一種微反應精餾板製備2,6‑二叔丁基對甲酚的方法及其設備與流程
2023-11-10 15:24:43 5
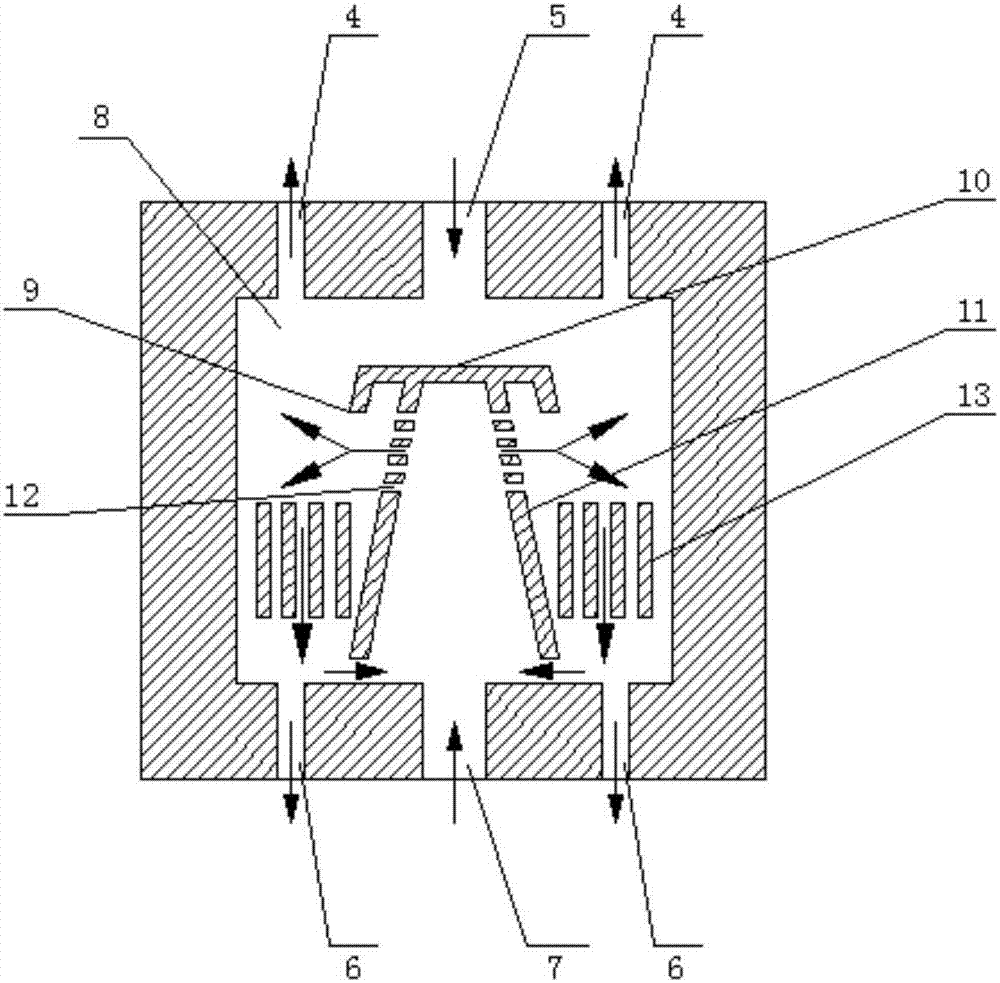
本發明涉及一種製備2,6-二叔丁基對甲酚的工藝方法及其設備,特別是一種微反應精餾板製備2,6-二叔丁基對甲酚的工藝方法及其設備。
背景技術:
2,6-二叔丁基對甲酚是一種優良的通用型酚類抗氧劑,能抑制或延緩塑料、橡膠的氧化降解,廣泛用於各種潤滑油、汽油、石蠟中,也可用作食品抗氧化劑。目前的生產工藝主要為烷基化反應,採用異丁烯、叔丁醇或甲基叔丁基醚等烷基化劑,用濃硫酸、芳磺酸等作為催化劑,在常壓或高壓下反應製備。但傳統的液體酸對設備具有很強的腐蝕性,增加了設備投資,且烷基化後需要進行鹼洗、水洗以除去殘留的酸,產生大量的廢水,生產成本較高。且催化劑不能循環利用,副反應不易控制,產物難以分離。
中國專利CN 1313270 A公開了一種製備2,6-二叔丁基對甲酚的新工藝,採用離子交換樹脂為催化劑,在兩個串聯的反應釜中通入異丁烯進行烷基化反應,直至反應達到終點。但是,這種傳統的反應釜的氣液接觸面積小,反應速率受氣液傳質限制,反應需要時間長,且反應溫度較高,容易加劇異丁烯聚合反應,副產物增多。
中國專利CN 103212438 B公布了一種用於烴化分離間甲酚和對甲酚的催化劑及分離方法,以甲基叔丁基醚為烷基化劑,離子液體為催化劑,能有效抑制副反應,對設備腐蝕性小。但採用離子液體為催化劑,存著成本高、工業化生產難度大等問題。
微化工技術是20世紀90年代以來快速發展起來的化工科技前沿技術,微化工裝置在傳質、傳熱、反應等方面展現出良好的性能,因而逐漸成為研究的熱點。但目前研究的微化工設備形式比較簡單,主要集中在單一微通道、或十字型、Y型交叉微通道等,結構簡單,不能滿足複雜多樣、品種繁多的實際化工生產需求;另一方面,研究者們對於反應與分離的微化工設備研究是分別進行的,沒有結合起來,因此微反應與微精餾裝置的結構、單元耦合方式與物流流動方式、水力學特性等都有待研究。
基於2,6-二叔丁基對甲酚的製備現狀與微化工裝置的優勢,本發明提出了一種微反應精餾板製備2,6-二叔丁基對甲酚的工藝方法及設備。
技術實現要素:
本發明的目的在於針對當前技術中存在的不足,提供一種微反應精餾板製備2,6-二叔丁基對甲酚的方法及設備。該方法採用微反應精餾板為反應裝置,並根據大量研究和實驗,得到了適合裝置的反應參數,使反應精餾裝置內氣液充分接觸,實現高效傳質與傳熱,提高轉化率,並及時移走反應熱。
本發明的技術方案為:
一種微反應精餾板製備2,6-二叔丁基對甲酚的方法,包括以下步驟:
將對甲酚經第一預熱器預熱至70~90℃,進料壓力0.3~1.0MPa下由上方中心通道進入微反應精餾板中;同時,異丁烯經第二預熱器預熱至70~90℃,進料壓力0.3~1.0MPa下由下方中心通道進入微反應精餾板中,對甲酚與異丁烯在微反應精餾板中反應生成液相產物,從微反應精餾板下方側通道採出,液相反應產物經精餾分離可得到2,6-二叔丁基對甲酚,經重結晶、乾燥後得成品;過量異丁烯與低沸點產物從微反應精餾板上方側通道排出;
