餘熱餘壓製冷強化合成產物液化分離的方法與流程
2023-05-14 16:47:31 1
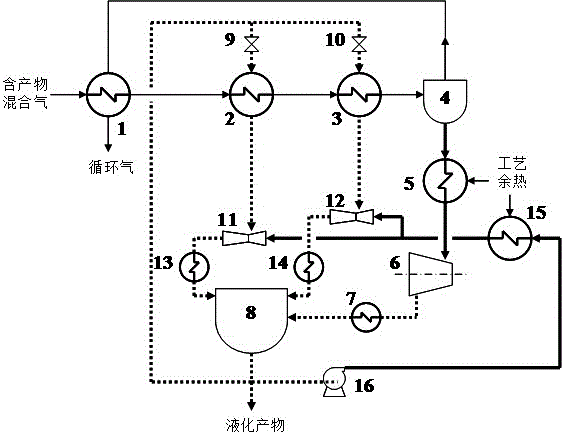
本發明涉及利用工業過程餘熱餘壓製冷的節能技術領域,特別是合成氨、合成甲醇等工業過程需要採用低溫液化分離化學反應產物的方法。
背景技術:
合成氨、合成甲醇等加壓合成化學反應工藝系統,反應器出口高壓氣體混合物中含一定比例的產物與反應物,在相同壓力下產物的液化溫度遠高於反應物,因此使氣體混合物冷卻降溫至低於產物的液化溫度,即可使產物液化分離、氣體反應物循環返回反應器。根據產物的熱力學性質,系統壓力越高、溫度越低、越有利於產物液化分離。在系統壓力一定的前提下,強化分離主要靠降低物系溫度。溫度降至低於常溫冷卻水,則需要製冷提供低溫冷媒。溫度越低、製冷能耗就越大,這是制約現有技術液化分離溫度未能達到理想的產品得率所需低溫的主要因素。以13.0MPa合成氨工藝為例,現工藝液化分離溫度0℃,反應器生成的合成氨液化分離產品得率不到80%、超過20%的產物殘流於循環氣又被帶回反應器,降低了反應器產能。突破此種制約的方法是利用化學反應工藝系統內部餘熱餘壓製冷,從而使液化分離溫度降低免受製冷能耗限制。特別是以高壓低溫分離所得的液化產物自身為製冷劑,在降壓進入儲罐之前,發揮其所含壓力能的作用、吸收餘熱提高焓值後絕熱膨脹做功,完成降壓過程的同時輸出機械功,一舉兩得。本發明方法基於上述原理利用化學工藝系統餘熱餘壓製冷強化反應產物低溫液化分離,具有節能、減排、增產多重有利效果。
技術實現要素:
本發明公開一種利用化學反應工藝系統餘熱餘壓製冷強化反應產物低溫液化分離的方法,用反應器出口工藝流體經低溫t4(-20~0℃)高壓p4(4.5~24.5MPa)液化分離所得的反應產物為冷媒,使循環使用的製冷劑從常溫降至製冷所需的低溫,冷媒溫升至t0(55~65℃)後再吸收工藝系統的餘熱升溫至t5(135~185℃)又成為膨脹機工質,絕熱膨脹至壓力p6(0.01~2.0 MPa)、溫度t6(0~60℃)、輸出機械功W6(熱-功轉換率18%~33%)。膨脹機出口工質在常溫空氣冷卻條件下液化後,既作為液化產物輸出,也用作製冷劑循環,還用作噴射器的工作流體:用作製冷劑時,在製冷溫度t2(-10~10℃)或 t3(-25 ~ -5℃)下吸熱汽化並被強制吸入噴射器、升壓到能夠用常溫空氣冷卻液化的壓力p8(0.01~2.0 MPa);用作噴射器的工作流體時,將其從p8加壓到p15(0.3~20 MPa),再利用工藝餘熱使其汽化並過熱到t15(135~185℃)從而具有足夠的能量進入噴射器吸引t2或 t3溫度下汽化的製冷劑蒸汽,並與之混合升壓至p8,在常溫空氣冷卻條件下液化,循環使用。
本發明技術路線是:反應器出口壓力p0(5~25 MPa)、產物含量摩爾百分數y0(5~20%)的混合氣體,通過前置換熱設備降溫到T0(35~45℃)後,在循環冷卻器1中被溫度t4(-20~0℃)的低溫循環氣冷卻降溫至T1(15~25℃),繼續在一級低溫換熱器2中被t2(-10~10℃)溫度下汽化的製冷劑吸熱冷卻降溫至T2(-5~15℃),繼續在二級低溫換熱器3中被t3(-25 ~ -5℃)溫度下汽化的製冷劑吸熱冷卻降溫至產物液化分離所需的低溫T3(-20~0℃),然後在氣液分離器4中分離,得到壓力p4(4.5~24.5MPa)、溫度t4(-20~0℃)的液化產物和同溫同壓的循環氣,循環氣中殘餘產物的含量y4比反應器出口含量 y0低85%以上。循環氣通過循環換熱器1回收冷量後其溫度提升至高於30℃,再通過前置換熱設備進一步升溫至高於50℃返回反應器循環。
