一種電弧增材製造有限元建模方法與流程
2024-02-11 01:17:15 3
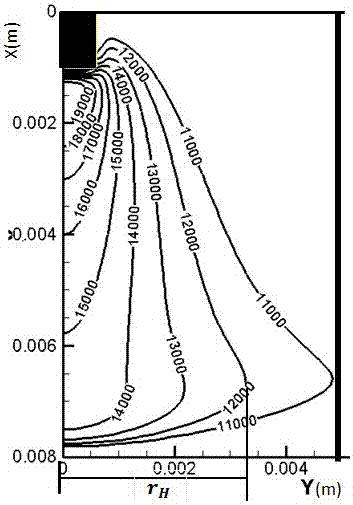
本發明涉及電弧增材製造領域,具體涉及一種電弧增材製造有限元建模方法。
背景技術:
近年來,增材製造技術作為新興技術發展迅速,不斷地被應用於工業生產中。成形材料由最初的光固化樹脂不斷地向金屬材料發展,成形結構也向著大型化整體化發展。採用電弧作為熱源的電弧增材製造,具有熱輸入高,成形速度快,成本低,設備簡單等特點,非常適用於大型化整體化結構件,包括大型模具、大型航空發動機、大型飛機壁板等。但是,電弧增材製造過程還存在許多成形缺陷,同時成形過程的物理機理還尚未完成探明。依靠傳統的工業試驗方法研究成形過程物理機理,不僅存在一定盲目性,而且效率低,耗費生產成本,更棘手的是有些物理參數試驗難以獲得或者不能獲得。因此,採用有限元數值模擬方法研究電弧增材製造自然而然成為大多數學者的選擇。
電弧增材製造有限元數值模擬方法的一般步驟包括幾何建模、網格劃分、材料參數加載,增材區域及增材路徑定義、邊界條件及熱源模型定義、計算求解。因此,在電弧增材製造有限元建模之前需要明確增材區域尺寸、材料參數以及電弧增材工藝參數,但是增材區域尺寸在電弧增材製造實驗之前是個未知數,傳統的建模方法必須在實驗之後才能給出增材區域的尺寸參數,以這種方式建模則違背了數值模擬的原則。雖然,現有的有限元軟體在建模之前無能為力,但是其它的流體動力學模擬軟體的模擬結果可以為有限元建模提供必要參數。
綜上所述,利用流體動力學模擬軟體率先進行電弧形態和熔滴形態模擬,得出增材區域寬度和高度,實現電弧增材製造有限元建模,對電弧增材製造數值模擬研究以及物理機理研究具有重要的意義。特別是在目前國內增材製造的工業背景下,研究電弧增材製造物理機理以及實現電弧增材製造建模具有一定的迫切性。
技術實現要素:
本發明所要解決的技術問題是針對上述現有技術的不足提供一種電弧增材製造有限元建模方法,本電弧增材製造有限元建模方法以期準確預測增材區域生死單元的寬度和深度,使電弧增材製造能夠順利建模。同時,還採用實驗方法,確定測溫點位置,驗證溫度場模型,然後根據相對誤差修正模型,直至獲得準確的有限元模型,提高計算機模擬的計算精度。
為實現上述技術目的,本發明採取的技術方案為:
一種電弧增材製造有限元建模方法,包括以下步驟:
步驟1:計算電弧形態,確定增材區域生死單元寬度;
步驟2:計算熔滴形態,確定增材區域生死單元高度;
步驟3:根據增材區域生死單元寬度和增材區域生死單元高度建立電弧增材製造有限元幾何模型;
步驟4:通過驗證電弧增材製造有限元幾何模型的溫度分布,進而修正電弧形態和熔滴形態,從而修正電弧增材製造有限元幾何模型。
作為本發明進一步改進的技術方案,所述步驟1包括以下步驟:
(1)定義電弧增材製造初始工藝參數,材料熱物性參數,電勢邊界條件;
(2)根據電流連續方程及歐姆定律求解軸向和徑向的電流密度:
其中σ是電弧的材料電導率,z是軸向坐標,r是徑向坐標,是電勢,jz是軸向的電流密度,jr是徑向的電流密度;
根據安培環流定律求解電弧自感應磁場強度:
其中μ0是真空磁導率,b0是電弧自感應磁場強度;
根據軸向的電流密度jz、徑向的電流密度jr以及公式(5)的能量方程,求解能量方程中的熱量源項q,熱量源項q為電阻熱和電子流傳遞熱之和:
其中kb是玻爾茲曼常數,e是電子電荷,t為電弧形態的溫度場,q是熱量源項;
根據電弧自感應磁場強度b0、軸向的電流密度jz、徑向的電流密度jr以及動量守恆方程,求解動量守恆方程中的動量源項:
fz=jr×b0+ρg(6),
fr=-jz×b0(7),