微反應精餾板內有酸性催化劑;所述酸性催化劑具體為金屬催化劑,具體為V2O5/ZrO2;其中,V2O5的佔金屬催化劑的質量分數為0.1%~0.5%;
對甲酚與異丁烯進料量摩爾比為1:3~4;對甲酚空速為0.2~1.0h-1;
所述的微反應精餾板,包括基板與蓋板及板夾;基板為刻有微腔室的聚二甲基矽氧烷(PDMS)薄板,蓋板為玻璃片,基板與蓋板通過板夾進行鍵合;所述微腔室包括兩個位於微反應精餾板上方的側通道、一個上方中心通道,兩個位於微反應精餾板下方的側通道、一個下方中心通道,和一個中心腔室;
所述的中心腔室的形狀為正方形,邊長為1300~2200μm;中心腔室的深度為80~100μm;
微腔室的上下四個側通道寬度相同,均為80~100μm;
微腔室的上下兩個中心通道寬度相同,均為160~200μm;
所述中心腔室內對稱分布有一個未刻蝕π字形隔板,所述π字形隔板包括一個頂板與兩個支腿,其中,頂板的長度為400~500μm,頂板的寬度為50~100μm,支腿的寬度為50~100μm;
所述的頂板兩端都有下沿,下沿長度為40~50μm,下沿與相鄰支腿平行;
兩個支腿與頂板呈75~90°,所述的兩個支腿最上端在頂板處的間距為200~300μm;
兩個支腿的最底端距中心腔室下內壁距離為80~100μm;
所述支腿,在每個支腿上部刻蝕有四條水平微通道,微通道寬度為40~60μm;最上方的微通道頂端與頂板下沿高度齊平,微通道間距為40~60μm;
π字形隔板的高度為1000~1500μm;
所述π字形隔板的兩個支腿的外側各保留有四個垂直的矩形隔板,矩形隔板長度為400~600μm,寬度為50~100μm;相鄰矩形隔板的間距為50~100μm;最左側矩形隔板距相近內壁尺寸為50~100μm;最右側矩形隔板距相近內壁尺寸為50~100μm;矩形隔板最底端距中心腔室內壁尺寸為160~200μm;
所述矩形隔板側壁四周塗覆有酸性催化劑,所述酸性催化劑塗覆厚度為2~5μm。
基板上的微腔室採用光刻蝕技術在PDMS基板上加工得到,基板與微腔室的壁厚均為2cm;
本發明的有益效果為:
本發明中,通過異丁烯過量,可以提高對甲酚轉化率,過量的異丁烯可帶走反應熱,防止裝置飛溫,保證反應正常進行;反應溫度低,異丁烯自聚反應幾乎不發生,簡化產物精製過程;將酸性催化劑活性組分負載在反應通道內,對設備腐蝕性小,無需鹼洗、水洗,不產生廢水,節省設備投資;相較於傳統反應精餾設備,微反應精餾板的尺寸在微米級,氣液接觸過程中傳質、傳熱梯度大,微設備的比表面積大,提供給氣液兩相的傳質、傳熱面積大,因而傳質、傳熱效率高,促進反應的快速進行和反應熱的快速轉移;相較於傳統微反應精餾設備,微反應精餾板放大過程簡單,通過微設備的並聯可實現處理量的增減,無放大效應。
附圖說明
圖1是本發明所述實施例的微反應精餾板製備2,6-二叔丁基對甲酚的生產工藝圖;
圖2是本發明所述微反應精餾板底板的主視圖;
其中,1,第一預熱器;2,第二預熱器;3,微反應精餾板;4,上方側通道;5,上方中心通道;6,下方側通道;7,下方中心通道;8,中心腔室;9,π字形隔板;10,頂板;11,支腿;12,微通孔;13,矩形隔板。
具體實施方式
