一種內鏈節全自動壓裝設備的製作方法
2024-03-30 04:54:05
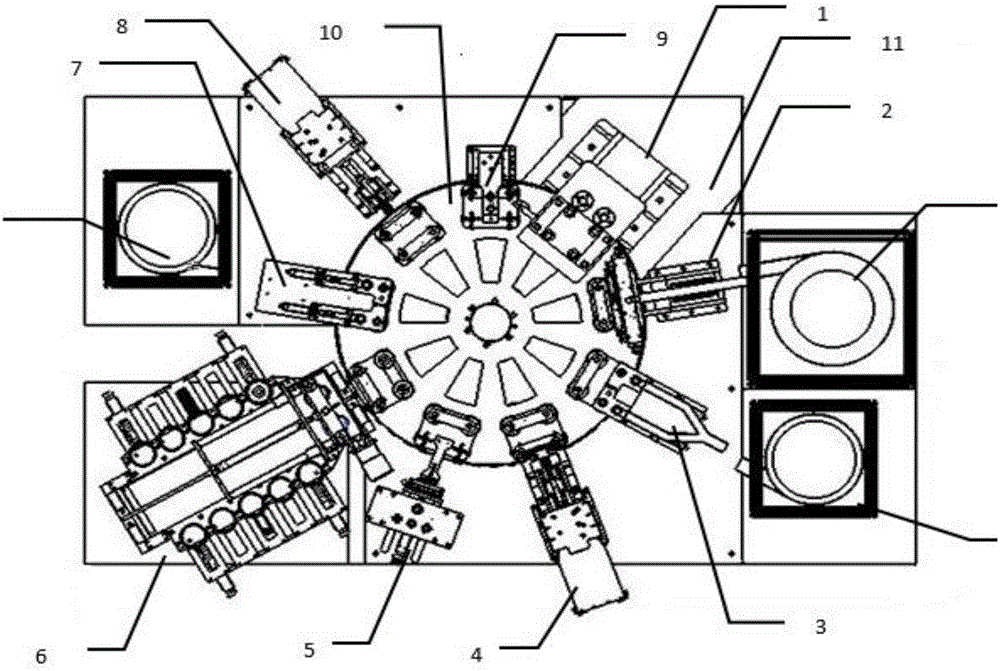
本發明屬於機械自動化設備領域,具體涉及一種內鏈節全自動壓裝設備。
背景技術:
內鏈節是由套筒,外墊圈,內墊圈,滾輪,外鏈板,內鏈板構成,傳統的工作模式採用人工或多臺設備分別將內鏈節的各部件組裝在一起,存在組裝效率低,產品質量不穩定,產量低,工位長期重複組裝會造成工人的眼睛疲勞等問題,事故率高,每個工位的維修也十分費勁,維修時間較長,這就迫切需要一種全自動化的裝配系統來提高它的安全性和生產效率。
因此,設計一種內鏈節全自動壓裝設備,模塊化設計,功能獨立,具有檢修維護方便,自動化程度高,勞動力強度低,降低成本,操作簡單,產量高的優點是本領域需要解決的技術問題。
技術實現要素:
本發明要解決的技術問題:設計一種內鏈節全自動壓裝設備,模塊化設計,功能獨立,具有檢修維護方便,自動化程度高,勞動力強度低,降低成本,操作簡單,產量高的優點
為解決上述技術問題,本發明技術方案如下:
一種內鏈節全自動壓裝設備:包括主傳動機構,主轉盤,機座,9個上料機構,9個送料裝置,所述主傳動機構由帶制動電機,渦輪蝸杆減速機,高精度凸輪分割器組成,所述主轉盤位於所述凸輪分割器的上方,所述9個上料機構迴轉式分布於主轉盤外圍,固定於機座上,所述9個送料裝置迴轉式固定於主轉盤之上,所述9個上料機構包括油缸壓裝機構,套筒上料機構,外墊圈上料機構,內墊圈上料機構,鏈板上料機構,所述鏈板上料機構包含兩套,內層鏈板上料機構,外層鏈板上料機構,半成品翻轉機構,滾輪上料機構,成品下料機構,所述9個送料裝置由第一送料裝置,第二送料裝置,第三送料裝置,第四送料裝置,第五送料裝置,第六送料裝置,第七送料裝置,第八送料裝置,第九送料裝置組成。
優選的,所述油缸壓裝機構包括支架,安裝底座,液壓缸,調節壓板,壓裝板,所述液壓缸為125mm,液壓系統的額定壓力為14mpa,通過調節螺母來調整調節壓板的下壓高度,通過油缸壓裝機對每個零件進行壓裝,所述油缸壓裝機構與第一送料裝置相配合。
優選的,所述套筒上料機構,由套筒料道,套筒推料雙向氣缸,調節螺杆,套筒導向孔,調節螺母,支架,安裝底座構成,套筒推料氣缸左右設有調節螺杆,所述套筒料道的入口與第一送料振動盤出料口連接,通過套筒雙向氣缸拉動箱體內部錯位板,使重疊的兩零件自由落入導向孔內,落入與該機構配合的第二送料裝置上。
優選的,所述外墊圈上料機構,由支架,安裝底座,外墊圈推料板,外墊圈料道,外墊圈落料孔,外墊圈推料氣缸,外墊圈儲料筒構成,所述外墊圈料道與第二送料振動盤出料口連接,通過外墊圈推料氣缸將外墊圈推送至第三送料配合裝置上,所述推料氣缸與外墊圈料道平行,所述推料板設於推送氣缸前端,儲料筒後面,所述外墊圈上料機構與第三送料裝置相配合。