其中ρ是電弧的材料密度,g是重力加速度,fz是指電弧的軸向電磁力,fr是指電弧的徑向電磁力,fz和fr均屬於電弧的動量源項;
根據動量方程和連續性方程,求解電弧的軸向速度場和電弧的徑向速度場:
其中u是電弧的軸向速度場,v是電弧的徑向速度場,t是時間,p是壓強,μ是材料黏性係數,其中公式(8)為軸向動量方程,公式(9)為徑向動量方程,公式(10)是質量連續性方程,公式(10)是對壓強p的修正;
根據熱量源項q、電弧的軸向速度場u和電弧的徑向速度場v並結合能量方程確定電弧形態的溫度的分布t:
其中cp是電弧的材料等壓比熱容,k是電弧的材料熱導率,t為電弧形態的溫度場;
(3)根據電弧形態的溫度場t獲得加熱斑點半徑rh,則增材區域生死單元寬度為2rh。作為本發明進一步改進的技術方案,所述步驟2包括以下步驟:
(1)確定熔滴的表面張力、重力、電磁力和等離子體流力:
fγ=2πrγ(12),
其中r是焊絲半徑,γ是熔滴表面張力係數,fγ為熔滴的表面張力;
其中g是重力加速度,ρ是熔滴的材料密度,fg為熔滴的重力;
其中表示電流密度,表示磁感應強度的矢量,fm為熔滴的電磁力;
其中cd是等離子流係數,ap是等離子流力作用面積,ρf是等離子流密度,vf是等離子流的速度,fp為熔滴的等離子體流力;
(2)將熔滴的表面張力、重力、電磁力和等離子體流力在徑向的分力表示為fr1,熔滴的表面張力、重力、電磁力和等離子體流力在軸向的分力表示為fz1,fr1和fz1為熔滴的動量源項;
(3)將fr1代替步驟1中的fr,fz1代替步驟1中的fz,帶入步驟1中的公式(8)、公式(9)和公式(10)求解熔滴的軸向速度場u1和熔滴的徑向速度場v1;
(4)使用vof模型,對熔滴運動過程自由界面行為進行追蹤:
其中f是單元格流體體積分數;
(5)根據求解的熔滴形態即單元格流體體積分數f,獲得熔滴半徑rd,則增材區域生死單元高度
作為本發明進一步改進的技術方案,所述步驟3包括以下步驟:
(1)根據實際基板幾何尺寸,構建基板幾何模型;
(2)根據增材區域生死單元寬度增材區域生死單元高度以及增材區域長度l構建增材區域生死單元幾何模型;
(3)對基板幾何模型和增材區域生死單元幾何模型進行網格劃分。
作為本發明進一步改進的技術方案,所述步驟4包括以下步驟:
(1)加載電弧增材製造的初始條件;
(2)加載雙橢球熱源模型,定義熱邊界條件和換熱邊界條件,熱邊界條件包括環境初始溫度以及裝夾條件,換熱邊界條件包括環境初始溫度、換熱單元以及裝夾條件:
公式(17)中qf(x,y,z)為前半橢球的熱流密度值,公式(17)中的a和b分別表示前半橢球的長度和深度,cf表示前半橢球的寬度,ff是前半橢球的熱量分配係數,公式(18)中qr(x,y,z)為後半橢球的熱流密度值,公式(18)中的a和b分別表示後半橢球的長度和深度,cr表示後半橢球的寬度,fr是後半橢球的熱量分配係數,公式(17)和公式(18)中x,y,z是三維方向的坐標,q2是增材製造熱輸入,e是自然數,fr和ff滿足條件:
fr+ff=2(19);
(3)根據導熱偏微分方程,得到電弧增材製造過程的溫度場tc:
其中cp是增材材料的材料等壓比熱容,ρ是增材材料的材料密度,k是增材材料的材料熱導率,為內熱源強度;
(4)在基板上選取5個紅外測溫點,沿增材區域的起弧處的垂直方向10mm處取第一紅外測溫點,沿增材區域的收弧處的垂直方向10mm處取第二紅外測溫點,再在第一紅外測溫點和第二紅外測溫點之間選取3個紅外測溫點,每個相鄰的紅外測溫點之間的距離均為l/4,l為增材區域長度;
(5)將測量的溫度分布表示為tt並記錄測溫時間,將測溫時間作為冷卻時間,進而確定模擬的冷卻時間的依據,電弧增材製造冷卻過程的模擬時間大於記錄測溫時間;