根據圖1所示,一種微反應精餾板製備2,6-二叔丁基對甲酚的工藝方法,包括以下步驟:
將對甲酚經第一預熱器1預熱至70~90℃,由上方中心通道5進入微反應精餾板3中,同時,異丁烯經第二預熱器2預熱至70~90℃,由下方中心通道7進入微反應精餾板中,對甲酚與異丁烯在微反應精餾板3中反應生成液相產物,從微反應精餾板下方側通道6採出,液相反應產物經精餾分離可得到2,6-二叔丁基對甲酚,經重結晶、乾燥後得成品;過量異丁烯與低沸點產物從微反應精餾板上方側通道4排出(可收集、處理後循環使用);對甲酚與異丁烯原料的進料壓力為0.3~1.0MPa;微反應精餾板內有酸性催化劑;所述酸性催化劑具體為金屬催化劑,為公知材料,具體為V2O5/ZrO2;其中,V2O5的佔金屬催化劑的質量分數為0.1%~0.5%;對甲酚與異丁烯進料量摩爾比為1:3~4;對甲酚空速為0.2~1.0h-1。
根據圖2所示,一種微反應精餾板製備2,6-二叔丁基對甲酚的設備,為微反應精餾板,包括基板與蓋板及板夾;基板為刻有微腔室的聚二甲基矽氧烷(PDMS)整塊薄板,蓋板為玻璃片,基板與蓋板通過板夾進行鍵合;
所述微腔室包括兩個位於微反應精餾板上方的側通道4、一個上方中心通道5,兩個位於微反應精餾板下方的側通道6、一個下方中心通道7,和一個中心腔室8;所述的中心腔室8的形狀為正方形,邊長為1300~2200μm;中心腔室的深度為80~100μm;微腔室的上下四個側通道4(6)寬度相同,均為80~100μm;微腔室的上下兩個中心通道5(7)寬度相同,均為160~200μm;
所述中心腔室8內對稱分布有一個未刻蝕π字形隔板9,所述π字形隔板包括一個頂板10與兩個支腿11,所述的頂板長度為400~500μm,所述的頂板兩端都有下沿,下沿長度為40~50μm,下沿與相鄰支腿平行;兩個支腿與頂板(形成的銳角)呈75~90°,所述的兩個支腿最上端在頂板處的間距為200~300μm;兩個支腿的最底端距中心腔室下內壁尺寸為80~100μm;所述支腿,在每個支腿上部刻蝕四條水平微通道,微通道寬度為40~60μm;最上方的微通道頂端與頂板下沿高度齊平,微通道間距為40~60μm;π字形隔板的高度為1000~1500μm(所述的π字形隔板的高度是指頂板頂部到支腿底端的尺寸);所述π字形隔板的兩個支腿兩側各保留有四個垂直的矩形隔板13,矩形隔板13長度為400~600μm,寬度為50~100μm;矩形隔板13之間的的間距為50~100μm;最左側矩形隔板距相近內壁的距離為50~100μm;最右側矩形隔板距相近內壁尺寸為50~100μm;矩形隔板最底端距中心腔室內壁的距離為160~200μm;所述矩形隔板側壁四周塗覆有酸性催化劑,所述酸性催化劑塗覆厚度為2~5μm。(微腔室內的π字形隔板9和矩形隔板13中所述的形狀均指它們在中心腔室底部的投影形狀,為未經刻蝕後保留下來的結果,即未刻蝕部分的厚度同中心腔室的深度)