氣液分離器4得到的壓力p4(4.5~24.5MPa)、溫度t4(-20~0℃)的低溫液化產物首先作為冷媒吸收從常溫儲罐8循環去一級低溫換熱器2和二級低溫換熱器3的製冷劑的熱量後,再在前置換熱設備被反應器來的混合氣體加熱溫升至t0(55~65℃),再通過餘熱回收器5加熱至t5(135~185℃),又成為膨脹機的工質進入膨脹機6絕熱膨脹輸出機械功W6(熱-功轉換率18%~33%),膨脹機出口工質壓力p6(0.01~2.0 MPa)、溫度t6(0~60℃),通過常溫空氣冷卻器7冷凝為壓力p8(0.01~2.0 MPa)、溫度t8(0~60℃)的液體,進入常溫儲罐8緩衝暫存後作為液化產物輸出,或作為製冷劑及噴射器的工作流體循環使用。
從常溫儲罐8循環去一級低溫換熱器2和二級低溫換熱器3的製冷劑被氣液分離器4得到的冷媒降溫到t9= t10(-15~5℃)而達到過冷狀態,分別通過減壓閥9和10進入一級低溫換熱器2和二級低溫換熱器3吸熱汽化製冷,成為各自汽化溫度t2(-10~10℃)和t3(-25 ~ -5℃)下的飽和製冷劑蒸汽,被強制吸入對應吸入壓力的一級噴射器11和二級噴射器12。用加壓泵16將噴射器工作流體從常溫儲罐8的壓力p8加壓到p15(0.3~20 MPa),在前置換熱設備被反應器來的混合氣體餘熱加熱溫升至55~65℃後再通過餘熱回收器15加熱汽化並過熱到t15(135~185℃),然後分別進入一級噴射器11和二級噴射器12吸引各自對應的一級低溫換熱器2和二級低溫換熱器3來的飽和製冷劑蒸汽,並通過混合使之升壓到常溫空氣冷卻器13和14對應的冷凝壓力p8(0.01~2.0 MPa),液化並進入常溫儲罐8。噴射器工作流體質量流量與吸入的製冷劑蒸汽質量流量之比0.8~1.8。
本發明所述壓力值均指絕對壓力,所述工藝餘熱的利用溫區為(65℃~200℃),所述大氣溫度在(-20℃~40℃)範圍。
附圖說明
附圖1是本發明提供的利用化學反應工藝系統餘熱餘壓製冷強化反應產物低溫液化分離方法的示意圖。圖中:1-循環換熱器;2-一級低溫換熱器;3-二級低溫換熱器;4-氣液分離器;5、15-餘熱回收器;6-膨脹機;7、13、14-常溫空氣冷卻器;8-常溫液體產物儲罐;9、10-減壓閥;11-一級噴射器;12-二級噴射器;16-加壓泵。
具體實施方案
以下結合但不限於實施例闡述本發明具體實施方式
實施例1 日產1320噸氨合成塔出口氣體中產品氨的液化分離
氨合成塔出口氣體物流:總流量23926.5 kmol/h,含氨4228.3 kmol/h,其餘為氮、氫氣
氨合成塔出口氣體總壓:13.0 MPa
氨分離後循環氣總壓:12.2 MPa
餘熱熱源1:變換工序收集185℃水蒸汽冷凝液,137120 kg/h
餘熱熱源2:廢熱鍋爐產185℃,1.0MPa飽和水蒸汽,20000 kg/h
