例,溝槽225a、225b在頂視圖中具有的形狀等於針對通道9a、9b再次在頂視圖中選擇的形狀。在任何情況下,與針對溝槽225a、225b選擇的形狀無關,在隨後的製造步驟中,它們將在方向Z上被布置為與相應通道9a、9b對齊,從而彼此流體連接。
接下來(圖10),執行從襯底201的背側201b的蝕刻步驟,以在對應於壓電元件226的位置中形成凹部231(在隨後步驟中,該凹部限定室10)。凹部231通過蝕刻襯底201直到到達薄膜層202來得到。根據一個實施例,薄膜層202用作蝕刻停止層。同時地,襯底201被蝕刻以在分別對應於溝槽225a、225b的位置中形成第一通孔233a和第二通孔233b,使得第一通孔233a和溝槽225a將一起形成中間入口通道11a,以及第二通孔233b和溝槽225b將一起形成中間出口通道11b。為了形成中間入口通道11a和中間出口通道11b,有利地以已知方式提供對齊標記。
作為所描述內容的備選,進一步可以在通過溝槽225a、225b暴露的表面部分上蝕刻襯底201,以形成通孔233a、233b。以這種方式,不需要設置對齊標記。
圖11至圖14示出了第二晶圓4的微加工的步驟,第二晶圓4 包括用於容納壓電致動器的腔5以及用於流體6的入口通道9a和出口通道9b。
參照圖11,提供晶圓4,晶圓4包括襯底401,該襯底例如具有包括在近似100μm和1000μm之間(具體近似為725μm)的厚度。根據本實用新型的實施例,襯底401例如由諸如矽的半導體材料製成。襯底401具有第一表面401a和第二表面401b,它們在方向Z上彼此相對。在襯底401上形成例如由多晶矽或外延生長的矽製成的結構層409。可以進一步在襯底401和結構層409之間設置界面層410,其例如由氧化矽(SiO2)製成。
接下來(圖12),執行在結構層409上形成掩模403的步驟。為此,掩模層403例如由光致抗蝕劑形成。掩模層403被光刻地限定以形成被設計為界定晶圓4的部分409』和409」(它們在後續步驟中將形成入口通道9a和出口通道9b)以及晶圓4的部分409」』(其在後續步驟中將形成包圍室5)的掩模區域。然後,通過圖13所示的蝕刻步驟(用箭頭406表示),結構層409在其不被掩模403保護的表面部分上方延伸的區域被部分或完全去除。襯底401與結構層409之間的界面層410用作蝕刻停止層。
掩蔽蝕刻的又一步驟(圖14)僅發生在晶圓4將形成入口通道9a和出口通道9b的區域中,這能夠完全去除暴露的襯底區域401(和可能的界面層)以形成提供入口通道9a和出口通道9b的沿著Z延伸穿過晶圓4的整個厚度的通孔。
不同地,相對於圖11-圖14的處理步驟(第二晶圓4的處理),可以並行地或者以時間序列來執行參照圖2至圖10描述的處理步驟(第一晶圓2的處理)。
在任何情況下,參照圖15A,第二晶圓4(在圖13的處理步驟中)和第一晶圓2(在圖10的處理步驟中)被耦合到一起,使得:入口通道9a和中間入口通道11a將在方向Z上基本相互對齊並且相互流體連接;出口通道9b和中間出口通道11b將在方向Z上基本相互對齊並且相互流體連接;以及室5將完全包圍壓電元件226。
圖15B示出了在圖15A的耦合步驟結束時的第一晶圓2和第二晶圓4。
參照晶圓4,結構層409的沿著Z延伸到大於形成室5的凹部的高度的部分是被設置用於與晶圓2機械耦合的區域。在圖15A所示的耦合步驟期間,為了保證晶圓2和晶圓4之間的良好粘合,在機械耦合區域上的晶圓4上施加接合聚合物(未示出)。在晶圓2和晶圓4之間的對齊和耦合的步驟之後,熱處理的步驟(根據所使用的接合聚合物改變持續時間和溫度)能夠實現晶圓2和晶圓4相互的完全粘合。
參照圖16,現在描述用於處理第三晶圓8的步驟。可以與參照圖2至圖15B描述的任何步驟同時地或者在其之前或者在其之後以不同方式執行這些處理步驟。
參照圖16,提供了包括襯底801(例如,半導體材料,具體為矽)的第三晶圓8,該襯底具有在方向Z上彼此相對的頂面801a和底面801b。
例如通過熱氧化在第一表面801a上形成氧化矽(SiO2)的界面層803。界面層803例如具有包括在近似0.5μm和5μm之間(具體為近似1μm)的厚度。