(6)提取模擬溫度場結果與實驗測量結果,計算相對誤差:
其中tc是步驟(3)模擬的電弧增材製造過程的溫度場結果、tt是步驟(5)實驗測溫結果;
(7)預先設定相對誤差範圍,若步驟(6)獲得的相對誤差結果不在預先設定的相對誤差範圍之內,則修正增材區域生死單元寬度和增材區域生死單元高度進而修正前半橢球的長度、深度和寬度以及後半橢球的長度、深度和寬度,直至獲得的模擬溫度場結果與實驗測量結果在預先設定的相對誤差範圍內,最終確定增材區域生死單元幾何模型。
本發明與現有技術相比,有益效果為:本發明針對電弧增材製造有限元建模前無法預先確定增材區域幾何尺寸建模問題,採用電弧形態模擬技術以及熔滴形態模擬技術,可以準確獲得增材區域生死單元寬度和增材區域生死單元高度的幾何尺寸;本發明可以在電弧增材製造實驗前,確定增材區域生死單元寬度與高度,減少電弧增材製造數值模擬過程不必要的實驗量;本發明通過數值模擬與實驗驗證相結合的方法,驗證模擬獲得的溫度場,不斷修正模型,直至獲得準確的有限元模型,提高計算機模擬的計算精度。
附圖說明
圖1為本發明的流程示意圖。
圖2為本發明的電弧增材製造過程電弧形態與加熱斑點半徑的結構示意圖。
圖3為本發明的電弧增材製造過程熔滴形態與熔滴半徑的結構示意圖。
圖4為本發明的電弧增材製造有限元幾何模型的結構示意圖。
圖5為本發明的溫度場實驗驗證測溫點位置的結構示意圖。
圖6為本發明的電弧增材製造幾何尺寸的結構示意圖。
圖7為本發明的電弧增材製造溫度場模擬結果的結構示意圖。
具體實施方式
下面根據圖1對本發明的具體實施方式作出進一步說明:
本發明提出一種電弧增材製造有限元建模方法,電弧增材製造模擬過程結合電弧形態模擬技術、熔滴形態模擬技術和有限元模擬技術,並加以實驗驗證,能夠在電弧增材製造有限元建模之前確定增材區域生死單元幾何尺寸,實現電弧增材製造有限元模擬準確計算,主要流程如圖1所示。本發明通過以下步驟實現:
步驟1:計算電弧形態,確定增材區域生死單元寬度;
步驟2:計算熔滴4形態,確定增材區域生死單元高度;
步驟3:根據增材區域生死單元寬度和增材區域生死單元高度建立電弧增材製造有限元幾何模型;
步驟4:通過驗證電弧增材製造有限元幾何模型的溫度分布,進而修正電弧形態和熔滴形態,從而修正電弧增材製造有限元幾何模型。
所述步驟1包括以下步驟:
(1)定義電弧增材製造初始工藝參數,材料熱物性參數,電勢邊界條件;
(2)根據電流連續方程及歐姆定律求解電弧的軸向和徑向的電流密度:
其中σ是電弧的材料電導率,z是軸向坐標,r是徑向坐標,是電勢,jz是軸向的電流密度,jr是徑向的電流密度;
根據安培環流定律求解電弧自感應磁場強度:
其中μ0是真空磁導率,r是徑向坐標,b0是電弧自感應磁場強度;
根據軸向的電流密度jz、徑向的電流密度jr以及公式(5)的能量方程,求解能量方程中的熱量源項q,熱量源項q為電阻熱和電子流傳遞熱之和:
其中kb是玻爾茲曼常數,e是電子電荷,t為電弧形態的溫度場;
根據電弧自感應磁場強度b0、軸向的電流密度jz、徑向的電流密度jr以及動量守恆方程,求解動量守恆方程中的動量源項:
fz=jr×b0+ρg(6),
fr=-jz×b0(7),
其中ρ是電弧中氣體的材料密度,g是重力加速度,fz是指電弧的軸向電磁力,fr是指電弧的徑向電磁力,fz和fr均屬於電弧的動量源項;
根據動量方程和連續性方程,求解電弧的軸向速度場u和電弧的徑向速度場v:
其中u是電弧的軸向速度場,v是電弧的徑向速度場,t是時間,p是壓強,μ是材料黏性係數,其中公式(8)為軸向動量方程,公式(9)為徑向動量方程,公式(10)是質量連續性方程,公式(10)是對壓強p的修正;