日產1320噸氨合成塔出口壓力p0(≤13.0MPa)、氨含量摩爾百分數y0(≥17.67%)的混合氣體23926.5 kmol/h,通過前置換熱設備降溫到T0(35℃)後,在循環冷卻器1中被溫度t4(-10℃)的低溫循環氣冷卻降溫至T1(24℃),繼續在一級低溫換熱器2中被t2(0℃)溫度下液氨汽化吸熱冷卻降溫至T2(10℃),繼續在二級低溫換熱器3中被t3(-16℃)溫度下液氨汽化吸熱冷卻降溫至混合氣體中產品氨液化分離所需的低溫T3(≤-10℃),進入氣液分離器4中分離,得到壓力p4(≤12.2MPa)、溫度t4(≤-10℃)的液氨3594 kmol/h和同溫同壓的循環氣,循環氣中殘餘氨含量y4(≤2.38%)比反應器出口y0低86.5%以上。循環氣通過循環換熱器1回收冷量後其溫度提升至31℃,再通過前置換熱設備進一步升溫至55℃返回氨合成塔循環。
氣液分離器4得到的低溫液氨61098 kg/h首先作為冷媒吸收從常溫儲罐8循環去一級低溫換熱器2和二級低溫換熱器3作為製冷劑的液氨的熱量後,繼續在前置換熱設備被氨合成塔來的混合氣體餘熱加熱溫升至t0(≥60℃),再通過餘熱回收器5用137120 kg/h水蒸汽冷凝液(185℃)餘熱加熱至t5(180℃),作為膨脹機工質進入膨脹機6絕熱膨脹輸出機械功W6(14076.6 MJ/h,熱-功轉換率≥20.6%),膨脹機出口工質壓力p6(2.0 MPa)、溫度t6(50℃)通過常溫空氣冷卻器7冷凝為壓力p8(≤2.0 MPa)、溫度t8(≤50℃)的液氨,進入常溫儲罐8緩衝暫存後作為液氨產品輸出61098 kg/h。
作為製冷劑從常溫儲罐8循環去一級低溫換熱器2和二級低溫換熱器3的液氨34860 kg/h首先被氣液分離器4得到的低溫液氨降溫到t9= t10(-5℃)而達到過冷狀態,然後分別通過減壓閥9和10進入一級低溫換熱器2(15810 kg/h)和二級低溫換熱器3(19050 kg/h)吸熱汽化製冷,成為各自汽化溫度t2(0℃)和t3(-16℃)下的飽和氨蒸汽,並被強制吸入各自對應的一級噴射器11和二級噴射器12。用加壓泵16將作為噴射器工作流體的41000 kg/h液氨從常溫儲罐8的壓力p8加壓到p15(≤8.0 MPa),在前置換熱設備被氨合成塔來的混合氣體餘熱加熱溫升至60℃後再通過餘熱回收器15用廢熱鍋爐產飽和水蒸汽20000 kg/h(185℃)加熱汽化並過熱到t15(180℃),然後分別進入一級噴射器11(15800 kg/h)和二級噴射器12(25200 kg/h)吸引各自對應的一級低溫換熱器2和二級低溫換熱器3來的飽和氨蒸汽,並通過混合使噴射器出口達到常溫空氣冷卻器13和14對應的冷凝壓力p8(2.0 MPa),液化返回常溫儲罐8。
本實施例利用合成氨工藝系統餘熱(185℃水蒸汽冷凝液137120 kg/h和185℃廢熱蒸汽20000 kg/h)製冷,強化合成塔出口混合氣體低溫冷凝液化分離合成氨產品,與現有技術相比,獲得的有益效果是:
使日產1320噸氨合成塔產量提高到1460噸,產能增加10.6%;
節約機械壓縮製冷能耗11274 MJ/h並且輸出機械功14076 MJ/h,合計節能25350MJ/h;
節約冷卻水2000噸/每小時。