優選的,所述外鏈板上料機構,由外鏈板推料板,外鏈板上料板,外鏈板推料氣缸,外鏈板上料機構安裝底座,支架,與送料裝置相配合的安裝組件,所述外鏈板推料氣缸與推料板連接,位於推料板下方,所述上料板分布於外鏈板上料機構兩側,垂直於推料板,所述上料板上設置了3條料道,所述內鏈板上料機構與外鏈板上料機構結構相同,分別與第四送料裝裝置,第八送料裝置向配合。
優選的,所述半成品翻轉機構,由支架,安裝底座,轉臂,位於轉臂前部的電磁鐵,位於轉臂中間的旋轉缸,位於轉臂尾部的推送氣缸,調節螺杆,所述調節螺杆通過面板垂直於轉臂之上,與轉臂連接,調節螺杆的上部設有調節螺母,通過調節螺杆上的螺母來調節下壓的行程,轉臂前端電磁鐵處施加的壓力不得大於3kg,所述半成品翻轉機構與第五送料裝置相配合。
優選的,所述滾輪上料機構,由支架,安裝底座,碼料桶,雙排推料組件,調節螺釘,滾輪推料氣缸,皮帶輸送機,取料頭組件構成,碼料桶與支架垂直,所述滾輪上料機構與第六送料裝置相配合。
優選的,所述內墊圈上料機構與第七送料裝置相配合。
優選的,所述外墊圈上料板的推料板為為Y型結構。
優選的,所述內鏈節全自動壓裝設備適用於節距主尺寸為133.17mm內鏈節,所述9個送料裝置,每個送料裝置之間間距為40°角固定於主轉盤上。
通過上述技術方案,本發明的一種內鏈節全自動壓裝設備,其有益效是:通過高精度凸輪分割器,主轉盤外圍的9個上料機構,對位於主轉盤上的9送料裝置精準的定位,實現全自動化組裝,減少人員的投入,降低生產成本,功能的獨立可以帶來維修成本和維修時間的降低,在降低了生產成本的基礎上,還能提高生產產量。
附圖說明
為了更清楚地說明本發明實施例或現有技術中的技術方案,下面將對實施例或現有技術描述中所需要使用的附圖作簡單地介紹,顯而易見地,下面描述中的附圖僅僅是本發明的一些實施例,對於本領域普通技術人員來講,在不付出創造性勞動的前提下,還可以根據這些附圖獲得其他的附圖。
圖1為本發明一種內鏈節全自動壓裝設備的示意圖;
圖2為主傳動機構立體結構示意圖
圖3為鏈板上料機構立體結構示意圖
圖4為墊圈上料機構立體結構示意圖圖
圖5為套筒上料機構立體結構示意圖圖
圖6為油缸壓裝機構立體結構示意圖
圖7為半成品翻轉機構立體結構示意圖
圖8滾輪上料機構立體結構示意圖
具體實施方式
下面將結合本發明實施例中的附圖,對本發明實施例中的技術方案進行清楚、完整地描述,顯然,所描述的實施例僅僅是本發明一部分實施例,而不是全部的實施例。
參考圖1,圖2,圖3,圖4,圖5,圖6,圖7,圖8,一種內鏈節全自動壓裝設備,包括主傳動機構,主轉盤10,機座11,9個上料機構,所述主傳動機構由帶制動電機11-3,渦輪蝸杆減速機11-2,高精度凸輪分割器11-1組成,所述主轉盤位於所述凸輪分割器的上方,所述9個上料機構包括油缸壓裝機構1套筒上料機構2,外墊圈上料機構3,內墊圈上料機構7,鏈板上料機構,所述鏈板上料機構包含兩套,內層鏈板上料機構8,外層鏈板上料機構4,半成品翻轉機構5,滾輪上料機構6,成品下料機構9,所述9個送料裝置由第一送料裝置1-20,第二送料裝置2-20,第三送料裝置3-20,第四送料裝置4-20,第五送料裝置5-20,第六送料裝置6-2,第七送料裝置7-20,第八送料裝置8-20,第九送料裝置9-20組成。