接下來,在界面層803上形成外延生長矽的結構層805,其具有包括在近似10μm和1000μm之間(具體為近似25μm)的厚度。具體地,結構層805外延生長,直到其達到大於期望厚度(例如,近似3μm厚)的厚度,然後經受CMP(化學機械拋光)步驟以減小其厚度並得到具有低粗糙度的頂面805a。
結構層805可以是除多晶矽之外的材料,例如矽或一些其他材料,只要其可以以相對於製作界面層803的材料選擇性的方式被去除即可。
接下來(圖17),執行結構層805的掩蔽蝕刻的步驟以形成第一溝槽806和第二溝槽807,這兩個溝槽將在後續步驟中形成第一限制通道16和第二限制通道18。通過第一溝槽806和第二溝槽807,暴露界面層803的相應表面區域。在平面XY的頂視圖中,第一溝槽806和第二溝槽807具有矩形形狀,其主側沿著方向X且次側沿著方向Y。通過結構層805的厚度限定深度。在同一蝕刻步驟期間,進一步形成孔808,其例如在平面XY中具有圓形截面和包括在2μm和200μm之間的直徑以及等於結構層805的厚度的深度。在後續製造步驟中,孔808將形成噴嘴13的一部分。
然後(圖18),執行將第三晶圓8耦合至第一晶圓2的步驟。該耦合步驟可以發生在圖15A的步驟之前或之後。
為了利於後續製造步驟的執行,通過熱釋放雙粘合帶將第二晶圓4與又一晶圓耦合,該又一晶圓具有有利於正被製造的設備的操控的唯一功能。該步驟在圖中未示出。在製造處理的結束,所述又一操控晶圓將被去除。操控晶圓例如是矽且具有近似500μm的厚度。熱釋放雙粘合帶例如通過層壓位於所述晶圓上。
參照圖19,晶圓8的襯底801利用研磨步驟和後續的化學蝕刻步驟完全去除,以便去除襯底801沒有被研磨步驟去除的任何可能的殘留物。化學蝕刻進一步表現出比研磨更加精確的優勢,並且可以選擇蝕刻化學劑以關於將被去除的材料具有選擇性,蝕刻停止在界面層803處。
因此,在該步驟中,建議在暴露的界面層803上設置對齊標記(未示出)。所述標記具有在後續處理步驟中高精度地識別孔808的空間布置以完成流體噴射噴嘴的形成的功能。
然後(圖20),執行抗蝕劑掩模810的形成、光刻和光致抗蝕劑掩模810的顯影的步驟,以露出界面層803的將形成噴嘴13的噴射孔的部分,並且最後執行對下覆的界面層803的蝕刻以形成與孔808同軸的通孔812,該通孔812在平面XY中具有圓形截面。
最後,然後去除光致抗蝕劑掩模810,由此完成噴嘴13的形成。由此形成圖1A的設備1。
圖21示出了本實用新型的又一變化。根據該實施例,不存在出口通道9b、中間出口通道11b和第二限制通道18。在這種情況下,噴射設備100類似於圖1A和圖1B的噴射設備1,並且如圖2至圖20所述來製造,除了不執行設想形成出口通道9b、中間出口通道11b和第二限制通道18的步驟。因此,根據該實施例,不考慮流體的循環,在列印/流體噴射的操作步驟期間,在流體被引入室6之後,僅通過噴嘴13從噴射設備100流出。形成噴射設備100的其餘元件與噴射設備1的相同,因此通過相同的參考標號標示並且不再進行描述。
從根據本公開提供的本實用新型的特性來看,所實現的優點是明顯的。
具體地,根據本實用新型的用於製造流體噴射設備的步驟僅要求三個晶圓的耦合,因此降低了未對齊的風險,僅要求晶圓耦合的兩個步驟,並且限制了製造成本。
此外,通過提供限制通道16、18進一步降低了未對齊的風險,其中限制通道16、18的主要延伸在第三晶圓8所在的平面中,即在與從入口孔9a提供流體的方向和從噴嘴13噴射的方向二者垂直的方向上。由此,不需要特殊布置來對具有彼此不同截面的通道進行同軸耦合,而在現有技術的情況下,限制通道16、18的主要延伸與從入口孔提供流體的方向一致。
最後,明顯地,在不背離由權利要求限定的本實用新型的範圍的情況下,可以對本文所述和所示內容進行修改和變化。
具體地,附圖中所述和所示的實施例包括單個噴嘴。實際應用通常要求根據被噴射的流體的量形成多個噴嘴。在這種情況下,噴射設備將通過圖中所述和所表示的類型的多個基礎噴射模塊來形成,該多個基礎噴射模塊彼此相鄰且利用從半導體材料的相同晶圓開始的公共微加工步驟來得到。