實施例2 日產300噸甲醇合成塔出塔氣中產品甲醇的液化分離
甲醇合成塔出塔氣:總流量6080.9 kmol/h,含甲醇433 kmol/h,含水38.3 kmol/h,其餘為不凝性合成氣
甲醇合成塔出塔氣總壓:≤5.0 MPa
甲醇合成塔循環氣總壓:≤4.88 MPa
餘熱熱源1:變換工序收集185℃水蒸汽冷凝液,10500 kg/h
餘熱熱源2:廢熱鍋爐產185℃,1.0MPa飽和水蒸汽,1560 kg/h
日產300噸甲醇合成塔出塔壓力p0(≤5.0MPa)、甲醇含量摩爾百分數y0(≤7.12%)的混合氣體6080.9 kmol/h,通過前置換熱設備降溫到T0(40℃)後,在循環冷卻器1中被溫度t4(0℃)的低溫循環氣冷卻降溫至T1(15℃),繼續在一級低溫換熱器2中被t2(-10℃)溫度下的製冷劑甲醇汽化吸熱冷卻降溫至T2(≤0℃),進入氣液分離器4中分離,得到壓力p4(≤4.88MPa)、溫度t4(≤0℃)的甲醇液428.4 kmol/h(13708.7 kg/h)和同溫同壓的低溫循環氣,低溫循環氣中殘餘甲醇含量y4(≤0.082%)比甲醇合成塔出口y0低98.8%。低溫循環氣通過循環換熱器1回收冷量後其溫度提升至35℃,通過前置換熱設備返回甲醇合成塔。
氣液分離器4得到的低溫甲醇液13708.7 kg/h首先作為冷媒吸收從常溫(65℃)儲罐8循環去一級低溫換熱器2作為製冷劑的甲醇液的熱量後,在前置換熱設備被甲醇合成塔來的混合氣體餘熱加熱溫升至t0(65℃),再通過餘熱回收器5用10500 kg/h水蒸汽冷凝液(185℃)餘熱加熱至t5(180℃),作為膨脹機工質進入膨脹機6絕熱膨脹輸出機械功W6(1091.8 MJ/h,熱-功轉換率≥22%),膨脹機出口工質壓力p6(0.105 MPa)、溫度t6(65℃)通過常溫空氣冷卻器7冷凝為壓力p8(0.105MPa)、溫度t8(≤65℃)的甲醇液,進入常溫儲罐8緩衝暫存後作為產品甲醇輸出13708.7 kg/h。
作為製冷劑從常溫儲罐8循環去一級低溫換熱器2的65℃甲醇液1778.6 kg/h首先被氣液分離器4得到的低溫甲醇液降溫到t9(3℃)達到過冷狀態,然後通過減壓閥9進入一級低溫換熱器2吸熱汽化製冷,成為汽化溫度t2(≤-10℃)下的飽和甲醇蒸汽,並被強制吸入一級噴射器11。用加壓泵16將作為噴射器工作流體的2976.8 kg/h甲醇液從常溫儲罐8的壓力p8加壓到p15(≤0.9 MPa),在餘熱回收器15中用廢熱鍋爐產(185℃)飽和水蒸汽1560 kg/h加熱汽化並過熱到t15(180℃),然後進入一級噴射器11吸引一級低溫換熱器2汽化來的飽和甲醇蒸汽,並通過混合使噴射器出口達到常溫空氣冷卻器13對應的冷凝壓力p8(≥0.105 MPa),液化返回常溫儲罐8。
本實施例利用甲醇工藝系統餘熱(185℃水蒸汽冷凝液10500 kg/h和185℃廢熱蒸汽1560 kg/h)製冷,強化甲醇合成塔出口混合氣體低溫冷凝液化分離,與現有技術相比,獲得的有益效果是:
使日產300噸甲醇合成塔產量提高到329噸,產能增加9.67%;
使循環氣含水降至0.005%以下;
輸出機械功1091.8 MJ/h;
節約冷卻水500噸/每小時。
本發明不限於上述實施例,其技術方案已在發明內容部分予以說明。