所述油缸壓裝機構包括支架1-5,安裝底座1-4,液壓缸,調節壓板1-2,調節螺母1-1,壓裝板1-3,所述液壓缸為125mm,液壓系統的額定壓力為14mpa,通過調節螺母來調整調節壓板的下壓高度,通過油缸壓裝機對每個零件進行壓裝,所述油缸壓裝機構與第一送料裝置相配合。所述油缸壓裝機構包括支架1-5,安裝底座1-4,液壓缸,調節壓板1-2,調節螺母1-1,壓裝板1-3,所述液壓缸為125mm,液壓系統的額定壓力為14mpa,通過調節螺母來調整調節壓板的下壓高度,通過油缸壓裝機對每個零件進行壓裝,所述油缸壓裝機構與第一送料裝置相配合。
所述套筒上料機構,由套筒料道2-1,套筒推料雙向氣缸2-5,調節螺杆2-6,套筒導向孔2-4,支架2-2,安裝底座2-3構成,套筒推料氣缸左右設有調節螺杆,所述套筒料道的入口與第一送料振動盤出料口連接,通過套筒雙向氣缸拉動箱體內部錯位板,使重疊的兩零件自由落入導向孔內,落入與該機構配合的第二送料裝置2-20上。
所述外墊圈上料機構,由支架3-4,安裝底座3-5,外墊圈推料板3-3,外墊圈料道3-1,外墊圈落料孔3-7,外墊圈推料氣缸3-2,外墊圈儲料筒3-6構成,所述外墊圈料道3-1與第二送料振動盤3-10出料口連接,通過外墊圈推料氣缸3-2將外墊圈推送至第三送料裝置3-20上,所述推料氣缸3-2與外墊圈料道3-1平行,所述推料板3-3設於推送氣缸3-2前端,儲料筒3-6後面,所述外墊圈上料機構3與第三送料裝置3-20相配合,所述外墊圈上料板的推料板為Y型結構。
所述外鏈板上料機構,由外鏈板推料板4-6,外鏈板上料板4-1,外鏈板推料氣缸4-5,外鏈板上料機構安裝底座4-4,支架4-3,與送料裝置相配合的安裝組件4-2,所述外鏈板推料氣缸4-5與推料板4-6連接,位於推料板4-6下方,所述上料板分布於外鏈板上料機構兩側,垂直於推料板4-6,所述上料板上設置了3條料道,所述內鏈板上料機構與外鏈板上料機構結構相同,分別與第四送料裝裝置,第八送料裝置向配合。
所述半成品翻轉機構5,由支架5-5,安裝底座5-6,轉臂5-3,位於轉臂前部的電磁鐵5-4,位於轉臂5-3中間的旋轉缸5-2,位於轉臂尾部的推送氣缸5-7,調節螺杆5-1,所述調節螺杆通過面板5-8垂直於轉臂5-3之上,與轉臂5-3連接,調節螺杆5-1的上部設有調節螺母5-9,通過調節螺杆上的螺母5-9來調節下壓的行程,轉臂前端電磁鐵5-4處施加的壓力不得大於3kg,所述半成品翻轉機構5與第五送料裝置5-20相配合。
所述滾輪上料機構6,由支架6-7,安裝底座6-4,碼料桶6-1,雙排推料組件,調節螺釘6-6,滾輪推料氣缸6-5,皮帶輸送機6-3,取料頭組件6-2構成,碼料桶6-1與支架6-7垂直,所述滾輪上料機構6與第六送料裝置6-20相配合。