根據圖2所示,對甲酚與異丁烯在微反應精餾板內的流動與反應精餾過程為,對甲酚由上方中心通道5流入微反應精餾板的中心腔室8,在頂板10的作用下進入矩形隔板13間隙中,對甲酚在矩形隔板13表面的酸性催化劑的作用下發生反應,反應生成的液體一部分由支腿底部間隙進入π字形隔板9內部,另一部分液體由下方側通道6流出。進入π字形隔板9內部的液體與來自下方中心通道的異丁烯接觸,進入π字形隔板9內部,新鮮異丁烯與液相進行混合傳質,異丁烯乏氣與反應產生的低沸點副產物汽化聚結,氣液混合物由微通孔12噴出,裹挾著新鮮異丁烯的對甲酚進入矩形隔板間隙進行反應,過量的異丁烯乏氣及低沸點反應產物則由上方側通道4排出。
實施例1:使用上述設備和工藝方法製備2,6-二叔丁基對甲酚,其中:
對甲酚預熱器與異丁烯預熱器預熱溫度為70℃;
原料進料壓力為0.5MPa;
催化劑中V2O5的質量分數為0.1%
催化劑塗覆厚度為2μm;
對甲酚空速為1.0h-1;
對甲酚與異丁烯進料量摩爾比為1:3。
中心腔室的邊長為2200μm;
中心腔室的深度為100μm;
微腔室的上下四個側通道寬度為100μm;
微腔室的上下兩個中心通道寬度為200μm;
π字形隔板的高度為1500μm;
π字形隔板的兩個支腿與π字形隔板的頂板呈80°;
頂板的長度為400μm;
頂板的寬度為50μm,支腿的寬度為50μm;
π字形隔板的頂板兩端下沿長度為40μm;
π字形隔板的兩個支腿最上端間距尺寸為200μm;
π字形隔板的兩個支腿上方的四個微通道寬度為50μm;
π字形隔板的兩個支腿上方的四個微通道的間距為50μm;
π字形隔板最底端距中心腔室內壁尺寸為100μm;
矩形隔板長度為600μm;
矩形隔板的寬度為100μm;
矩形隔板的間距為100μm;
最左側矩形隔板距相近內壁尺寸為100μm;
最右側矩形隔板距相近內壁尺寸為100μm;
矩形隔板最底端距中心腔室內壁尺寸為200μm;
微反應精餾板溫度穩定在76℃;
微反應精餾板採出的液相反應產物中2,6-二叔丁基對甲酚質量分數:82%;對甲酚轉化率:90%
實施例2:使用上述設備和工藝方法製備2,6-二叔丁基對甲酚,其中:
對甲酚預熱器與異丁烯預熱器預熱溫度為70℃;
原料進料壓力為0.5MPa;
催化劑中V2O5的質量分數為0.1%
催化劑塗覆厚度為2μm;
對甲酚空速為1.0h-1;
對甲酚與異丁烯進料量摩爾比為1:4。
中心腔室的邊長為2200μm;
中心腔室的深度為100μm;
微腔室的上下四個側通道寬度為100μm;
微腔室的上下兩個中心通道寬度為200μm;
π字形隔板的高度為1500μm;
π字形隔板的兩個支腿與π字形隔板的頂板呈80°;
頂板的長度為400μm;
頂板的寬度為50μm,支腿的寬度為50μm;
π字形隔板的頂板兩端下沿長度為40μm;
π字形隔板的兩個支腿最上端間距尺寸為200μm;
π字形隔板的兩個支腿上方的四個微通道寬度為50μm;
π字形隔板的兩個支腿上方的四個微通道的間距為50μm;
π字形隔板最底端距中心腔室內壁尺寸為100μm;
矩形隔板長度為600μm;
矩形隔板的寬度為100μm;
矩形隔板的間距為100μm;
最左側矩形隔板距相近內壁尺寸為100μm;
最右側矩形隔板距相近內壁尺寸為100μm;
矩形隔板最底端距中心腔室內壁尺寸為200μm;
微反應精餾板溫度穩定在75℃;