根據熱量源項q、電弧的軸向速度場u和電弧的徑向速度場v並結合能量方程確定電弧形態的溫度的分布t:
其中cp是電弧的材料等壓比熱容,k是電弧的材料熱導率,t為電弧形態的溫度場;
(3)參見圖2,根據電弧形態的溫度場t獲得加熱斑點半徑rh,則增材區域生死單元寬度為
所述步驟2包括以下步驟:
(1)確定熔滴4的表面張力、重力、電磁力和等離子體流力:
fγ=2πrγ(12),
其中r是焊絲半徑,γ是熔滴4表面張力係數,fγ為熔滴4的表面張力;
其中g是重力加速度,ρ是熔滴4的材料密度,fg為熔滴4的重力;
其中表示電流密度,表示磁感應強度的矢量,fm為熔滴4的電磁力;
其中cd是等離子流係數,ap是等離子流力作用面積,ρf是等離子流密度,vf是等離子流的速度,fp為熔滴4的等離子體流力;
(2)將熔滴4的表面張力、重力、電磁力和等離子體流力在徑向的分力表示為fr1,熔滴4的表面張力、重力、電磁力和等離子體流力在軸向的分力表示為fz1,fr1和fz1為熔滴4的動量源項;
(3)將fr1代替步驟1中的fr,fz1代替步驟1中的fz,帶入步驟1中的公式(8)、公式(9)和公式(10)求解熔滴4的軸向速度場u1和熔滴4的徑向速度場v1;
(4)使用vof模型,對熔滴4運動過程自由界面行為進行追蹤:
其中f是單元格流體體積分數;
(5)根據求解的熔滴4形態即界面的單元格流體體積分數f,獲得熔滴4半徑rd,則增材區域生死單元高度參見圖3;其中熔滴4界面處流體體積分數f的範圍為0~1,熔滴4中f為1,其他區域f為0,所以根據熔滴4界面處流體體積分數f的值可計算熔滴4界面的曲率,即可獲得熔滴4半徑rd。
所述步驟3包括以下步驟:
(1)根據實際基板2幾何尺寸,構建基板2幾何模型;
(2)參見圖4,根據增材區域生死單元寬度增材區域生死單元高度以及增材區域長度l構建增材區域生死單元幾何模型1;
(3)參見圖6,對基板2幾何模型和增材區域生死單元幾何模型1進行網格劃分。
所述步驟4包括以下步驟:
(1)加載電弧增材製造的初始條件;
(2)加載雙橢球熱源模型,定義熱邊界條件和換熱邊界條件,熱邊界條件包括環境初始溫度以及裝夾條件,換熱邊界條件包括環境初始溫度、換熱單元以及裝夾條件:
公式(17)中qf(x,f,z)為前半橢球的熱流密度值,公式(17)中的a和b分別表示前半橢球的長度和深度,cf表示前半橢球的寬度,ff是前半橢球的熱量分配係數,公式(18)中qr(x,y,z)為後半橢球的熱流密度值,公式(18)中的a和b分別表示後半橢球的長度和深度,cr表示後半橢球的寬度,fr是後半橢球的熱量分配係數,公式(17)和公式(18)中x,y,z是三維方向的坐標,q2是增材製造熱輸入,q=kui,是焊接效率、電壓和電流的乘積,k是焊接效率,e是自然數,fr和ff滿足條件:
fr+ff=2(19);
(3)根據電弧增材製造的初始條件、熱邊界條件、換熱邊界條件和導熱偏微分方程,得到電弧增材製造過程的溫度場tc:
其中cp是增材材料的材料等壓比熱容,ρ是增材材料的材料密度,k是增材材料的材料熱導率,為內熱源強度;
(4)參見圖5,在基板2上選取5個紅外測溫點3,沿增材區域的起弧處的垂直方向10mm處取第一個紅外測溫點3,沿增材區域的收弧處的垂直方向10mm處取第二個紅外測溫點3,再在第一個紅外測溫點3和第二個紅外測溫點3之間選取3個紅外測溫點3,每個相鄰的紅外測溫點3之間的距離均為l/4,l為增材區域長度;
(5)將測量的溫度分布表示為tt並記錄測溫時間,將測溫時間作為冷卻時間,進而確定模擬的冷卻時間的依據,電弧增材製造冷卻過程的模擬時間大於記錄測溫時間;