所述內墊圈上料機構7與第七送料裝置7-20相配合。
所述內鏈節全自動壓裝設備適用於節距主尺寸為133.17mm內鏈節,所述9個送料裝置,每個送料裝置之間間距為40°角固定於主轉盤上。
所述成品下料機構8與油缸壓裝機連接,用於將壓裝好成品,進行取出。
首先9個上料機構通過與之配套的9個送料裝置,分別把零件放入送料裝置中,送料裝置通過凸輪分割器對主轉盤的控制,進行40°的旋轉,停止,重複的循環進行,將每個零部件通過送料裝置,送入油缸壓裝機的壓裝板上,製成成品後,成品取料機構通過與油缸壓裝機的連接,進行取件。
首先套筒上料機構與第一振動盤的出料口連接,實現自動上料,該機構有缺料報警功能,上料後再與主轉盤配套的第二送料裝置相連接,將套筒送至第二送料裝置上,再通過第二送料裝置將零件送至壓裝位置,進行壓裝,外墊圈上料機構與第二振動盤的出料口連接,通過振動盤自動送料將外墊圈送至第三送料裝置上,再通過轉盤的旋轉將外墊圈送到壓裝位置,實現自動上料,只需要操作工定時定量向振動盤中放入外墊圈,該機構中無缺料檢測,外墊圈機構有能夠實現鏈板翻轉的功能,需人工定時查看振動盤是否有料,外墊圈安裝完畢後,外鏈板上料機構通過人工手動上料,通過外鏈板上料機構與第四送料裝置配合後將外鏈板送至壓裝位置,外鏈板上料機構需要工人手動上料,機構採用齒輪齒條自製翻轉機構,結構簡單可靠,鏈板放置時,儘量確保三個料道中儲料數量相同,套筒,外墊圈,外鏈板組裝完畢後,整個部件的一半已經完成,在通過主轉盤的轉動,半成品翻轉機構通過電磁鐵,旋轉缸對半成品進行翻轉,將翻轉後的半成品通過送料裝置送至壓裝位置,與剩餘零件重疊,等待壓裝。翻轉的過程中,轉臂下壓不得使電磁鐵接觸轉盤上的鏈板,通過調節螺杆上的螺母來調節下壓行程,間隙2-3mm為宜。機構中最為關鍵的配件為旋轉缸,不管在使用或是靜止狀態,不得在轉臂處施加大於3kg的外力,以免損壞旋轉缸,隨著主轉盤的轉動,滾輪上料機構通過人工上料,通過與送料裝置的配合,將滾輪送至壓裝位置進行壓裝,在使用中,若機構皮帶鬆弛,可通過尾部的調節螺釘來調節皮帶輸送的張緊力,向碼料桶中放置滾輪時,儘量確保每個碼料桶中的滾輪數量一致,在氣動系統斷氣或者氣壓不足時,不得認為拉動取料頭,以免損壞取料爪,主轉盤的旋轉將內墊圈上料機構送入送料裝置的內墊圈送入壓裝位置,內鏈板上料機構通過第三振動盤自動上料,通過與之配合的送料裝置將內鏈板上料機構送至壓裝位置進行壓裝,壓裝完畢後,所有零件組裝完畢後,通過成品下料機構取回部件,最終完成內鏈節的一個自動化組裝。
對所公開的實施例的上述說明,使本領域專業技術人員能夠實現或使用本發明。對這些實施例的多種修改對本領域的專業技術人員來說將是顯而易見的,本文中所定義的一般原理可以在不脫離本發明的精神或範圍的情況下,在其它實施例中實現。因此,本發明將不會被限制於本文所示的這些實施例,而是要符合與本文所公開的原理和新穎特點相一致的最寬的範圍。