微反應精餾板採出的液相反應產物中2,6-二叔丁基對甲酚質量分數:85%;對甲酚轉化率:93%
實施例3:使用上述設備和工藝方法製備2,6-二叔丁基對甲酚,其中:
對甲酚預熱器與異丁烯預熱器預熱溫度為70℃;
原料進料壓力為0.5MPa;
催化劑中V2O5的質量分數為0.1%
催化劑塗覆厚度為2μm;
對甲酚空速為0.5h-1;
對甲酚與異丁烯進料量摩爾比為1:4。
中心腔室的邊長為2200μm;
中心腔室的深度為100μm;
微腔室的上下四個側通道寬度為100μm;
微腔室的上下兩個中心通道寬度為200μm;
π字形隔板的高度為1500μm;
π字形隔板的兩個支腿與π字形隔板的頂板呈80°;
頂板的長度為400μm;
頂板的寬度為50μm,支腿的寬度為50μm;
π字形隔板的頂板兩端下沿長度為40μm;
π字形隔板的兩個支腿最上端間距尺寸為200μm;
π字形隔板的兩個支腿上方的四個微通道寬度為50μm;
π字形隔板的兩個支腿上方的四個微通道的間距為50μm;
π字形隔板最底端距中心腔室內壁尺寸為100μm;
矩形隔板長度為600μm;
矩形隔板的寬度為100μm;
矩形隔板的間距為100μm;
最左側矩形隔板距相近內壁尺寸為100μm;
最右側矩形隔板距相近內壁尺寸為100μm;
矩形隔板最底端距中心腔室內壁尺寸為200μm;
微反應精餾板溫度穩定在73℃;
微反應精餾板採出的液相反應產物中2,6-二叔丁基對甲酚質量分數:92%;對甲酚轉化率:97%
實施例4:使用上述設備和工藝方法製備2,6-二叔丁基對甲酚,其中:
對甲酚預熱器與異丁烯預熱器預熱溫度為80℃;
原料進料壓力為0.5MPa;
催化劑中V2O5的質量分數為0.1%
催化劑塗覆厚度為2μm;
對甲酚空速為0.3h-1;
對甲酚與異丁烯進料量摩爾比為1:4。
中心腔室的邊長為2200μm;
中心腔室的深度為100μm;
微腔室的上下四個側通道寬度為100μm;
微腔室的上下兩個中心通道寬度為200μm;
π字形隔板的高度為1500μm;
π字形隔板的兩個支腿與π字形隔板的頂板呈80°;
頂板的長度為400μm;
頂板的寬度為50μm,支腿的寬度為50μm;
π字形隔板的頂板兩端下沿長度為40μm;
π字形隔板的兩個支腿最上端間距尺寸為200μm;
π字形隔板的兩個支腿上方的四個微通道寬度為50μm;
π字形隔板的兩個支腿上方的四個微通道的間距為50μm;
π字形隔板最底端距中心腔室內壁尺寸為100μm;
矩形隔板長度為600μm;
矩形隔板的寬度為100μm;
矩形隔板的間距為100μm;
最左側矩形隔板距相近內壁尺寸為100μm;
最右側矩形隔板距相近內壁尺寸為100μm;
矩形隔板最底端距中心腔室內壁尺寸為200μm;
微反應精餾板溫度穩定在82℃;
微反應精餾板採出的液相反應產物中2,6-二叔丁基對甲酚質量分數:92%;
對甲酚轉化率:99%
由此可見,採用微反應精餾板製備2,6-二叔丁基對甲酚,儘管烷基化反應是放熱反應,但由於異丁烯過量,且裝置傳熱速率快,反應過程中裝置只有小幅度溫升,且溫度穩定,不會發生飛溫現象;通過分析反應產物可知,對甲酚轉化率高,2,6-二叔丁基對甲酚收率高。
本發明未盡事宜未公知技術。