(6)提取模擬溫度場結果與實驗測量結果,計算相對誤差:
其中tc是步驟(3)模擬的電弧增材製造過程的溫度場結果,tt是步驟(5)實驗測溫結果;
(7)預先設定相對誤差範圍,若步驟(6)獲得的相對誤差結果不在預先設定的相對誤差範圍之內,則修正增材區域生死單元寬度和增材區域生死單元高度進而修正前半橢球的長度、深度和寬度以及後半橢球的長度、深度和寬度,直至獲得的模擬溫度場結果與實驗測量結果在預先設定的相對誤差範圍內,最終確定增材區域生死單元幾何模型1。
下面以基板2為q235鋼,電弧增材h13熱作模具鋼的模擬進行分析。
對於建立電弧增材製造有限元模型,現以h13熱作模具鋼為例,基板2採用q235鋼,根據實際的電弧增材製造過程,確定電弧增材製造初始工藝參數,如表1所示。
表1h13電弧增材製造工藝參數
電弧形態及熔滴4形態模擬採用的材料熱物性參數如表2所示,由於處於電弧狀態,氬氣的材料參數都是以10000k下的材料參數為基準。參考電弧增材製造過程的實際情況,對計算機模擬的時間、空間進行離散。主要指定義模擬的時間步長(10-6s),網格尺寸(0.1mm*0.1mm)。
表2電弧形態及熔滴4形態模型中採用的材料熱物性參數
步驟a:針對氬氣保護氣體以及相應的工藝參數,求解步驟1中的偏微分方程組,包括能量方程、動量方程以及質量連續方程,求解獲得電弧溫度分布狀態,根據電弧溫度分布狀態確定電弧能量範圍rh,這個範圍根據電弧溫度來判斷,一般要求電弧溫度高於12000,進而確定增材區域生死單元寬度(如圖2所示),其中步驟1求解的電弧溫度分布狀態採用的是氬氣的材料熱物性參數;
步驟b:針對h13熱作模具鋼焊絲相應的工藝參數,求解步驟2中的偏微分方程組,特別注意自由界面追蹤vof模型求解,求解獲得熔滴4形態,根據熔滴4進入熔池5形態,確定熔滴4半徑rd,進而確定增材區域生死單元高度參見圖3,其中步驟2求解的熔滴4形態採用的是h13的材料熱物性參數;
步驟c:建立電弧增材製造幾何模型,其中基板2尺寸為250mm*150mm*4mm,根據增材區域生死單元寬度2rh、增材區域生死單元高度2rd以及增材長度l構建增材區域生死單元幾何模型1,如圖4和圖6所示。
步驟d:針對q235基板和h13增材材料,加載電弧增材製造初始條件、加載雙橢球熱源模型,定義熱邊界條件和換熱邊界條件,包括環境初始溫度、換熱單元以及裝夾條件等,求解步驟四中溫度場微分方程組,獲得最終電弧增材製造過程的溫度場結果(參見圖7,其中黑色的部分是基板,基板上的長方體是增材區域,漸變色是溫度場),如圖5所述,選取基板2上5個紅外測溫點,在長度方向選取五個點進行測溫,將測量的溫度分布表示為tt並記錄測溫時間,將測溫時間作為冷卻時間,進而確定模擬的冷卻時間的依據,電弧增材製造冷卻過程的模擬時間大於記錄測溫時間;本例子根據驗證實驗確定能接受的相對誤差為30%,若結果不在誤差範圍之內則修正電弧形態模型以及熔滴形態模型,直至獲得能接受的結果。
本發明針對電弧增材製造有限元建模前無法預先確定增材區域幾何尺寸建模問題,採用電弧形態模擬技術以及熔滴形態模擬技術,可以準確獲得增材區域生死單元寬度和增材區域生死單元高度的幾何尺寸;本發明可以在電弧增材製造實驗前,確定增材區域生死單元寬度與高度,減少電弧增材製造數值模擬過程不必要的實驗量;本發明通過數值模擬與實驗驗證相結合的方法,驗證模擬獲得的溫度場,不斷修正模型,直至獲得準確的有限元模型,提高計算機模擬的計算精度。
本發明的保護範圍包括但不限於以上實施方式,本發明的保護範圍以權利要求書為準,任何對本技術做出的本領域的技術人員容易想到的替換、變形、改進均落入本發明的保護範圍。